Alumiinihiekkavalu on yksi vanhimmista ja monipuolisimmista metallien valumenetelmistä, jota käytetään laajalti nykyaikaisessa teollisuudessa monimutkaisten, kestävien ja kustannustehokkaiden komponenttien valmistukseen. Alumiinihiekkavalun valmistajat voivat tuottaa monimutkaisia geometrioita, joissa on monimutkaisia piirteitä, joiden työstäminen kiinteästä materiaalista olisi muuten ollut joko epäkäytännöllistä tai kannattamatonta kaatamalla sulaa alumiinia valmisteltuihin hiekkamuotteihin. Menetelmä soveltuu erityisesti pienen ja keskisuuren volyymin tuotantoon, prototyyppien valmistukseen ja korkeisiin rakenteellisiin valukappaleisiin sovelluksissa, jotka kattavat ilmailu-, auto-, puolustus- ja energiateollisuuden alat.
Hiekkavaletun alumiinin mielenkiintoisin piirre on, että se on sekä joustava että toimiva. Alumiinilla on erittäin hyvä lujuus suhteessa painoon, korroosionkestävyys ja kierrätettävyys, mikä tekee siitä erinomaisen valumateriaalin. Yhdessä hiekan lämmönkestävyyden ja korkean muovattavuuden kanssa prosessi tarjoaa skaalautuvan tuotantokyvyn ja erinomaisen mittatarkkuuden. Mallisuunnittelu, muotin koostumus, sulan laatu ja ruiskutussuunnittelu ovat avaintekijöitä jokaisen valukappaleen onnistumisen kannalta.
Erinomaisen alumiinihiekkavalujen valimon on hallittava metallitekniikan klassisten tosiasioiden lisäksi myös prosessien innovaatiot. Nykyiset laitokset soveltavat uusinta teknologiaa vikojen estämiseksi ja valukappaleen parhaan suorituskyvyn varmistamiseksi käyttämällä 3D-hiekkatulostusta, simulointiohjelmistoja ja reaaliaikaista prosessin seurantaa. Tarkkuusvalmistetut ja valetut alumiiniosat pystyvät nyt täyttämään tiukat turvallisuutta, toleranssia ja kestävyyttä koskevat tekniset standardit.
Kun kysyntä kasvaa monimutkaisille komponenteille, joiden toimitusaika on nopeampi ja ympäristövaikutukset pienemmät, ammattimaisten alumiinihiekkavalupalvelujen on kehityttävä edelleen. Tässä artikkelissa perehdytään itse prosessin teknisiin yksityiskohtiin, sen tekniseen työnkulkuun, materiaaleihin, haasteisiin, innovaatioihin ja niin edelleen.
Alumiinin hiekkavalun perusteet
Alumiinihiekkavalun ydin on sulan alumiinin valaminen hiekkamuottiin, joka muotoillaan lopullisen osan geometriaa jäljittelevällä mallilla. Kun alumiini on jähmettynyt, hiekkamuotti ravistetaan pois, jolloin valettu kappale jää jäljelle. Prosessilla on myös erinomainen mittava joustavuus ja skaalautuvuus korkean sekoituksen ja pienen volyymin valmistusolosuhteissa.
Prosessi perustuu ei-pysyvän muotin, hiekan, käyttöön, joka voidaan kierrättää ja käyttää uudelleen, mikä minimoi materiaalien ja kustannusten tuhlauksen. Hiekkamuotit koostuvat tavallisimmin kvartsihiekasta, johon on lisätty sideainetta, ja sideainejärjestelmän luonne vaikuttaa yleensä huomattavasti tuloksena olevaan pintakäsittelyyn, mittatarkkuuteen ja jäähtymisnopeuteen.
Virtausprosessi hiekkavalun alumiinin suunnittelussa
Alumiinin hiekkavalu on tekninen prosessi, joka koostuu joukosta tarkasti kalibroituja toimintoja, joiden tarkoituksena on muuttaa raakalumiini erityisiksi, hyvin rakennetuiksi ja tarkasti mitoitetuiksi osiksi. Sekä materiaali- että mekaanista asiantuntemusta tarvitaan perusteellisesti, jotta prosessin kaikki vaiheet onnistuvat. Seuraavassa analysoidaan vaiheittain, miten alumiinin hiekkavalu toteutetaan ammattimaisesti ja teknisesti.
1. Mallin suunnittelu ja valmistus
Alumiinihiekkavaluprosessin ensimmäinen vaihe on mallin, lopullisen valukappaleen fyysisen kopion, suunnittelu ja valmistus. Malleissa on otettava huomioon melko kriittiset poikkeamat, kuten kutistuma, veto ja työstövara. Koska alumiini supistuu, mallit muotoillaan jäähdytyksen aikana hieman suurempina kuin valmis osa. Alumiiniseosten kutistuma on yleensä 1,3 prosenttia, mutta se voi vaihdella seoksesta ja jäähdytysolosuhteista riippuen.
