Aluminum sand casting is one of the oldest and most versatile metal casting processes, widely used in modern manufacturing to produce complex, durable, and cost-effective components. Aluminum Sand casting Manufacturers can generate complex geometries with intricate features that would have otherwise been either impractical or unprofitable to machine out of solid material through pouring molten aluminum into prepared sand molds. This method is especially suitable in low to medium-volume production, prototyping, and high structural castings on applications spanning the aerospace, automotive, defence, and energy industries.
The most interesting about the sand-casting aluminum is that it is both flexible and functional. Aluminum has a very good strength versus weight, corrosion resistance, and recyclability, and thus makes it an excellent casting material. Together with the thermal resistance of sand and its high moulding capability, the process provides scalable production capability with excellent dimensional accuracy. Pattern design, the makeup of the mold, the quality of the melt, and gating design are key factors to the success of every casting.
An excellent foundry of aluminum sand castings has to control not only the classic facts in metal technology but also touch on innovations in the processes. The current facilities apply the latest technology to prevent defects and ensure the best performance of the casting by using 3D sand printing, simulation software, and real-time process monitoring. Precision-engineered and casting aluminum parts are now capable of meeting stringent engineering standards for safety, tolerance, and durability.
As demand grows for complex components with faster lead times and lower environmental impact, professional aluminum sand casting services must continue evolving. This article goes into the technical ins and outs of the process itself, its engineering workflow, materials, challenges, innovations, and so on.
The Fundamentals of Aluminum Sand Casting
At its core, aluminum sand casting involves pouring molten aluminum into a sand mold cavity, which is shaped by a pattern that replicates the final part’s geometry. When the aluminum solidifies, the sand mold is shaken off, leaving the cast piece. The process also has an outstanding dimensional flexibility and scalability capability in high-mix low-volume manufacturing conditions.
The process is based on the use of a non-permanent mould, sand, that may be recycled and re-utilized, minimizing the waste of materials and expenses. Sand molds most commonly consist of silica sand with a binder added, and the nature of the binder system generally influences considerably the resulting surface finish, dimensional accuracy, and rate of cooling.
The process of Flow in the Engineering of Sand Casting Aluminum
Sand casting aluminum is an engineering process that consists of a set of accurately calibrated activities that aim at transforming raw aluminum into specific, well-built, and accurately dimensioned parts. Both the material and mechanical expertise are required to be in-depth to make all of the stages of the process successful. The following is a step-by-step analysis of the way in which sand casting of aluminum is implemented professionally and technically.
1. Pattern Design and making
In the sand casting aluminum process, the initial step is designing and manufacturing the pattern, a physical copy of the final casting. The allowances that must be included in patterns are rather critical, such as shrinkage, draft, and machining stock. As aluminum contracts, during cooling patterns are laid out a little bigger than the finished component. The shrinkage rate of aluminum alloys is normally applied at 1.3 per cent; however, depending upon the alloy and the conditions of cooling, it may vary.
Vertical portions of moulds are given draft angles, normally a few degrees between 1 and 3, to ensure that the pattern can be removed easily in the sand mold, being careful not to destroy the cavity. Additional allowances (machining allowances) are included such that there is no adverse interaction between the post-processing and the final part. Patterns may be made out of wood, metal, resin, or even 3D-printed polymer materials, depending on the accuracy demands and the needs of the production volume.
2. Mold Making (Molding and Core Setting)
After preparing the pattern, the mold is to be prepared. For the sand cast, aluminum mold, there are two separate halves: the cope (upper half) and the drag (lower half). They are produced by stuffing the sand around the mold in a flask. Depending on the application, the sand is generally silica-based and is amalgamated with binders such as clay (green sand) or chemical resins (no-bake sand).
In case the part design has internal space and hollow parts, it necessitates the use of sand cores. They are placed in the mold cavity, after which the metal is poured. Cores can be fabricated using core boxes, and in precision production, they can be printed with greater precision using 3D sand printing. The exact footprint of the core is very important in order to have a rigid structure and adherence to the final part dimension.
3. The Design of the Gating System
The timeliness and effectiveness of the gating system formed are significant towards the success of the process of sand casting aluminum. This system consists of a pouring basin, sprue, runners, and gates, which coerce the impounded aluminum into the involvement of the mold. Adequate gating will prevent a lot of turbulence, minimize airlock, and also make sure that there is an even fill.
