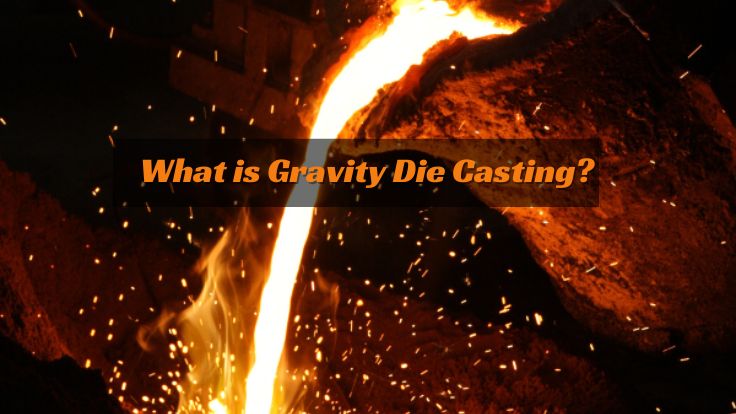
In der modernen Fertigung ist der Metallguss von entscheidender Bedeutung, wenn es darum geht, Bauteile mit komplexen Geometrien in hoher Qualität herzustellen. Eines der effizientesten Verfahren hierfür ist der Kokillenguss. Dieses Verfahren ist eine Kombination aus Präzision, Effizienz und Kosteneffizienz und daher eine bevorzugte Lösung für Branchen wie die Automobilindustrie, die Luft- und Raumfahrt und die Industrieausrüstung. Im Wesentlichen wird beim Kokillenguss die Schwerkraft genutzt, um eine Form mit Metall zu füllen, ohne dass eine Hochdruckanlage verwendet werden muss, so dass der Prozess nicht sehr komplex ist. Wenn Sie Ingenieurwissenschaften studieren, Produktionsleiter sind oder sich einfach nur für Gusstechnologien interessieren, dann ist das Wissen über das Kokillengießen von entscheidender Bedeutung, um sich einen Überblick über die Metallproduktion zu verschaffen.
Die Grundprinzipien des Aluminium-Kokillengusses, seine Funktionsweise, wichtige Faktoren wie Temperatur und Zeit, die Art der verwendeten Materialien sowie seine Vor- und Nachteile und die üblichen Anwendungen werden in diesem Artikel behandelt.
Wie funktioniert der Aluminium-Kokillenguß?
Aluminium-Kokillenguss ist ein Verfahren des Dauerformgusses, das üblicherweise für die Herstellung von Nichteisen-Metallteilen aus Aluminium eingesetzt wird. Beim Aluminium-Kokillenguss wird geschmolzenes Aluminiummetall nur durch den Einfluss der Schwerkraft in eine wiederverwendbare Metallform gegossen. Im Gegensatz zum Hochdruckguss, bei dem das Metall mit einem Druck von mehreren tausend psi in die Form gepresst wird, wird beim Schwerkraftguss allein die natürliche Schwerkraft genutzt, so dass die geschmolzene Metalllegierung ungehindert in die Hohlräume der Form fließen kann.
Im Folgenden wird der typische Ablauf dieser Tätigkeit beschrieben:
- Die auf etwa 150-300° C vorgewärmte Metallform (in der Regel aus Gusseisen oder Stahl) wird zur Vermeidung von Temperaturschocks und zur Förderung des reibungslosen Fließens des Metalls gegen die Metallform gedrückt.
- Die Matrize wird mit einem Schmiermittel aus Keramik oder Graphit überzogen, damit das geschmolzene Metall nicht an ihr kleben bleibt.
- Geschmolzenes Metall (in Form von Aluminium-, Magnesium- oder Kupferlegierungen), das auf etwa 650-750 °C (je nach Art des Materials) erhitzt wird, wird in die Form gegossen.
- Das geschmolzene Metall wird über einen Anguss in den Formhohlraum gedrückt und nimmt unter der Wirkung der Schwerkraft die gesamte Form ein.
- Die Form lässt das Gussteil innerhalb von 20 bis 90 Sekunden erstarren, je nach Größe und Material.
- Anschließend wird die Matrize geöffnet und der Chip manuell ausgeworfen oder aus der Matrize entfernt.
- Bevor das Produkt seine Endfertigung erreicht, wird überschüssiges Material von Kufen und Angüssen abgeschnitten.
Da bei diesem Verfahren die Schwerkraft und nicht mechanischer Druck zum Einsatz kommt, ist die Einrichtung der Anlagen einfacher und die Kosten für Wartung und Werkzeuge sind in der Regel niedriger.
Schritt-für-Schritt-Verfahren des Schwerkraftkokillengusses
Das Kokillengussverfahren ist wegen seiner einfachen Wiederholbarkeit beliebt und kann auch qualitativ hochwertiges Metall mit engen Toleranzen herstellen. Im Gegensatz zum Druckguss wird hier allein die Schwerkraft genutzt, um den Formhohlraum zu füllen, was den gesamten Prozess kosteneffizienter und mechanisch weniger schwerfällig macht.
