يُعد الصب بالقالب عالي الضغط (HPDC) أحد أكثر عمليات صب المعادن استخدامًا في التصنيع الحالي. يختار المصنعون عملية HPDC لأنها تتيح إنتاج أجزاء معدنية معقدة تحقق دقة عالية ومعدلات إنتاج سريعة ودقة أبعاد فائقة وتشطيبات نهائية سلسة. وتتيح عملية الصب بالضغط العالي للضغط العالي لصناعات السيارات والفضاء وإنتاج مكونات الإلكترونيات والسلع الاستهلاكية تصنيع أجزاء متينة خفيفة الوزن لتطبيقات مثل المحركات والمباني والعناصر الهيكلية والتركيبات الميكانيكية. تواجه عملية تصنيع القوالب المصبوبة بالقالب عالي الضغط العديد من المخاطر التي تخلق عيوبًا كبيرة تقلل من جودة المنتج مع تقصير العمر الافتراضي له وتؤثر على الأداء. تتشكل العيوب المختلفة من التصميم غير المناسب للقالب وتدفق المعدن المنصهر المضطرب والغازات المحتبسة ومعدلات التبريد غير المتسقة والإجهاد الحراري أثناء عملية الإنتاج. تواجه تقنية HPDC سبعة عيوب أساسية تشمل المسامية، والإغلاق على البارد، وعيوب الانكماش، وتكوين الوميض، والعيوب السطحية، والعيوب السطحية، وسوء التآكل، وتآكل القالب، واللحام. تتسبب هذه الأنواع من عيوب التصنيع في تدهور قوة المواد مع إنتاج أبعاد غير منتظمة وتأثيرات بصرية غير مرغوب فيها والتي يمكن أن تحرض على انهيار المكونات. يتصدى المصنعون لمشاكل الإنتاج من خلال تحسين معلمات المعالجة وتحسين طرق المعالجة إلى جانب أنظمة التحكم في درجة الحرارة وإجراءات الصب بمساعدة التفريغ. تُعد برامج المراقبة والمحاكاة في الوقت الفعلي من الأساليب المتقدمة لمراقبة الجودة مع زيادة الكفاءة والموثوقية في عملية الصب بالقالب.
تقدم هذه المقالة تحليلاً شاملاً لمشكلات التصنيع القياسية أثناء الضغط العالي صب القوالب التكنولوجيا مع شرح الأسباب الجذرية واستراتيجيات الحلول لتقليل هذه العيوب. لا يمكن للمصنعين تحسين جودة مكونات القوالب المصبوبة وطول عمرها، وبالطبع أداءها وتقليل الهدر وتكاليف الإنتاج في الوقت نفسه، إلا من خلال فهم هذه التحديات وتطبيق أفضل الممارسات. ستساعد الكفاءة في هذه العيوب التصنيعية مهندسي صب القوالب ومديري الإنتاج وأخصائيي مراقبة الجودة على تحسين عملياتهم للحصول على أفضل النتائج في مجال صب القوالب.
1. المسامية
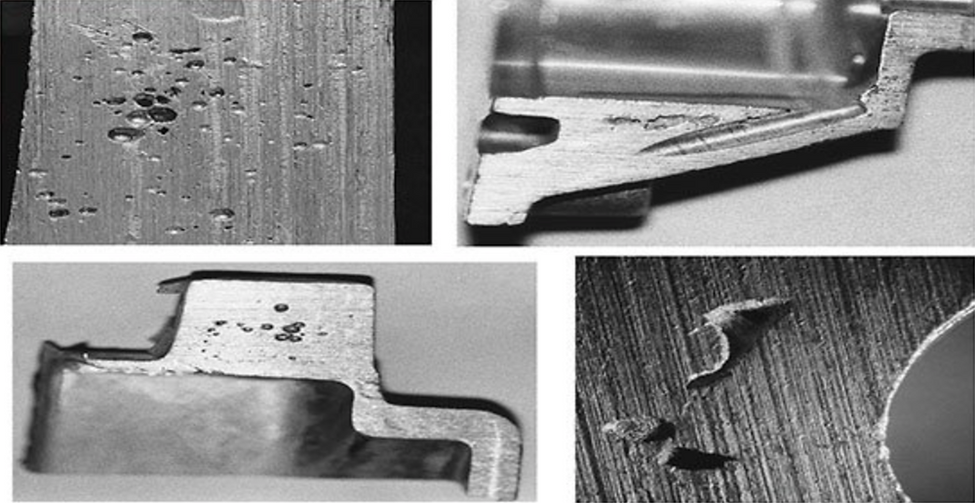
تُعرّف المسامية بأنها ثقوب صغيرة أو شوائب غازية موجودة داخل المصفوفة المعدنية، ونتيجة لذلك تؤثر على الخواص الميكانيكية وتقلل من القوة، بما في ذلك السماح بمرور الهواء والغازات عبر الهيكل، وتؤدي إلى عيوب سطحية مرئية في المنتجات المصبوبة بالقالب.
