ホットチャンバー・ダイカストは、金属部品を非常に高精度に、また表面の優れた仕上げを実現するために広く使用されている、非常に効果的な製造プロセスです。特に亜鉛、マグネシウム、鉛を含む合金のような融点の低い金属の鋳造に適しています。射出システムが溶融金属に浸漬されるという事実に代表されるように、高速サイクルタイムと大量生産の経済性が可能である。
コールド・チャンバー・ダイカストとホット・チャンバー・ダイカストについて鋳物を検討するとき、同じような比較対象が必ずひとつ出てくる。どちらも加圧ダイカストの一種であるが、設計、用途、使用材料の適合性などの点で大きく異なる。例えば、ホット・チャンバー・ダイカストは、炉を機械に置き換えた高速ダイカストです。そのため、低融点金属の制約がある。逆に、コールド・チャンバー・タイプの機械は、高温の金属が設備に直接触れないため、アルミニウムや真鍮のような高融点の液体に適している。
ホットチャンバーダイカストプロセスは、材料の無駄が少なく、人件費が安く、複雑な形状を高い公差で製造できるのが特徴です。自動車、電子機器、配管、消費者製品などの業界で人気があります。とはいえ、コールド・チャンバー・ダイカストとホット・チャンバー・ダイカストのどちらを使用するかは、使用する材料の種類や部品設計の側面にも左右されます。
の重要な詳細を検証している。 ホットチャンバー・ダイカストその部品、材料、工程の説明、制約、そしてなぜそれが現代の製造業において不可欠な工程なのかという理由。
ホット・チャンバー・ダイカストとは?
ホットチャンバーダイカストは、溶融金属を高圧で金型キャビティに注入する金属鋳造技術です。この方法の特徴は、射出機構がどこに配置されているかということです:溶融金属に直接注入されます。サイクルタイムと生産効率は、特に亜鉛、マグネシウム、一部の鉛合金のような低融点の金属では、このセットアップで高いです。
ホットチャンバー。この名称は、射出機構(プランジャーとグースネック)が溶融金属領域と常に接触(充填)していることから、システムのホットチャンバーを表している。プランジャーが下降すると、溶融金属がグースネックを通って金型キャビティに圧縮されます。金属が固まると金型が開き、部品が排出され、このプロセスが無数に繰り返される。
ホットチャンバー・ダイカスト・プロセス
ホットチャンバーダイカストプロセスは、金型の精度が非常に重要な金属部品の製造に利用される高精度で高速な製造技術のプロセスであり、優れた表面仕上げが施される。低融点合金に最も適しており、亜鉛、マグネシウム、鉛は低融点合金の一例である。その主な特徴は、短いサイクルタイムと優れた材料効率である。
ホットチャンバー・ダイカスト・プロセスは、複雑な端部を簡単に、しかも1個あたりの価格が手ごろなことから、主に自動車、電子機器、家電製品、金物産業など、さまざまな製品の製造に広く用いられている。ホットチャンバー・ダイカストプロセスを以下に順を追って説明する:
ホットチャンバー・ダイカスト・プロセス-ステップ・バイ・ステップの概要
1.金属を溶かす
ダイカストは、ダイカストマシンに組み込まれた炉で、金属(通常は亜鉛またはマグネシウム)を溶融成形することから始まります。溶融金属は、鋳造機に直接接続された金属ポット内で一定の温度に保たれます。この絶え間ない熱供給により、鋳造工程は連続的に行われます。
2.インジェクション・システムへの充填プロセス
ホットチャンバーシステムでは、グースネックと呼ばれる部品の一部が水没した状態で溶湯の一部が存在する。射出シリンダー内を流れるプランジャーは、溶湯がグースネックから射出注入孔に湧き出る位置まで後方に引かれる。次のステップでは、この金属を金型キャビティに射出する。
3.溶湯注入
グースネックが充填されると、プランジャーが油圧または空気圧で押し進められ、溶融金属がグースネック・チャンネルを通って金型キャビティ(ダイとも呼ばれる)に押し込まれます。これは、金属が硬化し始める前にキャビティが完全に充填されるように、高い速度と圧力で行われます。
4.鋳型での鋳造と凝固
金型内のこの高温の金属は、金型の比較的冷たい鋼鉄によって素早く冷却される。凝固には、部品のサイズと複雑さに応じて数秒かかります。このステップでは、金型冷却チャンネルが熱の除去を補助し、サイクル速度が低下しないようにし、収縮や気孔などの欠陥が発生しないようにします。
5.金型の排出と開放
金属が凝固したら、金型の半分を開きます。エジェクターシステムは金型の可動半分に設置され、エジェクターピンを使って力強く作動し、完成した鋳物をキャビティから押し出します。エジェクション中に部品が損傷することなく出てくることが保証されます。
