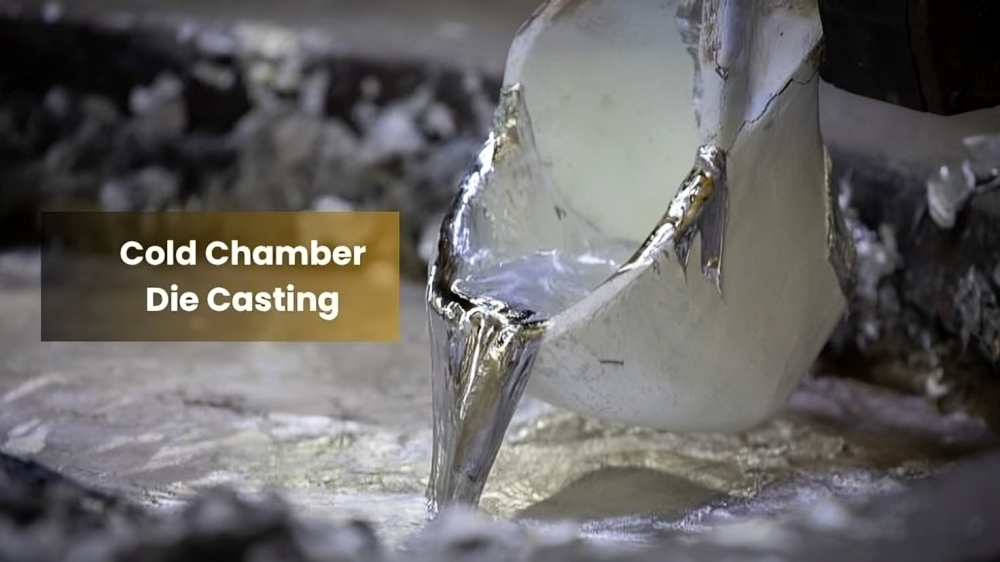
Cold Chamber Die Casting is a precision type of manufacturing technique applied in the manufacture of complicated metal components characterized by high levels of strength and precision. This process can best be used in metals having a high threshold of the melting point, like aluminum, brass, and copper alloys. Cold chamber die casting systems are not placed into molten metal like a hot chamber die casting system; instead, the metal is put into the cold chamber die casting machine by manually ladling metal into the cold chamber die casting machine after it is melted in another furnace. The arrangement wears less on the machine and uses alloys that are tougher.
Among the important factors that make companies opt to use this method are the special cold chamber die casting advantages and disadvantages. It has top dimensional accuracy, smooth surface finishes, as well as long cycle times. Nevertheless, its strength and durability of the constituents are its favorites in the automotive, aerospace, and electronic markets.
The difference between hot and cold chamber die casting is crucial to make the right choice of the process. Hot chamber die casting is more rapid and applied to metals of low-melting point, such as zinc, whereas the cold chamber die casting system is designed to handle higher temperatures and stronger metals. Manufacturers will also be able to manufacture long-lasting and reliable parts with this process that have a high degree of precision in their specifications.
In the present article, we are going to discuss the principle of operation of cold chamber die casting, its main parts, the nature of the metal employed, and technological parameters of cold chamber die casting, including clamping force and cycle time. The cold chamber die casting advantages and disadvantages will also be considered to provide you with a full picture of this important manufacturing process.
What is the Cold Chamber Die Casting?
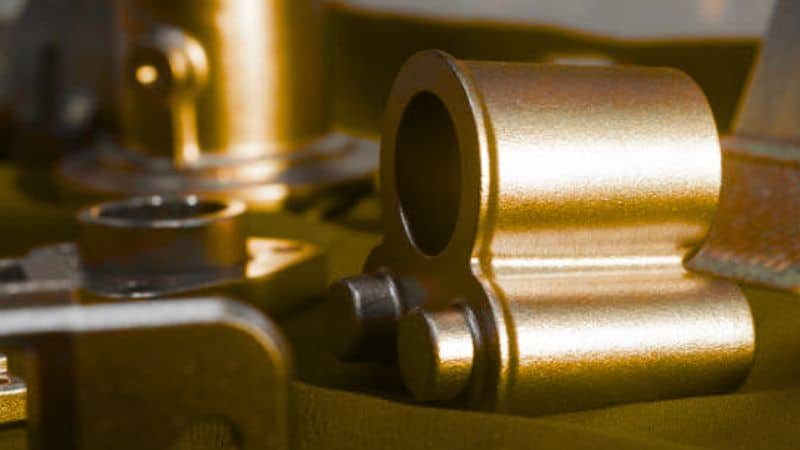
コールド・チャンバー・ダイカスト: A cold chamber die casting process is a metal casting process where molten metal is ladled either manually or automatically into a separate cold chamber outside the injection system. Thereafter, the metal is pushed with high pressure into a mold cavity, which causes the metal to cool and crystallize in the desired shape.
