핫 챔버 다이캐스팅은 금속 부품을 매우 높은 정밀도와 우수한 표면 마감으로 생산하는 데 매우 널리 사용되는 매우 효과적인 제조 공정입니다. 특히 아연, 마그네슘 및 납이 포함된 일부 합금과 같이 녹는점이 낮은 금속을 주조하는 데 적합합니다. 용융 금속에 사출 시스템을 담그기 때문에 고속 사이클 타임과 대량 생산의 경제성을 실현할 수 있다는 점이 특징입니다.
콜드 챔버 다이캐스팅과 핫 챔버 다이캐스팅을 고려할 때 항상 비슷한 비교 대상이 등장합니다. 둘 다 압력 다이캐스팅의 변형이지만 설계, 응용 분야 및 사용되는 재료의 호환성 측면에서 많은 차이가 있습니다. 예를 들어 핫 챔버 다이캐스팅은 용광로가 기계로 대체된 고속 다이캐스팅입니다. 여기에는 저융점 금속의 한계가 있습니다. 반대로 콜드 챔버 유형의 기계는 뜨거운 금속이 장비와 직접 접촉하지 않기 때문에 알루미늄 및 황동과 같이 녹는점이 높은 액체에 더 적합합니다.
핫 챔버 다이캐스팅 공정은 재료 낭비를 최소화하고 인건비를 낮추며 공차가 큰 복잡한 형상을 제조할 수 있다는 특징이 있습니다. 자동차, 전자, 배관 및 소비재와 같은 산업에서 널리 사용됩니다. 하지만 콜드 챔버 다이캐스팅을 사용할지 핫 챔버를 사용할지 여부는 사용되는 재료의 유형과 부품 설계 측면에 따라 결정됩니다.
이 문서에서는 다음과 같은 중요한 세부 사항을 살펴봅니다. 핫 챔버 다이 캐스팅부품, 재료, 공정 설명, 제약 조건 및 현대 제조 산업에서 필수적인 공정인 이유에 대해 설명합니다.
핫 챔버 다이 캐스팅이란?
핫 챔버 다이캐스팅은 용융 금속을 고압으로 금형 캐비티에 주입하는 금속 주조 기술입니다. 이 방법의 독특한 부분은 사출 메커니즘이 배치되는 곳입니다: 용융 금속에 직접 주입됩니다. 특히 아연, 마그네슘 및 일부 납 합금과 같이 녹는점이 낮은 금속의 경우 이 방식을 사용하면 사이클 시간과 생산 효율이 높습니다.
핫 챔버. 이 이름은 사출 메커니즘(플런저와 구즈넥)이 용융 금속 영역과 지속적으로 접촉(충전)하기 때문에 시스템의 핫 챔버를 설명합니다. 플런저가 하강하면서 구즈넥을 통해 용융 금속을 압축하여 금형 캐비티로 주입합니다. 금속이 굳으면 금형이 열리고 부품이 배출되며, 이 과정은 무수히 반복됩니다.
핫 챔버 다이 캐스팅 공정
핫 챔버 다이캐스팅 공정은 금속 부품 제조에 사용되는 고정밀 고속 제조 기술로, 공구의 정확도가 매우 중요하고 표면 마감이 뛰어난 공정입니다. 아연, 마그네슘, 납 등이 저융점 합금에 가장 적합하며, 저융점 합금의 예로는 아연, 마그네슘, 납 등이 있습니다. 주요 특징은 사이클 시간이 짧고 재료 효율성이 뛰어나다는 점입니다.
이 공정은 저렴한 개당 가격으로 복잡한 끝단을 쉽게 만들 수 있기 때문에 주로 자동차, 전자, 가전 및 하드웨어 산업에서 다양한 제품을 제조하는 데 광범위하게 사용됩니다. 핫 챔버 다이캐스팅 공정은 다음과 같이 단계별로 나열되어 있습니다:
핫 챔버 다이캐스팅 공정 - 단계별 개요
1. 금속이 녹았습니다.
주조는 다이캐스팅 기계의 통합된 용광로에서 금속(보통 아연 또는 마그네슘)을 녹여 성형하는 것으로 시작됩니다. 용융된 금속은 주조기에 직접 연결된 금속 포트 내에서 일정한 온도로 유지됩니다. 이러한 끊임없는 열 공급을 통해 주조 공정이 연속적으로 이루어집니다.
