Hay muy pocos lugares donde uno pueda aprender a soldar aluminio fundido, y el conjunto de habilidades necesarias para hacerlo es muy especializado. Sin embargo, el aluminio fundido es un material que se crea vertiendo aluminio fundido en un molde, lo que da como resultado un material poroso con impurezas. Esto no ocurre con las aleaciones de aluminio estándar. Debido a estas características, la soldadura es más difícil, y es necesario prepararla con cuidado, controlar el calor con precisión y utilizar las técnicas adecuadas para producir soldaduras fuertes y robustas. La oxidación es uno de los mayores obstáculos a la hora de soldar aluminio fundido. Esta fina capa de óxido, que se forma cuando se expone al aire, es mucho más gruesa que la que se forma de forma natural en el aluminio, y se funde a una temperatura mucho más alta que el propio aluminio, lo que dificulta la fusión. Además, la presencia de impurezas y gases atrapados en el aluminio fundido puede dar lugar a porosidad, que proporciona soldaduras débiles si no se limpian y precalientan adecuadamente.
El TIG (gas inerte de tungsteno) es el método preferido para la precisión y la limpieza, mientras que el MIG (gas inerte metálico) es útil para la velocidad y el material más grueso. Para obtener una soldadura fuerte y sin defectos, es necesario utilizar el metal de aportación correcto (como 4045, 5356 o 4047) y la combinación de gas de protección (de argón puro o mezclas de argón y helio). Una buena preparación incluye una limpieza y precalentamiento adecuados en la medida de lo posible para minimizar el agrietamiento, la porosidad y la falta de fusión. La resistencia y la vida útil de las uniones soldadas se mejoran aún más con tratamientos posteriores a la soldadura, como el alivio de tensiones, el esmerilado y la protección contra la corrosión después de la soldadura.
Aunque la mayoría de los soldadores de aluminio fundido son de acero soldado, los soldadores pueden trabajar con éxito con aluminio fundido utilizando las técnicas y herramientas adecuadas y prestando atención a los detalles, siempre que en las industrias se requieran componentes ligeros y de alta resistencia. Se trata de un proceso dominable que conduce a un mayor desarrollo de las aplicaciones de soldadura de aluminio y a un rendimiento fiable y predecible de las estructuras de aluminio en entornos críticos.
Comprender el aluminio fundido
Sin embargo, antes de proceder con las técnicas de soldadura necesarias para el aluminio fundido, es fundamental comprender bien en qué consiste el aluminio fundido y qué lo diferencia de otros metales. El aluminio fundido difiere del aluminio forjado, que se moldea mecánicamente mediante laminación o extrusión, en que el aluminio fundido puede adoptar formas complejas de gran precisión fundiendo aluminio y vertiendo esta forma fundida en un molde. La estructura interna única así producida, normalmente caracterizada por porosidad, impurezas y composición variable de la aleación, tiene un efecto importante en la soldabilidad.
Para poder soldar aluminio fundido con éxito, hay que conocer sus propiedades químicas y físicas, sus pros y sus contras, así como los distintos tipos de aleaciones de aluminio fundido de diversas industrias. Estos factores se tendrán en cuenta para determinar el método de soldadura necesario, la selección del material de aportación y las técnicas de preparación previas a la soldadura para realizar soldaduras resistentes y sin defectos.
Propiedades del aluminio fundido: ¿Qué diferencia a una fundición?
Otra consideración importante que el uso de aluminio fundido tiene varias propiedades que lo hacen ligero, anticorrosivo y muy flexible. Sin embargo, las mismas propiedades también plantean algunas dificultades cuando se está soldando, siempre que no se tomen las medidas adecuadas.
1. Porosidad: El reto oculto
Posiblemente una de las mayores preocupaciones de la soldadura del aluminio fundido es la porosidad; se conoce como las pequeñas burbujas de gas que quedan atrapadas en el metal cuando se está fundiendo. Estos ocho son el resultado del atrapamiento de gases como el hidrógeno, la formación de pequeños poros como resultado de la contracción durante el enfriamiento del metal de aluminio y las impurezas.
🔹 Cómo afecta la porosidad a la soldadura
- Debilita la resistencia mecánica y la soldadura puede agrietarse.
