Das Druckgussverfahren (HPDC) ist eines der am häufigsten eingesetzten Metallgussverfahren in der heutigen Fertigung. Die Hersteller entscheiden sich für das HPDC-Verfahren, weil es die Herstellung komplexer Metallteile ermöglicht, die sowohl hohe Präzision und schnelle Produktionsraten als auch hervorragende Maßgenauigkeit und glatte Oberflächen aufweisen. HPDC ermöglicht es der Automobil- und Luftfahrtindustrie sowie der Herstellung von Elektronikkomponenten und Konsumgütern, leichte und langlebige Teile für Anwendungen wie Motoren und Gehäuse, Strukturelemente und mechanische Baugruppen herzustellen. Der Herstellungsprozess des Druckgusses birgt zahlreiche Risiken, die zu erheblichen Mängeln führen, die die Produktqualität mindern und gleichzeitig die Lebensdauer verkürzen und die Leistung beeinträchtigen. Verschiedene Defekte entstehen durch unsachgemäße Formgestaltung, turbulente Strömung der Metallschmelze, eingeschlossene Gase, uneinheitliche Abkühlungsraten und thermische Belastung während des Produktionsprozesses. Bei der HPDC-Technologie treten sieben Hauptdefekte auf, darunter Porosität, Kaltverschlüsse, Schrumpfungsdefekte, Gratbildung, Oberflächendefekte, Fehlläufe, Gesenkerosion und Löten. Diese Arten von Herstellungsfehlern führen zu einer Verschlechterung der Materialfestigkeit, unregelmäßigen Abmessungen und unerwünschten visuellen Effekten, die zu einem Ausfall der Komponenten führen können. Die Hersteller bekämpfen die Produktionsprobleme durch die Optimierung der Verarbeitungsparameter und bessere Untergrabungsmethoden zusammen mit kontrollierten Temperatursystemen und vakuumunterstützten Gießverfahren. Echtzeit-Überwachung und Simulationssoftware sind fortschrittliche Methoden der Qualitätskontrolle, die die Effizienz und Zuverlässigkeit des Druckgussverfahrens erhöhen.
Dieser Artikel bietet eine umfassende Analyse der Standardherstellungsprobleme bei Hochdruck Druckgießen Technologie mit Erklärungen zu den Grundursachen und Lösungsstrategien zur Verringerung dieser Mängel. Nur wenn die Hersteller diese Herausforderungen verstehen und bewährte Verfahren anwenden, können sie die Qualität, Langlebigkeit und natürlich die Leistung ihrer Druckgussteile verbessern und gleichzeitig den Ausschuss und die Produktionskosten senken. Die Kenntnis dieser Herstellungsfehler hilft Druckgussingenieuren, Produktionsleitern und Qualitätssicherungsspezialisten, ihre Prozesse zu optimieren, um die besten Druckgußergebnisse zu erzielen.
1. Porosität
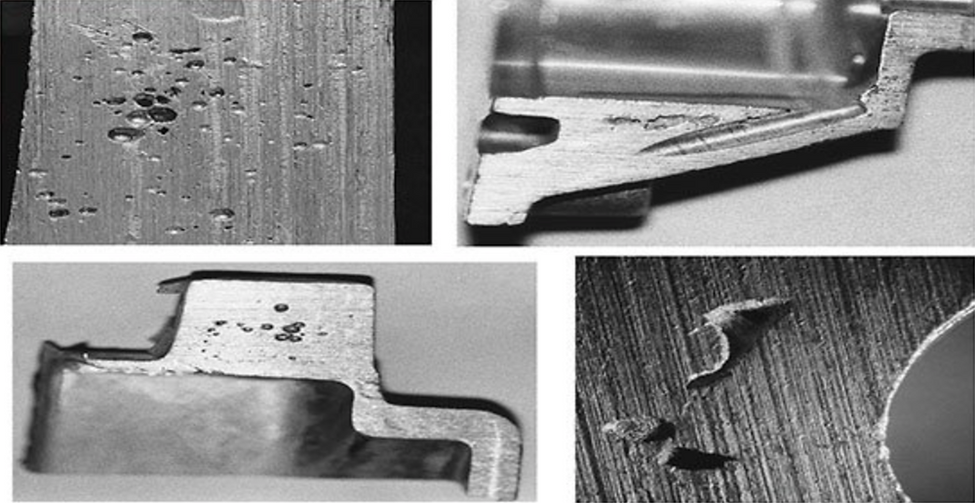
Porosität ist definiert als kleine Löcher oder Gaseinschlüsse in der Metallmatrix und beeinträchtigt die mechanischen Eigenschaften, indem sie die Festigkeit verringert, Luft und Gase durch die Struktur dringen lässt und zu sichtbaren Oberflächenfehlern bei Druckgussprodukten führt.