2. 주입 시스템 충전 과정
핫 챔버 시스템에는 구즈넥이라고 하는 부품의 일부가 잠긴 용융 금속의 일부가 있습니다. 사출 실린더 내부에서 작동하는 플런저는 용융 금속이 사출 입구 구멍으로 구즈넥으로 분출될 수 있는 위치까지 뒤로 당겨집니다. 다음 단계는 이 금속을 금형 캐비티에 주입하는 것입니다.
3. 용융 금속 주입
구즈넥이 채워지면 플런저가 유압 또는 공압에 의해 앞으로 밀려나면서 용융 금속이 구즈넥 채널을 통해 금형 캐비티(다이라고도 함)로 강제로 들어가게 됩니다. 이 작업은 금속이 굳기 시작하기 전에 캐비티가 완전히 채워지도록 높은 속도와 압력으로 이루어집니다.
4. 금형에서 주조 및 응고
금형의 뜨거운 금속은 금형의 비교적 차가운 강철에 의해 빠르게 냉각됩니다. 응고에는 부품의 크기와 복잡성에 따라 몇 초가 걸립니다. 이 단계에서 금형 냉각 채널은 열을 제거하여 사이클 속도가 저하되지 않고 수축이나 다공성과 같은 결함이 발생하지 않도록 도와줍니다.
5. 금형 꺼내기 및 열기
금속이 굳으면 금형 반쪽이 열립니다. 이젝터 시스템은 금형의 가동 가능한 절반에 배치되며, 이젝터 핀을 사용하여 힘을 받아 작동하여 완성된 주물을 캐비티 밖으로 밀어냅니다. 이젝터 핀은 이젝션 중에 부품이 손상되지 않고 나올 수 있도록 보장합니다.
6. 보조 작업 및 트리밍
작품이 배출된 후에는 플래시, 러너 또는 스프루스라는 추가 재료가 포함될 수 있습니다. 이러한 재료는 수작업으로 트리밍하거나 자동 트리밍합니다. 부품은 표면 마감, 기계 가공 또는 코팅과 같은 용도에 따라 추가 가공이 가능합니다.
7. 반복 주기
기계는 다시 사용할 수 있도록 깨끗하게 청소됩니다. 핫 챔버 다이캐스팅은 사이클 시간이 매우 짧아 부품의 복잡성과 크기에 따라 10~20초 만에 몇 개의 완성품을 만들 수 있는 것이 특징입니다.
주기 시간 및 효율성
핫 챔버 공정의 가장 큰 장점은 속도입니다. 핫 챔버 기계. 금속을 챔버에 넣어야 하는 콜드 챔버 다이캐스팅과 달리 금속을 용광로에서 꺼내는 방식입니다. 따라서 사이클 단계가 절약되고 생산 효율성이 향상됩니다.
이 프로세스의 장점
- 사이클 시간 단축 및 생산성 향상
- 실제 고차원적 성능과 반복성
- 표면 마감이 개선되어 많은 경우 후속 처리가 필요하지 않습니다.
- 재료 사용의 경제성 및 낭비 최소화
- 자동화에 친화적이며 합리적인 가격으로 대규모 생산이 가능합니다.
핫 챔버 다이 캐스팅 재료
핫 챔버 다이캐스팅 공정은 녹는점이 낮거나 중간 정도인 금속 및 합금에 적합합니다. 사용되는 재료는 주조 공정 중에 용융 금속으로 지속적으로 젖기 때문에 강철 부품(예: 구즈넥 및 플런저 시스템)을 부식시킬 수 없어야 합니다.
핫 챔버 다이캐스팅에 가장 자주 사용되는 재료와 그 특성 및 일반적인 적용 분야는 다음과 같습니다:
1. 아연 합금
다이캐스팅 공정(핫 챔버)에 가장 일반적으로 사용되는 재료는 아연입니다. 주조성, 강도 및 표면 마감이 우수하여 다양한 산업 분야에서 매우 인기가 있습니다.