Muottien pystysuorille osille annetaan luonnoskulmat, jotka ovat yleensä muutaman asteen välillä 1-3, jotta malli voidaan helposti irrottaa hiekkamuotissa varoen tuhoamasta onteloa. Lisävaraukset (työstövaraukset) sisällytetään siten, että jälkikäsittelyn ja lopullisen kappaleen välillä ei ole haitallisia vuorovaikutuksia. Mallit voidaan valmistaa puusta, metallista, hartsista tai jopa 3D-tulostetuista polymeerimateriaaleista tarkkuusvaatimusten ja tuotantomäärän tarpeiden mukaan.
2. Muotinvalmistus (muottivalu ja ytimen asetus)
Mallin valmistamisen jälkeen valmistetaan muotti. Hiekkavaletussa alumiinimuotissa on kaksi erillistä puoliskoa: yläpuolisko (cope) ja alaosa (drag). Ne valmistetaan täyttämällä hiekkaa muotin ympärille pullossa. Hiekka on sovelluksesta riippuen yleensä silikapohjaista, ja se amalgamoidaan sideaineiden, kuten saven (vihreä hiekka) tai kemiallisten hartsien (no-bake-hiekka) kanssa.
Jos osan rakenteessa on sisätilaa ja onttoja osia, on käytettävä hiekkasydämiä. Ne sijoitetaan muottipesään, minkä jälkeen metalli valetaan. Ytimet voidaan valmistaa käyttämällä ydinlaatikoita, ja tarkkuustuotannossa ne voidaan tulostaa suuremmalla tarkkuudella 3D-hiekkatulostuksen avulla. Ytimen tarkka jalanjälki on erittäin tärkeää, jotta rakenne on jäykkä ja jotta se pysyy kiinni lopullisen osan mitassa.
3. Porttijärjestelmän suunnittelu
Muodostetun sulkemisjärjestelmän oikea-aikaisuus ja tehokkuus ovat merkittäviä tekijöitä alumiinin hiekkavaluprosessin onnistumisen kannalta. Järjestelmä koostuu valualtaasta, ruiskusta, juoksuputkista ja portista, jotka pakottavat valetun alumiinin muottiin. Riittävällä sulkujärjestelmällä estetään suuri turbulenssi, minimoidaan ilmansulku ja varmistetaan myös tasainen täyttö.
Tarvitaan myös nousuputkia (vaihtoehtoisesti syöttölaitteita), joita voidaan pitää sulan metallin säiliönä, joka tasoittaa jähmettymisen jälkeen tapahtuvan kutistumisen suuntaa. Insinöörit käyttävät yleensä valusimulointiohjelmistoja tutkiessaan ja optimoidessaan syöttö- ja nousujärjestelmiä. Ennustaminen tapahtuu käyttämällä simulointityökaluja, kuten MAGMASoftia tai ProCASTia, jotta tyypilliset virheet, kuten kylmäsulkeumat, virhevalut ja kutistumishuokoisuus, voidaan korjata käytännössä ennen tuotantoa.
4. Cu-sulatus ja metallin käsittely
Alumiini sulatetaan yleensä reverberatoriouunissa, upokasuunissa tai induktiouunissa, ja valinta riippuu erän tilavuudesta, seoksen tarpeista ja tarvittavan energian määrästä. Puhtaan alumiinin sulamislämpötila on noin 660 celsiusastetta (1220 Fahrenheitin lämpötilaa), vaikka seosten sulamispiste voi vaihdella hieman koostumuksesta riippuen.
Kaasun imeytyminen, erityisesti vetykaasun imeytyminen, on yksi suurimmista teknisistä ongelmista sulatuksen aikana. Kuuma alumiini ottaa hyvin helposti vetyä joko ilmankosteudesta tai ladatuista luvuista. Valmiissa valukappaleessa esiintyy vetyä enemmän huokoisuutta. Tämän vuoksi sula altistetaan kaasunpoistomenetelmille, joihin usein liittyy passiivisten kaasujen (kuten argon tai typpi) syöttäminen, jotka työnnetään sulaan pyörivän juoksupyörän avulla. Sulaan voidaan myös lisätä valuaineita, joilla poistetaan sulasta oksideja ja sulkeumia.
