
Оглавление
ToggleФормы для литья под давлением: Постоянство и стабильность
Литье под давлением, краеугольный камень современного производства, славится своей точностью, долговечностью и однородностью. В основе этого процесса лежит форма для литья под давлением - важнейший инструмент, определяющий качество и эффективность конечного продукта. Компания TheDieCasting.com гордится тем, что поставляет первоклассные формы для литья алюминия под давлением и решения по оснастке для литья под высоким давлением для отраслей промышленности по всему миру. Давайте погрузимся в сложный мир литья под давлением и узнаем, как мы неизменно добиваемся совершенства в качестве ведущего производителя форм для литья под давлением.
Что такое пресс-форма для литья под давлением?
Литейная форма - это специально разработанный инструмент, используемый в процессе литья под давлением для придания расплавленному металлу формы точных компонентов. Эта форма может быть сконструирована из двух половин, называемых полостью и сердцевиной, обе из которых специально спроектированы и разработаны для актуализации желаемой формы продукции. Благодаря высокому давлению расплавленный металл заполняет полость формы и создает высокоточную и тонкую отделку поверхности разрабатываемых деталей.
Наш опыт в качестве производителя литейной оснастки позволяет компании TheDieCasting.com создавать формы, отвечающие специфическим требованиям различных отраслей промышленности. Наши формы играют ключевую роль в продвижении и производственном процессе в автомобильной промышленности, бытовой электронике и различных других отраслях.
Цена пресс-формы для литья под давлением
Разблокируйте высокопроизводительные и экономически эффективные решения для ваших литьевых форм
Получить предложение
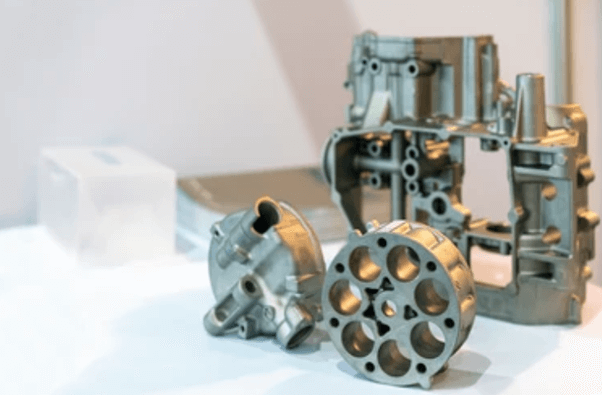
Роль материалов в пресс-форме для литья под давлением
В частности, важно выбрать подходящий материал для формы, которая будет использоваться при создании бетонных конструкций. Использование инструментальной стали или другого специализированного сплава является обычным делом из-за требований к высокому давлению и экстремальным температурам в процессе литья под давлением. Наша команда TheDieCasting.com гарантирует, что каждая созданная нами форма для литья алюминия под давлением будет рассчитана на жесткие условия производства и обеспечит стабильные результаты в течение длительного срока службы.
Используя высокотехнологичные материалы, мы помогаем покупателям сократить расходы и повысить долговечность их производственных линий. Такое внимание к качеству материалов выделяет нас как надежного производителя форм для литья под давлением.
Виды оснастки для литья под давлением
Различные решения по оснастке используются для решения сложных задач в промышленности с применением процесса литья под давлением. Две наиболее значимые категории - это оснастка для литья под высоким давлением и оснастка для традиционного литья под давлением.
Оснастка для литья под высоким давлением
Оснастка для литья под высоким давлением предназначена для процессов, в которых расплавленный металл впрыскивается в форму под очень высоким давлением. Этот метод отлично подходит для создания сложных форм с хорошей точностью размеров в эпоксидных деталях. Компания TheDieCasting.com специализируется на изготовлении форм для литья под высоким давлением, которые обеспечивают быстрое время цикла, минимальную пористость и превосходную прочность готовых изделий.
Она используется для производства высокопроизводительных компонентов и других электронных приложений в автомобильной и аэрокосмической промышленности. Наша команда использует передовые технологии, чтобы гарантировать, что каждая пресс-форма для литья под высоким давлением соответствует самым строгим отраслевым стандартам.