It is usually applied to metal with a large melting point, like brass, aluminum, and copper alloys. The purpose of avoiding corrosion and thermal fatigue that can result in improper working of components of the injection system, unlike in the hot chamber ダイカストプロセス, where the injection mechanism is suspended in molten metal, the cold chamber process keeps the injection facilities segregated.
The application of the practice of the latter, i.e., Cold Chamber Die Casting, is especially advantageous, where the metals used would harm the components, contacting them. High pressure can be used in the injection process itself, and denser, stronger components with a brilliant surface finish and dimensional stability would be possible.
Die Casting Process- Step by Step
The object of the Cold Chamber Die Casting technique is to make highly accurate and hard metal parts that are frequently composed of alloys that have melt-points that are at high temperatures, such as aluminum and brass. Let us have a step-by-step breakdown of how it works:
1. The External Furnace is used to melt the Metal
The process is similar to that of hot chamber casting except that the melting of metal is done in a separate furnace outside. This is required in that the molten metal in the cold chamber casting will cause a high level of heat to be experienced internally that cannot be handled. The metal is melted, after which it is able to be transferred into the casting machine.
2. Pouring the molten metal into the Shot Sleeve
Thereafter, the molten metal is ladled into the shot sleeve in the die casting machine. This is manually done or arm-driven. The shot sleeve is a strong, resistant to heat tube into which the metal rests and is later injected. This should be taken very fast to prevent premature solidification.
3. Plunger forces the metal into the die.
A steel plunger travels into the shot sleeve and presses the molten metal at high pressure in the die cavities. The force makes sure that the metal fills the mold even in any complicated pattern or with a very thin wall, and decreases the chances of any flaws, such as air pockets.
4. There is the Solidification of Metal within the Die
When the mold is filled, the metal starts cooling and solidifying within the die. This solidification step is very important in coming up with a good and precise part. The cooling time is dependent on the part metal, part thickness, and die temperature.
5. The Brass Die and Ejector Pins Force-Out the Casting
When the part has solidified, the clamping unit of the machine opens the die, and ejection pins force the casting out of the mold cavity. The portion is then moved to a cooler station or a trimming station.
6. Removal of Flash (Removal of Excess Metal)
There is some over metal on the sides called flash that is around the edges of the casting where the halves of the die come together. This is then removed by mechanical trimming, grinding, or machining, depending on what the finish requires. This will prevent the final works from being below the intended shape and tolerance.
7. Die cycle reset and Lubrication
The die is washed and greased before entering the next cycle in order to be of good quality and avoid sticking. When the oiling is done, the die is again clamped, and the machine is switched to reset for more cycles.
8. Quality Inspection and finishing
This is a complete part that is checked to ensure quality defects do not exist, like cracks, shrinkage, or abnormalities on the surface. Depending on the end-use requirement of the part, it can be subjected to additional machining, surface treatment, or assembled (if required).