Im Folgenden finden Sie eine schrittweise Anleitung, wie Aluminium-Kokillenguss in einer gewöhnlichen Einrichtung durchgeführt wird:
1. Vorbereitung der Form
Der erste Prozess beim Aluminium Gravity Casting besteht in der Vorbereitung der Form, die auch als Kokille bezeichnet wird. Für die Herstellung dieser Formen, die für wiederholte Verwendung gedacht sind, wird normalerweise Stahl oder Gusseisen verwendet. Nach dem Gießen des Metalls wird die Form gründlich gereinigt, um alle Rückstände von früheren Gussstücken zu entfernen.
Nach der Reinigung wird die Form auf eine Temperatur zwischen 150°C und 300°C vorgewärmt. Vorwärmen bedeutet, dass die geschmolzene Aluminiumlegierung beim Kontakt nicht zu schnell abkühlt, was zu Fehlern wie Kaltverschlüssen oder unzureichender Füllung führt. Ein Trennmittel, in der Regel eine Beschichtung auf Graphit- oder Keramikbasis, wird auf die Innenfläche der Form aufgetragen. Diese Beschichtung hat zwei Funktionen: Sie sorgt dafür, dass die geschmolzene Aluminiumlegierung nicht an der Form kleben bleibt, und trägt zu einer glatteren Oberfläche des Endprodukts bei.
2. Schmelzen von Aluminiumlegierungen
Auf die Vorbereitung der Form folgt das Schmelzen der ausgewählten Metalllegierung. Die Mengen der Metalllegierungen werden in den Ofen gegeben und bis zur Gießtemperatur geschmolzen, die von der Legierung abhängt. So liegen die Schmelzpunkte von Aluminiumlegierungen in der Regel im Bereich von 650°C-750°C, während für Kupferlegierungen Schmelzpunkte zwischen 900°C und 1100°С erforderlich sind.
Es ist äußerst wichtig, die Schmelztemperatur genau zu kontrollieren. Eine Übererwärmung könnte eine verstärkte Oxidation oder Gasaufnahme zur Folge haben, während eine Untererwärmung zu einer unvollständigen Füllung der Formen oder schlechten mechanischen Eigenschaften führen könnte.
3. Gießen des geschmolzenen Metalls Legierung
Wenn die richtige Schmelztemperatur erreicht ist, wird das geschmolzene Metall in die vorgewärmte Form gegossen. Beim Kokillenguss wird keine mechanische Kraft oder gar Druck ausgeübt. Die Schwerkraft bewirkt, dass die Aluminiumlegierungen auf natürliche Weise durch eine Reihe von Angüssen und Anschnitten in den Eingang des Formhohlraums fließen.
Dieser Schritt erfordert einen langsamen, kontrollierten Guss, damit keine Turbulenzen entstehen, die Gase einschließen und zu Porosität im Gussteil führen können. Bei einigen fortschrittlichen Systemen besteht die Möglichkeit, die Form während des Gießens sehr langsam zu kippen - das Kipp-Kokillengießen, um einen sanften und gleichmäßigen Metallfluss zu erzeugen.
4. Füllen des Formhohlraums
Sobald das geschmolzene Metall in die Form eindringt, füllt es alle Teile des Hohlraums unter der Form der Matrize aus. Die Formgestaltung ist an diesem Punkt sehr wichtig. Richtig konstruierte Anschnittsysteme verteilen das Metall, um Turbulenzen, kalte Stellen oder Bereiche mit möglicher Schrumpfung zu vermeiden.
Da der Metallfluss allein durch die Schwerkraft erfolgt, ist es notwendig, dass das Metall mit der richtigen Geschwindigkeit und Temperatur gegossen wird. Eine unzureichende Fließkontrolle kann zu Fehlern wie unvollständigen Füllungen oder Kaltverschlüssen führen - Stellen, an denen sich zwei Metallfronten berühren, aber nicht zusammenschmelzen.
5. Erstarrung und Abkühlung
Nachdem der Hohlraum gefüllt ist, beginnt die geschmolzene Metalllegierung abzukühlen und fest zu werden. Die Abkühlungszeit hängt von der Größe und Komplexität des Gussteils sowie von der Art des verwendeten Metalls ab. So können beispielsweise kleine Aluminiumteile bereits nach 20-30 Sekunden erstarren, während große oder dickere Teile 60-90 Sekunden und mehr benötigen können.
Die Kokille ist in den meisten Fällen wassergekühlt, um die Abkühlgeschwindigkeit zu steuern. Durch die kontrollierte Abkühlung werden das Korngefüge und die Eigenspannungen verbessert und reduziert, so dass die Gussteile stabiler und zuverlässiger werden.
6. Öffnen der Matrize und Entnahme der Teile
Die Form wird nach der Erstarrung der Aluminiumlegierung geöffnet. Je nach Konstruktion kann das Gussteil manuell entnommen oder durch den Druck der in die Form eingebauten mechanischen Auswerferstifte ausgestoßen werden. Da für das Gießen eine Metallform verwendet wird, kann die Form für Tausende von Zyklen wiederverwendet werden, so dass das Verfahren für mittlere bis hohe Stückzahlen kostengünstig ist.
Bei der Entnahme der Teile ist darauf zu achten, dass das Gussteil oder die Form nicht beschädigt wird. Zu diesem Zeitpunkt hat das Gussteil noch überschüssiges Material von den Angusskanälen und Anschnitten übrig, das im nächsten Schritt entfernt werden muss.