- Contribuye a la contaminación de las soldaduras y, por tanto, socava la resistencia de las uniones realizadas.
- Asegura los gases en la zona de soldadura, una vez formadas las irregularidades de la superficie.
🔹 Cómo minimizar la porosidad durante la soldadura
- La preparación de la superficie del metal mediante la limpieza debe ser adecuada antes de empezar a soldar.
- Agarre el papel de aluminio y caliéntelo para reducir cualquier tensión térmica en el aluminio y también para minimizar la formación de burbujas de aire.
- Para ello debe utilizarse gas inerte de alta calidad 100% Argón para evitar la oxidación.
2. La oxidación: La barrera para las soldaduras limpias
Es un elemento que reacciona con otros elementos, en particular con el oxígeno que se encuentra en el espacio que rodea al metal. Esta oxidación genera una piel muy fina pero extremadamente dura de óxido de aluminio (Al₂O₃) a través de la cual se impide la corrosión ulterior del aluminio. Sin embargo, la capa de óxido es un problema crítico a la hora de soldar, ya que su temperatura de fusión ronda los 2037°C (3700°F), muy superior a la del aluminio, 660°C (1221°F).
Investigación sobre por qué la oxidación es un problema en la soldadura
- ¿Es decisivo para la formación de la unión larga entre el relleno de soldadura y el metal base?
- Esto provocaba contaminación en el baño de soldadura y, por tanto, soldaduras deficientes.
- Necesita preparación antes de la soldadura, ya que tiene una capa de óxido.
🔹 Diferentes técnicas de eliminación y control de la oxidación
- Enjuague el artículo de aluminio con agua tibia, Después, debe utilizar un cepillo de acero inoxidable que sólo se debe utilizar para la limpieza de aluminio para fregar la capa de óxido.
- Limpie la superficie con acetona o alcohol como proceso de limpieza previo a la soldadura, ya que el aceite flota en los metales y la grasa se hunde.
- Para cortar la oxidación, se recomienda utilizar CA en la soldadura TIG.
3. Sensibilidad térmica: Gestión de la conductividad térmica
A diferencia del acero, el aluminio tiene una alta conductividad térmica y puede absorber y emitir calor con facilidad. Esto siempre ha supuesto un problema a la hora de mantener una temperatura de soldadura estándar:
- Fusión incompleta debido a la rápida pérdida de calor.
- Tres, deformaciones o distorsiones principalmente en piezas finas de aluminio.
- Quemaduras, especialmente en secciones muy porosas o delgadas de aluminio fundido.
🔹 Cómo superar los problemas de sensibilidad al calor
- Esto se hace para regular el flujo de calor de tal manera que todas las partes del material utilizado estén a la temperatura deseada.
- Ser capaz de poner a punto el sistema de control térmico y el uso inclinado de la soldadura TIG.
- De esta forma se puede reducir la cantidad de calor que se aplica en la zona de soldadura, utilizando pasadas de soldadura más cortas.
Tipos comunes de aleaciones de aluminio fundido
Se pueden fundir varios tipos de aleaciones de aluminio en función de su composición química y propiedades mecánicas. He aquí algunas de las ventajas y desventajas de cada tipo, así como las aplicaciones en las que serían más útiles.
1. Aluminio fundido A356: La aleación de alta resistencia
Su composición: Comprende principalmente aluminio (Al), silicio (Si) y magnesio (Mg).
Características principales
- Tiene una gran resistencia a la tracción y es adecuado para aplicaciones estructurales.
- Excelente resistencia a la corrosión, especialmente en ambientes húmedos.
- Tiene buena soldabilidad, aunque puede ser necesario un tratamiento térmico posterior a la soldadura para recuperar la resistencia.
🔹 Aplicaciones comunes
- Se utiliza en componentes de motores, ruedas y cajas de transmisión de la industria del automóvil.
- Industria aeroespacial: se utiliza en piezas estructurales de aviones por su relación resistencia-peso.
- Dispositivos médicos - Se utiliza en instrumentos quirúrgicos y carcasas de alta resistencia.
2. 319 Aluminio fundido: El allo resistente al desgaste
Composición: Contiene niveles más altos de silicio (Si) y cobre (Cu) que el A356.