Metals to be used in the process of cold chamber die casting
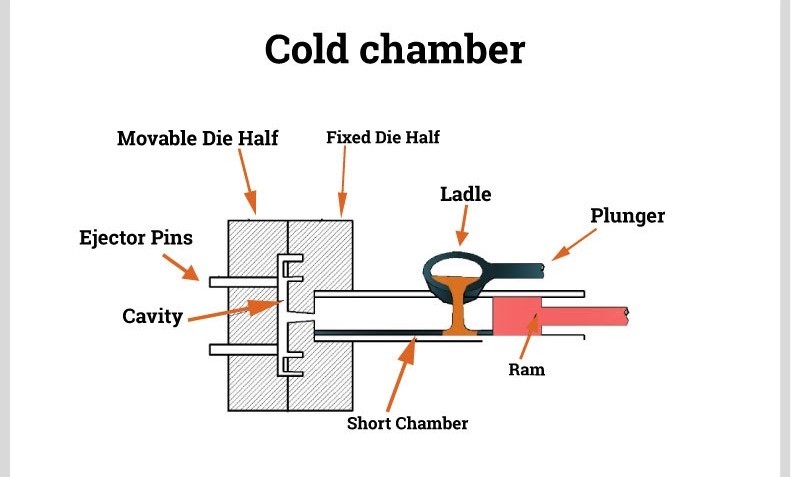
High melting metals will benefit from the use of the Cold Chamber Die Casting. Such metals are very strong and resistant to heat as they are very welcoming to structures. The following metals are commonly used during this process
アルミニウム合金
The most venerable metal in cold chamber die casting is aluminum. It is light, resistant to corrosion, and exhibits a high strength-to-weight ratio. Aluminum components are used in auto, aerospace, and electronics because those areas require precision and durability.
マグネシウム合金
The die casting lightest structural metal is magnesium. It is used because of its strength and its ability to dampen vibration. Aerospace and electronics magnesium alloys are somewhat cheaper to cast in cold chamber molds, but many are more typically cast in hot chamber systems.
Brass and copper Alloys
Parts with low resistivity and corrosion protection are made of copper and brass alloy. The metals are suitable for plumbing items, marine equipment, and electrical connectors. They are extremely durable and wear-resistant, which suggests their suitability in extreme environments.
Zinc-Aluminum ( Z A )Alloys
To enhance strength and fluidity, ZA alloys mix zinc with larger amounts of aluminum. In cold chamber casting, these alloys find application where fine surface finishing and high strength to withstand load are required (washing machine hardware, gearing, and ornamental pieces).
Specialty Alloys
Specially designed applications might necessitate special alloys, including nickel-base or titanium-base alloys. They find their application in such industries as aerospace or medical equipment, where their ability to work under a high level of stress is significant. They are, however, less prevalent because they are expensive and complex.
The table is given below
The following table is clean and clear with the properties of metals of everyone who uses Cold Chamber Die Casting profiles, their densities of these metals, their melting point, main characteristics, and their uses:
Metal | 密度 (g/cm³) | Melting Point (°C) | Main Characteristics | 代表的なアプリケーション |
アルミニウム合金 | 2.7 | ~660 | Lightweight, corrosion-resistant, good conductivity | Automotive parts, electronics casings, aerospace components |
マグネシウム合金 | 1.7 | ~650 | Ultra-lightweight, good strength-to-weight ratio | Aerospace brackets, mobile devices, and structural frames |
Copper Alloys | 8.9 | ~1085 | Excellent electrical/thermal conductivity, corrosion-resistant | Electrical connectors, plumbing fittings, and marine hardware |
真鍮 | ~8.4 | ~900–940 | Strong, corrosion-resistant, good machinability | Decorative hardware, valves, gears |
Zinc-Aluminum (ZA) | ~5.0 | ~380–500 | Good surface finish, wear resistance, and easy to cast | Industrial components, furniture fittings, and pump housings |
Nickel/Titanium Alloys | 8.0–8.9 | 1300+ | High strength, extreme temperature resistance | Aerospace, defense, specialized medical components |
Cold Chamber Die Casting Machine Components
A cold chamber die casting machine is a sophisticated machine that processes or deals with hot molten metals such as aluminum, brass, and magnesium. All the components are collaborative and make sure to provide accurate, fast, and consistent metal casting. The main components and their roles are given below:
1. Furnace (External Melting Unit)
In cold chamber die casting, the furnace is external, unlike hot chamber systems. In this independent area, molten metal is melted and subsequently manually or automatically transferred to the shot sleeve. This segregates the molten metal so that it does not contact sensitive internal parts, and it enables high-melting-point alloy handling.