6.二次加工とトリミング
射出された後に、フラッシュ、ランナー、スプルーと呼ばれる余分な材料が含まれることがある。これらは手作業でトリミングされるか、自動でトリミングされます。部品は、表面仕上げ、機械加工、コーティングなど、用途に応じてさらに加工することができます。
7.サイクルを繰り返す
機械は、再び使用するために清掃されます。ホットチャンバーダイカストの特徴は、サイクルタイムが非常に短いことで、部品の複雑さや大きさによっては、わずか10~20秒で数個の完成品ができることもあります。
サイクルタイムと効率
ホットチャンバー製法の最大の利点はスピードである。ホットチャンバー機。コールド・チャンバー・ダイカストでは、金属をチャンバー内に杓で入れる必要がありますが、ホット・チャンバー・ダイカストでは、金属は炉から引き抜かれます。そのため、サイクル工程が短縮され、生産効率が向上します。
このプロセスの利点
- サイクルタイムの短縮と優れた生産性
- 真の高次元性能と再現性
- 表面仕上げが向上し、多くの場合、後加工の必要性がなくなる。
- 材料を経済的に使用し、無駄を最小限に抑える。
- リーズナブルな価格で大量生産が可能なオートメーションに適している。
ホットチャンバー・ダイカスト材料
ホットチャンバーダイカストプロセスは、融点が低~中程度の金属や合金に適しています。使用される材料は、鋳造プロセス中に溶融金属で連続的に濡れるため、スチール部品(グースネックやプランジャーシステムなど)を腐食させないようにする必要があります。
ホットチャンバー・ダイカストで最も頻繁に使用される材料と、その特性および一般的な用途を以下に示す:
1.亜鉛合金
ダイカストプロセス(ホットチャンバー)で使用される最も一般的な材料は亜鉛です。鋳造性、強度、表面仕上げが良いため、様々な産業で非常に人気があります。
主なメリット
- 非常に低い融点 (~419 °C または 786 o F )
- 大きな強度対重量比
- 優れたフローと高い寸法精度
- 優れた耐食性
- 溶融温度が低く、金型寿命が長い。
亜鉛の一般的な合金:
- ザマック2、3、5、7(ザマック3が一番人気)
- ZA合金(亜鉛-アルミニウム)だが、アルミニウムの金属含有率が高い方が、コールド・チャンバーには適しているかもしれない。
アプリケーション
- 自動車部品
- 電気部品
- 構造と固定具
- 歯の正確さ ギアとケース
2.マグネシウム合金
マグネシウムは最も軽い構造用金属であり、強度重量比も優れている。ホットチャンバー・ダイカストでマグネシウムが使われる理由は、ここで使われる部品の多くが、最小の質量とともに強度を必要とするからだ。
主なメリット
- 軽量(アルミニウムより約33%軽い)
- 強度と剛性が高い。
- 優れたEMI/RFIシールド(電子機器に最適)
- 環境に優しく、リサイクル可能
一般的な合金:
- ダイカストで使用される最も一般的なマグネシウム合金はAZ91Dである。
アプリケーション
- ノートパソコンとスマートフォンの筐体
- 自動車ダッシュボードのフレーム
- 航空宇宙部品
- 電動工具
注: マグネシウムはコールド・チャンバー機でも鋳造できるが、鋳造するマグネシウムが小さい場合は、ホット・チャンバー機を使用するのが望ましい。サイクルタイムが短くなるからである。
3.鉛と錫の合金
鉛と錫の合金は、ホットチャンバー・ダイカストにおける健康と環境の制限のため、ほとんど使用されなくなったが、過去には特殊な用途で使用されていた。
主なメリット
- 低融点(~327℃(鉛)、~232℃(スズ)
- 高密度(バランスウェイトや放射線シールドなどの用途に最適)
- 優れた寸法安定性
アプリケーション
- アンティーク調の金具
- 精密機器
- 弾薬部品
- 装飾品
警告だ: その毒性のため、鉛合金は今日、多くの産業や国で厳しく制限されている。
4.カドミウム基合金(ノット・ソー・コム)
これらは、毒性や規制上の理由から適用されることはほとんどなかったが、以前は、耐摩耗性だけでなく、優れた鋳造サービスであることから選ばれていた。
高温合金が使われない理由。
ホットチャンバー・ダイカストの特徴的な限界は次のようなものである:
- アルミニウム
- 真鍮
- 銅
- スチール
この種の金属は高温になり、プランジャーやグースネックなどホットチャンバー機の水没部品と反応するため、ホットチャンバー機は損傷したり腐食したりする。コールド・チャンバー・ダイカストでは、溶融金属と射出機構を分離するため、このような金属が使用されます。
要約表ホットチャンバーダイカストに適した材料