주요 혜택:
- 매우 낮은 융점(~419 °C 또는 786 o F )
- 큰 중량 대비 강도 비율
- 화려한 흐름과 높은 치수의 정확도
- 우수한 내식성
- 낮은 용융 온도, 긴 금형 수명
아연의 일반적인 합금에는 다음이 포함됩니다:
- 자막 2, 3, 5, 7(자막 3이 가장 인기 있음)
- ZA 합금(아연-알루미늄)을 사용할 수 있지만, 금속 함량이 높은 알루미늄이 저온실에 더 적합할 수 있습니다.
애플리케이션:
- 자동차 부품
- 전기 부품
- 구조 및 고정
- 치아 정확도 기어 및 케이스
2. 마그네슘 합금
마그네슘은 가장 가벼운 구조용 금속으로 무게 대비 강도가 우수합니다. 핫 챔버 다이캐스팅에 마그네슘이 사용되는 이유는 여기에 사용되는 많은 부품이 최소한의 질량과 함께 강도가 필요하기 때문입니다.
주요 혜택:
- 경량(알루미늄보다 약 33% 가벼움)
- 그들은 잘 잠기고 뻣뻣하고 강도와 강성이 좋습니다.
- 뛰어난 EMI/RFI 차폐(전자제품에 적합)
- 환경 친화적이고 재활용 가능
일반적인 합금:
- 다이캐스팅에 사용되는 가장 일반적인 마그네슘 합금은 AZ91D입니다.
애플리케이션:
- 노트북과 스마트폰의 케이스
- 자동차 대시보드의 프레임
- 항공우주 부품
- 전동 공구
참고: 마그네슘은 저온 챔버 기계에서도 주조할 수 있지만, 주조되는 마그네슘이 작은 경우에는 고온 챔버 기계를 사용하는 것이 바람직합니다. 사이클 시간이 더 짧기 때문입니다.
3. 납 및 주석 합금
납과 주석 합금은 핫 챔버 다이캐스팅에서 건강 및 환경 제한으로 인해 대부분 제거되었지만 과거에는 특수 용도로 사용되었습니다.
주요 혜택:
- 낮은 융점(~327 o C(납) 및 ~232 °C(주석))
- 고밀도(밸런스 웨이트 또는 방사선 차폐와 같은 용도에 가장 적합)
- 뛰어난 치수 안정성
애플리케이션:
- 앤티크 스타일의 피팅
- 정밀 기기
- 탄약 구성 요소
- 장식 아이템
경고: 납의 독성 때문에 오늘날 납 기반 합금은 많은 산업과 국가에서 사용이 엄격하게 제한되고 있습니다.
4. 카드뮴 기반 합금(그렇지 않음)
독성 및 규제상의 이유로 드물게 적용되었지만 이전에는 우수한 주조 서비스 및 내마모성 때문에 선택되었습니다.
고온 합금을 사용하지 않는 이유입니다.
핫 챔버 다이 캐스팅의 특징적인 한계는 다음과 같습니다:
- 알루미늄
- 황동
- 구리
- Steel
이러한 유형의 금속은 플런저 및 구즈넥 등과 같이 핫 챔버 기계의 수중 부품에 고온 및 반응성을 가지므로 핫 챔버 기계가 손상되거나 부식될 수 있습니다. 오히려 용융 금속과 사출 메커니즘을 분리하는 콜드 챔버 다이캐스팅에 사용됩니다.
요약 표: 핫 챔버 다이캐스팅에 적합한 재료
재료 | 녹는점 | 장점 | 일반적인 사용 |
아연 합금 | ~419°C | 뛰어난 흐름, 표면 마감, 내구성 | 자동차, 전자, 하드웨어 |
마그네슘 합금 | ~650°C | 가볍고 튼튼하며 재활용 가능 | 항공우주, 전자, 자동차 인테리어 |
납 합금 | ~327°C | 고밀도, 간편한 캐스팅 | 방사선 차폐, 탄약 |
주석 합금 | ~232°C | 우수한 디테일 캐스팅, 비부식성 | 악기, 앤티크 디자인 |
알루미늄 합금이 핫 챔버 다이캐스팅에 적용되지 않는 이유는 무엇입니까?