Características principales
- Muy buena resistencia al desgaste para aplicaciones pesadas.
- Es más quebradizo y tiene un mayor contenido de silicio, por lo que es más difícil de soldar.
- Se necesitan materiales de relleno especializados (4047) para evitar el agrietamiento.
🔹 Aplicaciones comunes
- Variantes resistentes al desgaste: culatas de automóviles y bloques de motor.
- Las bombas y las carcasas deben ser duraderas.
- Las piezas para maquinaria industrial están destinadas a las condiciones más severas y de mayor tensión mecánica.
3. 535 Aluminio fundido: La aleación para uso marino
Composición: Contiene un alto porcentaje de magnesio (Mg) para resistir la corrosión.
Características principales
- Resistencia superior a la corrosión, especialmente en entornos de agua salada.
- La soldabilidad es buena, pero se requiere una limpieza completa previa a la soldadura para evitar la contaminación.
- Más fácil de moldear y reparar que la 319.
🔹 Aplicaciones comunes
- Su alta resistencia a la corrosión del agua salada los hace adecuados para cascos de embarcaciones, piezas de motores marinos y hélices.
- Se utiliza para piezas aeronáuticas y aeroespaciales que requieren materiales resistentes y ligeros.
- Elementos que suponen una amenaza mínima para los componentes industriales sometidos a entornos químicos agresivos.
Por qué es importante comprender la fundición de aluminio para soldar
Empezar a dominar la soldadura de aluminio fundido consiste en determinar de qué está hecho el aluminio fundido, sus propiedades y los retos asociados. Por lo tanto, como el aluminio fundido se utiliza ampliamente en la ingeniería de automoción, aeroespacial y naval, los soldadores necesitan estrategias para la porosidad de la fundición, la oxidación y la sensibilidad al calor.
Diferentes tipos de escayola aleaciones de aluminio responden a la soldadura de forma diferente, y usted debe elegir los materiales de aportación, el gas de protección y la técnica de soldadura correctos, lo que supone la diferencia entre una soldadura fuerte y fiable o una unión débil y porosa.
Con la preparación del material, el uso de los procedimientos de limpieza correctos y la regulación del aporte de calor, los soldadores pueden abordar los problemas asociados al aluminio fundido y generar soldaduras potentes y duraderas que cumplan con las duras aplicaciones.
Desafíos de la soldadura del aluminio fundido
La soldadura de aluminio fundido es notoriamente difícil debido a las propiedades físicas y químicas únicas del aluminio fundido. El conocimiento de estos retos ayuda a los soldadores a utilizar las herramientas y los métodos de aplicación adecuados, lo que da como resultado soldaduras fuertes y sin defectos.
1. Problemas de oxidación: Un importante obstáculo para la soldadura
Cuando el aluminio se expone al aire, se oxida casi instantáneamente, produciendo óxido de aluminio (Al₂O₃) muy fino pero muy resistente. A continuación, explicó que la capa de óxido formada durante la oxidación inicial del aluminio tiene un punto de fusión de 2.037°C (3.700°F), tres veces superior al punto de fusión del aluminio, que es de 660°C (1.221°F). Sin embargo, esta enorme diferencia en los puntos de fusión provoca graves dificultades en la soldadura, entre las que cabe destacar las siguientes:
- Fusión incompleta (la capa de óxido impide que el metal de aportación se adhiera correctamente al material base).
- Soldaduras contaminadas - Presencia de oxidación, que puede causar porosidad, uniones débiles e inclusiones cuando se deja en la soldadura.
- El óxido produce un arco inestable, que hace que el arco se desplace y el rendimiento de la soldadura sea errático.
Solución
La soldadura TIG con corriente alterna (CA) ayuda a mantener la capa de óxido fuera de la pieza y a conservar la estabilidad del arco. Además, un cepillo específico para acero inoxidable y limpiadores químicos como la acetona pueden limpiar la oxidación antes de soldar.
2. Impurezas y contaminación: La amenaza oculta
El aluminio suele fundirse a partir de materiales reciclados, por lo que puede incluir gases atrapados, residuos de aceite, suciedad y otras impurezas relacionadas con la producción de la fundición. Estos contaminantes deben limpiarse correctamente antes de soldar, o pueden provocar:
- La soldadura se debilita y es propensa a agrietarse debido a las pequeñas bolsas de gas (porosidad).