素材 | 融点 | メリット | 典型的な使用例 |
亜鉛合金 | ~419°C | 優れた流動性、表面仕上げ、耐久性 | 自動車、エレクトロニクス、ハードウェア |
マグネシウム合金 | ~650°C | 軽量、高強度、リサイクル可能 | 航空宇宙、エレクトロニクス、自動車内装 |
鉛合金 | ~327°C | 密度が高く、キャストしやすい。 | 放射線遮蔽、弾薬 |
錫合金 | ~232°C | 細部までよく鋳造され、腐食しない | 楽器、アンティークデザイン |
アルミニウム合金がホットチャンバーダイカストに適用できない理由とは?
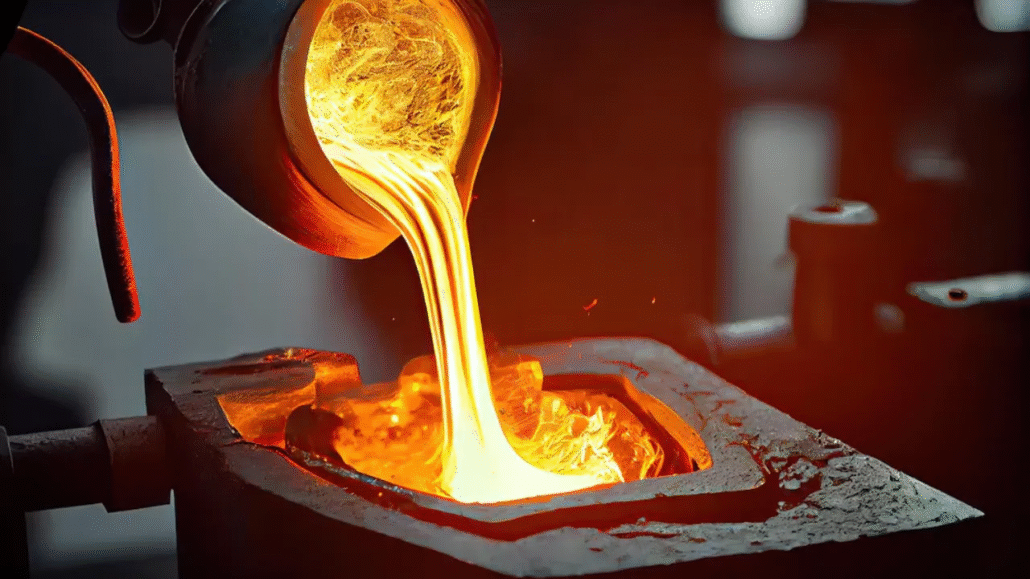
アルミニウム合金はダイカスト産業で非常に多くの用途がありますが、強度、軽量性、耐食性などの理由から、ホットチャンバーダイカストでは熱間鋳造できません。通常は、コールド・チャンバー・ダイカスト法で鋳造されます。
これを説明するために、"アルミ合金がホットチャンバー・ダイカストで使用されない "技術的、材料的な理由は何か。
1.大きな融解温度
アルミニウムがホット・チャンバー・プロセスに適合しない主な要因は、融点が高いことである。アルミニウム合金の大半は660 o C(1220 o F)以上で溶融します。
グースネックやプランジャー、その他の射出部品は、ホットチャンバー機では常に溶融金属に浸漬される。亜鉛(419℃)やマグネシウム(~650℃)のような比較的融点の低い金属の場合には効果的である。しかし、これらの部品は、アルミニウムの高温ではすぐに劣化または破壊され、装置の故障や高価な修理につながる。
- コールドチェンバー対応SACスーツ
- ホット・チェンバーは控えめに言っても暑すぎる
2.スチール部品への攻撃
アルミニウムは化学的に反応しやすく、特に高温の鉄金属を腐食する傾向があります。グースネックやノズルのようなものが溶融プールにあるホットチャンバーシステムでは、アルミニウムは腐食するだけでなく、スチール部品を食い破り、機械の寿命を劇的に縮めます。
この反応は装置の寿命を縮めるだけでなく、溶湯を汚染し、鋳造不良や最終製品の欠陥の原因となる。
3.機器の互換性の問題
ホットチャンバー機は小型で高速の機械ですが、低融点金属の迅速な反復鋳造に適しています。内蔵炉は射出システムと密接に連動しています。アルミニウムのような高融点の合金を使用するには、次のような条件が必要です:
- 強化部品
- 耐高温合金は特殊合金でできている
- より複雑な断熱システム
これでは、ホットチャンバーダイカストの簡便さとスピードの利点が生かされない。これが、組立業者が溶融アルミニウムを外部に注入し、注入システムも水没させないコールドチャンバー機を選択する理由である。
4.酸化とドロスのリスク
高温では、アルミニウムは空気の存在下で容易に酸化しやすい。この酸化により、金属が連続的に露出するホットチャンバー配置では、ドロス(酸化アルミニウム)が形成される可能性がある:
- It pollutes the metal
- Surface defects are caused by causes
- And results in mechanical deficiencies of the finished product
This risk is minimized by the fact that cold chamber die casting reduces the amount of time molten aluminum is exposed.
5.安全に関する懸念
Processing aluminum in a hot chamber machine would pose a great risk of burn injuries, leakage and breakdown of the machine. Further thermal stress associated with working at higher temperatures exposes to further threat of:
- There is bleeding molten metal leakage
- Blowing out reactions of steam
- Pressure components failure
The cold chamber systems enable improved isolation and safety regulation with these high temperatures.