5. Sulan metallin torjunta
Kun sulatettu alumiini on puhdistettu ja ilmastoitu, se kaadetaan muottiin käyttäen porttijärjestelmää. Kaadon on oltava täysin hallittua ja jatkuvaa ilman, että muotti sekoittuu, jolloin ilmaa jää ja jähmettyy varhaisessa vaiheessa. Manuaalisissa kokoonpanoissa käytetään kauhoja, joita käyttävät henkilöt, jotka on koulutettu valamiskorkeuteen ja -nopeuteen. Robottikauhat ovat yksi niistä vaiheista, jotka takaavat turvallisen ja korkean toistettavuuden automaattisissa järjestelmissä.
Valulämpötila on yleensä 690-740 °C seoksesta ja muotin monimutkaisuudesta riippuen. Valaminen alhaisissa lämpötiloissa voi aiheuttaa kylmäsulkuja tai epätäydellistä täyttöä, ja valaminen korkeissa lämpötiloissa voi aiheuttaa enemmän kaasun poimimista ja hapettumista.
6. Jähmettyminen ja jäähdytys
Jähmettymisvaihe on yksi tärkeimmistä vaiheista, kun alumiinia valetaan hiekkavalumenetelmällä. Kun alumiini muuttuu kiinteäksi, se supistuu, ja kutistumisesta on huolehdittava sulkemis- ja noususuunnittelussa. Hallitun jäähdytyksen tarkoituksena on tasainen mikrorakenne sekä sisäisten jännitysten ja kutistumisonteloiden vähentäminen.
Valun eri alueiden geometriasta ja seinämän paksuudesta riippuen niiden jäähtymisnopeudet vaihtelevat. Sen sijaan käytetään suunnattua jähmettymistä, useimmiten suunnittelemalla valukappale siten, että valukappale on suunnattu siten, että jähmettyminen tapahtuu ohuesta paksuun, mikä ohjaa kutistumisontelot nousuputkiin. Jäähdytyksen nopeuttamiseksi tietyillä alueilla ja siten raerakenteen säätämiseksi ja vikojen minimoimiseksi yksi tekniikka on käyttää jäähdytyskappaleita, metallisia inserttejä muotissa.
7. Ravistelu, puhdistus ja huuhtelu.
Kun muotti on onnistuneesti poistettu, muotti ravistetaan auki sen jälkeen, kun valukappale on täysin jähmettynyt. Hiekan poistamiseksi tehdään leikkaus tai hionta mekaanisesti tai käsin. Leikkaus tehdään valukappaleen, porttijärjestelmän ja nousuputkien kohdalla.
Valun pinnalla on yleensä hiekkajäämiä ja oksidisaostumia, ja näiden saostumien poistamiseksi suoritetaan puhdistusprosesseja, kuten hiekkapuhallusta, hiontaa tai jopa kemiallista peittausta. Tässä vaiheessa tehdään myös rasvanpoistoa, jossa poistetaan tarpeetonta metallia ja hienonnetaan paksuja pintoja. Myös muotissa käytetyt ytimet poistetaan.
8. Lämpökäsittely ja koneistus (tarvittaessa)
Monille hiekkavalualumiiniosille tehdään valun jälkeinen lämpökäsittely niiden mekaanisten ominaisuuksien parantamiseksi. Tavanomaisia menetelmiä ovat mm:
- ikäkarkaistavien alumiiniseosten (esim. A356-T6) T5/T6-karkaisu, jossa lujuus ja kovuus lisääntyvät huomattavasti.
- Hehkutus, jotta sen sisällä olevat jännitykset saadaan poistettua ja siitä saadaan sitkeämpää.
Lämpökäsittelyn jälkeen voidaan tarvita tarkkaa koneistusta lopullisten toleranssien saavuttamiseksi, erityisesti niiden pintojen osalta, jotka liittyvät muihin osiin tai joiden on oltava tarkasti mitoitettuja.
Vastaesimerkkejä: Hiekkavalettujen osien CNC-jyrsintä, poraus ja sorvaus ovat yleisiä jälkikäsittelyjä.
9. Laadunvarmistus ja tarkastus
Viimeisessä vaiheessa tehdään lopputarkastus, jolla varmistetaan, että valettu osa täyttää vaaditut vaatimukset. Seuraavassa on tavanomainen laadunvarmistus hiekkavalutyyppiselle alumiinille:
- Mittaukseen perustuva tarkastus (CMM, koordinaattimittauskone tai laser- tai muu skannaus).
- Rikkomaton testaus (Non-Destructive Testing, NDT), kuten röntgenkuvaus, ultraäänitarkastus tai väriaineella tehtävä tunkeutumistarkastus, jotka paljastavat sisäiset tai pintaviat.
- Mekaaniset vetolujuus-, venymä- ja kovuuskokeet, erityisesti rakenteellisesti käytettävien valukappaleiden osalta.
- Tarkastustiedot on kirjattu lokiin, jotta tietoja voidaan jäljittää ja parantaa prosessin myöhempiä toistoja.