Risers (alternatively called feeders) are also required, and these can be seen as a reservoir of molten metal that offsets the direction of shrinkage that comes after solidification. Casting simulation software is usually utilized by engineers to study and optimize the gating and riser systems. Prediction takes place by using simulation tools such as MAGMASoft or ProCAST so that typical defects such as cold shuts, misruns, and shrinkage porosity can all be corrected virtually before any production takes place.
4. Cu Melting and Metal Treating
Aluminum is usually melted by a reverberatory furnace, a crucible furnace, or an induction furnace, and the choice depends on the batch volume, alloy needs, and the amount of energy needed. The melting temperature of pure aluminum is about 660 degrees Celsius (1220 Fahrenheit), although alloys can vary ever so slightly in melting point based on composition.
Gas absorption, specifically, the absorption of hydrogen gas, is one of the great technical difficulties during melting. Hot aluminum is very easy to take up the hydrogen either from the air moisture or from the charged figures. More than hydrogen, porosity occurs in the finished casting. As a response to this, the melt is exposed to degassing procedures, which frequently involve the introduction of passive gases (such as argon or nitrogen) which is pushed into the melt using a rotary impeller. Fluxing agents can also be added to remove the oxides and inclusions from the melt.
5. Fighting of Molten Metal
When the melted aluminum is cleaned and conditioned, it is then poured into the mold with use of the gating system. The pouring should be fully under control and continuous without mixing up the mold, and thus air entrapment and solidification at an early stage. Manual setups incorporate ladles that are operated by people trained on pouring height and rate. Robotic ladling is one of those steps that guarantee safe and high repeatability in automated systems.
The temperature of the pouring is usually 690-740 °C according to the alloy and the mold complexity. Pouring at low temperatures may cause cold shuts or incomplete fill, and pouring at high temperatures may cause more pickup in the gas and oxidation.
6. Solidification and Cooling
The solidification step is one of the most important steps of the process of casting aluminum with a sand casting method. When aluminum turns into a solid, it contracts, and the shrinkage should be taken care of during the gating and riser designs. The purposes of the controlled cooling are the uniform microstructure and the reduction of the internal stresses and shrinkage cavities.
Depending on the geometry at various areas of casting, and according to wall thickness, they have varying cool-down rates. Instead, there is the use of directional solidification, most often by designing the casting so that the casting is oriented such that solidification occurs thin to thick, which directs the shrinkage cavities to risers. To speed cooling in certain regions and thereby to regulate grain structure and minimise defects, one technique is to use chills, metal inserts in the mold.
7. Shakeout, cleaning, and fettling.
After the mold is removed successfully, the mold is shaken open after the casting has completely solidified in a process known as shakeout. Cutting or grinding is done mechanically or manually to remove the sand. The cutting is done at the casting and gating system and risers.
Casting usually comes out with sand residues on the surface and oxide deposits, and cleaning processes such as shot blasting, grinding, or even chemical pickling are carried out to remove these deposits. Fettling is also done in this phase, in which unnecessary metal is removed and thick surfaces are made finer. There is also the removal of any cores that the mold has used.
8. Heat Treatment and machining (In case necessary)
Many sand casting aluminum parts undergo post-casting heat treatment to improve their mechanical properties. Among the usual approaches are:
- T5/ T6 tempering of age hardening aluminium alloys (e.g. A356-T6), where the strength and hardness are substantially increased.
- Annealing, so as to get out stresses inside it and make it more ductile.
Precision machining can be required after heat treatment to meet final tolerances, in particular in those surfaces that mate with other parts or must be closely dimensioned.
Counter examples: CNC milling, drilling, and turning of sand-cast parts are common post-processes.
9. Quality Assurance and Inspection
The last step is to do a final check to make sure that the cast part has the right specifications as required. The following is the usual quality assurance of the sand casting type aluminum:
- Inspection based on dimension (CMM, Coordinate Measuring Machine, or laser or other scanning).
- Non-Destructive Testing (NDT) like X-ray radiography, ultrasonic testing, or dye penetrant inspection that reveal the internal or surface faults.
- Mechanical tests of tensile strength, elongation, and hardness, especially in the case of castings being used structurally.
- The inspection data has been logged to be able to trace the data and further improve the subsequent replications of the process.