アルミニウムのホットチャンバーとコールドチャンバーの比較
特徴 | ホットチャンバー・ダイカスト | コールド・チャンバー・ダイカスト |
Injection Mechanism | Submerged (gooseneck system) | External ladling |
Suitable for Aluminum? | No | Yes |
Melting Point Tolerance | Up to ~650°C | Can handle > 700°C |
Risk of Corrosion | High with aluminum | Low (no immersion of injection parts) |
サイクルタイム | 速い | Slightly slower |
ホットチャンバー・ダイカスト部品のシステム
The Hot Chamber Die Casting process is based on a group of well-engineered components that complement each other to produce accurate and repeatable castings. All the parts are very vital when it comes to efficiency, speed, and accuracy. Being aware of these elements contributes to the production, preventive, and quality controls.
The main constituents of a Hot Chamber Die Casting machine are as shown below:
1.もう一つの炉(金属鍋)
In the core of the system, there is a furnace, or the so-called metal pot, where the molten metal, which will be used in casting, is situated. In hot chamber die casting, an equivalent furnace is incorporated into the machine and maintains the metal at a sufficiently high temperature to use it immediately. As opposed to cold chamber systems, the process of immersion of other components in this molten bath separates it.
2.グースネック
Gooseneck constitutes a bent metal pipe connecting the furnace with the injection chamber. It is crucial in redirecting hot metal from the pot to the mould. The gooseneck will be composed of strong, heatproof materials because it is constantly in contact with molten metal. The design further assists in sustaining the pressure and makes the metal buttery in injection.
3.プランジャー/インジェクションシリンダー
The plunger mechanism or injection cylinder does the task of forcing molten metal into the die cavity. It operates with the gooseneck. When the plunger is pushed down, the molten metal becomes pressurised, causing the melt to force its way through the gooseneck into the mould. This should be done in a fast and forceful manner so that the die cavity will be filled fully.