- Inclusiones: - Ha quedado atrapada en la soldadura una sustancia no metálica que reduce la resistencia de la soldadura.
- Algunas zonas pueden fusionarse bien y otras pueden quedar débiles con una calidad de soldadura irregular.
Solución
Se utiliza acetona o alcohol para limpiar a fondo la superficie de grasa y suciedad. Los gases atrapados deben expulsarse con un soplete de precalentamiento antes de soldar.
3. La conductividad térmica es demasiado alta: Es necesario controlar el calor
En cambio, el aluminio absorbe y transmite el calor con extrema rapidez, en comparación con el acero. Esto puede dar lugar a:
- Demasiado calor puede fundir las secciones más finas (quemar).
- Calentamiento desequilibrado (alabeo y distorsión) - El metal se estropea porque se ha calentado de forma desigual.
- Penetración inconsistente - Disipación de calor demasiado rápida que provoca una fusión débil en la unión soldada.
Solución
Además, es conveniente precalentar el aluminio a 150°C - 315°C (300°F - 600°F) para obtener una distribución uniforme del calor y una mejor penetración de la soldadura. Un mayor aporte de calor a la velocidad de desplazamiento controlada mantiene estable el baño de soldadura.
Herramientas y equipos esenciales para soldar aluminio fundido
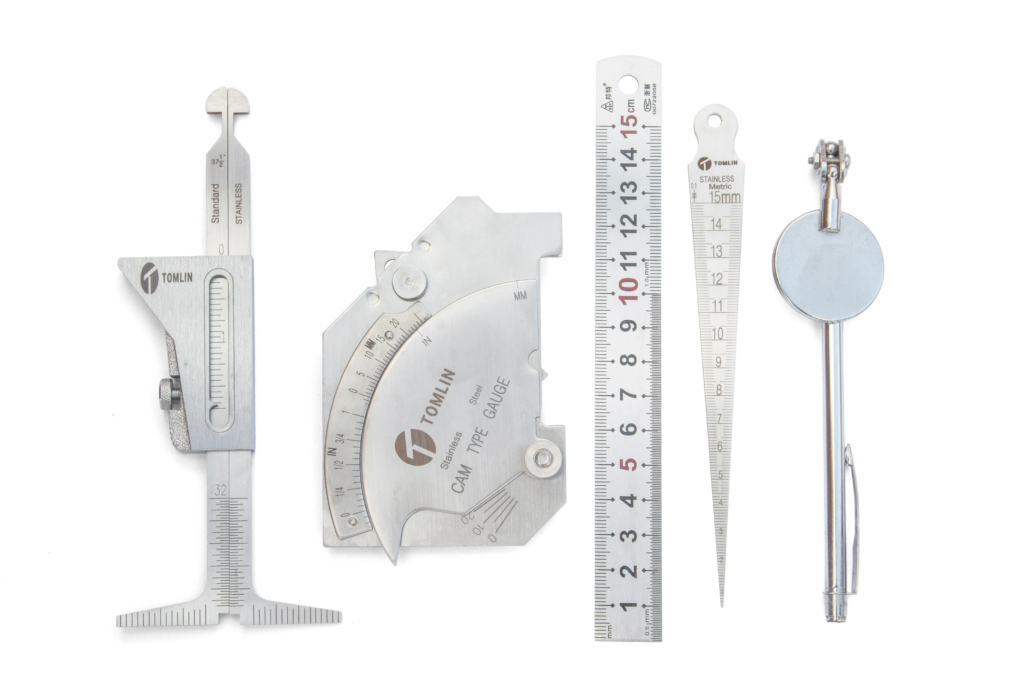
Al soldar aluminio fundido, se requiere un equipo especializado y debe soldarse con precisión, con fuerza y tiene durabilidad en la soldadura.
- Un proceso de soldadura es en sí mismo una herramienta que debe elegirse con cuidado, y eso es lo que se trata en esta guía de máquinas de soldar.
- La selección correcta de la máquina de soldar es muy importante cuando se va a soldar aluminio.