7. Beschneiden und Endbearbeitung
Das herausgezogene Gussteil enthält in der Regel zusätzliches Metall, das am Anguss und am Anschnittsystem befestigt ist. Dieses Material wird mechanisch mit einer Säge, einer Schere oder Schleifwerkzeugen abgetrennt. Weitere Nachbearbeitungsschritte können Entgraten, Kugelstrahlen, maschinelle Bearbeitung oder Wärmebehandlung sein, um das Produkt zu spezifizieren.
Ziel dieser Phase ist es, das Aussehen des Gussteils zu verfeinern, die Maßgenauigkeit zu erhöhen und es für seine endgültige Funktion oder Montage vorzubereiten.
8. Inspektion und Qualitätskontrolle
Der letzte Prozess des Kokillengussverfahrens ist die Prüfung. Die Oberflächenfehler, Maßtoleranzen und inneren Fehler der Gussteile werden zuverlässig geprüft. Zunächst werden visuelle Prüfungen durchgeführt, je nach Bedarf gefolgt von anderen, fortgeschritteneren Techniken wie:
- Röntgenuntersuchungen werden angeordnet, um innere Porosität oder Schrumpfung festzustellen.
- Oberflächenrisse mittels Farbeindringprüfung.
- Ultraschallprüfung für strukturelle Konsistenz
- Druckprüfung, insbesondere für die flüssigkeitsführenden Komponenten
Nur die Gussteile, die alle Qualitätsprüfungen bestanden haben, werden zur Verwendung oder zur Lieferung an die Kunden freigegeben. Die beanstandeten Teile werden in der Regel eingeschmolzen und recycelt, so dass weniger Material verschwendet wird.
Arten des Kokillengusses
Das Kokillengießen ist ein vielseitiges Verfahren, das es in verschiedenen Formen gibt, um unterschiedliche Teilegeometrien, Materialien und Produktionsanforderungen zu erfüllen. Auch wenn der Kern der Idee - das Füllen einer Metallform mit Hilfe der Schwerkraft - erhalten bleibt, gibt es für das Kokillengussverfahren spezifische Arten oder besser gesagt Methoden, die verschiedene Hersteller anwenden, um eine bestimmte Anwendung zu erfüllen.
1. Kokillenguss Kokillenguss
Dies ist die typischste Form des Kokillengusses. Die Herstellung großer Mengen desselben Bauteils erfolgt in einer wiederverwendbaren Metallform (meist aus Stahl oder Gusseisen). Die Form wird vorgewärmt und dann mit einem Trennmittel versehen und mit geschmolzenem Metall gefüllt. Nach dem Erstarren wird das Teil aus der Form entnommen und recycelt.
Anwendungen: Bauteile von Kraftfahrzeugen, Armaturen von Rohrleitungen und Pumpengehäuse
Vorteile: Hohe Maßgenauigkeit, gute Oberflächengüte und lange Lebensdauer der Form
2. Kipp-Kokillengießen
Bei dieser Methode wird die Form während des Gießvorgangs langsam geneigt. Dadurch kann das geschmolzene Metall den Formhohlraum langsam und gleichmäßig ausfüllen, so dass Turbulenzen und die Gefahr des Einschlusses von Gas oder kalten Schloten vermieden werden.
Anwendungen: Dünnwandige Komponenten oder Teile, in denen Luft eingeschlossen werden kann
Vorteile: Verbesserte innere Festigkeit, verbesserte Oberfläche und geringeres Auftreten von Mängeln
3. Niederdruck-Kokillengießen (Hybrid)
Technisch gesehen handelt es sich hierbei um eine separate Kategorie, obwohl einige dies als eine Variante betrachten, bei der ein niedriger Gasdruck (normalerweise 0,7 - 1,5 bar) auf das geschmolzene Metall angewendet wird, um es sanft in die Form zu drücken. Es vereint die Vorteile der Einfachheit des Schwerkraftgießens mit einigen Vorteilen der Druckregelung.
Anwendungen: Fahrzeugräder und Strukturkomponenten sind ebenfalls aus hochintegriertem Guss.
Vorteile: Bessere Kontrolle des Metallflusses, bessere mechanische Eigenschaften
4. Sandkernunterstütztes Schwerkraftgießen
Bei dieser Methode werden Sandkerne verwendet, die in die Metallform eingesetzt werden, wo sie die Bildung von inneren Hohlräumen oder Hinterschneidungen ermöglichen, die mit einer reinen Metallform nicht möglich wären.
Anwendungen: Komplexe Motorkomponenten, Ventilgehäuse
Vorteile: Ermöglicht die Herstellung fortschrittlicher Teile bei gleichzeitiger Verlängerung der Lebensdauer einer Dauerform.