Metallurgical Aspects of Aluminum Sand Casting
Aluminum alloys applied for sand casting can usually be divided into the following two groups: non-heat-treatable and heat-treatable alloys. Familiar alloys are A356, A319, and 319.1, selected according to the needs of strength, thermal conductivity, and resistance to corrosion. The cooling rates and alloying elements like silicon, magnesium, and copper have a large effect on the grain structure of the casting.
One of the most demanding aspects of the process of aluminum sand casting is that of porosity control. The solubility of hydrogen gas in aluminum is also very high in the liquid phase than in the solid phase, which tends to cause microporosity in the solidifying pool. The standard methods of limiting this challenge are vacuum degassing and inert gas flushing.
Materials Used in Aluminum Sand Casting
The materials used in aluminum sand casting are critical to the performance, manufacturability, and durability of the final product. They not only comprise the aluminum alloys but also different kinds of sand, binders, as well as auxiliary materials in the mold and core manufacture. Social-economic factors. By selecting each material, it is essential to reach a compromise on castability and mechanical properties, surface finish, and cost-effectiveness. The main material categories under which the process is performed are presented below in detail.
1. Leghe di alluminio
The selection of aluminum alloy is the key to any sand casting aluminum process. Various alloys offer various mechanical properties, corrosion, and thermal behavior. In general, these alloys fall under two broad categories: wrought (forged/rolled) and casting alloys. Sand casting also uses casting-grade aluminum alloys since they are best suited for casting, fluidity, and solidification.
Most Often, Cast Aluminum Alloys are:
A356 (Al-Si7-Mg):
This is one of the most popular alloys in the area of sand casting services for aluminum. It is extremely castable, has relatively good corrosion resistance, and can be heat-treated to the T6 (high strength, high ductility) temper, which renders it most useful. Age-hardening treatments are possible by the addition of magnesium.
319 (Al-Si-Cu-Mg):
Good wear resistance and machinability are also known for 319, which is applied in automotive applications and general engineering. But its corrosion resistance is worse than that of A356.
535 (Al-Mg):
It is an alloy with high magnesium content, and hence it has very good corrosion resistance as well as impact strength. It finds common use in aerospace and marine applications.
Aluminum-Silicon (Al-Si) Alloys:
These alloys have received recognition for their high fluidity and lower shrinkage, especially when used in complex components as sand-casting aluminum parts.
Additives and Grain Refiners:
To enhance casting quality, in order to reduce porosity and to enhance the mechanical properties, titanium-boron master alloys (e.g., AlTi5B1) may be added to provide grain refinement. Modification of the silicon stage in Al-Si alloys typically employs the use of strontium, which increases ductility and decreases hot tearing.
2. Sand Materials
In the method, the main molding material is sand in the process of the aluminum sand casting foundry. Its purpose is to create the mold cavity that the molten aluminum is poured into. The sand should be able to tolerate high temperature (above 700 o C), be dimensionally accurate, and also be able to withstand erosion by the stream of metal.
The Sand to be used:
Silica Sand:
The most frequently used and cheapest sand. It is good in terms of refractoriness as well as workability. But this contains problems on thermal expansion, which may result in casting defects such as veining or hot tears unless this is well-controlled.
Chromite Sand:
This sand possesses better thermal conductivity and thermal shock resistance; thus, it can be used in high-temperature investments as well as in thick-section castings of large piece work.
Zircon Sand:
Applied in applications where the accuracy concerning dimensions is of utmost importance. It is much more costly but has very low thermal expansion and high refractoriness.
The size of a sand grain:
Fine-grained sand gives out a smoother finish on the surface and affects the permeability. The size of coarse-grained sand raises permeability and mold strength; however, the final product could be rougher. With regard to part geometry and finish specifications, a compromise is usually chosen.
3. Binding and Additives
Aluminum sand casting: Sand used in the aluminum castings is held together using a binder, making a mold that is solid enough to hold under the pressure of molten aluminum. Binders are either organic or inorganic, and they are chosen depending on the sand system that is utilized.
Green Sand Binders:
Bentonite Clay:
A clay swelling which is used in a green sand system to offer plasticity and cohesion. It is mixed with water to form reusable molding material.
Water:
It is an activator in green sands and helps the bonding between the clay and compacts sand.
Chemically Bonded Sand Systems:
Furan Resin:
A natural bonding agent a high strength and good finishing. They are normally applied in a bake system.
- Phenolic Urethane Cold Box (PUCB) was the last product type.
- Has a great core strength and dimensional accuracy. Dietz is extensively employed in the production of cores.