- Soldadora TIG (gas inerte de tungsteno) (GTAW) - La mejor para soldaduras de precisión y alta calidad. Permite un mejor control de la entrada de calor y es buena para la reparación de aluminio fundido.
- TIG (gas inerte de tungsteno) - Adecuado para metales internos, pero mucho más lento que el MIG. Lo mejor para secciones de fundición de aluminio más gruesas.
1. Metales de aportación: Refuerzo de la soldadura
Una soldadura fuerte y sin grietas depende de una buena varilla de relleno.
- 4045 Masilla de Aluminio - Opción de uso general para reparaciones de aluminio fundido.
- Relleno de aluminio 5356 - Proporciona alta resistencia y resistencia a la corrosión, ideal para aplicaciones marinas.
- Relleno de aluminio - 4047 tiene un alto contenido de silicio para la reducción de la formación de grietas, la mejora de la escorrentía
2. SHEILDING GAS
Como su nombre indica, es un gas presente en el fundente de soldadura que evita la oxidación y la porosidad. Suelen ser gases inertes elegidos por sus propiedades deseadas.
- La soldadura se protege de la contaminación atmosférica mediante gas de protección.
- Argón 100% - para soldadura TIG y MIG, la mejor elección para conseguir un arco estable y un baño de soldadura limpio.
- Mezcla de argón y helio - El helio aumenta la entrada de calor y la penetración, por lo que se utiliza para cortar secciones de aluminio más gruesas.
3. Herramientas de limpieza y preparación
La soldadura no puede tener éxito hasta que no haya una superficie limpia.
- Elimina la oxidación sin contaminar la superficie, cepillo de acero inoxidable.
- Si necesita limpiar aceite, grasa o suciedad antes de soldar, la acetona o el alcohol funcionarán bien.
- Se evita el choque térmico y se expulsa la humedad y los gases atrapados.
Preparación del aluminio fundido para la soldadura
Hay que evitar los defectos y obtener una soldadura fuerte mediante una preparación adecuada.
Paso 1: Limpieza de la superficie
Como el aluminio retiene tanto la suciedad, la grasa, la oxidación y la humedad, no queda más remedio que limpiar.
🔹 ¿Por qué es importante la limpieza?
- Evita la porosidad y la contaminación.
- Ayuda a una mejor fusión entre el metal de aportación y el material base.
- Ayuda a mantener el arco estable durante la soldadura.
🔹 Proceso de limpieza:
- El aluminio puede desengrasarse con acetona o alcohol para eliminar el aceite y los contaminantes.
- Retire SIEMPRE la capa de óxido con un cepillo de acero inoxidable (dedicado sólo para aluminio).
- Es importante evitar tocar la superficie limpiada con las manos desnudas para prevenir la recontaminación.
Paso 2: Precalentar el aluminio
Reduce la tensión interna y mejora la penetración de la soldadura.
🔹 ¿Por qué Precalentar?
- Minimiza las grietas en el aluminio fundido poroso.
- Asegura una mejor distribución del calor y calidad de la soldadura.
- Ayuda a expulsar los gases y la humedad atrapados.
🔹 Cómo precalentar el aluminio fundido:
- Rectificar la pieza a 150°C - 315°C (300°F - 600°F).
- Se puede utilizar un termómetro de infrarrojos para controlar la temperatura.
- También puede debilitarse por sobrecalentamiento; evítelo.
Técnicas de soldadura del aluminio fundido
Para soldar con éxito aluminio fundido, hay que asegurarse de utilizar la técnica correcta, mantener un buen control del calor y utilizar los parámetros de soldadura adecuados. A continuación se indican los mejores métodos de soldadura para aluminio fundido con detalles sobre sus mejores prácticas.
1. Soldadura TIG (la mejor por su precisión y resistencia)
El método preferido para soldar aluminio fundido es la soldadura con gas inerte de tungsteno (TIG) o la soldadura por arco de tungsteno con gas (GTAW) porque tiene la precisión necesaria para producir soldaduras limpias y fuertes.
🔹 Consejos clave para la soldadura TIG
- Utilice el modo CA: El modo CA permite una ruptura más eficaz de la capa de óxido de aluminio y la estabilidad del arco.
- A 15° es el mejor ángulo para la antorcha: Esto le asegura una penetración uniforme y sin contaminación.