Tabelle: Arten des Kokillengusses
Typ | Beschreibung | Anwendungen | Die wichtigsten Vorteile |
Dauerform Schwerkraftgießen | Verwendet eine wiederverwendbare Metallform für Großseriengüsse | Automobilteile, Pumpengehäuse | Hohe Genauigkeit, glatte Oberfläche, lange Lebensdauer der Matrize |
Kipp-Kokillengießen | Die Form wird während des Gießens gekippt, damit das Metall gleichmäßig fließt | Dünnwandige oder luftempfindliche Bauteile | Weniger Mängel, bessere innere Struktur |
Niederdruck-Schwerkraftgießen | Kombiniert Schwerkraftgießen mit niedrigem Druck (0,7-1,5 bar) zur Unterstützung des Metallflusses | Fahrzeugräder, Strukturteile | Verbesserte Fließkontrolle, stärkere Gussteile |
Sandkernunterstütztes Gießen | Verwendung von Sandkernen innerhalb der Metallform für komplexe Innenformen | Motorblöcke, Ventilgehäuse | Ermöglicht das Gießen von hohlen oder komplizierten Teilen |
Materialien für den Kokillenguss
Das Kokillengießen ist eines der gebräuchlichsten Kokillengießverfahren; es wird meist bei Nichteisenlegierungen angewandt. Die an diesem Verfahren beteiligten Werkstoffe müssen eine hohe Fließfähigkeit, einen mittleren Schmelzpunkt und eine ausgezeichnete Gießbarkeit aufweisen, damit das geschmolzene Metall den Formhohlraum fehlerfrei ausfüllen kann. Da beim Schwerkraftgießen nur die Schwerkraft zum Füllen der Form genutzt wird, ohne dass ein äußerer Druck ausgeübt wird, ist die Auswahl des Werkstoffs ein noch entscheidenderer Faktor, um die Maßgenauigkeit, Oberflächenqualität und Festigkeit zu erreichen. Zu den wichtigsten Materialien, die beim Kokillenguss verwendet werden, gehören;
Aluminium-Legierungen
Aluminium ist aufgrund seines geringen Gewichts, seiner außergewöhnlichen Korrosionsbeständigkeit und seiner einfachen Gießbarkeit das am häufigsten verwendete Material im Kokillengussverfahren. Typische Aluminiumlegierungen sind A356, AlSi12 und A319. Diese Legierungen bieten eine gute Mischung aus Festigkeit, Duktilität und Wärmeleitfähigkeit, wodurch sie sich für Automobilteile wie Motorblöcke, Zylinderköpfe, Getriebegehäuse und andere Strukturteile eignen.
Die für den Kokillenguss verwendeten Aluminiumlegierungen schmelzen in der Regel in einem Temperaturbereich zwischen 660°C und 750°C. Das geschmolzene Aluminium fließt gleichmäßig in die Metallform und kühlt schnell ab, wobei sich ein dichtes, feinkörniges Gefüge bildet. Sie können auch mit einer T5- oder T6-Wärmebehandlung versehen werden, die die mechanischen Eigenschaften verbessert. Das Schwerkraftgießen von Aluminium bietet eine hohe Maßgenauigkeit, eine gute Oberflächengüte und eine lange Lebensdauer, wenn die Form gut gewartet wird.
Legierungen auf Kupferbasis
Das Schwerkraftgießen ist auch mit Kupferlegierungen möglich, insbesondere mit Bronze und Messing. Diese Werkstoffe werden dort eingesetzt, wo hohe Verschleißfestigkeit, ausgezeichnete Festigkeit und hervorragende thermische/elektrische Leitfähigkeit erforderlich sind. Bronzeguss wird zum Beispiel in Bereichen wie Schiffsschrauben, Pumpengehäusen und Lagern verwendet, während Messing in Bereichen wie Sanitärarmaturen und dekorativen Beschlägen zum Einsatz kommt.
Die Schmelztemperaturen von Kupferlegierungen sind höher und liegen zwischen 1000° und 1200° Celsius. Dadurch wird das Material der Gussform thermisch belastet und der Gießprozess muss gut kontrolliert werden, um Oxidation und Schrumpfungsfehler zu vermeiden. Das Schwerkraftgießen unter Verwendung von Kupferlegierungen kann bei entsprechender Kontrolle starke Teile mit hervorragender Leistung unter extremen Bedingungen liefern.
Magnesium-Legierungen
Magnesiumlegierungen werden im Kokillenguss eingesetzt, wenn die Konstruktion von Leichtbaustrukturen ein zentrales Anliegen ist, wie z. B. in der Luft- und Raumfahrt und in der Automobilindustrie. Zu den gängigen Legierungen gehört AZ91D, das ein gutes Gleichgewicht zwischen Festigkeit, Gießbarkeit und Korrosionsbeständigkeit bietet. Sein Hauptvorteil ist die geringe Dichte von etwa 1,8 g/cm³, was bedeutet, dass es das leichteste Konstruktionsmetall ist, das verwendet wird.
Magnesiumlegierungen werden bei etwa 600°C - 650°C verflüssigt. Wegen der hohen Reaktivität sollten sie in geschützter Umgebung oder mit Hilfe von Flussmitteln gegossen werden, um Oxidation und Verbrennungen zu vermeiden. Nichtsdestotrotz ermöglicht das Schwerkraftgießen die Herstellung von Magnesiumbauteilen, die im Vergleich zu anderen Umformverfahren ein hohes Maß an Präzision und weniger Abfall aufweisen.
Zink-Legierungen

Obwohl sich Zink eher für Druckgussverfahren eignet, wird es für bestimmte Anwendungen auch für den Schwerkraftguss verwendet, insbesondere für kleine, eng anliegende Teile mit engeren Toleranzen. Zinklegierungen wie Zamak 3 und Zamak 5 werden wegen ihres niedrigen Schmelzpunkts (ca. 385 °C), der guten Fließfähigkeit und der Nachbildung feiner Details in Formen bevorzugt.