Alumiinin hiekkavalun metallurgiset näkökohdat
Hiekkavalussa käytettävät alumiiniseokset voidaan yleensä jakaa kahteen ryhmään: ei-lämpökäsiteltävät ja lämpökäsiteltävät seokset. Tuttuja seoksia ovat A356, A319 ja 319.1, jotka on valittu lujuuden, lämmönjohtavuuden ja korroosionkestävyyden tarpeiden mukaan. Jäähdytysnopeuksilla ja seosaineilla, kuten piillä, magnesiumilla ja kuparilla, on suuri vaikutus valukappaleen raerakenteeseen.
Yksi alumiinihiekkavaluprosessin vaativimmista osa-alueista on huokoisuuden hallinta. Vetykaasun liukoisuus alumiiniin on myös erittäin suuri nestemäisessä faasissa kuin kiinteässä faasissa, mikä aiheuttaa yleensä mikrohuokoisuutta jähmettyvään altaaseen. Tavanomaisia menetelmiä tämän haasteen rajoittamiseksi ovat tyhjiöpoisto ja suojakaasuhuuhtelu.
Alumiinin hiekkavalussa käytettävät materiaalit
Alumiinihiekkavalussa käytettävät materiaalit ovat ratkaisevia lopputuotteen suorituskyvyn, valmistettavuuden ja kestävyyden kannalta. Niitä ovat alumiiniseosten lisäksi erilaiset hiekat, sideaineet sekä muotin ja ytimen valmistuksessa käytettävät apumateriaalit. Sosioekonomiset tekijät. Kutakin materiaalia valittaessa on tärkeää päästä kompromissiin valettavuuden ja mekaanisten ominaisuuksien, pintakäsittelyn ja kustannustehokkuuden suhteen. Seuraavassa esitellään yksityiskohtaisesti tärkeimmät materiaaliryhmät, joissa prosessi suoritetaan.
1. Alumiiniseokset
Alumiiniseoksen valinta on avainasemassa kaikissa alumiinin hiekkavaluprosesseissa. Eri seokset tarjoavat erilaisia mekaanisia ominaisuuksia, korroosiota ja lämpökäyttäytymistä. Yleisesti ottaen nämä seokset voidaan jakaa kahteen laajaan luokkaan: muokatut (taotut/valssatut) ja valuseokset. Hiekkavalussa käytetään myös valualumiiniseoksia, koska ne soveltuvat parhaiten valuun, juoksevuuteen ja jähmettymiseen.
Useimmiten valetut alumiiniseokset ovat:
A356 (Al-Si7-Mg):
Tämä on yksi suosituimmista seoksista alumiinin hiekkavalupalvelujen alalla. Se on erittäin hyvin valettavissa, sillä on suhteellisen hyvä korroosionkestävyys, ja se voidaan lämpökäsitellä T6-luokkaan (korkea lujuus, korkea sitkeys), mikä tekee siitä erittäin käyttökelpoisen. Ikäkarkaisukäsittelyt ovat mahdollisia lisäämällä magnesiumia.
319 (Al-Si-Cu-Mg):
319 tunnetaan myös hyvästä kulutuskestävyydestä ja työstettävyydestä, ja sitä käytetään autoteollisuudessa ja yleisessä konepajateollisuudessa. Sen korroosionkestävyys on kuitenkin huonompi kuin A356:n.
535 (Al-Mg):
Se on seos, jossa on korkea magnesiumpitoisuus, ja siksi sillä on erittäin hyvä korroosionkestävyys ja iskunkestävyys. Sitä käytetään yleisesti ilmailu- ja avaruusalalla sekä merenkulkualan sovelluksissa.
Alumiini-pikiseokset (Al-Si):
Nämä seokset ovat saaneet tunnustusta suuren juoksevuutensa ja pienemmän kutistumisensa ansiosta, erityisesti silloin, kun niitä käytetään monimutkaisissa komponenteissa, kuten hiekkavaletuissa alumiiniosissa.
Lisäaineet ja viljanjalostajat:
Valulaadun parantamiseksi, huokoisuuden vähentämiseksi ja mekaanisten ominaisuuksien parantamiseksi voidaan lisätä titaani-boori-mestaseoksia (esim. AlTi5B1) raekoon hienontamiseksi. Al-Si-seosten piivaiheen muokkaamisessa käytetään yleensä strontiumia, joka lisää sitkeyttä ja vähentää kuumarepeytymistä.
2. Hiekka Materiaalit
Menetelmässä tärkein valumateriaali on hiekka alumiinihiekkavalun valimoprosessissa. Sen tarkoituksena on luoda muottiontelo, johon sula alumiini kaadetaan. Hiekan on siedettävä korkeaa lämpötilaa (yli 700 o C), oltava mittatarkkaa ja myös kestettävä metallivirran aiheuttamaa eroosiota.