- La longitud de arco corta es importante: Cuanto más corto es el arco, mejor es el control del calor y menos propenso a quemaduras y porosidad.
- Elija la varilla de relleno adecuada: la 4047 (con alto contenido en silicio) reduce el agrietamiento y la 5356 proporciona superioridad en fuerza y resistencia a la corrosión.
- Arranque de alta frecuencia, proporciona un arranque suave del arco sin contaminar el electrodo con tungsteno.
Mejor para: Piezas finas de fundición de aluminio, reparaciones de precisión, aplicaciones aeroespaciales y navales.
2. Soldadura MIG (la más rápida y eficaz)
Una alternativa más rápida a la soldadura TIG, excepto para secciones de aluminio muy gruesas, es la soldadura con gas inerte metálico (MIG), también conocida como soldadura por arco metálico con gas (GMAW). Sin embargo, el control de la tensión y la velocidad del hilo durante la soldadura MIG es muy importante para evitar defectos como porosidad o quemaduras.
🔹 Consejos clave para la soldadura MIG:
- Utiliza una técnica de empuje: Si tiras hacia atrás para acercarte, contaminas completamente la superficie y no queda tan limpia.
- En el modo de transferencia por pulverización, se eliminan las salpicaduras significativas y el arco es muy estable, produciendo una soldadura de alta calidad.
- Los ajustes adecuados permiten una buena fusión sin sobrecalentamiento.
- El helio mejorará la penetración y puede utilizarse para secciones más gruesas, o utilizar argón puro o una mezcla de argón y helio.
- El precalentamiento de la pieza ayuda a reducir el choque térmico y disminuye el agrietamiento.
Mejor para: Piezas de fundición de aluminio más gruesas, reparaciones de automóviles, aplicaciones industriales.
3. Métodos de soldadura alternativos (cuando surja un caso especial)
En ocasiones, la soldadura TIG o MIG no será el mejor método debido a la sensibilidad al calor, la complejidad de la pieza o la necesidad de reparación. Para casos especiales, pueden utilizarse los siguientes métodos alternativos.
- La soldadura fuerte es el uso de un metal de aportación a baja temperatura que minimiza el riesgo de distorsión o debilitamiento de los componentes sensibles al calor.
- La transferencia de metal en frío (CMT) es de bajo calor y la tensión térmica es menor, ideal para reparaciones delicadas.
- Soldadura por láser: puede suministrar un aporte térmico local preciso a componentes de aluminio de paredes finas.
Mejor para: Aplicaciones de bajo calor, reparaciones menores y soldadura de alta precisión.
Defectos de soldadura y cómo solucionarlos
Los componentes de aluminio fundido plantean problemas incluso a los soldadores experimentados debido a la porosidad, el agrietamiento y las dificultades de fusión. Estos defectos, y las formas de evitarlos y solucionarlos, son de vital importancia si se quiere conseguir alguna vez soldaduras fiables, fuertes y duraderas.
1. Porosidad (bolsas de gas en soldaduras)
Las bolsas de gas atrapadas en la soldadura se consideran porosidad, lo que debilita la estructura. Dado que el aluminio fundido es "poroso" por naturaleza, es más propenso a este defecto.
🔸 Causas
- O Contaminación con suciedad, aceite, grasa u oxidación.
- Un caudal bajo de gas de protección o una fuga en el sistema.
- Tiene un enfriamiento rápido, que atrapa el gas en la soldadura.
Soluciones
- Asegúrate de que la superficie del aluminio está limpia antes de soldar, y límpiala a fondo con acetona o incluso alcohol.
- Elimine la oxidación con un cepillo de acero inoxidable (dedicado al aluminio).
- Mantener un caudal de gas adecuado (15-25 CFH para Argón puro).
- Reduzca la expansión del gas atrapado y aumente la penetración precalentando la pieza.
- Reducir los problemas de porosidad utilizando un relleno de silicona más alto (por ejemplo, 4047).
Consejo profesional: Mantenga siempre el metal de aportación seco y sin humedad, ya que la presencia de humedad en las varillas de aportación puede introducir porosidad en la soldadura.