Additives:
Probably the oldest mines in the world are the coal mines of this coal district; they extend to a depth of 2,200 feet or more, and have been known to continue next to the vein, towards the sea, where the coal is called sea-coal, or coal-dust.
Incorporated with green sand to enhance the black-color on the surface of the mold and eliminate defects in casting, such as metal penetration.
Iron Oxide:
It is useful to decrease veining and expansion faults in hot areas.
Graphite:
Enhances the fabrication of sand where it possesses high levels of sand flowability and mold release.
4. Core Materials
Internal hollows and intricate shapes in so-called sand casting aluminum parts are produced by cores. They are typically cast in high-purity silica sand, having a binder system identical to the mould but frequently more rigid and accurate.
Materials that are important in core production are:
- Silica sand ( high mesh )
- Binders (furan resin or PUCB)
- Vent wires or core vents, to enable the escape of the gas in casting
Binder jetting in 3D-printed sand cores is getting popular in high-tech foundries. These do away with the usage of core boxes and enable fast prototyping of complex geometries.
5. Mold coating and Mold washes
Refractory coatings are applied (or mold washes) to enhance the surface finish of the casting or to provide thermal and chemical protection to the mold or core.
Such common coating materials are:
Zircon-based coatings
Zircon-based coatings are also excellent in terms of their refractoriness and insulation properties in high-temperature aluminum alloys.
Graphite-based coatings:
Encourage easy casting and are applicable in chill zones.
Aluminosilicate-based:
The aluminosilicate-based coatings are general-purpose protective coatings that minimize surface flaws.
The process of applying these coatings is done through brushing, spraying, or dipping, and then one dries it before pouring the metal. They mitigate the danger of sand erosion, metal penetration, and gas-related development.
6. Other auxiliary and Process Materials
Other materials used in aluminum sand casting services include:
Fluxes:
To clean the melt and to take out the non-metallic inclusions. Depending on the type of alloy used, common ones are chloride-based or fluoride-type flux.
Degassing Tablets or Gases:
These may involve tablets of hexachloroethane or the like, though in contemporary foundries, argon gas degassing is favoured on environmental and safety grounds.
Probes, thermocouples, and Pyrometers:
Temperature sensors are available in the form of high-temperature alloys and ceramic materials for monitoring melt and mold conditions.
Sleeves and riser exothermic materials :
It is placed in risers to keep molten metal feed longer. These have insulating materials or exothermic materials that give out heat in solidification.
The Function of the Aluminum Sand Casting Foundry
The highly sophisticated casting foundry is the so-called aluminum sand casting, which has molding machines, core producing stations, melting furnaces, and inspection systems. Foundries are specialised in casting, maximum quality of the casted item, minimum cycle time, and maximum material efficiency. Developed foundries combine such digital tools as:
- Simulation Software: So-called simulation software (such as MAGMASoft and FLOW-3D Cast) simulates the filling and solidification of the mould and enables foundry engineers to fine-tune the gating design and pre-predict faults.
- Automatic Core: Complicated inner shapes could easily be created with new 3D-printed sand cores with the usage which diminishes the expenditure on tooling and time.
- Non-Destructive Testing (NDT): This involves the use of X-ray testing, ultrasound, as well as dye penetrant to ascertain the completeness of the part cast.
A successful aluminum sand casting foundry has a quality control system with all the global standards, such a ASTM B26, ISO 8062-3, and AMS 4218 to guarantee a stable quality of cast aluminum alloys.
Advantages of Aluminum Sand Casting Services
Professional aluminum sand casting services offer end-to-end casting solutions, including design consultation, rapid prototyping, tooling, and post-processing. These are OEM and tier-1 supplier part-sourcing services, in need of the fastest turnaround, custom part geometry, and functionality.
Some of them are the main advantages:
- Low Tooling Expenses: Sand casting has a low requirement for tooling costs compared to die casting, which makes it the best option for short production runs.
- Service: Service providers are advised to come up with customized alloys depending on the mechanical or thermal characteristics required.
- Rapid Prototyping: It is possible to prepare a prototype in days instead of weeks with the use of current digital pattern-making.
As industries demand faster product cycles and greater customization, high-quality aluminum sand casting services become invaluable partners in supply chains.