Käytettävä hiekka:
Piihiekka:
Yleisimmin käytetty ja halvin hiekka. Se on hyvä sekä tulenkestävyydeltään että työstettävyydeltään. Lämpölaajenemiseen liittyy kuitenkin ongelmia, jotka voivat johtaa valuvirheisiin, kuten suonittumiseen tai kuumiin repeämiin, ellei niitä hallita hyvin.
Kromiittihiekka:
Tällä hiekalla on parempi lämmönjohtavuus ja lämpöshokin kestävyys, joten sitä voidaan käyttää korkean lämpötilan investoinneissa sekä suurten kappaleiden paksupintaisissa valukappaleissa.
Zirkonihiekka:
Sovelletaan sovelluksissa, joissa mittatarkkuus on erittäin tärkeää. Se on paljon kalliimpaa, mutta sen lämpölaajeneminen on erittäin vähäistä ja sen tulenkestävyys on korkea.
Hiekanjyvän koko:
Hienorakeinen hiekka tekee pinnasta sileämmän ja vaikuttaa läpäisevyyteen. Karkearakeisen hiekan koko lisää läpäisevyyttä ja muotin lujuutta, mutta lopputuote voi olla karkeampi. Kappaleen geometrian ja viimeistelyvaatimusten osalta valitaan yleensä kompromissi.
3. Sidonta ja lisäaineet
Alumiinin hiekkavalu: Alumiinivalussa käytetty hiekka pidetään yhdessä sideaineen avulla, jolloin muotista saadaan riittävän kiinteä, jotta se kestää sulan alumiinin paineen. Sideaineet ovat joko orgaanisia tai epäorgaanisia, ja ne valitaan käytettävän hiekkajärjestelmän mukaan.
Vihreä hiekka Sideaineet:
Bentoniittisavi:
Savinen paisutuskerros, jota käytetään viherhiekkajärjestelmässä plastisuuden ja koheesion lisäämiseksi. Se sekoitetaan veteen uudelleenkäytettävän muottimateriaalin muodostamiseksi.
Vesi:
Se on vihreän hiekan aktivaattori, joka auttaa saven sitoutumista ja tiivistää hiekkaa.
Kemiallisesti sidotut hiekkajärjestelmät:
Furaanihartsi:
Luonnollinen sideaine, korkea lujuus ja hyvä viimeistely. Ne levitetään yleensä paistojärjestelmässä.
- Fenoliuretaanikylmälaatikko (PUCB) oli viimeinen tuotetyyppi.
- Sillä on suuri ydinvoima ja mittatarkkuus. Dietziä käytetään laajalti sydänten valmistuksessa.
Lisäaineet:
Tämän hiilialueen hiilikaivokset ovat luultavasti maailman vanhimmat kaivokset; ne ulottuvat vähintään 2 200 jalan syvyyteen, ja niiden tiedetään jatkuvan suonen vieressä kohti merta, jossa hiiltä kutsutaan merihiileksi tai hiilipölyksi.
Yhdistetään vihreään hiekkaan mustan värin tehostamiseksi muotin pinnalla ja valuvirheiden, kuten metallin tunkeutumisen, poistamiseksi.
Rautaoksidi:
Se on hyödyllinen suonitus- ja laajentumishäiriöiden vähentämiseksi kuumilla alueilla.
Grafiitti:
Parantaa hiekan valmistusta, kun sillä on korkea hiekan juoksevuus ja muotin irtoaminen.
4. Ydinmateriaalit
Niin sanottujen hiekkavalettujen alumiiniosien sisäiset ontelot ja monimutkaiset muodot valmistetaan ydinkappaleilla. Ne valetaan tyypillisesti erittäin puhtaasta piihiekasta, jonka sideainejärjestelmä on sama kuin muotissa, mutta usein jäykempi ja tarkempi.
Ydintuotannossa tärkeitä materiaaleja ovat:
- Silikahiekka ( tiheä silmäkoko )
- Sideaineet (furaanihartsi tai PUCB)
- Tuuletusvaijerit tai ydinaukot, jotka mahdollistavat kaasun poistumisen valussa.
Sideaineen suihkutus 3D-tulostetuissa hiekkasydämissä on tulossa suosituksi korkean teknologian valimoissa. Niiden avulla ei tarvitse käyttää ydinlaatikoita, ja ne mahdollistavat monimutkaisten geometrioiden nopean prototyyppien valmistuksen.
5. Muotin pinnoitus ja muotin pesu
Tulenkestävät pinnoitteet levitetään (tai muotin pesu) parantamaan valukappaleen pintakäsittelyä tai antamaan muotille tai ytimelle lämpö- ja kemiallisen suojan.