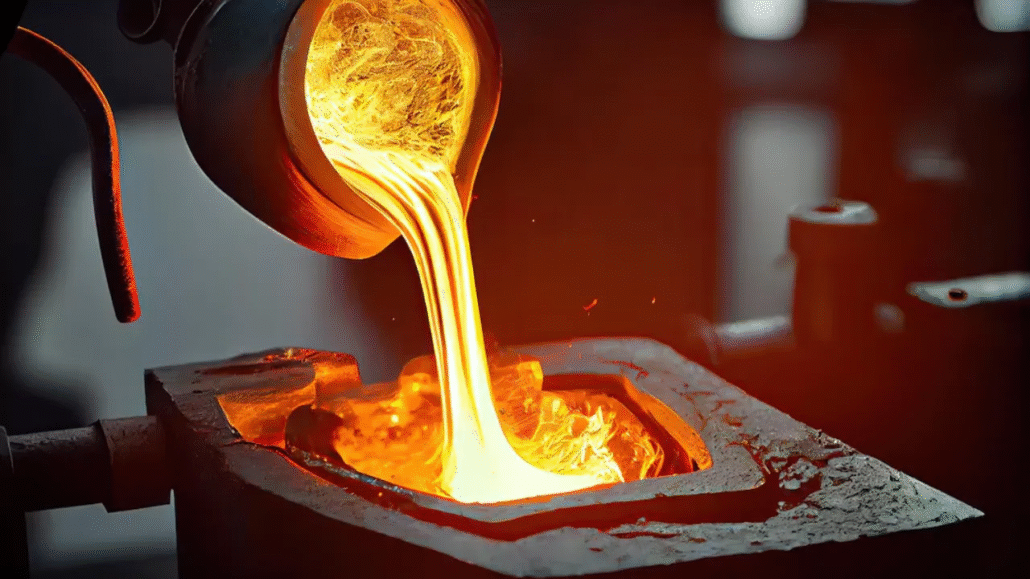
알루미늄 합금은 다이캐스팅 산업에서 매우 다양한 용도로 사용되지만 강도, 경량 특성 및 내식성 때문에 핫 챔버 다이캐스팅에서는 핫캐스팅이 불가능합니다. 대신 일반적으로 저온 챔버 다이캐스팅 기법으로 처리합니다.
이를 설명하기 위해 "알루미늄 합금이 핫 챔버 다이캐스팅에 사용되지 않는" 기술적 및 재료적 이유는 무엇입니까?
1. 큰 용융 온도
알루미늄이 핫챔버 공정과 호환되지 않는 가장 큰 이유는 녹는점이 높기 때문입니다. 대부분의 알루미늄 합금은 약 660℃(1220℉) 이상에서 녹습니다.
구즈넥과 플런저 및 기타 사출 부품은 핫 챔버 기계에서 항상 용융 금속에 잠겨 있습니다. 아연(419°C), 마그네슘(~650°C)과 같이 상대적으로 녹는점이 낮은 금속의 경우 효과적입니다. 그러나 이러한 부품은 알루미늄의 높은 온도에서 빠르게 열화되거나 파괴되어 장비의 고장과 수리 비용이 발생할 수 있습니다.
- 콜드 챔버 호환 SAC 슈트
- 너무 뜨거워서 말할 수 없는 핫챔버
2. 강철 부품에 대한 공격
알루미늄은 화학적으로 반응성이 강하고 특히 고온에서 철 금속을 부식시키는 경향이 있습니다. 구즈넥과 노즐과 같은 품목이 용융 풀에 있는 핫 챔버 시스템에서 알루미늄은 부식될 뿐만 아니라 강철 부품을 부식시켜 기계의 수명을 크게 단축시킬 수 있습니다.
이러한 반응은 장비의 수명을 단축시킬 뿐만 아니라 용융 금속을 오염시키고 최종 제품의 주조 불량 및 불완전성을 유발합니다.
3. 장비 호환성 문제
핫 챔버 기계는 작고 빠른 기계이지만 저융점 금속의 빠른 반복 주조를 수행하는 데 적합합니다. 내장된 퍼니스는 사출 시스템과 밀접하게 연결되어 있습니다. 알루미늄과 같이 녹는점이 높은 합금을 사용하려면 이 용광로가 필요합니다:
- 강화된 구성 요소
- 고온에 강한 합금은 특수 합금으로 만들어집니다.