Precision and Performance in Sand Casting Aluminum Parts
Sand casting aluminum parts remains a cornerstone in the production of engine blocks, transmission housings, manifold covers, and aircraft components. The process can also handle simple and complex part geometries with wall thicknesses of between 3mm to 75mm, depending on the strength of the mold and the flowability of the alloy involved.
Key performance metrics for sand casting aluminum parts include:
- Dimensional Tolerance: Able to tolerate between 0 and 0.5 percent of their nominal values according to the quality of the molds.
- Surface Roughness: This is between 150 -500 RMS, although with secondary process, they can be finer.
- Resistenza meccanica: Tensile strengths are alloy and treatment dependent, and are typically between 170-300 millimeter of Pascal (MPa).
Engineers can decrease the amount of shrinkage defects and make uniform structures during the grain structure through carefully selected gating and riser systems.
Challenges and Innovations in Aluminum Sand Casting
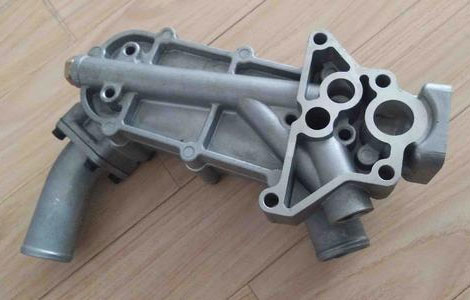
Although aluminum sand casting has stood the test of time as a versatile and cost-effective manufacturing method, it faces multiple technical and operational challenges that affect casting quality, production efficiency, and scalability. Luckily, the process is being transformed greatly with the help of new solution innovations as the industry faces these challenges with new tools and technologies. Here goes a further breakdown of both challenges that continue to plague the art of aluminum sand casting and emerging innovations that seem to have arisen in the field.
1. Melt quality and Gas Porosity
Challenge:
One of the most critical and persistent problems in aluminum sand casting is gas porosity, primarily due to hydrogen absorption. When molten, Aluminum has the tendency to absorb hydrogen gas, notably in the presence of moist conditions or under abuse by the utilization of contaminated charge materials. As the Metal cools, the solubility of Hydrogen falls, hence the gas precipitates, forming minute holes in the casting. Such pores seriously limit resistance to fatigue and sealing capacities as well as mechanical strength.
Innovation:
Solution to this problem has been solved by employing modern degassing technology in modern foundries, like rotary degassing technology, use of inert gases like argon or nitrogen. These systems stir the melt so as to bring more surface area and free up the trapped hydrogen. Moreover, flush rings in-line degassing systems are used to remove oxides and inclusions. Some of the plants are even putting up real-time gas monitoring sensors to evaluate the hydrogen’s state during melting and pouring.
2. Dimensional Sadness and Mold Sticking to it
Challenge:
Keeping strict dimensional tolerances with the method of sand casting aluminum is not easy because the sand mold is a variable thing. These geometric changes can be brought about by sand compaction, moisture content, as well as thermal expansion, among others, thus causing some parts that no longer be within their specifications. Also, the reusable patterns denote a higher probability of vibration to dimensional drift, and it is not considered over time.
Innovation:
To counter this, numerous foundries are utilizing digitally controlled molding machines that provide uniform pressure in the compaction of the molds and achieve a degree of uniformity in their mold quality. 3D sand print (binder jetting) is transforming the creation of molds, as it does not require a physical pattern. These cast molds are highly accurate to the micron level, suitable for prototyping and small manufacturing runs. In conjunction with casting simulation software, engineers are able to simulate dimensional changes on cooling and offset the changes at pattern design.
3. Light automation and heavy Labor dependence
Challenge:
Traditional aluminum sand casting processes are labor-intensive, particularly in mold preparation, pouring, and finishing. The manual operations not only curtail the throughput but also the variability of the casting. In addition, the use of skilled labor may prove to be a bottleneck, especially in areas where there is a scarcity of labor.
Innovation:
Robotic automation is changing repetitive and risky operations like the actuality of molds, pouring, and grinding. The collaboration robots (cobots) would have the capacity to collaborate with people in fundamental assembly and extraction of castings. Foundries are also embracing automated pouring installations that have laser sensors and vision systems to allow a balance in pouring rates and the temperature of pouring to be controlled with accuracy. Such advancements not only contribute to the efficiency of production but also to safety and unification in the workplace.