Tällaisia yleisiä pinnoitemateriaaleja ovat:
Zirkonipohjaiset pinnoitteet
Zirkonipohjaiset pinnoitteet ovat myös erinomaisia, kun otetaan huomioon niiden tulenkestävyys ja eristysominaisuudet korkean lämpötilan alumiiniseoksissa.
Grafiittipohjaiset pinnoitteet:
Edistävät helppoa heittoa ja soveltuvat kylmillä alueilla.
Aluminosilikaattipohjainen:
Alumiinisilikaattipohjaiset pinnoitteet ovat yleiskäyttöisiä suojapinnoitteita, jotka minimoivat pintavirheet.
Nämä pinnoitteet levitetään sivelemällä, ruiskuttamalla tai kastamalla, ja sitten ne kuivataan ennen metallin valamista. Ne vähentävät hiekkaeroosion, metallin tunkeutumisen ja kaasuun liittyvän kehityksen vaaraa.
6. Muut apu- ja prosessimateriaalit
Muita alumiinihiekkavalupalveluissa käytettäviä materiaaleja ovat:
Virtaukset:
Sulan puhdistamiseksi ja ei-metallisten sulkeumien poistamiseksi. Käytetyn seoksen tyypistä riippuen yleisiä ovat kloridipohjaiset tai fluoridityyppiset vuonet.
Kaasunpoistotabletit tai -kaasut:
Näissä voidaan käyttää heksakloorietaani- tai vastaavia tabletteja, vaikka nykyisissä valimoissa suositaankin ympäristö- ja turvallisuussyistä argonkaasun kaasunpoistoa.
Anturit, termoparit ja pyrometrit:
Lämpötila-antureita on saatavana korkean lämpötilan seoksina ja keraamisina materiaaleina sulan ja muotin olosuhteiden seurantaan.
Hylsyjen ja nousuputkien eksotermiset materiaalit :
Se sijoitetaan nousuputkiin, jotta sulan metallin syöttö säilyisi pidempään. Niissä on eristäviä materiaaleja tai eksotermisiä materiaaleja, jotka luovuttavat lämpöä jähmettyessään.
Tehtävä alumiini hiekkavalu Foundry
Erittäin kehittynyt valimo on niin sanottu alumiinihiekkavalimo, jossa on valukoneet, ydintuotantoasemat, sulatusuunit ja tarkastusjärjestelmät. Valimot ovat erikoistuneet valamiseen, valetun kappaleen maksimaaliseen laatuun, minimaaliseen sykliaikaan ja maksimaaliseen materiaalitehokkuuteen. Kehittyneissä valimoissa yhdistyvät sellaiset digitaaliset työkalut kuin:
- Simulation Software: Niin sanotut simulointiohjelmistot (kuten MAGMASoft ja FLOW-3D Cast) simuloivat muotin täyttymistä ja jähmettymistä, ja niiden avulla valimon insinöörit voivat hienosäätää syöttösuunnittelua ja ennakoida vikoja.
- Automaattinen ydin: Monimutkaiset sisäiset muodot voidaan helposti luoda uusilla 3D-tulostetuilla hiekkasydämillä, joiden käyttö vähentää työkalujen ja ajan käyttöä.
- Rikkomaton testaus (NDT): Tässä yhteydessä käytetään röntgentutkimusta, ultraäänitutkimusta sekä väriaineella tehtävää tunkeutumistutkimusta, jolla varmistetaan valetun osan täydellisyys.
Onnistuneella alumiinihiekkavalimolla on laadunvalvontajärjestelmä, jossa noudatetaan kaikkia maailmanlaajuisia standardeja, kuten ASTM B26, ISO 8062-3 ja AMS 4218, jotta voidaan taata valettujen alumiiniseosten vakaa laatu.
Edut alumiini Sand Casting Services
Ammattimaiset alumiinihiekkavalupalvelut tarjoavat kokonaisvaltaisia valuratkaisuja, mukaan lukien suunnittelukonsultointi, nopea prototyyppien rakentaminen, työkalujen valmistus ja jälkikäsittely. Nämä ovat OEM- ja tier-1-toimittajien osien hankintapalveluja, jotka tarvitsevat nopeinta läpimenoaikaa, mukautettua osan geometriaa ja toiminnallisuutta.
Jotkut niistä ovat tärkeimmät edut:
- Alhaiset työkalukustannukset: Hiekkavalun työkalukustannukset ovat alhaisemmat kuin painevalun, joten se on paras vaihtoehto lyhyisiin tuotantosarjoihin.
- Palvelu: Palveluntarjoajia kehotetaan kehittämään räätälöityjä seoksia vaadittujen mekaanisten tai termisten ominaisuuksien mukaan.