2. Shot Sleeve
A horizontal steel tube called the shot sleeve is used, and the molten metal is poured into it before injection. It contains the molten metal temporarily and directs it to flow into the mould cavity when pressure is exerted by the plunger. The shot sleeve should be able to withstand the heat and abrasion at every casting cycle.
3. Plunger and plunger Rod
A plunger is a piston-like object (having the shape of a rod) that forces the molten metal out of the shot sleeve and into the mold. It is attached to a rod and it moves at high speed and power, and the cavity is filled at high speed to reduce the possibility of defects such as porosity or cold shuts.
4. Die or Mold
The final product is shaped with the help of the die. It consists of two halves, which are the movable half (ejector die) and the fixed half (cover die). There are complicated cooling, air vent, and metal flow internal channels in the die. Good die design will guarantee the accuracy of dimensions and a smooth finish.
5.クランプユニット
This unit maintains the die halves in contact at high-pressure injection. It subjects it to thousands of pounds of pressure so that the molten metal does not leak. When solidification has been achieved, the clamping unit moves to open the die to be able to eject the finished part.
6. Ejection System
Once the metal has solidified within the die, the part is ejected out of the mold by ejector pins or ejector mechanisms. These pins are nicely set in a way such that they do not destroy the casted object. They have a high volume production, which is usually automated and has part-detecting sensors.
7.冷却システム
There is a cooling system, which implies water or oil channels within the die to regulate temperature. It assists in controlling solidification time in the piece of casting and cuts down on the cycle time. Good cooling avoids overheating of the die and assures good part uniformity.
8. Hydraulic and Control Systems
The modern cold chamber die casting machines are equipped with cooperative hydraulic systems to regulate the movement of the plunger, clamping unit, as well as ejection system. Computerized control systems monitor these and precisely control speed, pressure, time, and temperature of injection into the die.
9. Lubrication System
Each cycle, lubricants are sprayed onto the die surfaces and shot sleeve to minimize friction, enhance the movement of metal, and avoid sticking. Automatic lubrication systems. The automatic lubrication systems are used in high-volume environments where consistency is sought and minimum time is spent by the machine.
10. Safety Devices and Monitoring Devices
Safety, operators are protected as cold chamber machines have safety interlocks, emergency stops, and temperature sensors to guarantee functional operation. The monitoring systems would offer real-time records on the performance of machines and early identification of problems.
What Does it Mean by Clamping Force and Cycle Time?
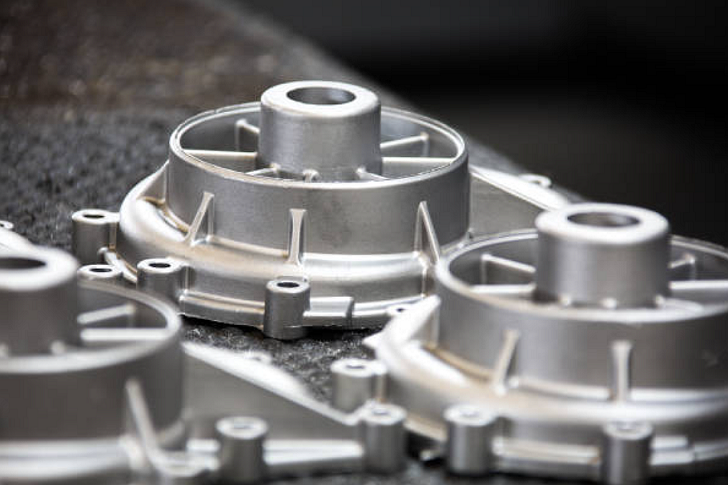
Cycle time and clamping force are the performance parameters necessary in the case of Cold chamber die casting. Directly, they impact part quality, speed of production, and machine efficiency. Getting to know more about such terms assists manufacturers in maximizing production and minimizing defects.
Clamping Force
The clamping force is the pressure to maintain the two halves of the die closed when the molten metal is injected. The molten metal is poured into a die with very high pressure (sometimes 10,000 psi or even more) in cold chamber die casting, and therefore, the die has to be locked firmly so as to prevent separation or leakage.
- Depending on the size and complexity of a part, clamping force is measured in tons, and an average of 100-plus to more than 3,000 tons is suggested.