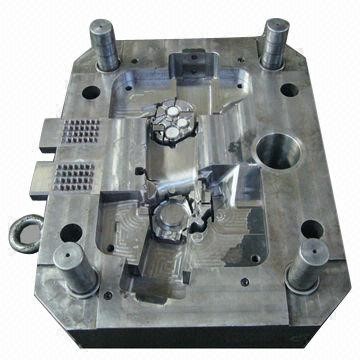

Общее литье под давлением Инструментальная оснастка
Общая оснастка для литья под давлением включает в себя формы и сопутствующие инструменты для применения, не требующего экстремальных давлений в системах высокого давления. Эти инструменты в основном применяются при мелкосерийной обработке или при работе с деталями простых форм. Как опытный производитель оснастки для литья под давлением, мы понимаем все нюансы оснастки высокого давления и общей оснастки, гарантируя нашим клиентам решения, соответствующие их конкретным требованиям.
Процесс создания пресс-формы для литья под давлением
Создание формы для литья под давлением - это высокотехничный процесс, включающий в себя несколько этапов, каждый из которых требует тщательного внимания к деталям. В компании TheDieCasting.com мы придерживаемся структурированного подхода, чтобы обеспечить высочайшее качество форм:
Дизайн и проектирование
Процесс начинается с консультаций с нашими клиентами, чтобы понять их. Существует профессиональное программное обеспечение, с помощью которого наша команда конструкторов создает подробные эскизы пресс-формы. Будь то сложная конструкция оснастки для литья под высоким давлением или простая литьё алюминия под давлением Мы гарантируем, что конструкция будет оптимальной с точки зрения эффективности и долговечности.
Выбор материала
Выбор подходящего материала является важным критерием эффективности контейнера. Мы точно подбираем материалы, способные выдерживать давление и температуру, присущие этапу эксплуатации, без ущерба для структуры. Это означает, что каждая пресс-форма, произведенная здесь, обеспечивает вам долговременную надежность.
Производство и тестирование
После того, как дизайн кресла и материал, из которого оно будет изготовлено, определены, форма создается с помощью высокотехнологичной обработки на станках с ЧПУ и других точных методов. После изготовления каждая пресс-форма для литья под давлением проходит тщательное тестирование, чтобы проверить ее работоспособность в смоделированных условиях эксплуатации. Такое внимание к деталям гарантирует, что форма будет выполнять свою работу в реальных условиях.
Области применения форм для литья под давлением
Универсальность оснастки для литья под давлением делает ее бесценной в различных отраслях промышленности. Формы, которые мы предлагаем на TheDieCasting.com, применяются во многих областях, включая автомобилестроение, электронику, промышленное оборудование и многие другие.
Например, наши формы для литья алюминия под давлением играют важную роль в производстве легких, но прочных компонентов, таких как блоки двигателей, корпуса трансмиссий и структурные элементы в автомобильной промышленности. Аналогичным образом, электронная промышленность полагается на нашу оснастку для литья под высоким давлением для создания сложных деталей с отличной тепло- и электропроводностью.
Наша способность адаптироваться к уникальным требованиям каждой отрасли является свидетельством нашего опыта как ведущего производителя литейной оснастки.
Преимущества использования высококачественных форм для литья под давлением
Качество формы играет главную роль в определении эффективности литья под давлением. Высококачественные формы, как те, которые производит TheDieCasting.com, имеют ряд преимуществ:
Точность и последовательность
Хорошо спроектированная литейная форма обеспечивает точное соответствие каждого производимого компонента техническим условиям. Такая степень точности характерна для тех отраслей промышленности, где достижение пространственных допусков и точности размеров может привести к функциональному отказу.
Экономическая эффективность
Точные формы, такие как наши формы для литья под высоким давлением, сокращают количество ошибок и материалов, используемых при литье, что приводит к экономии средств. Наши формы разработаны таким образом, чтобы минимизировать пористость и обеспечить более высокий выход бездефектных деталей, предоставляя вам экономически эффективное решение, которое максимально повышает эффективность вашего производства.
Долговечность
В TheDieCasting.com мы используем отборные материалы и самые современные технологии для создания форм, которые могут прослужить долгие годы. Такая долговечность не только обеспечивает надежность и стабильность производственного процесса, но и снижает необходимость в частой замене и обслуживании, предоставляя вам долгосрочное и экономически эффективное решение.