الأسباب:
- المحتويات الغازية الموجودة في المواد قبل الصب.
- الاضطراب المفرط في تدفق المعدن المنصهر.
- تهوية سيئة وتصميم القالب غير مناسب.
- التصلب السريع الذي يسبب مسامية الانكماش.
- تلوث المعدن المنصهر.
- الضغط غير الكافي الذي يسبب عدم وجود تدفق منتظم للمعدن.
الوقاية والحلول:
- تأكد من تحقيق التخلص المناسب من الغازات من خلال تصميم البوابات والتنفيس.
- إبطاء معدل الحقن لتعزيز نعومة المعدن الداخل إلى التجويف.
- يجب حل مشكلة احتباس الهواء عن طريق تقنية الصب بالقالب بمساعدة التفريغ.
- تأكد من إزالة الغاز من المعدن المنصهر بشكل كافٍ قبل حقنه.
- التحكم في معدل التبريد للتغلب على مشكلة التشققات وتكوين عيوب التصلب الأخرى.
- افحص أسطح القوالب ونظفها كثيرًا لتقليل فرص حدوث مسامية بسبب الملوثات.
2. الإغلاق البارد
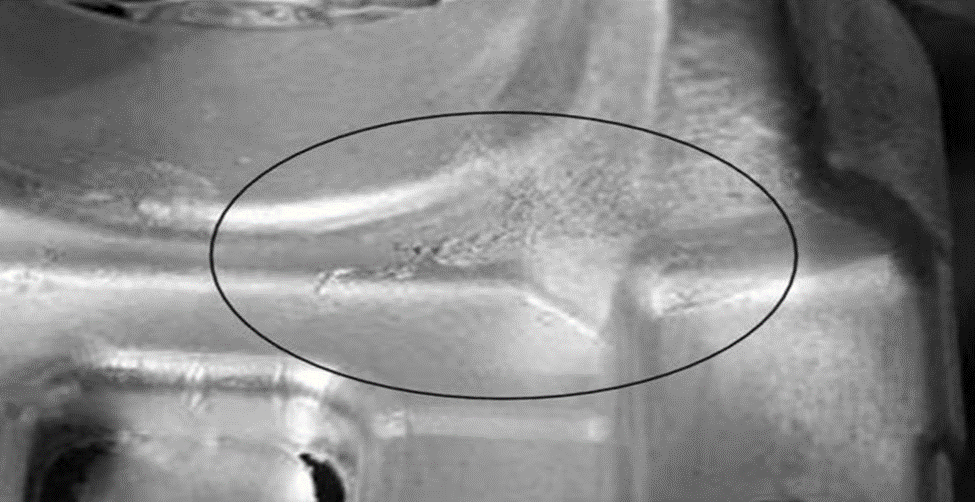
ينشأ الإغلاق البارد عندما لا يندمج تياران من المعدن المنصهر بشكل صحيح ويشكلان مناطق ترابط ضعيفة أو طبقات مرئية في الصب. لا يقلل هذا العيب من القوة الميكانيكية فحسب، بل يزيد أيضًا من خطر حدوث كسر، كما يؤثر سلبًا على متانة المكوّن ومظهره.
الأسباب:
- انخفاض درجة حرارة المعدن المنصهر.
- تتميز بسرعة الحقن البطيئة، مما يؤدي بشكل عام إلى التصلب المبكر.
- تصميم رديء للقالب مع عدم كفاية قنوات التدفق.
- يمكن أن يسبب الأكسدة المفرطة التي تشكل أغشية سطحية تمنع الاندماج السليم.
- تدفق معدني غير متناسق بسبب سوء تصميم نظام البوابات.
الوقاية والحلول:
- كما يجب الحفاظ على درجة حرارة صب المعدن المثلى لضمان السيولة المناسبة.
- قم بزيادة سرعة الحقن لإكمال التعبئة وجعلها قطعة واحدة.
- تخلص من حواجز التدفق غير الضرورية في تصميم القالب بحيث يمكن للمعدن أن يتحرك دون صعوبة.