2. Agrietamiento (soldaduras débiles y quebradizas)
Una de las razones más comunes del agrietamiento es la elevada tensión térmica o la selección de un material de relleno inadecuado. El aluminio se contrae mucho al enfriarse, lo que genera tensiones que provocan grietas.
🔸 Causas
- Provoca grietas de contracción bajo una gran tensión térmica.
- Emplear el metal de aportación equivocado y, por tanto, la incompatibilidad.
- El precalentamiento es insuficiente, lo que provoca un enfriamiento desigual y la acumulación de tensiones.
Soluciones
- Caliente la pieza a 150°C -315°C (300°F - 600°F) para minimizar el choque térmico.
- Utilice una varilla de relleno de alto contenido en silicio de 4047, que resiste el agrietamiento.
- Asegúrese de que la soldadura se enfría lentamente para que no se produzcan fracturas por tensión.
- Las piezas de fundición de aluminio de gran tamaño pueden soldarse mediante una técnica multipaso para distribuir el calor uniformemente y reducir las tensiones.
Consejo profesional: Si aparecen grietas después de soldar, elimínelas con una amoladora de troqueles, limpie la zona y vuelva a soldar con el precalentamiento adecuado.
3. Falta de fusión (unión débil entre el metal y el cordón de soldadura)
Se dice que no hay fusión cuando ésta no se ha producido entre el cordón de soldadura y el material base, formando una unión más débil. A menudo, la causa de este defecto es un aporte térmico insuficiente o unas técnicas de soldadura inadecuadas.
🔸 Causas
- Baja entrada de calor restringe de que se puede fundir correctamente.
- Velocidad de desplazamiento rápida y sin penetración.
- Así se crea la fusión incompleta causada por un ángulo incorrecto de la antorcha.
Soluciones
- Aumente los ajustes de calor para penetrar correctamente en el metal base.
- La velocidad de desplazamiento debe reducirse para permitir que los núcleos se fusionen más profundamente.
- Mantenga un ángulo constante de la antorcha (10-15 grados) para una penetración consistente.
- Para una mezcla de gas Helio-Argon y aluminio grueso fundido, la entrada de calor subirá.
Consejo profesional: En caso de que se detecte falta de fusión, se rectifica la soldadura defectuosa, se limpia la superficie y se vuelve a realizar la soldadura con mayor calor y menor velocidad de desplazamiento.
Tratamiento y acabado posteriores a la soldadura
Una vez finalizada la operación de soldadura, la solidez, la durabilidad y la resistencia a la corrosión sólo pueden garantizarse mediante un acabado adecuado y tratamientos posteriores a la soldadura.
Paso 1: Tratamiento antiestrés
- Después, la soldadura se enfría lentamente para evitar tensiones residuales y grietas.
- Si es necesario, debe emplearse un tratamiento térmico posterior a la soldadura para restaurar la resistencia mecánica de los componentes críticos.
- No enfriar la soldadura con agua o chorro de aire, ya que un enfriamiento rápido podría provocar nuevas grietas.
Consejo profesional: Se recomienda cubrir la pieza soldada con una manta térmica para que se enfríe gradualmente y se reduzca el riesgo de grietas por tensión.
Paso 2: Esmerilado y pulido
- Si el exceso de material de soldadura y alisar la superficie, utilice un disco de láminas o amoladora de troqueles.
- Si la aplicación es para un cosmético pulido, entonces pulir el aluminio en papel de lija fino (600 - 1200 Grit) o ruedas de pulido.
- Para terminar, mezcle la soldadura con el metal circundante si es necesario.
Consejo profesional: No utilice una herramienta de amolar de acero al carbono sobre aluminio, porque la contaminación puede causar problemas de corrosión.
Paso 3: Protección contra la corrosión
Aunque el aluminio es naturalmente resistente a la corrosión debido a la capa de óxido, se puede ofrecer una mayor protección en el caso de entornos agresivos para aumentar su vida útil.
- Anodizado - Se refiere a un procedimiento en el que se forma una capa protectora de óxido para aumentar la resistencia a la corrosión y mejorar el aspecto de la pieza.
- Recubrimiento en polvo - Proporciona a la pieza un acabado duradero que la protege contra el desgaste y los daños causados por el medio ambiente.