Устойчивое развитие производства форм для литья под давлением
TheDieCasting.com придерживается практики устойчивого развития бизнеса как основы компании. Мы стремимся сократить количество отходов и энергопотребление при изготовлении форм настолько, насколько это практически возможно. Например, наши формы для литья алюминия под давлением разработаны с учетом эффективности, обеспечивая оптимальное использование материалов и снижая воздействие на окружающую среду.
Кроме того, мы всегда стремимся к новым решениям в области устойчивого развития производства, например, в области утилизации лома и энергосбережения на существующих производственных предприятиях. Но если придерживаться этой приверженности, то устойчивое развитие не только полезно для мира, но и укрепляет "зеленые" миссии наших клиентов.
Почему стоит выбрать TheDieCasting.com для пресс-форм для литья под давлением?
Являясь надежным производителем литейной оснастки, мы создали репутацию компании с превосходным опытом, передовыми технологиями и ориентированным на клиента сервисом. В Stereo наша команда концентрируется не только на способностях и навыках сотрудников, но и на предоставлении лучшего, чтобы оправдать ожидания клиента.
Наша приверженность качеству проявляется в каждой пресс-форме, которую мы производим, будь то сложное решение по оснастке для литья под высоким давлением или стандартная конструкция оснастки для литья под давлением. После многих лет роста и концентрации на совершенствовании мощностей компании мы являемся надежным партнером для отраслей промышленности на мировом уровне.
Будущее форм для литья под давлением
Индустрия литья под давлением имеет множество подотраслей, которые в основном определяются новыми материалами, дизайном и новыми технологиями. Для этого мы постоянно отслеживаем возникающие тенденции на TheDieCasting.com, чтобы предоставить клиентам инновационные варианты. От разработки более эффективных форм для литья алюминия под давлением до изучения возможностей проектирования оснастки с помощью искусственного интеллекта - мы стремимся расширить границы возможного.
Поскольку промышленность продолжает требовать повышения производительности и устойчивости, наш опыт ведущего производителя форм для литья под давлением позволяет нам уверенно решать эти задачи.
Сотрудничество с TheDieCasting.com для получения превосходных форм для литья под давлением
Выбор лучшего партнера для вашего бизнеса по литью под давлением сегодня требует большего внимания, чем когда-либо. В TheDieCasting.com мы сочетаем техническое превосходство, инновационный дизайн и исключительное обслуживание клиентов, чтобы предоставить лучшие формы для литья под давлением для вашего бизнеса. Нужна ли вам индивидуальная форма для литья под высоким давлением или универсальная алюминиевая форма для литья под давлением, мы готовы воплотить ваше видение в жизнь.
Свяжитесь с нами сегодня, чтобы узнать больше о наших решениях в области литейной оснастки и понять, как наш опыт ведущего производителя литейной оснастки может поднять ваши производственные процессы на новую высоту.
Вопросы и ответы
1. В чем разница между алюминиевыми формами для литья под давлением и формами для литья под высоким давлением?
Формы для литья алюминия под давлением предназначены для производства деталей из алюминия или его сплавов. Эти формы разработаны таким образом, чтобы использовать преимущества таких свойств алюминия, как легкость, отсутствие коррозии и хорошая теплопроводность. Они часто используются
в автомобильной промышленности, аэрокосмической отрасли и электронике, где необходимы прочность и малый вес.
С другой стороны, формы для литья под высоким давлением предназначены для работы в жестких условиях, когда расплавленный металл впрыскивается в полость формы под очень высоким давлением. Такие формы отличаются точностью и могут использоваться для создания сложных форм, не имеющих высоких допусков и требующих низкой шероховатости поверхности. Хотя формы для литья алюминия под давлением являются подмножеством форм для литья под высоким давлением, последняя категория также включает формы для других металлов, таких как магний и цинк. Когда речь заходит о литье под давлением и быстрой оснастке, TheDieCasting.com предлагает лучшее из двух миров, чтобы удовлетворить ваши потребности для каждого приложения.
2. Сколько времени занимает проектирование и изготовление литейной формы?