- الكشف عن مشكلات التدفق وحلها قبل الإنتاج باستخدام أدوات التحليل الحراري.
- يجب تطبيق تقنيات التهوية المناسبة لتجنب احتباس الهواء الذي غالباً ما يضاعف من عيوب الإغلاق البارد.
3. عيوب الانكماش
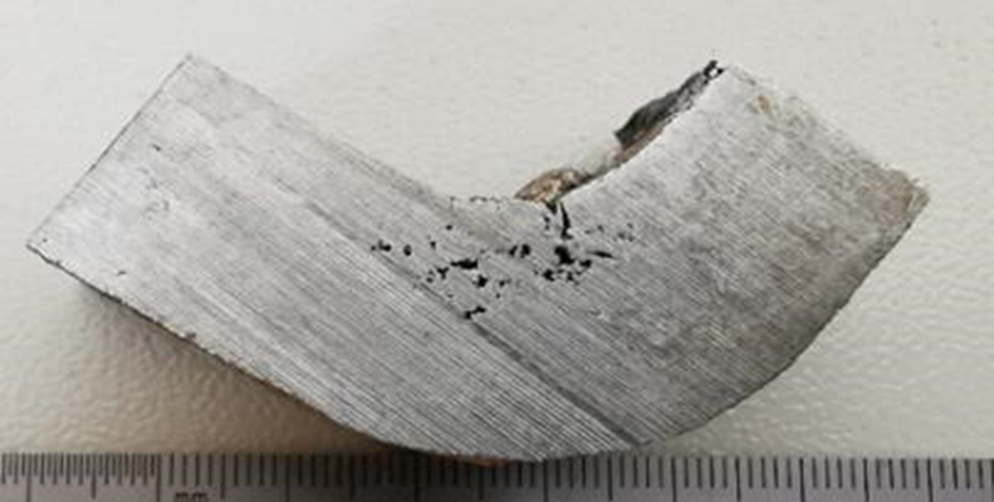
تحدث عيوب الانكماش بسبب انكماش المعدن أثناء التبريد مما يؤدي إلى حدوث فراغات أو تجاويف داخلية، مما يؤدي إلى تدهور السلامة الهيكلية للصب. ونتيجةً لذلك، تقلل هذه العيوب من القوة الميكانيكية للمنتج النهائي، وتتسبب في فشل محتمل تحت الضغط، وتؤدي إلى ضعف جودة السطح، مما يؤثر على كل من الأداء الوظيفي والجمالية للمنتجات النهائية.
الأسباب:
- عدم كفاية التغذية المعدنية أثناء التصلب
- معدلات التبريد غير متساوية بسبب التصميم غير المناسب للقالب
- انكماش معدني مرتفع بسبب تركيبة السبيكة
- تبريد سريع يسبب انكماشاً موضعياً
- عدم كفاية الضغط أثناء مرحلة التصلب
الوقاية والحلول:
- تعديل القالب لإعطاء تبريد موحد وتغذية مناسبة للمعدن المنصهر.
- استخدم سبائك ذات ميل أقل للانكماش، وذات خصائص تصلب أفضل.
- يتم استخدامه لتحسين إعدادات الضغط أثناء التصلب لملء فراغات الانكماش وتقليلها.
- استخدم طرق التبريد المتحكم بها لتحقيق التوازن في معدلات التصلب وخفض الإجهاد الحراري.
- تنفيذ أدوات المراقبة والمحاكاة في الوقت الحقيقي للتنبؤ بعيوب الانكماش ومنع حدوثها.
4. تشكيل الوميض

يُشار إلى الطبقات المعدنية الرقيقة الزائدة المتكونة عند خط الفراق أو فجوة القالب بسبب تسرب المعدن عالي الضغط باسم الوميض. على الرغم من أنه يمكن إزالة الوميض بعد الصب، إلا أن الوميض الزائد يؤدي إلى زيادة هدر المواد، وتآكل الأدوات، وتكاليف الإنتاج المرتبطة بها، وبالتالي يقلل من الكفاءة الكلية لعملية الصب بالقالب.
الأسباب:
- يتسبب ضغط الحقن الزائد في دفع المعدن المنصهر إلى داخل فجوات القالب.
- القالب البالي أو بسبب قفل القالب بشكل غير صحيح للسماح بالتسريبات.
- حيث لا توجد قوة تشبيك كافية، مما يتسبب في انفصال القالب أثناء الحقن.
- ستقع بشكل سيء مع وجود فجوات لتسرب المعدن للخارج.