4.金型組立
The die or mould is manufactured as two sections, the cover die (which is stationary) and the ejector die (movable). To get the final product, these well-machined halves will make up the cavity. The mould is frequently water cooled and contains vents and gates, and runners to maintain a desirable flow and cooling effect. To eliminate the solidified part, there are pins at the ejector side following casting.
5.クランプユニット
The clamping unit ensures that the die halves are well bonded together during the injection of molten metal. It has to resist the casting pressure that arises when casting. When the metal cooled and solidified, the clamping unit opens the mould, and the finished part comes out of it. The clamping should also be strong in order to avoid metal leakages and to maintain the quality of parts.
6.エジェクターシステム
Once the part solidifies, the ejector system is used. A part is ejected out of a mould cavity by ejector pins, which are usually found in the moving half of the die. This system has to be well coordinated such that the final product is not affected and the mould is not damaged.
7.冷却システム
Cooling is vital in order to control the cycle times and avoid defects. The circulating cooling system makes use of water or oil channels in the die in such a manner that the circulating fluid cools the metal in a short period as well as in a fast and uniform manner. A faster cooling also prolongs the life of the mould, and enables the parts to be handled at an increased rate.
8.潤滑システム
Between cycles, die casting moulds are lubricated to avoid sticking and wear. Lubricants are sprayed on the die to help in releasing the parts as well as ensure a long life of the tools and stability of casting conditions. There is usually automated application to facilitate the even and timed application.
9.コントロールパネル
Hot chamber die casting systems are also available in the modern system and are fitted with a digital control panel enabling management of temperature, injection speed, cycle time, and clamping force, among others. Such systems enhance uniformity in the processes, reduce the level of human error and ease the setting of parameters to suit various part designs.
10.安全機能
Safety features have been incorporated in the machine because of the temperature and pressure when it is hot. They comprise shut-offs, shields, interlocks and temperature monitors to safeguard the operators as well as the equipment.
ホットチャンバー・ダイカストの利点
The Hot Chamber Die Casting process has many advantages, such that many manufacturers are always willing to engage in the process:
1.高速生産
The injection system forms part of the molten metal reservoir system, and so metal does not have to be ladled into the chamber. The combination of this system yields higher injection speeds and low cycle time- hot chambers systems are therefore suitable in homes mass production.
2.材料の経済性
Very little wastes are generated through this process. The leftover material can be used again most of the time, and thereby the total cost of the material reduces considerably. This aspect of sustainability is an increasing problem in contemporary production.
3.より良い表面仕上げ
Surface finishes of parts manufactured by the hot chamber casting are usually of good quality. In many cases, this saves on extra machining or finishing operations.
4.長い金型寿命
As the metals used in the process of Hot Chamber Die Casting have lower melting points, those metals are less aggressive on moulded materials. This causes increased diesel life and lower maintenance charges.
ホットチャンバー・ダイカストの欠点
One cannot argue with the fact that “Hot Chamber Die Casting” is not without limitations:
Material Limitations: It does not go well with the metals that have high melting temperatures, such as aluminium and copper. The internal components of the machine can be harmed by either corrosive or heating effects of these.
Equipment Wear: The equipment wear can be a factor, even though less severe than the cold chamber casting, whereby the apparatus is constantly exposed to melted metal.
Size Limitation: It can be applied to smaller and medium components since further expansion of the system can be inefficient and complicated.
ホットチャンバー・ダイカスト
This is a widely applied technique in all sorts of industries, particularly where precision and large-scale parts are required:
- 自動車: Pieces such as carburettor houses, fuel system units and transmission components.
- コンシューマー・エレクトロニクス Portable cases, multi-functional parts of devices and equipment.
- Hardware and Tools: Hardware material based on Zinc, hinges, handles, locks, etc.
- Medical devices: Miniature, highly precise and tough devices.
The hot chamber process is fast and consistent, which is a quality that is advantageous to these industries. With most of these products being models that need detailed designs, the dimensional stability that is given by the Hot Chamber Die Casting comes as a big plus.