- The clamp force required is based on the area of the casting, in projection, and on the injection pressure.
- When the force applied is insufficient, molten metal can escape at the parting line, creating defects called flash.
- In case it is too large, the machine might be subjected to unnecessary wear, or a part might become deformed by overcompression.
- The appropriate clamping force makes clean and precise castings, with tight tolerances.
サイクルタイム
Cycle time is the amount of time required to cast using a complete cycle of the machine, i.e. when the machine is injecting to when the next machine is injecting. In cold chamber die casting, the cycle will comprise:
- Pouring of metal into the shot sleeve
- Filling of metal into the die. Injection of the metal into the die
- The part cooling and solidification: Cooling and solidification of the part
- The opening and the ejection of the part
- The lubing and loading for the next bang
The common cold chamber cycle time is between 30 seconds and 2 minutes, and this is based on the alloy, part thickness, and part complexity. The smaller the cycles, the more production will take place, although there is a danger of not filling fully or cooling properly. Longer cycles are better in terms of casting but lower in terms of output and cost. In a highly volume manufacturing environment, it is important to optimize cycle time in order to maintain equilibrium between quality and efficiency.
The reasons why these are important are:
A die casting machine should produce sufficient clamping force to withstand the injection pressure of molten metal without the opening of the die. Meanwhile, there is a good optimized cycle time to ensure a quick production without difficulty in casting.
All these combine to have a direct impact on the following factors:
- Productivity
- Part consistency
- Operational costs
- Tooling life
Advantages and Disadvantages of Cold Chamber Die Casting
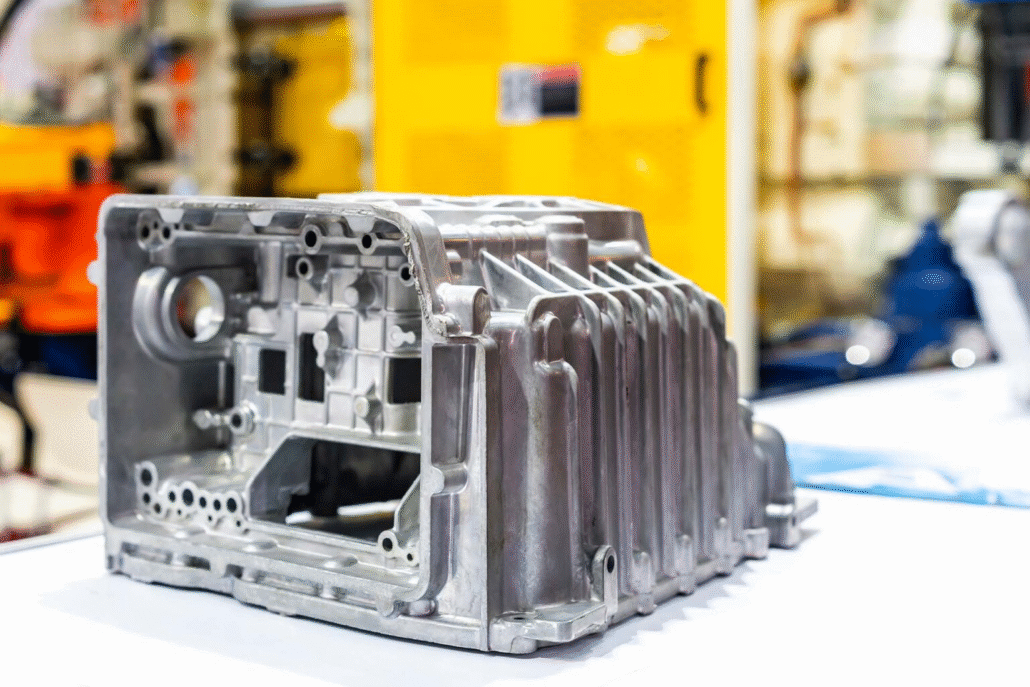
コールド・チャンバー・ダイカスト: Cold Chamber Die Casting is an ideal method of manufacturing complex and strong metal components of high melting point alloys such as aluminum, magnesium, and copper. Although this is a very efficient method in industrial applications, it has particular strengths and weaknesses. The cold chamber die casting advantages and disadvantages, let us take a look at them in detail.