- تحكم غير واضح في تدفق المعادن عن طريق تزييت القالب
الوقاية والحلول:
- يجب الحفاظ على قوة التشبيك المناسبة لتجنب انفصال القالب وتكوين الوميض.
- قم بفحص القوالب البالية واستبدالها بانتظام للحصول على ختم مناسب.
- تأكد من الإعدادات المثلى للضغط بحيث يتم ملء الحشوة وتعبئتها بأقل قدر من الوميض.
- لمنع الفجوات غير المقصودة والتسرب المعدني غير المقصود يجب تحسين إعادة تنظيم القالب.
- القيام بتقنيات تشحيم القوالب الدقيقة للتحكم في تدفق المعدن وتقليل تسرب المعدن الزائد.
5. فحص العيوب السطحية (البثور والتشققات والتجاعيد)

تتسبب مجموعة متنوعة من العيوب السطحية، والبثور، والشقوق، والتجاعيد، في تدهور المظهر البصري والقوة الميكانيكية للمسبوكات ويجب منعها وإزالتها. كما أنها تسبب عيوب اللحام التي تقلل من متانة المنتج، وتزيد من معدل الرفض، وتجعل المنتج ضعيفًا بعد معالجات ما بعد الصب مثل الطلاء أو الطلاء.
الأسباب:
- الهواء المحبوس في البلاستيك السائل أثناء الصب.
- أيضًا، هناك إجهاد حراري ومخالفات سطحية بسبب معدلات التبريد غير المنتظمة.
- ارتفاع درجة الحرارة أو سوء التحكم في درجة الحرارة أثناء التصلب.
- أو الشوائب أو الشوائب المعدنية التي قد تؤثر على سطح الصب
- تسبب سوء تشحيم القالب في تدفق المعدن غير المتكافئ وعدم انتظامه على السطح.
الوقاية والحلول:
- التفريغ المناسب للمعدن المنصهر لتجنب الغازات المحتبسة قبل الصب.
- التحكم في التصلب وتجنب الإجهاد الحراري باستخدام تقنيات التبريد المنتظم.
- يجب تحسين التحكم في درجة حرارة القالب لمنع ارتفاع درجة الحرارة والتبريد غير المتساوي.
- خلق رقابة صارمة على جودته تسمح له باكتشاف جميع الشوائب قبل الصب.
- تطبيق الطلاء ومواد التشحيم للقالب على أساس جودة السطح وتقليل العيوب.
6. الشوائب والتلوث
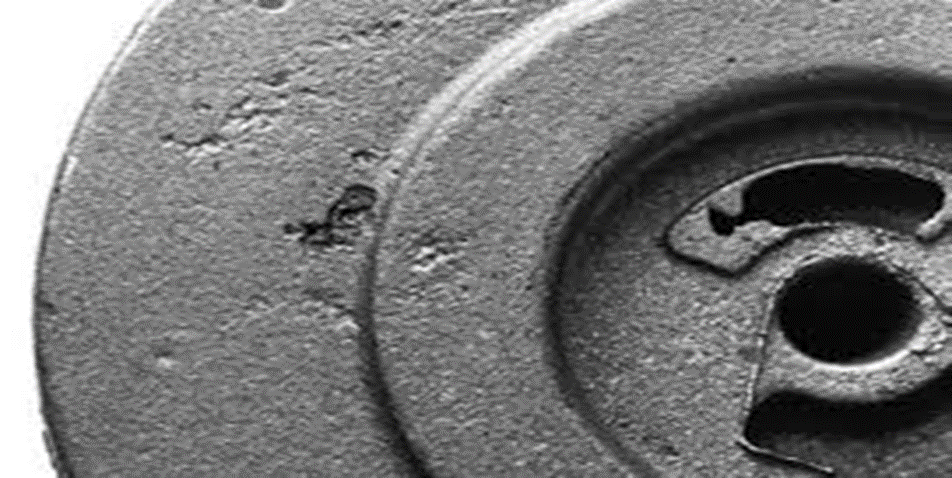
الجسيمات الغريبة غير المرغوب فيها، مثل الخبث أو أغشية الأكسيد أو الأوساخ أو الشوائب الأخرى التي تعلق في الصب النهائي، تخلق خصائص ميكانيكية ضعيفة وضعف السلامة الهيكلية وعيوب السطح وتسمى شوائب. يمكن أن يقلل وجود هذه الملوثات من أداء مكونات القوالب المصبوبة ومتانتها بحيث لا تكون مناسبة للتطبيقات عالية الدقة.