Сроки проектирования и изготовления литейной формы зависят от нескольких факторов, включая сложность конструкции, размер формы и специфические требования проекта. В большинстве других случаев изготовление формы может занять от трех недель до трех месяцев.
В компании TheDieCasting.com все начинается с консультации с вами для определения ваших требований. Последним шагом на этапе разработки концепции является проектирование нашего изделия с помощью современной программы автоматизированного проектирования. Затем наша команда дизайнеров разрабатывает производственный план для легкого изготовления продукта. После завершения проектирования компания переходит к этапу закупки материалов и производства, используя современные технологии, такие как компьютерная обработка с числовым программным управлением и другие технологии. Затем проводятся эксплуатационные испытания, чтобы проверить пресс-форму на максимальные возможности. Мы также информируем наших клиентов
На протяжении всего процесса, сообщая им о любых изменениях в сроках выполнения работ.
3. Каковы основные преимущества использования форм для литья под высоким давлением?
Формы для литья под высоким давлением обладают рядом существенных преимуществ, что делает их предпочтительным выбором для современного производства. Их применение включает в себя изготовление сложных и тонких деталей, которые отличаются высокой точностью и повторяемостью. Система высокого давления обеспечивает проникновение расплавленного металла во все участки формы, поэтому конечный продукт имеет точные размеры и полированную поверхность.
Еще одно преимущество - эффективность, которую обеспечивает команде бамбуковая конструкция. При литье под высоким давлением время цикла относительно быстрое, что позволяет изготавливать много деталей за короткий срок, что хорошо подходит для отраслей с высокими требованиями. Кроме того, формы для литья под высоким давлением позволяют уменьшить пористость, что повышает механическую надежность изделий. LinkedIn: Формы высокого давления обеспечивают структурную прочность деталей, поскольку снижают уровень пористости. Компания TheDieCasting.com разрабатывает и производит формы для литья под высоким давлением, чтобы обеспечить эти преимущества, сохраняя при этом экономическую эффективность и долговечность.
4. Как вы обеспечиваете качество и долговечность форм для литья под давлением?
Как вы увидите на сайте TheDieCasting.com, качество и долговечность лежат в основе нашего стратегического мышления. Мы используем инструментальную сталь и другие марки или сплавы, чтобы гарантировать, что наши формы смогут выдержать жесткое давление и температуру при использовании процесса литья под давлением. Наше производство включает в себя использование технологических методов, таких как компьютерное числовое управление обработкой, которые обеспечивают высокую точность форм.
Помимо качества материалов, существуют протоколы испытаний. Каждая пресс-форма для литья под давлением проходит испытания в смоделированных условиях эксплуатации, чтобы убедиться, что она соответствует или превосходит спецификации заказчика. Мы также даем рекомендации по уходу за пресс-формой для увеличения ее долговечности. Используя современные подходы к производству в сочетании с чрезвычайно высокими стандартами обеспечения качества, мы гарантируем, что клиенты получат формы, которые обеспечат высокую производительность в долгосрочном производстве.
5. Какие отрасли промышленности больше всего выигрывают от использования литейных форм, и как TheDieCasting.com может помочь?
Формы для литья под давлением незаменимы в отраслях, где важны точность, эффективность и долговечность. Например, автомобильная промышленность использует алюминиевые литейные формы для изготовления легких компонентов двигателей, корпусов трансмиссий и конструкционных деталей. Электронная промышленность использует формы для литья под высоким давлением для создания сложных компонентов с отличной тепло- и электропроводностью.
Аналогичным образом, в аэрокосмической промышленности, медицине и промышленном машиностроении используются литейные формы для производства высокопроизводительных компонентов.
Наши клиенты из самых разных отраслей промышленности, включая автомобильную, коммерческий транспорт, аэрокосмическую и потребительские товары, обращаются в TheDieCasting.com за решениями, наилучшим образом отвечающими их потребностям. Будь то изготовление легких деталей для электромобилей или прецизионных компонентов для медицинских приборов, наш опыт ведущего производителя оснастки для литья под давлением гарантирует, что каждый клиент получит правильное решение. Находясь в непосредственном контакте с ними, мы предоставляем лучшие проекты, соответствующие их потребностям, сложные производственные процедуры и превосходные услуги.