Zink-Kokillenguss wird für elektronische Produkte und Konsumgüter sowie für mechanische Teile mit geringer Belastung verwendet. Der Hauptvorteil der Verwendung von Zink im Kokillenguss ist die Fähigkeit, scharfe Kanten und feine Merkmale ohne umfangreiche Bearbeitungsprozesse herzustellen. Aufgrund seiner geringen mechanischen Festigkeit im Vergleich zu Aluminium oder Kupfer kann es jedoch nur für nicht-strukturelle Anwendungen eingesetzt werden.
Siliziumverstärkte Aluminium-Legierungen
Siliziumreiche Aluminiumlegierungen wie AlSi12 sind ideal für den Kokillenguss, da das zugesetzte Silizium die Fließfähigkeit erhöht, die Schrumpfung verringert und die Verschleißfestigkeit erhöht. Solche Legierungen werden häufig in Motorenteilen, Bremsteilen und Hydraulikgehäusen verwendet, bei denen die Dimensionsstabilität und Festigkeit von Bedeutung sind.
Der Siliziumgehalt, der im Bereich von 7-12% liegt, verbessert die Fähigkeit der Legierung, komplizierte Formen ohne Heißriss oder Gasporosität zu füllen. Diese Legierungen kristallisieren gleichmäßig, was zu weniger Defekten und geringer Nachbearbeitung führt.
Alternativen zum Schwerkraftgießen
Kokillenguss ist ein häufig angewandtes Verfahren zur Herstellung von Metallteilen mit mittlerem bis hohem Volumen und guten mechanischen Eigenschaften. Aber es ist nicht immer die beste Wahl. Eine Reihe von Faktoren wie die Komplexität der Teile, die gewünschte Oberflächenbeschaffenheit, die Kosten und das Produktionsvolumen sind ausschlaggebend für die Wahl des Gießverfahrens. Die Hersteller können in solchen Fällen auf verschiedene alternative Gießverfahren zurückgreifen. Im Folgenden werden die wichtigsten Alternativen zum Schwerkraftgießen mit ihren Stärken, Schwächen und üblichen Anwendungen näher betrachtet.
Sandgießen
Das traditionellste und flexibelste Gießverfahren ist der Sandguss. Dabei wird der Formhohlraum mit einer Sandmischung bearbeitet, die in der Regel durch Ton oder chemische Bindemittel gebunden ist. Zur Formgebung der Sandform wird ein Modell verwendet, das normalerweise aus Holz oder Metall besteht. Nach dem Formen der Form wird das geschmolzene Metall in den Hohlraum eingefüllt.
Dieses Verfahren eignet sich besonders gut für kleine bis mittlere Produktionsmengen, große Teile oder Teile mit komplexen inneren geometrischen Strukturen, die sich im massiven Metallguss nicht so einfach realisieren lassen. Sandguss ist relativ kostengünstig in Bezug auf die Werkzeugkosten und eignet sich daher für die Herstellung von Prototypen oder für kundenspezifische Aufträge.
Im Vergleich zum Kokillenguss führt Sandguss jedoch zu einer rauen Verarbeitung und einer geringeren Maßgenauigkeit. Die Form wird nach jedem Gebrauch zerstört, so dass die Produktionszeit und der Materialverlust bei hohen Stückzahlen höher sind. Dennoch ist das Sandgussverfahren eine flexible Option, wenn die Kosten für die Einrichtung eine geringe Priorität haben.
Druckgießen
Beim Druckguss (HPDC) wird geschmolzenes Metall unter hohem Druck, d.h. zwischen 600 und 1200 bar (1 Druck), in eine Stahlform gespritzt. Dieses Verfahren ermöglicht die Herstellung komplizierter Formen mit hoher Maßgenauigkeit und Oberflächenqualität bei hohen Geschwindigkeiten.
HPDC ist besonders hilfreich bei der Herstellung dünnwandiger Teile, die mit der reinen Schwerkrafttechnik nicht gegossen werden können. Dies ist eine gängige Praxis in der Automobil-, Elektronik- und Haushaltsgeräteindustrie. Die kurzen Zykluszeiten und der hohe Automatisierungsgrad machen es für die Produktion sehr hoher Stückzahlen kosteneffizient.
Die Hauptnachteile im Vergleich zum Kokillenguss sind die prohibitiv teuren Werkzeuge sowie die Neigung zu Gaseinschlüssen, die zu Porosität im Endprodukt führen können. Außerdem ist das Verfahren aufgrund des hohen Drucks in der Regel auf kleinere Bauteile beschränkt und kann für größere oder dickere Teile nicht verwendet werden.
Niederdruckgießen
Das Niederdruckgussverfahren (LPDC) ist eine modifizierte Version des Schwerkraftgusses. Anstatt das geschmolzene Metall einfach in die Form zu gießen, wird ein Überdruck (zwischen 0,7 und 1,5 bar) in die Ofenkammer eingeleitet, wodurch das geschmolzene Metall durch ein sogenanntes Steigrohr in die Form aufsteigt.
Diese Methode bietet mehr Kontrolle über den Metallfluss und minimiert das Risiko von Gasporosität. Es wird häufig bei Anwendungen eingesetzt, die Teile mit hoher Integrität erfordern, wie z. B. bei Fahrzeugrädern und strukturellen Aluminiumteilen. Im Vergleich zum Kokillenguss führt LPDC auch zu besseren mechanischen Eigenschaften und Ausschussraten.