الأسباب:
- على سبيل المثال، تتكون المواد الخام الملوثة من شوائب غير مرغوب فيها.
- لا يمكن ترشيح الجسيمات الغريبة في المعدن المنصهر بشكل جيد نتيجة لذلك
- بسبب التعرض المطول للهواء أثناء صهر المعادن أو صبها
- تشمل ممارسات مناولة المعادن غير الفعالة التي تؤدي بدورها إلى زيادة تكوين الخبث
- يتضمن التزييت غير الكافي للقالب إدخال مادة غريبة إلى المعدن المنصهر.
الوقاية والحلول:
- يجب تكرير المواد الخام عالية الجودة بشكل صحيح وبدون ملوثات.
- إعداد أنظمة ترشيح فعالة لإزالة الخبث والأكاسيد والشوائب الأخرى من المعدن المنصهر قبل الحقن.
- الحفاظ على التحكم في مناولة المعدن المنصهر واستخدام التدريع بالغاز الخامل للحد من الأكسدة حيثما أمكن.
- تنظيف معدات الصب وصيانتها بانتظام لمنع التلوث من المواد المتبقية.
- استخدم التزييت المناسب للقالب لضمان عدم تراكم أي مواد غريبة في تجويف القالب.
7. التجاوزات وعدم اكتمال التعبئة
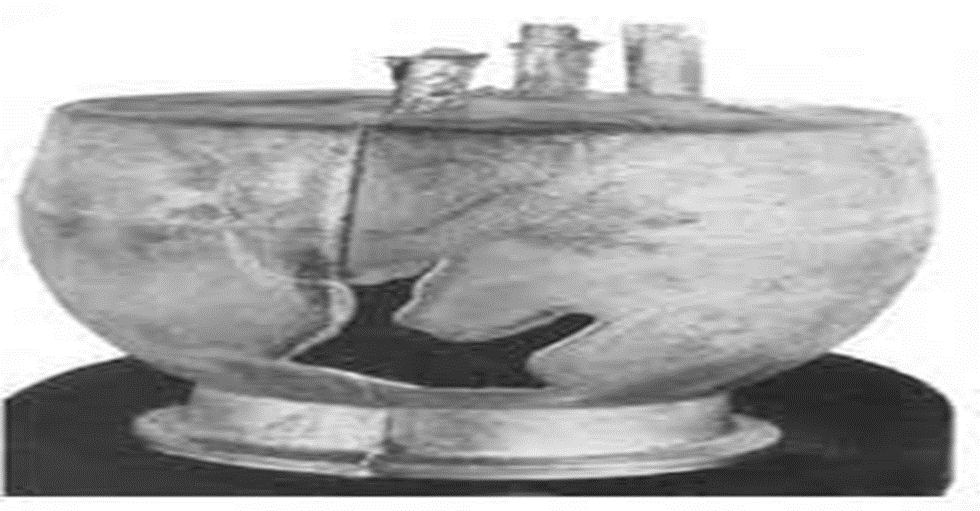
يحدث خطأ في التشغيل حيث يكون هناك ملء قصير لتجويف القالب، مما يتسبب في وجود أجزاء مفقودة وجدران رقيقة ونقاط ضعف في المكون النهائي. تأثيرات سلبية على السلامة الهيكلية والوظيفية للجزء وبهذه الطريقة غير مناسبة لتطبيقات الأداء.
الأسباب:
- عند انخفاض سرعة الحقن أو الضغط المنخفض، وعدم تغطية القالب بالكامل
- أسطح القوالب الباردة التي تمنع تدفق المعادن والتصلب المبكر
- يتسبب في عدم كفاية حجم المعدن المنصهر مما يؤدي إلى عدم كفاية ملء التجويف
- من سوء تصميم البوابات والعداء، مما يتسبب في توزيع غير متساوٍ للمعدن المنصهر
- ينتج عن الاضطراب المفرط جيوب من الهواء تسد التدفق المعدني
الوقاية والحلول:
- زيادة درجة حرارة المعدن لجعله قابلاً للتدفق وتجنب التصلب المبكر.
- وعلاوة على ذلك، يجب تحسين ملء التجويف من خلال ضبط ضغط الحقن وسرعته بشكل صحيح.
- الحفاظ على درجات حرارة العمل المناسبة للقوالب ومنعها من التبريد قبل الأوان.
- تحسين تصميم البوابات والعداءات لتعزيز التوزيع السلس والمتساوي للمعادن.