- 더 복잡한 단열 시스템
이렇게 되면 핫 챔버 다이캐스팅의 단순성과 속도 이점이 무의미해집니다. 이것이 바로 조립업체가 용융 알루미늄을 외부에 붓고 사출 시스템도 물에 잠기지 않는 콜드 챔버 기계를 사용하는 이유입니다.
4. 산화 및 드로스 위험
고온에서 알루미늄은 공기가 있으면 쉽게 산화되기 쉽습니다. 이러한 산화로 인해 금속이 지속적으로 노출되는 고온 챔버 배열에서 드로스(알루미늄 산화물)가 형성될 수 있습니다:
- 금속을 오염시킵니다.
- 표면 결함의 원인은 다음과 같습니다.
- 그리고 완제품의 기계적 결함을 초래합니다.
콜드 챔버 다이캐스팅은 용융 알루미늄이 노출되는 시간을 줄여주기 때문에 이러한 위험을 최소화할 수 있습니다.
5. 안전 문제
핫 챔버 기계에서 알루미늄을 가공하면 화상 부상, 누출 및 기계 고장의 위험이 매우 높습니다. 더 높은 온도에서 작업할 때 발생하는 열 스트레스는 더 큰 위협에 노출됩니다:
- 용융 금속 누출이 있습니다.
- 증기 분출 반응
- 압력 구성 요소 고장
저온 챔버 시스템을 사용하면 이러한 고온에서 향상된 격리 및 안전 규제가 가능합니다.
알루미늄의 핫 챔버와 콜드 챔버 비교
기능 | 핫 챔버 다이 캐스팅 | 콜드 챔버 다이 캐스팅 |
주입 메커니즘 | 서브머지드(구즈넥 시스템) | 외부 래들링 |
알루미늄에 적합합니까? | 아니요 | 예 |
융점 허용 오차 | 최대 ~650°C | 700°C 이상 처리 가능 |
부식 위험 | 알루미늄으로 높이 | 낮음(사출 부품의 침수 없음) |
주기 시간 | 빠른 | 약간 느림 |
핫 챔버 다이캐스팅 부품 시스템
핫 챔버 다이 캐스팅 공정은 정확하고 반복 가능한 주물을 생산하기 위해 서로를 보완하는 잘 설계된 구성 요소 그룹을 기반으로 합니다. 모든 부품은 효율성, 속도, 정확성 측면에서 매우 중요합니다. 이러한 요소를 인식하는 것은 생산, 예방 및 품질 관리에 기여합니다.
핫 챔버 다이캐스팅 기계의 주요 구성 요소는 아래와 같습니다:
1. 용광로 하나 더(금속 냄비)
시스템의 핵심에는 주조에 사용될 용융 금속이 들어 있는 용광로 또는 소위 금속 냄비가 있습니다. 핫 챔버 다이캐스팅에서는 이와 동등한 용광로가 기계에 통합되어 금속을 즉시 사용할 수 있을 만큼 충분히 높은 온도로 유지합니다. 저온 챔버 시스템과는 달리, 이 용탕에 다른 부품을 담그는 과정에서 부품이 분리됩니다.
2. 구즈넥
구즈넥은 용광로와 사출 챔버를 연결하는 구부러진 금속 파이프로 구성됩니다. 구즈넥은 뜨거운 금속을 용기에서 금형으로 방향을 전환하는 데 매우 중요합니다. 구즈넥은 용융 금속과 지속적으로 접촉하기 때문에 튼튼하고 내열성이 강한 소재로 구성됩니다. 이 디자인은 압력을 유지하는 데 도움이 되고 사출 시 금속을 버터처럼 부드럽게 만듭니다.
3. 플런저/사출 실린더
플런저 메커니즘 또는 사출 실린더는 용융 금속을 다이 캐비티에 강제로 주입하는 작업을 수행합니다. 구즈넥과 함께 작동합니다. 플런저를 아래로 누르면 용융 금속에 압력이 가해져 용융물이 구즈넥을 통해 금형 내부로 강제로 들어가게 됩니다. 이 작업은 금형 캐비티가 완전히 채워질 수 있도록 빠르고 강력한 방식으로 수행해야 합니다.