Eine solche verstärkte Kontrolle hat jedoch ihren Preis. Die Technologie ist komplizierter und kostspieliger, und der Prozess ist länger. Selbst unter diesen Bedingungen wird LPDC häufig gewählt, wenn eine bessere Gussqualität und innere Integrität erforderlich sind.
Schleudergießen
Beim Schleuderguss wird die Form mit hoher Geschwindigkeit gedreht, während das geschmolzene Metall hineingegossen wird. Durch die Zentrifugalkräfte wird das Metall hart gegen die Wände der Form gepresst, wodurch die Porosität verringert und eine extrem feinkörnige Struktur erzeugt wird.
Diese Technik eignet sich für zylindrische oder röhrenförmige Teile, d. h. Rohre, Ringe und Buchsen. Aufgrund der gerichteten Kristallisation und der dichten Beschaffenheit weisen die geformten Teile in der Regel hohe mechanische Eigenschaften und geringe Abnutzungseigenschaften auf.
Das Schleudergussverfahren ist jedoch in Bezug auf die Geometrie der Teile erheblich eingeschränkt - es kann nur bei symmetrischen Formen eingesetzt werden, und komplexe innere Merkmale sind schwer zu realisieren. Auch die anfängliche Einrichtung und Ausrüstung ist recht speziell, was sich für einige der Verfahren als Hindernis erweist. Bei runden, hochleistungsfähigen Teilen ist das Schleudergussverfahren jedoch eine gute Option im Vergleich zum Schwerkraftguss.
Feinguss (Wachsausschmelzverfahren)
Feinguss, auch Wachsausschmelzverfahren genannt, ist ein Verfahren, bei dem eine Wachsform des herzustellenden Teils erstellt, eine Keramik (Beschichtung) aufgetragen und das Wachs ausgeschmolzen wird, so dass ein Hohlraum entsteht. In diesen Hohlraum wird dann Heißmetall gegossen, um das endgültige Teil herzustellen.
Dieses Verfahren ist sehr wertvoll, denn es ermöglicht die Herstellung sehr komplizierter und detaillierter Teile mit einer nahezu reinen Form. Es eignet sich perfekt für relativ kleine bis mittelgroße Bauteile mit hohen Anforderungen an die Maßgenauigkeit und die Ästhetik einer hochwertigen Oberfläche, wie z. B. Turbinenschaufeln, Bauteile für die Luft- und Raumfahrt und Schmuck.
Im Vergleich zum Kokillenguss hat der Feinguss eine langsamere Produktionsrate und hohe Kosten pro Teil, insbesondere bei großen Stückzahlen. Die Formen sind außerdem Einwegwerkzeuge und erfordern mehr Arbeitsschritte. Für komplizierte Teile, die nicht im Kokillengussverfahren hergestellt werden können, ist der Feinguss jedoch normalerweise die beste Option.
Wann sollte man Alternativen verwenden?
Die Wahl der besten Alternative zum Kokillengussverfahren hängt von den Anforderungen an das Teil und den Produktionsbedingungen ab. Sandguss ist beispielsweise ideal für einmalige oder große, schwere Teile. Druckguss eignet sich für Großserien, bei denen es auf grobe Details ankommt. Niederdruckguss ist perfekt, wenn die Zwecke eine verbesserte innere Integrität erfordern. Schleuderguss ist unschlagbar, wenn es um runde Teile geht, während Feinguss besser für komplexe und sehr präzise Teile geeignet ist.
Bei jeder Methode gibt es unterschiedliche Kompromisse in Bezug auf Preis, Werkzeuge, Geschwindigkeit und Teilequalität. Dabei liegt die Entscheidung in der Regel in der Abwägung dieser Faktoren mit der Funktion und dem ästhetischen Aspekt des Endprodukts.
Prozessparameter: Temperatur, Druck und Zeit
Mehrere technische Parameter beeinflussen den Erfolg des Kokillengusses:
1. Gießtemperatur
Bei Aluminiumlegierungen liegt diese in der Regel bei 650 - 750 °C. Wird zu heiß gegossen, kann dies zu Gaseinschlüssen und Porosität führen. Ist es zu kalt, gelangt das Metall möglicherweise nicht vollständig in die Form.
2. Formtemperatur
Die Gussformen werden normalerweise auf 150 bis 300 °C erhitzt. Eine vorgewärmte Form stellt sicher, dass das Metall nicht zu schnell erstarrt und der Metallfluss reibungsloser verläuft.
3. Abkühlzeit
Das Metall muss erstarren, bevor es nach dem Gießen entfernt wird. Die Abkühlungszeiten variieren je nach Legierung und Teilegeometrie, liegen aber in der Regel zwischen 20 und 90 Sekunden.
4. Nur Schwerkraft (kein externer Druck)
Beim Schwerkraftgießen werden im Vergleich zum Druckgießen keine äußeren Kräfte eingesetzt. Diese Einfachheit führt zu einer Verringerung der Kosten und des Verschleißes der Ausrüstung.
5. Schmierung und Beschichtung
Die Oberflächen der Matrizen werden geschmiert, um das Ablösen und die Oberflächengüte zu erleichtern. Zu den typischen Beschichtungen gehören Bornitrid und Graphitsuspensionen.