- قم بمحاكاة تدفق المعادن وإمكانية حدوث خطأ في التشغيل باستخدام برنامج محاكاة قبل الإنتاج.
8. تآكل القالب وتآكله
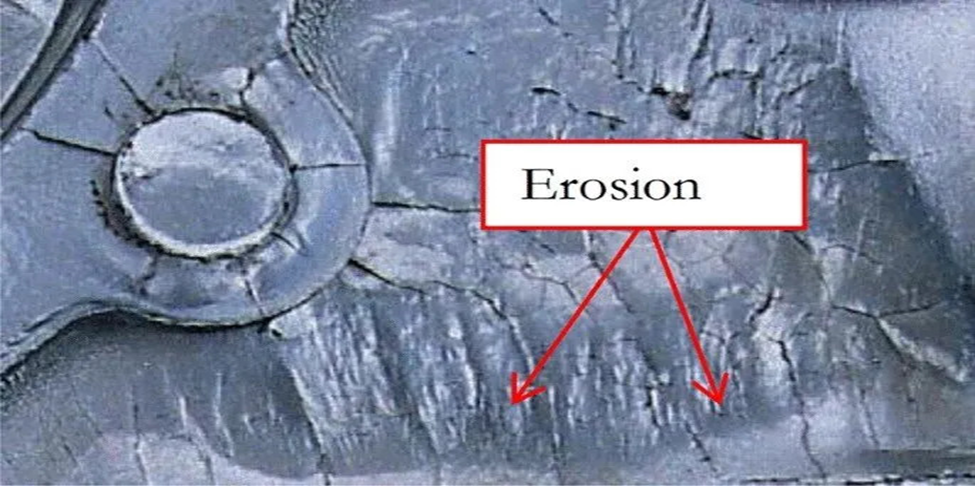
تآكل القوالب بالتآكل المنصهر هو تآكل أسطح القوالب بسبب تآكل المعدن عالي السرعة باستمرار لأسطح أجزاء القالب حتى يتم تحقيق الأبعاد المطلوبة، مما يؤدي إلى سوء تشطيب السطح وقصر عمر أداة القالب. في حالة حدوث هذا العيب، يكون استبدال القالب أمرًا شائعًا وبالتالي تزداد تكاليف الإنتاج بينما تتفاوت جودة الصب.
الأسباب:
- كما أنها تتعرض بشكل متكرر لمعدن مصهور بدرجة حرارة عالية مما يسبب تآكلًا تدريجيًا.
- مواد القوالب رديئة الجودة نسبياً مع مقاومة ضعيفة للإجهاد الحراري والميكانيكي على حد سواء
- يمكن أن يتسبب التدوير الحراري المفرط في حدوث تشقق للمادة بسبب الإرهاق.
- مما يؤدي إلى تدهور مادة القالب تحت الحقن العالي.
- تشحيم قليل؟ ينتج المزيد من الاحتكاك والمزيد من التآكل.
الوقاية والحلول:
- يتمثل أحدها في استخدام مواد قوالب عالية الجودة مقاومة للحرارة وأكثر متانة.
- يمكن استخدام الطلاءات الواقية للأسطح، مثل الطلاء بالنترة أو الطلاء الخزفي، لإطالة عمر القالب.
- يجب تنفيذ طرق التبريد المتحكم بها لتقليل الإجهاد الحراري والحث على التآكل المبكر.
- لتحقيق التوازن بين السرعة والضغط مع الحد الأدنى من الضغط على القالب.
- افحص القوالب بانتظام وقم بصيانتها للعثور على التآكل ومعالجته في أقرب وقت ممكن.