4. 금형/금형 조립
다이 또는 금형은 커버 다이(고정식)와 이젝터 다이(이동식)의 두 부분으로 제조됩니다. 최종 제품을 얻기 위해 이 잘 가공된 반쪽이 캐비티를 구성합니다. 금형은 주로 수냉식이며 바람직한 흐름과 냉각 효과를 유지하기 위해 통풍구와 게이트, 러너가 포함되어 있습니다. 주조 후 이젝터 쪽에는 응고된 부분을 제거하기 위해 핀이 있습니다.
5. 클램핑 유닛
클램핑 유닛은 용융 금속을 주입하는 동안 다이 반쪽이 서로 잘 결합되도록 합니다. 주조 시 발생하는 주조 압력에 견딜 수 있어야 합니다. 금속이 냉각되고 응고되면 클램핑 유닛이 금형을 열고 완성된 부품이 금형 밖으로 나옵니다. 금속 누출을 방지하고 부품의 품질을 유지하려면 클램핑도 튼튼해야 합니다.
6. 이젝터 시스템
부품이 고형화되면 이젝터 시스템이 사용됩니다. 부품은 일반적으로 금형의 움직이는 절반에 있는 이젝터 핀을 통해 금형 캐비티 밖으로 배출됩니다. 이 시스템은 최종 제품에 영향을 미치지 않고 금형이 손상되지 않도록 잘 조정되어야 합니다.
7. 냉각 시스템
사이클 시간을 제어하고 결함을 방지하려면 냉각이 필수적입니다. 순환 냉각 시스템은 금형에서 물 또는 오일 채널을 사용하여 순환 유체가 단시간에 빠르고 균일하게 금속을 냉각하는 방식으로 작동합니다. 냉각 속도가 빨라지면 금형의 수명이 연장되고 부품을 더 빠른 속도로 처리할 수 있습니다.
8. 윤활 시스템
사이클 사이에 다이 캐스팅 금형에 윤활유를 발라 달라붙거나 마모되는 것을 방지합니다. 윤활제는 금형에 분사되어 부품의 이형을 도울 뿐만 아니라 공구의 긴 수명과 주조 조건의 안정성을 보장합니다. 일반적으로 균일하고 정해진 시간에 도포할 수 있도록 자동화된 도포가 이루어집니다.
9. 제어판
핫 챔버 다이캐스팅 시스템은 최신 시스템에서도 사용할 수 있으며 온도, 사출 속도, 사이클 시간, 클램핑 력 등을 관리할 수 있는 디지털 제어 패널이 장착되어 있습니다. 이러한 시스템은 공정의 균일성을 높이고 인적 오류를 줄이며 다양한 부품 설계에 맞게 파라미터를 쉽게 설정할 수 있습니다.
10. 안전 기능
뜨거운 온도와 압력으로 인해 기계에 안전 기능이 통합되어 있습니다. 차단, 차폐, 인터록 및 온도 모니터로 구성되어 작업자와 장비를 안전하게 보호합니다.
핫 챔버 다이 캐스팅의 이점
핫 챔버 다이 캐스팅 공정에는 많은 장점이 있어 많은 제조업체가 항상 이 공정에 참여하고자 합니다:
1. 고속 생산
사출 시스템은 용융 금속 저장소 시스템의 일부를 형성하므로 금속을 챔버에 래들링할 필요가 없습니다. 이 시스템의 조합으로 사출 속도가 빨라지고 사이클 시간이 단축되므로 핫 챔버 시스템은 가정용 대량 생산에 적합합니다.
2. 재료의 경제성
이 과정에서 폐기물은 거의 발생하지 않습니다. 남은 재료는 대부분 다시 사용할 수 있으므로 재료의 총 비용이 상당히 절감됩니다. 이러한 지속 가능성 측면은 현대 생산에서 점점 더 큰 문제가 되고 있습니다.
3. 표면 마감 개선
핫 챔버 주조로 제조된 부품의 표면 마감은 일반적으로 품질이 우수합니다. 대부분의 경우 추가 가공 또는 마감 작업을 줄일 수 있습니다.