The benefits of Cold Chamber Die casting
1. The Perfect Match with High-Temperature Metals
Among the cold chamber die casting benefits is that it has fairly high melting alloys that include aluminum, brass, and copper. These metals cannot be used in the hot chambers machine since they would either corrode or break the parts of the injection. These harder alloys can be processed in the cold chamber process that has an external melting system.
2. Super Dimensional Precision and Repeatability
Cold chamber machines cast parts of the highest precision and tight tolerance, and in many cases, need little machining after casting. This is particularly in need when it comes to such industries as aerospace or automotive, where even minor deviations may cause either performance problems or even safety problems. High-pressure injection makes the complex shapes and thin-walled designs accurately detailed, cycle to cycle.
3. Greater Mechanical strength
The other advantage is that parts made in this process have a dense, fine structure. High pressure and speed of die-filling enable molten metal to adhere to the mold shape completely, removing porosities and microcracks. It leads to components, which are not only dimensionally stable but which are also robust enough to resist mechanical load.
4. Corrosion and Heating resistance
Metals such as aluminum and magnesium are naturally corrosion resistant, which makes them suitable for use in areas under wet conditions or even chemicals. Another advantage is that these materials preserve their structure at high temperatures, and this can be useful in engine parts, heat sinks, and electronic equipment housing.
5. Large-Scale Preproduction Automation-Friendly
Robotic arms can be fitted on cold chamber die casting machines, auto ladling systems, die spraying systems, and parts that eject automatically. The integration fosters effective and quick manufacture of thousands of parts, with quality being maintained. Although it may have a heavy initial investment but the fact that the process can easily be automated the resulting costs can be lower per unit.
The Cold Chamber Die Casting Downsides
1. Increased Cycle Time
The cold chamber is slower as compared to the hot chamber die casting process. The cycle requires either manual or robotic pouring of molten metal into the shot sleeve, and that costs time and decreases the number of parts that could be produced per hour. This might not be suitable when the production lines are very fast.
2. Increased Initial and Operating costs
Cold chamber machines usually cost more than the other kinds because they have a heavy-duty design and the necessity to have an outside furnace. The cost of operations is also raised due to the energy consumed in melting the metal separately and the use of more handling paraphernalia and workforce.
3. Porosity and Oxidation Possibility Risk
Since the molten metal is moved through open air and injected, it comes in contact with oxygen, and this can be subjected to oxidation. During the injection process, the air could also remain entrapped, creating gas porosity. Unless controlled by process control and die design, these defects may deteriorate the strength and appearance of the finished casting.
4. There are Upgraded Maintenance Requirements
The shot sleeves, plunger, and dies, due to the increased temperatures of operation and abrasive alloys, wear out quicker. Maintenance requirements are more Therefore, maintenance requirements are more often crucial to avoid casting faults as well as unplanned shutdowns.
5. Unsuitable with Alloys of Low Melting Points
Metals that melt at comparatively lower temperatures, such as zinc or lead, will not be cast well using cold chamber casting. Such materials are more appropriately dealt with through hot chamber casting, which is quicker, more cost-effective, and more appropriate in the short-run or intricate part manufacturing with low melting alloys.