9. التكسير الساخن
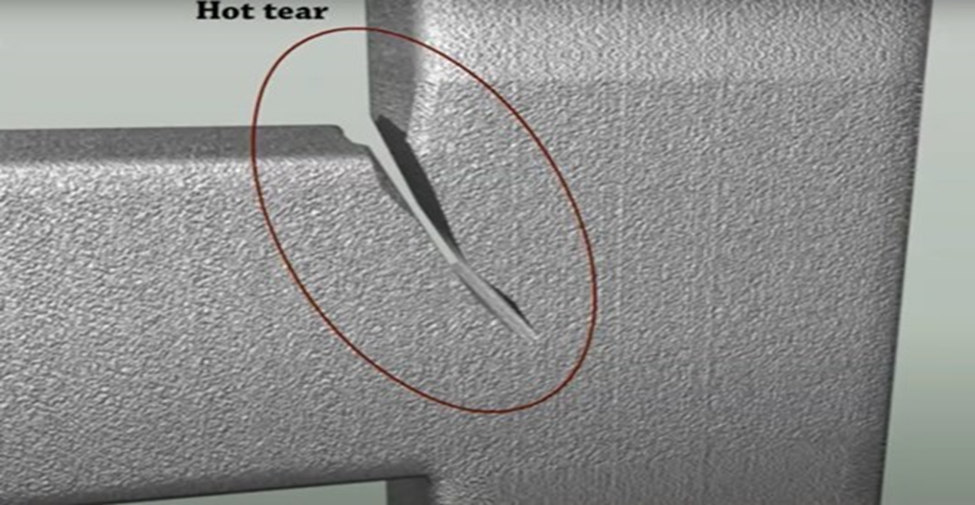
تُعرف التشققات التي تحدث أثناء الحالة شبه الصلبة للمعدن، بسبب الإجهاد الحراري العالي والانكماش المفرط باسم التشقق الساخن. تؤدي هذه التشققات إلى تدهور السلامة الميكانيكية للمسبوكة مما يزيد من فرصة فشل المسبوكة في المكان الذي توجد فيه التشققات تحت الضغط أو الحمل.
الأسباب:
- معدلات تبريد غير موثوق بها في القالب، مما يؤدي إلى وجود نقاط إجهاد في مناطق محددة
- لديها قابلية عالية للإجهاد الحراري والتشقق في تركيبة السبيكة.
- يسبب أيضًا إجهادًا متبقيًا مفرطًا متشكلًا أثناء التصلب السريع قيدًا على انكماش المعدن
- إذا كان تصميم القالب رديئًا، فستكون هناك اختلافات في درجات الحرارة عبر الصب.
- كان الضغط أثناء التصلب صغيرًا جدًا لمنع التشققات من الانتشار.
الوقاية والحلول:
- كما سيتضمن أيضًا تحسين معدلات التبريد لتحقيق التصلب المنتظم وتقليل الإجهاد الحراري.
- زيادة مقاومة التشقق للسبائك من خلال الاستخدام المناسب للسبائك ذات البنية الحبيبية الأفضل.
- استخدام تقنيات تخفيف الإجهاد بعد الصب، أي المعالجة الحرارية المضبوطة.
- تصميم قوالب ذات فرق أقل في درجات الحرارة.
- تأكد من الضغط المناسب أثناء تصلب المعدن حتى يتدفق ولا تحدث تشققات.
10. اللحام
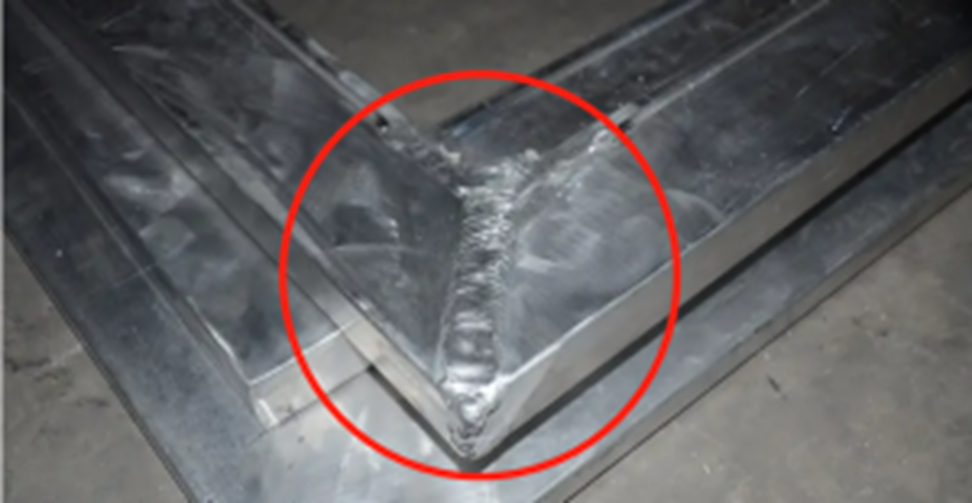
ويلتصق المعدن المنصهر بسطح القالب، وهو أمر يصعب إزالته مع الصب، مما يتسبب في عيوب السطح وتآكل القالب بالإضافة إلى طول فترة تعطل الإنتاج. كما يتسبب هذا العيب أيضًا في عدم دقة الأبعاد وسوء تشطيب السطح حيث ينتج عنه ضعف جودة المنتج النهائي بشكل عام.