4. Root Cause Prediction of Casting Defects
Challenge:
Concerns over casting defects like cold shuts, hot tears, shrinkage holes, and inclusions continue to be a major contributory factor to material wastage and product defects. The primary cause of these defects needs to be identified and removed to prevent their reoccurrence; this would demand an in-depth knowledge of fluid dynamics, thermo gradients, and alloy dynamics- aspects that are not readily available in any foundry without special measures.
Innovation:
Sophisticated computational fluid dynamics (CFD) and solidification modeling packages have recently become available that enable the engineer to simulate the complete casting process in a virtual world. FLOW-3D Cast, ProCAST, and MAGMASoft computer software are some of the software to forecast the molten steel defects, and where defects are likely to form before pouring any metal. The tools are used to optimize gating systems, riser placements, and cooling strategies to get castings that are free of defects. Further, machine learning models are being worked on where the defect data of the past is used to analyze and give real-time recommendations on the process to be adjusted.
5. Sustainability of the Environment and the Management of Waste
Challenge:
Aluminum sand casting generates waste in the form of spent sand, metal dross, flux residue, and off-spec parts. The disposal of sand, especially, presents a problem as chemically bonded sand might not be easy to recycle. Also, high energy usage in the melting process adds much to the carbon footprint in the foundry processes.
Innovation:
Most progressive foundries are investing in closed-loop sand reclamation systems, which recycle previously used sand through thermo-mechanical processes. Such systems cut down on the number of dumps, as well as the cost of raw materials. In the energy sense, the induction melting furnaces are more efficient and have minimal emissions than their traditional analogs, gas-fired reverberatory furnaces. Solar power, recycling of waste heat, and real-time monitoring of energy are also assisting foundries in cutting down environmental impact as they comply with the increasingly strict regulatory requirements.
6. Alloy Imposed Restrictions & Difficulty of Metallurgy
Challenge:
The use of applicable aluminum alloys in sand casting is associated with a trade-off between castability, mechanical properties, and heat-treatability. Certain high-performance alloys have poor fluidity or are prone to hot tearing during solidification and, as such, cannot be used in complex shapes.
Innovation:
Metallurgists are coming up with new specifications of aluminum alloys that are specially designed to suit sand casting. These are rare-earth modified alloys that enhance fluidity and minimize cracking, and nanoparticle-hardened aluminum powders, which have better strength-to-weight ratios. Also, grain refinement processes by master alloys (e.g, Al-Ti-B) are being standardized in favour of a uniform microstructure of alloys and ensuring better mechanical properties after casting.
7. Digitalization and intelligent Foundries
Challenge:
Conventional foundries are basically guided with knowledge that is mostly experience-related and not real-time data, and hence, there is inconsistency and minimal traceability in the production.
Innovation:
Smart foundries are emerging due to the practical emergence of Industry 4.0 technologies. Such facilities utilize IoT sensors, cloud analytics, and digital twins to observe the temperatures, pressure, humidity, as well as mold conditions at different stages of the casting process. Information relating to different stages is embedded in centralized dashboards, which allows predicting maintenance, quality assurance, and continuous improvement. The digital twins, creating the virtual extended versions of the whole process of casting, can be used to optimize the process and trace the root causes without shutting down the production.
Conclusione
Aluminum sand casting continues to play a critical role in industrial production, enabling the fabrication of both simple and complex parts with efficiency and economy. The process is made even more precise, sustainable, and flexible to suit the needs of modern manufacturing as the field of materials science and foundry technology advances. As an industry related to simulation, automation, and alloy research grows, reached the capacity of an aluminum sand casting foundry, a resurgence in this type of craft is overdue due to the demand for lightweight and high-performance metal parts.
Whether through the services of specialized aluminum sand casting services or the meticulous engineering behind sand casting aluminum parts,this technique will remain integral to industries that value structural integrity, design flexibility, and cost-effective production.
FAQs: Frequently Asked Questions
1: What is aluminum sand casting?
Aluminum sand casting is a process where molten aluminum is poured into sand molds to create complex metal parts. It can be perfectly used when low to medium volume production is needed and large parts are involved.
2: Where are sand casting aluminum parts used?
Sand casting aluminum parts are commonly used in the automotive, aerospace, marine, and industrial sectors for components like housings, brackets, and engine parts.
3: What should I do to select an appropriate aluminum sand casting foundry?
Seek a foundry known as an aluminum sand foundry with wide quality management, engineering support, alloy knowledge, and other value-added capabilities such as machining and heat treatment.