- Pintura o sellantes - Proporciona una protección rentable para piezas no críticas.
Consejo profesional: Si se utiliza pintura, debe emplearse una imprimación de grabado, ya que aumentará tanto la adherencia como la durabilidad.
Aplicaciones prácticas de la soldadura de aluminio fundido

La soldadura de aluminio fundido se utiliza habitualmente en muchas industrias, como la reparación de automóviles o la fabricación aeroespacial, entre otras.
1. Reparación de automóviles
- La capacidad de la soldadura TIG para localizar y reparar bloques de motor, culatas y cajas de transmisión.
- Reparación de llantas de aleación y componentes de la suspensión agrietados.
- Refuerzo de piezas del chasis para altas prestaciones o todoterreno.
Consejo profesional: Los componentes de aluminio soldado se encuentran en muchos vehículos de competición de alto rendimiento con el fin de mantener el peso bajo, pero aún así mantener la fuerza.
2. Aeroespacial y aviación
- Reparación de componentes del fuselaje de aeronaves y piezas del motor.
- Soldadura de estructuras de aluminio del tren de aterrizaje y el fuselaje para reducir el peso y mantener la resistencia.
- Fabricación de piezas aeroespaciales a medida, como depósitos de combustible, estructuras de alas y recipientes a presión.
Consejo profesional: A356 y 7075 son aleaciones de aluminio de calidad aeroespacial que sólo se sueldan si se utilizan técnicas especiales y un control térmico riguroso para mantener la integridad de la soldadura.
3. Industria naval
- Reparación de embarcaciones de aluminio, hélices y carcasas de motores marinos.
- Soldadura de aluminio marino resistente al agua salada.
- Reparación de estructuras offshore y componentes de construcción naval sometidos normalmente a entornos agresivos.
Consejo profesional: Para todas las aplicaciones marinas, el material de relleno debe ser siempre del tipo resistente al agua salada, como el 5 356.
4. Industria y construcción
- Reparación de piezas de maquinaria pesada y equipos de fábrica.
- Refuerzo de andamios de aluminio, tuberías y vigas de soporte.
- Fabricación de estructuras de aluminio a medida para la industria y la construcción.
Consejo profesional: El precalentamiento de grandes estructuras de aluminio fundido para la soldadura con el fin de evitar el agrietamiento y la distorsión se realiza generalmente en entornos industriales.
Conclusión
La soldadura de aluminio fundido es un proceso especializado que exige la combinación perfecta de preparación, equipo y conocimientos de soldadura de primera clase para realizar bien la tarea. Seguir los métodos correctos de limpieza, precalentamiento y soldadura le asegurará soldaduras fuertes y fiables. Sin embargo, no tiene por qué dedicarse a la industria aeroespacial, naval o automovilística ni a aplicaciones industriales para beneficiarse de la soldadura de aluminio fundido para reparaciones o fabricación. Con tiempo y práctica, paciencia y atención a los detalles, el aluminio fundido será algo que soldará sin apenas problemas, con defectos mínimos y resultados de calidad profesional. Con su técnica, hay que invertir tiempo para crear soldaduras que duren toda la vida de una pieza, en aplicaciones de alta resistencia.
Preguntas frecuentes sobre la soldadura de aluminio fundido
1. ¿Qué factores se consideran más difíciles en la soldadura de aluminio fundido?
La porosidad, la oxidación y la elevada conductividad térmica del aluminio fundido aumentan las fisuras, la porosidad y la debilidad de las soldaduras. La capa de óxido que lo recubre se funde a temperaturas muy superiores a las de fusión del propio aluminio, por lo que resulta difícil fundirlo.
2. ¿Cuál es el mejor tipo de soldadura de una fundición de aluminio?
El TIG permite realizar soldaduras precisas y limpias, mientras que el MIG es adecuado para materiales más gruesos. Las soldaduras fuertes requieren precalentamiento, el relleno correcto y gas de protección.
3. ¿Cuáles son las formas de evitar la porosidad y el agrietamiento?
Reduzca el estrés térmico limpiando a fondo la superficie, utilizando gas argón puro y precalentando a 300F - 600F. El uso de un metal de aportación con alto contenido en silicio (4047) puede contribuir a la resistencia al desarrollo de grietas.