Uses of Cold Chamber die casting
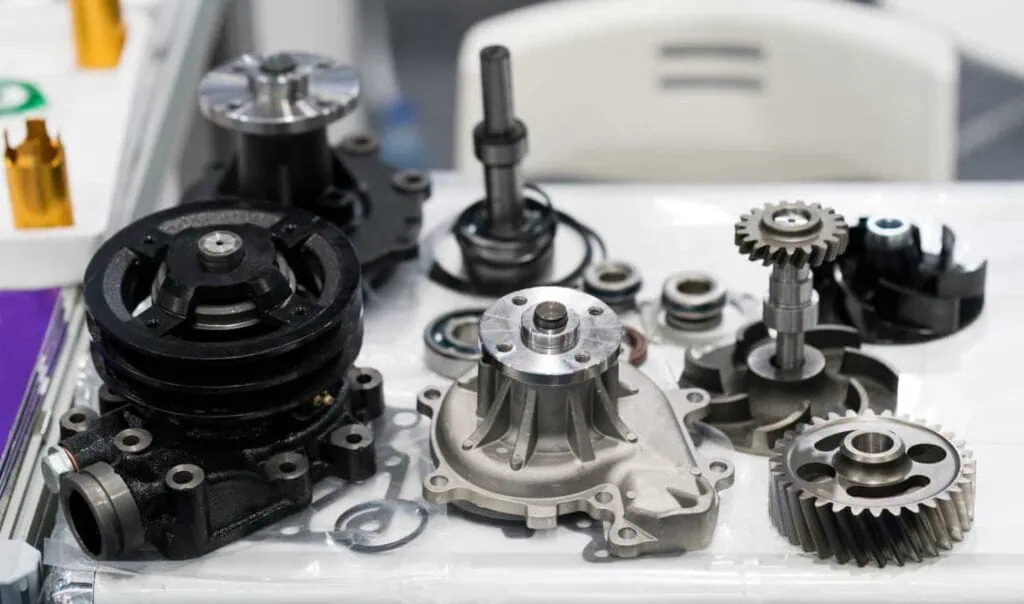
The process has a wide range of applications in a number of challenging sectors because of its capacity to synthesize robust yet lighter products. Application areas. Some important areas of application are:
- 自動車: Housing and engine blocks, transmission parts, and structural components.
- 航空宇宙 Light Components, and often have fine tolerances.
- コンシューマー・エレクトロニクス Casing and brackets in which the cosmetic and precision are of interest.
- Heat-Resisting and Corrosion-Resisting parts: Industrial Equipment.
What makes the Cold Chamber Die Casting especially useful are its repeatability and predictability, crucial when it comes to the safety of the product and its structural integrity, and its long-term endurance.
Difference between a Hot and Cold Chamber Die Casting
Die casting is an effective process that is employed in contemporary production as a great way of ensuring the production of good-quality metal parts in a very short period and with high precision. Normally, there are two primary forms of the die casting systems, the first is the hot chamber and the second is the cold chamber. The hot and cold chamber die casting varieties differ, and you must learn how to understand which one suits your specifications, rate of production, and suitability of the material with the design.
1. Metal Compatibility
The significant distinguishing appeal between hot chamber die casting and cold chamber die casting is the nature of the metals to be used by either machine. Hot chamber die casting applies to alloys with a low melting point, such as zinc, lead, and tin. Such metals will avoid damaging the interior of the machine.The cold chamber die casting, however, is used with alloys that have high melting points like copper, aluminum, and magnesium. These are metals that will need a stronger setup, since otherwise they are bound to ruin the parts of a hot chamber machine that are submerged in water.
2. Metal Injection Process
Hot chamber casting: The melt is made in a built-in furnace component of the machine. A metal feed system is immersed in the molten metal; it injects the molten metal directly into the die cavity.
Cold chamber casting entails a second furnace to liquefy the metal. The molten metal is later ladled either by hand or automatically into the shot sleeve, a nd then it is forced into the die. This distinction between loading and injecting is a characteristic component of the distinction between hot and cold chamber die casting.
3. Speed of production and Cycle Time
Hot chamber die casting tends to be faster and has shorter cycle times. The machine has the metal within easy reach, eliminating time wastage between shots. This makes it very convenient in high-scale manufacture where speed of production is of the essence.
Cold chamber die casting has a higher cycle time as it takes more time for ladling by hand or robot, or the period of solidifying. It is, however, best applied in manufacturing parts that have to be stronger, less prone to corrosion, and in terms of dimension.
4. Design of equipment and costs
Hot chamber die casting. Hot chamber machines are generally cheaper and smaller since they do not need a melting furnace. They also require fewer handling equipment. Nonetheless, they can only be utilized with metals that have low melting points and are non-corrosive.
Cold chamber die casting: Systems with cold chambers are bigger and more intricate, using external furnaces and transfer been through arms or robots of the molten metal. They are more flexible in terms of acceptance of stronger metals, but cost more initially than most other forms of packaging. It is believed that they are a more secure investment in the aerospace, automotive, and electronics industries.