الأسباب:
- زيادة حقيقة التصاق المعادن في السبيكة بسبب ارتفاع محتوى الألومنيوم فيها
- لارتفاع درجات حرارة القالب بشكل مفرط، بحيث يلتصق المعدن بسطح القالب
- حماية غير كافية ضد الالتصاق بسبب سوء تزييت القالب
- يتسبب التبريد غير الكافي في ترك المعدن المنصهر ملامسًا للقالب لفترة طويلة جدًا - الأسطح العلوية للقالب المتكلسة أو التالفة التي تعزز التصاق المعدن.
الوقاية والحلول:
- يتم دائمًا استخدام مواد تشحيم القوالب عالية الجودة لمنع التصاق المعادن.
- يسمح بالتحكم في درجة حرارة القالب في النطاق الأمثل إذا كان الالتصاق الساخن قويًا جدًا.
- تقليل التصاق المعدن باستخدام طلاء القالب المناسب، مثل طبقات السيراميك أو النيتريد.
- لتقليل زمن تلامس المعدن مع القالب، ولتحسين كفاءة نظام التبريد.
- افحص أسطح القوالب وصقلها بانتظام لتحقيق سطح أملس غير لاصق.
الخاتمة
الضغط العالي صب القوالب هي عملية تصنيع قوية تصنع أجزاء معدنية معقدة بدقة عالية وبأقصى قدر من الكفاءة. ومع ذلك، تنشأ أنواع مختلفة من العيوب باستخدام معلمات عملية غير مناسبة، ومشكلات المواد، و/أو عيوب تصميم القالب. يمكن للمصنعين اتخاذ تدابير وقائية، مثل القالب الأمثل للتحكم في العملية، والمواد المختارة بشكل صحيح، وما إلى ذلك، بعد فهم عيوب التصنيع المعتادة هذه.
يمكن للشركة تحسين جودة المنتج، وخفض تكاليف الإنتاج، وتحقيق كفاءة إنتاج أعلى في عمليات صب القوالب من خلال التركيز على التحسين المستمر للعمليات بالإضافة إلى استراتيجيات الوقاية من العيوب.
الأسئلة الشائعة (FAQs)
1. ما هي الأسباب الرئيسية للعيوب في الصب بالضغط العالي؟
تشمل الأسباب الرئيسية للعيوب في الصب بالقالب عالي الضغط التصميم غير المناسب للقالب وسوء تدفق المعدن والغاز المحبوس والإجهاد الحراري العالي والتبريد غير المتكافئ والمواد الخام الملوثة. يمكن تقليل هذه العيوب من خلال تحسين معلمات العملية ومن خلال استخدام تدابير مراقبة الجودة.
2. ما هو الدور الذي تلعبه المسامية فيما يتعلق بأداء مكونات القوالب المصبوبة؟
يؤدي وجود المسامية إلى إضعاف السلامة الهيكلية لمكونات القوالب المصبوبة، مما يقلل من القوة ويسبب تسرب الهواء في المكونات محكمة الضغط بالإضافة إلى عيوب التخدير. يمكن تقليل المسامية باستخدام التفريغ السليم للغازات وأنظمة البوابات المحسّنة والصب بمساعدة التفريغ.
3. كيف يمكن تجنب الإغلاق البارد في الصب بالقالب؟
يمكن أن تساعد درجة حرارة صب المعدن الصحيحة، وسرعات الحقن الأعلى، والتصميم الأمثل للقالب لتسهيل تدفق المعدن، وتطبيق أدوات التحليل الحراري لتحديد مشاكل التدفق المحتملة في منع الانغلاق البارد.
4. يعتبر تآكل القالب مصدر قلق مهم في الصب بالقالب عالي الضغط لأن؟
يؤدي التعريض المتكرر للمعدن المنصهر بدرجة حرارة عالية للقوالب إلى تآكل القوالب مما يقلل من عمر القوالب ويقلل من دقة الأجزاء المصبوبة. يمكن إطالة عمر القالب باستخدام مواد عالية الجودة للقالب واستخدام الطلاءات الواقية والتبريد المتحكم فيه.
5. ما الذي يجعل جودة المنتج المصبوب واتساقه أفضل؟
يتم إجراء رقابة صارمة على الجودة، وتحسين معلمات العملية، والتحكم في درجة حرارة القالب، واستخدام سبائك عالية الجودة، وفحص القالب والماكينات بشكل دوري من أجل التحسين المعتاد لجودة المنتج المصبوب.