4. 긴 금형 수명
핫 챔버 다이캐스팅 공정에 사용되는 금속은 녹는점이 낮기 때문에 성형 재료에 덜 공격적입니다. 따라서 디젤 수명이 늘어나고 유지보수 비용이 절감됩니다.
핫 챔버 다이 캐스팅의 단점
"핫 챔버 다이 캐스팅"에 한계가 없다는 사실에는 이의를 제기할 수 없습니다:
재료 제한: 알루미늄, 구리 등 녹는 온도가 높은 금속과 잘 어울리지 않습니다. 기계의 내부 부품이 부식성 또는 가열 효과로 인해 손상될 수 있습니다.
장비 마모: 장비 마모: 장비가 용융 금속에 지속적으로 노출되는 저온 챔버 주조보다는 덜 심각하지만 장비 마모가 요인이 될 수 있습니다.
크기 제한: 시스템을 더 확장하는 것은 비효율적이고 복잡할 수 있으므로 중소형 구성 요소에 적용할 수 있습니다.
핫 챔버 다이 캐스팅 애플리케이션
이는 모든 종류의 산업, 특히 정밀하고 큰 규모의 부품이 필요한 곳에서 널리 적용되는 기술입니다:
- 자동차: 카뷰레터 하우스, 연료 시스템 장치 및 변속기 부품과 같은 부품.
- 소비자 가전: 휴대용 케이스, 기기 및 장비의 다기능 부품.
- 하드웨어 및 도구: 아연, 경첩, 손잡이, 잠금 장치 등의 하드웨어 소재를 기반으로 합니다.
- 의료 기기: 초소형, 고도로 정밀하고 견고한 장치.
핫 챔버 공정은 빠르고 일관성이 있어 이러한 산업에 유리한 품질입니다. 이러한 제품의 대부분은 세밀한 설계가 필요한 모델이기 때문에 핫 챔버 다이캐스팅이 제공하는 치수 안정성이 큰 장점으로 작용합니다.
콜드 챔버 다이 캐스팅과 핫 챔버: 차이점 파악하기
콜드 챔버 다이 캐스팅과 핫 챔버 다이 캐스팅을 비교할 때 재료의 호환성, 생산 속도, 사이클 및 장비의 설계와 같은 다양한 측면을 고려해야 합니다.
1. 재료 사용
금속의 종류도 콜드 챔버 다이캐스팅과 핫 챔버 다이캐스팅의 가장 중요한 차이점 중 하나입니다. 핫 챔버 공정은 녹는점이 낮은 금속만 주조하고, 콜드 챔버 공정은 녹는점이 높은 알루미늄, 황동 및 구리 합금만 주조합니다.
2. 주입 시스템
핫 챔버 방식의 사출 메커니즘은 용융 금속에 잠겨 있습니다. 반면 저온 챔버 주조는 용융 금속을 손으로 국자로 사출 챔버에 공급하고 금형에 주입하는 방식입니다. 이 추가 작업으로 인해 공정이 지연됩니다.
3. 주기 시간 및 효율성
사이클 시간과 효율성은 한 사이클에서 샘플을 넘기거나 데이터를 입력하는 데 걸리는 시간을 나타냅니다. 사이클 시간과 관련하여 콜드 챔버 다이 캐스팅과 핫 챔버 다이 캐스팅 사이에는 큰 차이가 있습니다. 핫 챔버는 공정이 빠르기 때문에 대량 생산에 적합합니다. 콜드 챔버 주조는 더 느리지만 더 공격적인 금속과 더 높은 온도로 완화할 수 있습니다.
4. 구성 요소의 크기와 복잡성
더 크거나 더 영구적인 재료가 필요한 부품이나 섹션은 일반적으로 콜드 챔버 방식을 사용하여 주조합니다. 이에 비해 핫 챔버 주조는 사이클 속도가 매우 중요한 작고 복잡한 부품에 적합합니다.
핫 챔버 다이 캐스팅과 콜드 챔버 다이 캐스팅 중 하나를 선택할 때 제조업체는 속도와 재료 특성, 장비 마모에 따른 장단점을 고려해야 합니다.