Diese drei Parameter müssen sehr gut kontrolliert werden, um qualitativ hochwertige Gussteile mit minimalen Mängeln wie Porosität, Schrumpfung und Kaltverformung zu optimieren.
Anwendungen des Schwerkraftgießens
Das Kokillengießen ist eines der beliebtesten Metallgießverfahren, das aufgrund seiner Fähigkeit, präzise, langlebige und komplexe Teile aus Nichteisenmetallen herzustellen, in einer Vielzahl von Branchen breite Anwendung findet. Das Verfahren bietet eine hohe Wiederholbarkeit, angemessene mechanische Eigenschaften und eine genaue Maßkontrolle, was es sowohl für strukturelle als auch für funktionelle Anwendungen geeignet macht. Im Folgenden werden die wichtigsten Sektoren und einige Beispiele aufgeführt, in denen das Schwerkraftgießen kritisch eingesetzt wird.
1. Autoindustrie
Die Automobilindustrie ist einer der größten Abnehmer von Kokillengussteilen. Die Technik ist perfekt für die Herstellung von Teilen die sich durch Festigkeit, Hitzebeständigkeit und Formbeständigkeit auszeichnen müssen.
Zu den wichtigsten Anwendungen gehören:
- Zylinderköpfe und Motorblöcke
- Bremssättel und Hauptzylinder
- Aufhängungshalterungen und Querlenker
- Getriebegehäuse
Das Schwerkraftgießen ermöglicht die Herstellung komplexer Geometrien mit glatten Innenflächen, was für den effizienten Transport von Flüssigkeiten in Motoren und Bremsen sehr wichtig ist. Die Bauteile arbeiten bei Temperaturen zwischen 90 und 120 °C, aber die Festigkeit des Materials ist ein wichtiges Konstruktionskriterium.
2. Luft- und Raumfahrt und Luftfahrt
Gewichtsreduzierung und Zuverlässigkeit sind in der Luft- und Raumfahrt wichtig. Kokillenguss wird für Teile verwendet, die leicht und gleichzeitig haltbar sein müssen und bei denen keine Kompromisse bei den Abmessungen und der Ermüdungsbeständigkeit gemacht werden.
Typische Gussteile für die Luft- und Raumfahrt sind:
- Halterungen
- Komponenten des Gehäuses
- Luftkanalsysteme
- Motorabdeckungen
Aluminium- und Magnesiumlegierungen werden wegen ihres guten Verhältnisses zwischen Festigkeit und Gewicht häufig für Teile in der Luft- und Raumfahrt verwendet. Die Gussteile müssen atmosphärischen Belastungen, Temperaturschwankungen von -55°C bis 125°C während des Flugs und den mechanischen Vibrationen während des Flugs standhalten.
3. Industriemaschinen
Das Schwerkraftgießen wird im Schwermaschinenbau und in der Industrie eingesetzt, um Teile herzustellen, die unter erhöhter Belastung eine hohe Festigkeit und Verschleißfestigkeit aufweisen müssen.
Zu den gängigen Komponenten gehören:
- Getriebegehäuse
- Pumpengehäuse
- Kompressorgehäuse
- Verteiler
Diese Gussteile bestehen in der Regel aus Aluminium- oder Bronzelegierungen, wobei einige Konstruktionen Abweichungen in der Wandstärke und komplexe innere Hohlräume aufweisen. Der Betriebsdruck kann je nach System zwischen 10 bar und 150 bar variieren.
4. Gehäuse für Elektrik und Elektronik
Das Schwerkraftgießen wird für das Gießen von hitzebeständigen und korrosionsfesten Gehäusen für empfindliche elektrische und elektronische Komponenten verwendet.
Typische Anwendungen:
- Motorgehäuse
- Gehäuse von Beleuchtungskörpern
- Abzweigdosen
- Kühlrippen für Leistungsgeräte
Die Bauteile müssen eine hervorragende Wärmeableitung und Formstabilität gewährleisten und gleichzeitig das Eindringen von Umwelteinflüssen wie Staub und Feuchtigkeit verhindern. Aluminium-Silizium-Legierungen werden aufgrund ihrer Wärmeleitfähigkeit und Korrosionsbeständigkeit häufig für diese Zwecke eingesetzt.
5. Marine und Schiffbau
Anwendungen in der Schifffahrt erfordern Werkstoffe, die korrosionsbeständig gegen Salzwasser sind und auch ständiger Feuchtigkeit standhalten können. Kokillenguss wird verwendet, um starke Teile zu entwickeln, die unter solchen Umständen zuverlässig funktionieren.
Beispiele hierfür sind:
- Propellergehäuse
- Ventilkörper
- Gehäuse von Wasserpumpen
- Armaturen und Kupplungen
In diesem Fall handelt es sich in der Regel um Bronze und Aluminium-Bronze-Legierungen. Diese Gussteile sind eher druckdicht und funktionieren unter Bedingungen mit hoher Luftfeuchtigkeit, Salzeinwirkung und Temperaturen von 5°C bis 50°C.
6. Landwirtschaftliche Geräte
Die mit internen Kühlkanälen versehenen Kokillengussprodukte sind aufgrund ihrer Widerstandsfähigkeit gegen mechanische Stöße, Abnutzung durch Umwelteinflüsse und die Einwirkung von Düngemitteln oder Erde ein wertvoller Bestandteil von Landmaschinen.