- Nopea prototyyppien rakentaminen: It is possible to prepare a prototype in days instead of weeks with the use of current digital pattern-making.
As industries demand faster product cycles and greater customization, high-quality aluminum sand casting services become invaluable partners in supply chains.
Tarkkuus ja suorituskyky hiekkavaletuissa alumiiniosissa
Sand casting aluminum parts remains a cornerstone in the production of engine blocks, transmission housings, manifold covers, and aircraft components. The process can also handle simple and complex part geometries with wall thicknesses of between 3mm to 75mm, depending on the strength of the mold and the flowability of the alloy involved.
Key performance metrics for sand casting aluminum parts include:
- Dimensional Tolerance: Able to tolerate between 0 and 0.5 percent of their nominal values according to the quality of the molds.
- Surface Roughness: This is between 150 -500 RMS, although with secondary process, they can be finer.
- Mekaaninen lujuus: Tensile strengths are alloy and treatment dependent, and are typically between 170-300 millimeter of Pascal (MPa).
Engineers can decrease the amount of shrinkage defects and make uniform structures during the grain structure through carefully selected gating and riser systems.
Alumiinin hiekkavalun haasteet ja innovaatiot
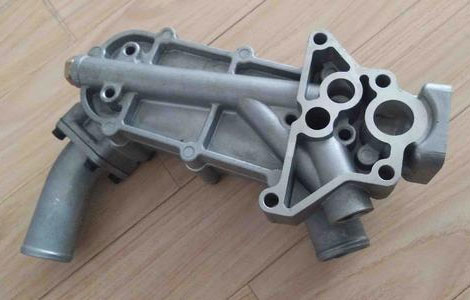
Although aluminum sand casting has stood the test of time as a versatile and cost-effective manufacturing method, it faces multiple technical and operational challenges that affect casting quality, production efficiency, and scalability. Luckily, the process is being transformed greatly with the help of new solution innovations as the industry faces these challenges with new tools and technologies. Here goes a further breakdown of both challenges that continue to plague the art of aluminum sand casting and emerging innovations that seem to have arisen in the field.
1. Sulan laatu ja kaasun huokoisuus
Haaste:
One of the most critical and persistent problems in aluminum sand casting is gas porosity, primarily due to hydrogen absorption. When molten, Aluminum has the tendency to absorb hydrogen gas, notably in the presence of moist conditions or under abuse by the utilization of contaminated charge materials. As the Metal cools, the solubility of Hydrogen falls, hence the gas precipitates, forming minute holes in the casting. Such pores seriously limit resistance to fatigue and sealing capacities as well as mechanical strength.
Innovaatio:
Solution to this problem has been solved by employing modern degassing technology in modern foundries, like rotary degassing technology, use of inert gases like argon or nitrogen. These systems stir the melt so as to bring more surface area and free up the trapped hydrogen. Moreover, flush rings in-line degassing systems are used to remove oxides and inclusions. Some of the plants are even putting up real-time gas monitoring sensors to evaluate the hydrogen’s state during melting and pouring.
2. Dimensiomainen suru ja siihen tarttuva muotti
Haaste:
Keeping strict dimensional tolerances with the method of sand casting aluminum is not easy because the sand mold is a variable thing. These geometric changes can be brought about by sand compaction, moisture content, as well as thermal expansion, among others, thus causing some parts that no longer be within their specifications. Also, the reusable patterns denote a higher probability of vibration to dimensional drift, and it is not considered over time.
Innovaatio:
To counter this, numerous foundries are utilizing digitally controlled molding machines that provide uniform pressure in the compaction of the molds and achieve a degree of uniformity in their mold quality. 3D sand print (binder jetting) is transforming the creation of molds, as it does not require a physical pattern. These cast molds are highly accurate to the micron level, suitable for prototyping and small manufacturing runs. In conjunction with casting simulation software, engineers are able to simulate dimensional changes on cooling and offset the changes at pattern design.
3. Kevyt automaatio ja voimakas työvoimariippuvuus
Haaste:
Traditional aluminum sand casting processes are labor-intensive, particularly in mold preparation, pouring, and finishing. The manual operations not only curtail the throughput but also the variability of the casting. In addition, the use of skilled labor may prove to be a bottleneck, especially in areas where there is a scarcity of labor.
Innovaatio:
Robotic automation is changing repetitive and risky operations like the actuality of molds, pouring, and grinding. The collaboration robots (cobots) would have the capacity to collaborate with people in fundamental assembly and extraction of castings. Foundries are also embracing automated pouring installations that have laser sensors and vision systems to allow a balance in pouring rates and the temperature of pouring to be controlled with accuracy. Such advancements not only contribute to the efficiency of production but also to safety and unification in the workplace.