コールドチャンバーダイカストとホットチャンバーダイカスト:その違いを知る
In the comparison between cold chamber die casting and hot chamber, there are various aspects which will need to be put into consideration, such as the compatibility of the materials, rates of production, cycle and the design of the equipment.
1.材料の使用
The type of metal is also one of the most significant differences between cold chamber die casting vs hot chamber. Hot chamber process only takes on metals which have low melting points, and cold chamber process takes on aluminium, brass and copper alloys which have high melting points.
2.インジェクションシステム
The injection mechanism in the hot chamber method is immersed in molten metal. Cold chamber casting, on the other hand, involves ladle feeding molten metal to the shot chamber by hand and injecting it into the die. This further action delays the process.
3.サイクルタイムと効率
Cycle time and efficiency denote the time it takes to turn over the sample or input of data in a cycle. There is also a big difference between cold chamber die casting vs hot chamber, with regards to cycle time. Hot chamber process is quick and hence suitable for large volume runs. Although cold chamber casting is slower, it can be eased with more aggressive metals and hotter temperatures.
4.コンポーネントのサイズと複雑さ
Sections or parts that are larger or need materials that are more permanent are usually cast using the cold chamber method. Comparatively, the hot chamber casting is suitable for smaller and complex parts where a cycle speed is vital.
When choosing a decision between hot chamber and cold chamber die casting, the manufacturer will have to look at the tradeoffs in the speed and material properties and wear on the equipment.
ホットチャンバー・ダイカストにおける設計上の考慮点
To design a part suitable for a hot chamber die casting part, the following issues need to be looked after: mould flow, parting lines, wall thickness, and ejector location. Since the molten metal is injected at high levels, the venting and cooling system plays an important role in preventing defects such as entrapment of air, shrinkage or incomplete fills.
The tolerances of the Hot Chamber Die Casting Process are usually smaller than those required by all the other casting processes, hence the reason why it is always used in manufacturing parts that need precision and have little machining.
環境と経済効果
Sustainable manufacturing is drawing more and more attention from modern foundries. Hot Chamber Die Casting is ideal in achieving this objective in that it shows a low scrap level and energy savings. The total carbon footprint of a part is much less than in other methods to produce metal parts because the metal being processed is recycled (no new metal is extracted), and cycle times are short.
The process is more economical when it involves a large output. Its cost of setting up the first die and machine may be high, but as the unit production scale increases, the costs involved drop tremendously.
結論
Hot Chamber Die Casting has a very critical place in the industries that require speed, accuracy, and efficiency in their production. Knowing of its operation and in making the comparison of cold chamber die casting and hot chamber connections, an engineer will be able to make informed decisions on the choice of the most suitable process in line with the needs of their product.
Whether to use one or the other, the metal nature, the needed production volume, and the final usage should be taken into consideration. Hot chamber casting is unrivalled in efficiency and quality with respect to making small to medium components of low-melting-point metals.
All in all, despite the existence of the two methods of casting, Hot Chamber Die Casting will always be the first solution to the problem of manufacturing quality components in time and dependably. With the manufacturing process becoming more efficient and sustainable, the need for such optimised and sustainable processes, such as the hot chamber casting, will only increase, which makes this method more applicable than ever before.
よくある質問
1.コールドチャンバーダイキャストとホットチャンバーメインキャストの仕組みは?
The injection system is the chief difference. The injection mechanism in hot chamber die casting is immersed in molten metal. The temperature is greater in the cold chamber, and the metal is ladled outside.
2.ホットチャンバーダイカストに最も適した金属は何ですか?
The metals that are commonly used are zinc and magnesium alloy since they have low melting temperatures, and they suit the immersed injection system in which they are used to make.
3.アルミニウムはホットチャンバーダイカストでは使用できません。
Aluminium is known to have a high melting point and is corrosive to the steel parts in the machine. The cold chamber method is used in its processing to prevent damage to its equipment.
4.ホットチャンバーダイカストの利点は何ですか?
It provides short cycle times, low labour costs, small tolerances, and high surface finishes of small and medium-sized parts.
5.ホットチャンバー・ダイカストは大型部品に適していますか?
Generally, no. It is minimized when the parts are small and detailed. Too large dimensions usually mean a need for cold chamber die casting because of the size and material restraint.