Zu den Schwerkraftgusskomponenten gehören:
- Hydraulische Ventilkörper
- Getriebedeckel
- Halterungen
- PTO-Gehäuseeinheiten (Power Take-Off-Systeme)
Diese Geräte arbeiten in der Regel im Freien bei einer großen Temperaturspanne (-20°C bis 50°C) und müssen auch bei Schmutz, Vibrationen und korrosiven Bedingungen funktionieren.
7. Konsumgüter und Hardware
Das Schwerkraftgießen wird auch bei der Herstellung von dekorativen und funktionellen Teilen in Konsumgütern eingesetzt, die sowohl stabil als auch dekorativ sein müssen.
Die Anwendungen umfassen:
- Türgriffe und Schlösser
- Beleuchtungssockel
- Kochgeschirr
- Werkzeug-Gehäuse
Für viele dieser Teile werden in der Regel Zink- oder Aluminiumlegierungen verwendet, da sie eine hervorragende Oberflächengüte aufweisen und feine Details mit wenig Bearbeitung für das Gießen aufnehmen können.
Schwerkraftgießen Vielseitigkeit
Die Vielseitigkeit des Kokillengusses liegt in der Fähigkeit, starke, präzise und komplexe Metallteile für verschiedene Branchen herzustellen. Von der Automobilindustrie über die Luft- und Raumfahrt bis hin zur Schifffahrt und zu Konsumgütern stellt dieses Gießverfahren eine solide Lösung dar, wenn die strukturelle Integrität, die Oberflächenbeschaffenheit, die Maßgenauigkeit usw. von vorrangiger Bedeutung sind.
Die Verwendung von wiederverwendbaren Stahlformen, Nichteisenlegierungen sowie der Schwerkraft-Metallfluss machen sie zu einer effizienten und zuverlässigen Lösung für die modernen Produktionsanforderungen.
Vorteile des Schwerkraftgießens
Die Anwendung des Schwerkraftgießens hat mehrere entscheidende Vorteile:
- Bessere mechanische Eigenschaften:
Infolge der weniger schnellen Erstarrung werden die Körner gleichmäßiger geformt, so dass eine hohe Festigkeit erreicht wird.
- Wiederverwendbare Gussformen:
Metallformen können für Tausende von Zyklen wiederverwendet werden, wodurch die Kosten pro Teil sinken.
- Verbesserte Oberflächengüte:
Im Gegensatz zum Sandguss ist die Oberfläche nicht nur glatter, sondern erfordert auch weniger Bearbeitung.
- Gute Maßgenauigkeit:
Es können Toleranzen in der Größenordnung von ±0,1 mm erreicht werden.
- Umweltverträglich:
Das Verfahren des Kokillengusses ist auch deshalb nachhaltig, weil die verwendeten Formen wiederverwendet werden können und vergleichsweise wenig Abfall anfällt.
Aufgrund dieser Vorteile bevorzugen viele Hersteller den Schwerkraftguss gegenüber anderen Verfahren wie dem Sandguss, wenn sowohl Volumen als auch Qualität gefordert sind.
Grenzen des Schwerkraftgießens
Das Kokillengussverfahren hat, wie alle anderen Verfahren auch, einige Nachteile, obwohl es für sich genommen vorteilhaft ist:
- Hohe Werkzeugkosten:
Im Vergleich zum Druckguss ist der Preis für Metallformen vergleichsweise höher als der für Sandformen.
- Begrenzt auf einfache Formen:
Diese filigranen Details und Hinterschneidungen sollten ohne einen komplexen Kern schwer sein.
- Längere Zykluszeiten:
Im Vergleich zum Hochdruckguss ist die Zykluszeit aufgrund des natürlichen Fließens und Abkühlens langsamer.
- Erfordert fachkundige Bedienung:
Temperatur- und Zeitsteuerungsgriffe sind entscheidend für die Vermeidung von Defekten.
Diese Einschränkung sollte bei der Entscheidung für den Einsatz von Schwerkraftguss für ein bestimmtes Teil berücksichtigt werden.
Schlussfolgerung
Kokillenguss ist ein praktisches, effektives und genaues Verfahren zur Herstellung von Metallwerkstücken, insbesondere aus Nichteisenlegierungen wie Aluminium und Kupfer. Durch die Nutzung der Schwerkraft anstelle von äußerem Druck zeichnet sich das Verfahren durch eine hohe Oberflächenqualität und Maßgenauigkeit aus und liefert zudem ein strukturell solides Objekt, weshalb dieses Verfahren in vielen Branchen beliebt ist.
Bei der Herstellung von Automobilteilen, Komponenten für die Luft- und Raumfahrt oder Industriegehäusen liefert das Schwerkraftgießen ein kostengünstiges, konsistentes Ergebnis. Durch die genaue Kontrolle von Parametern wie Gießtemperatur, Formtemperatur und Aushärtungsdauer können die Hersteller Gussteile herstellen, die in Bezug auf Leistung und Zuverlässigkeit hoch spezifiziert sind.
Angesichts des steigenden Bedarfs an leichten, stabilen und umweltfreundlichen Metallteilen ist die Kokillenguss ist eine wichtige Technologie im modernen Fertigungsparadigma.