핫 챔버 다이 캐스팅의 설계 고려 사항
핫 챔버 다이캐스팅 부품에 적합한 부품을 설계하려면 금형 흐름, 파팅 라인, 벽 두께, 이젝터 위치 등 다음과 같은 문제를 고려해야 합니다. 용융 금속이 높은 수준에서 주입되기 때문에 환기 및 냉각 시스템은 공기 혼입, 수축 또는 불완전한 충전과 같은 결함을 방지하는 데 중요한 역할을 합니다.
핫 챔버 다이캐스팅 공정의 공차는 일반적으로 다른 모든 주조 공정에 필요한 공차보다 작기 때문에 정밀도가 필요하고 가공이 거의 없는 부품 제조에 항상 사용되는 이유입니다.
환경 및 경제적 효과
지속 가능한 제조는 현대 파운드리에서 점점 더 많은 관심을 받고 있습니다. 핫 챔버 다이캐스팅은 스크랩 수준이 낮고 에너지를 절약할 수 있다는 점에서 이러한 목표를 달성하는 데 이상적입니다. 가공되는 금속이 재활용되고(새 금속을 추출하지 않음) 사이클 시간이 짧기 때문에 부품의 총 탄소 발자국은 다른 금속 부품 생산 방법보다 훨씬 적습니다.
이 공정은 생산량이 많을 때 더 경제적입니다. 첫 번째 금형과 기계를 설치하는 데 드는 비용은 높을 수 있지만, 단위 생산 규모가 커지면 관련 비용이 엄청나게 떨어집니다.
결론
핫 챔버 다이캐스팅은 생산 속도, 정확성 및 효율성을 필요로 하는 산업에서 매우 중요한 위치를 차지하고 있습니다. 엔지니어는 콜드 챔버 다이캐스팅과 핫 챔버 다이캐스팅을 비교하여 작동 방식을 파악하면 제품의 요구 사항에 따라 가장 적합한 공정을 선택할 때 정보에 입각한 결정을 내릴 수 있습니다.
어느 쪽을 사용할지 여부는 금속의 특성, 필요한 생산량, 최종 사용처를 고려해야 합니다. 핫 챔버 주조 는 저융점 금속의 중소형 부품을 만드는 데 있어 효율성과 품질 면에서 타의 추종을 불허합니다.
대체로 두 가지 주조 방법이 존재하지만, 핫 챔버 다이캐스팅은 항상 고품질 부품을 적시에 안정적으로 제조하는 문제에 대한 첫 번째 해결책이 될 것입니다. 제조 공정이 더욱 효율적이고 지속 가능해짐에 따라 핫 챔버 주조와 같이 최적화되고 지속 가능한 공정에 대한 필요성은 더욱 커질 것이며, 이는 이 방법을 그 어느 때보다 더 많이 적용할 수 있게 만들 것입니다.
자주 묻는 질문
1. 콜드 챔버 다이캐스팅과 핫 챔버 메인 캐스팅은 어떻게 다릅니까?
사출 시스템이 가장 큰 차이점입니다. 핫 챔버 다이캐스팅의 사출 메커니즘은 용융 금속에 잠겨 있습니다. 콜드 챔버는 온도가 더 높고 금속이 외부로 흘러나옵니다.
2. 핫 챔버 다이캐스팅에 가장 적합한 금속은 무엇인가요?
일반적으로 사용되는 금속은 아연과 마그네슘 합금으로, 용융 온도가 낮고 사출에 사용되는 침지 사출 시스템에 적합하기 때문입니다.
3. 알루미늄은 핫 챔버 다이캐스팅에 적용되지 않는데, 그 이유는 무엇인가요?
알루미늄은 녹는점이 높고 기계의 강철 부품을 부식시키는 것으로 알려져 있습니다. 콜드 챔버 방식은 장비 손상을 방지하기 위해 가공에 사용됩니다.
4. 핫 챔버 다이 캐스팅의 장점은 무엇인가요?
짧은 사이클 시간, 낮은 인건비, 작은 공차, 중소형 부품의 높은 표면 조도를 제공합니다.
5. 핫 챔버 다이캐스팅은 대형 부품에 적합한가요?
일반적으로는 없습니다. 부품이 작고 세밀한 경우 최소화됩니다. 치수가 너무 크면 일반적으로 크기와 재료 제한으로 인해 콜드 챔버 다이 캐스팅이 필요합니다.