5. Quality of Part and Usage
Both systems yield high-quality parts; however,,r cold chamber casting is usually favoured when complex shapes or parts that need to carry loads or face exposure to the environment are required. Smaller, detailed castings such as electrical connectors, locks, and consumer hardware are more typically done through hot chamber casting.
Surface finishing and porosity level of the parts are also factors in the difference between the hot and the cold chamber die casting. Hot chamber systems can be smoother and cause less porosity because of faster injection, but at the cost of slower injection, are weaker and more resistant to heat than cold chamber casting.
The Reasons Manufacturers Use Cold Chamber Die Casting
Although slower cycle times are a trademark of cold chamber systems rather than hot chamber systems, the method may still be favoured by many manufacturers, due to several factors:
- Material Flexibility: The technology is flexible to facilitate a large variety of tough metals resistant to corrosion.
- Better Part Quality: When parts are under higher pressures, much greater control is found, causing them to be denser and more consistent.
- Cost-Efficiency in large volumes: This may be costly to set up and to tool, but the cost per unit is dramatically reduced in large runs.
When combined with automated processes, the process can be scaled easily, keeping up high-quality levels and a low level of scrap.
Trends In Cold Chamber Die Casting in the Future
Due to the constant demand in industries needing lighter, stronger, and more sustainable components, even the process of Cold Chamber Die Casting is changing. This technique is being enabled by new advances in die materials, automation, and simulation software to expand it to new levels of performance.
Some of the trends in the future will be:
- Advanced Cooling Systems: To achieve swift cycles and die life span.
- AI and IoT: To have smarter monitoring and predictive maintenance.
- Eco-Friendly Alloys: Consume recycled material to minimize environmental waste.
These are some of the innovations that are meant to enhance the use of less energy, minimize wastage, and also work on overall efficiency, which would make the whole process even more appealing to the global manufacturers.
結論
In a concise recount, the Cold Chamber Die Casting is an essential method of producing powerful, accurate, and dense pieces that are formed out of metals having a high melting point. Its capability to work with such materials as aluminum, magnesium, and brass makes it indispensable in areas where quality and durability are necessary in the industry. The procedure itself may not be quite as fast as a hot chamber process, but in most cases, the result is worth the stopovers.
By comprehending the meaning of the difference between hot and cold chamber die casting, one understands the reason why cold chamber machines are favourable over those metals that would destroy the internal processes of a hot chamber machine. The difference with the machine is that it has an external furnace and metal is introduced to the shot sleeve manually, which maintains its life span, and makes it suitable for casting use.
Although there are some limitations, a profound understanding of the advantages and disadvantages of cold chamber die casting lets the manufacturers make proper decisions. The process provides greater strength, structural integrity, and design versatility, which are all important aspects of high-performance applications.
With the development of manufacturing technology, cold chamber die casting has maintained a very important role in the production of all kinds of items, including parts of an engine or even recent consumer electronics. As a manufacturer, an engineer, or a student, being familiar with the process is the key to success in the current paradigm of metalworking and product designing.
よくある質問
1. What is the use of the Cold Chamber Die Casting?
The term, Cold Chamber Die Casting, is usually applied in the manufacture of strong and complex metal components such as aluminum, magnesium, and copper. It is common in the car, aerospace, and electronics industries.
2. What are the cold chamber die casting advantages and disadvantages?
The benefits are that it is strong, has good dimensional accuracy, and is appropriate for high-melting-point metals. Its drawbacks are slow cycle times and expensive equipment, over that of the hot chamber methods.
3. What is a hot chamber and a cold chamber die casting?
The difference between the hot to cold chamber die casting is in the metal injection process. Hot chamber machines submerge the injector in melted metal, colder chamber machines have an outside furnace, and pouring molten metal by hand.
4. Which metals can be Cold Chamber Die Casting?
Light metals are best suited, such as aluminum alloys, brass, copper, and some magnesium alloys, which have high melting points and outstanding structural features.
5. What is the cycle time of cold Chamber Die Casting?
It depends on the part complexity and size, and usually takes an average of 30 seconds to 2 minutes, however, depending on the type of metal used.