4. Valuvikojen juurisyiden ennustaminen
Haaste:
Concerns over casting defects like cold shuts, hot tears, shrinkage holes, and inclusions continue to be a major contributory factor to material wastage and product defects. The primary cause of these defects needs to be identified and removed to prevent their reoccurrence; this would demand an in-depth knowledge of fluid dynamics, thermo gradients, and alloy dynamics- aspects that are not readily available in any foundry without special measures.
Innovaatio:
Sophisticated computational fluid dynamics (CFD) and solidification modeling packages have recently become available that enable the engineer to simulate the complete casting process in a virtual world. FLOW-3D Cast, ProCAST, and MAGMASoft computer software are some of the software to forecast the molten steel defects, and where defects are likely to form before pouring any metal. The tools are used to optimize gating systems, riser placements, and cooling strategies to get castings that are free of defects. Further, machine learning models are being worked on where the defect data of the past is used to analyze and give real-time recommendations on the process to be adjusted.
5. Ympäristön kestävyys ja jätehuolto
Haaste:
Aluminum sand casting generates waste in the form of spent sand, metal dross, flux residue, and off-spec parts. The disposal of sand, especially, presents a problem as chemically bonded sand might not be easy to recycle. Also, high energy usage in the melting process adds much to the carbon footprint in the foundry processes.
Innovaatio:
Most progressive foundries are investing in closed-loop sand reclamation systems, which recycle previously used sand through thermo-mechanical processes. Such systems cut down on the number of dumps, as well as the cost of raw materials. In the energy sense, the induction melting furnaces are more efficient and have minimal emissions than their traditional analogs, gas-fired reverberatory furnaces. Solar power, recycling of waste heat, and real-time monitoring of energy are also assisting foundries in cutting down environmental impact as they comply with the increasingly strict regulatory requirements.
6. Metallurgian asettamat rajoitukset ja vaikeus metallurgiassa.
Haaste:
The use of applicable aluminum alloys in sand casting is associated with a trade-off between castability, mechanical properties, and heat-treatability. Certain high-performance alloys have poor fluidity or are prone to hot tearing during solidification and, as such, cannot be used in complex shapes.
Innovaatio:
Metallurgists are coming up with new specifications of aluminum alloys that are specially designed to suit sand casting. These are rare-earth modified alloys that enhance fluidity and minimize cracking, and nanoparticle-hardened aluminum powders, which have better strength-to-weight ratios. Also, grain refinement processes by master alloys (e.g, Al-Ti-B) are being standardized in favour of a uniform microstructure of alloys and ensuring better mechanical properties after casting.
7. Digitalisaatio ja älykkäät valimot
Haaste:
Conventional foundries are basically guided with knowledge that is mostly experience-related and not real-time data, and hence, there is inconsistency and minimal traceability in the production.
Innovaatio:
Smart foundries are emerging due to the practical emergence of Industry 4.0 technologies. Such facilities utilize IoT sensors, cloud analytics, and digital twins to observe the temperatures, pressure, humidity, as well as mold conditions at different stages of the casting process. Information relating to different stages is embedded in centralized dashboards, which allows predicting maintenance, quality assurance, and continuous improvement. The digital twins, creating the virtual extended versions of the whole process of casting, can be used to optimize the process and trace the root causes without shutting down the production.
Päätelmä
Aluminum sand casting continues to play a critical role in industrial production, enabling the fabrication of both simple and complex parts with efficiency and economy. The process is made even more precise, sustainable, and flexible to suit the needs of modern manufacturing as the field of materials science and foundry technology advances. As an industry related to simulation, automation, and alloy research grows, reached the capacity of an aluminum sand casting foundry, a resurgence in this type of craft is overdue due to the demand for lightweight and high-performance metal parts.
Whether through the services of specialized aluminum sand casting services or the meticulous engineering behind sand casting aluminum parts,this technique will remain integral to industries that value structural integrity, design flexibility, and cost-effective production.
Usein kysytyt kysymykset: FAQ: Usein kysytyt kysymykset
1: Mitä on alumiinin hiekkavalu?
Aluminum sand casting is a process where molten aluminum is poured into sand molds to create complex metal parts. It can be perfectly used when low to medium volume production is needed and large parts are involved.
2: Missä hiekkavalettuja alumiiniosia käytetään?
Sand casting aluminum parts are commonly used in the automotive, aerospace, marine, and industrial sectors for components like housings, brackets, and engine parts.
3: Mitä minun pitäisi tehdä valitakseni sopivan alumiinihiekkavalimon?
Seek a foundry known as an aluminum sand foundry with wide quality management, engineering support, alloy knowledge, and other value-added capabilities such as machining and heat treatment.