Die Ursachen:
- Gasförmige Bestandteile, die in Materialien vor dem Gießen vorhanden sind.
- Übermäßige Turbulenzen im Strom des geschmolzenen Metalls.
- Schlechte Entlüftung und unsachgemäße Konstruktion der Form.
- Schnelle Erstarrung, die Schrumpfungsporosität verursacht.
- Verunreinigung des geschmolzenen Metalls.
- Unzureichender Druck, der kein gleichmäßiges Fließen des Metalls bewirkt.
Prävention und Lösungen:
- Stellen Sie sicher, dass durch die Gestaltung der Anschnitte und Entlüftungen eine ordnungsgemäße Gasableitung gewährleistet ist.
- Verlangsamen Sie die Einspritzgeschwindigkeit, um die Glätte des in die Kavität eintretenden Metalls zu verbessern.
- Das Problem des Lufteinschlusses sollte durch die vakuumunterstützte Druckgusstechnik gelöst werden.
- Stellen Sie sicher, dass das geschmolzene Metall vor dem Einspritzen ausreichend entgast wird.
- Kontrolle der Abkühlungsgeschwindigkeit, um das Problem der Rissbildung und der Bildung anderer Erstarrungsfehler zu vermeiden.
- Prüfen und reinigen Sie die Oberflächen der Matrizen häufig, um das Risiko von Porosität aufgrund von Verunreinigungen zu verringern.
2. Cold Shut
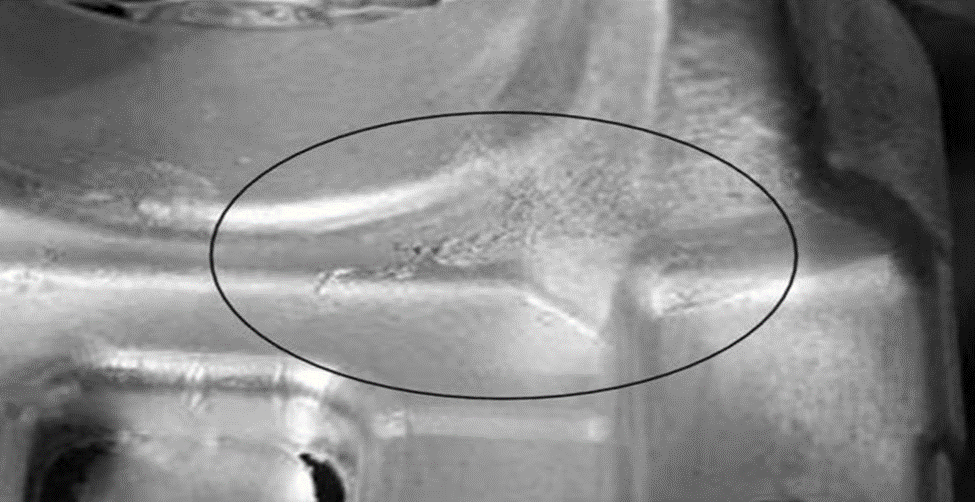
Ein kalter Verschluss entsteht, wenn zwei Ströme geschmolzenen Metalls nicht richtig verschmelzen und schwache Verbindungsstellen oder sichtbare Nähte im Gussteil bilden. Dieser Fehler vermindert nicht nur die mechanische Festigkeit, sondern erhöht auch das Risiko eines Bruchs und wirkt sich negativ auf die Haltbarkeit und das Aussehen des Bauteils aus.
Die Ursachen:
- Niedrige Temperatur des geschmolzenen Metalls.
- Es zeichnet sich durch eine langsame Einspritzgeschwindigkeit aus, die im Allgemeinen zu einer vorzeitigen Erstarrung führt.
- Schlechte Formgestaltung mit unzureichenden Fließkanälen.
- Dies kann zu einer übermäßigen Oxidation führen, die Oberflächenfilme bildet, die ein ordnungsgemäßes Verschmelzen verhindern.
- Ungleichmäßiger Metallfluss aufgrund eines schlecht konstruierten Anschnittsystems.
Prävention und Lösungen:
- Außerdem muss die optimale Temperatur für das Gießen von Metall eingehalten werden, um die richtige Fließfähigkeit zu gewährleisten.
- Erhöhen Sie die Einspritzgeschwindigkeit, um die Füllung zu vervollständigen und ein einziges Stück zu erhalten.
- Beseitigen Sie unnötige Fließhindernisse bei der Formgestaltung, damit sich das Metall ohne Schwierigkeiten bewegen kann.
- Erkennung und Behebung von Strömungsproblemen vor der Produktion durch den Einsatz thermischer Analysetools.
- Es sollten geeignete Entlüftungstechniken angewandt werden, um Lufteinschlüsse zu vermeiden, die häufig zu einer Verschlechterung der Kaltverformung führen.
3. Schrumpfungsdefekte
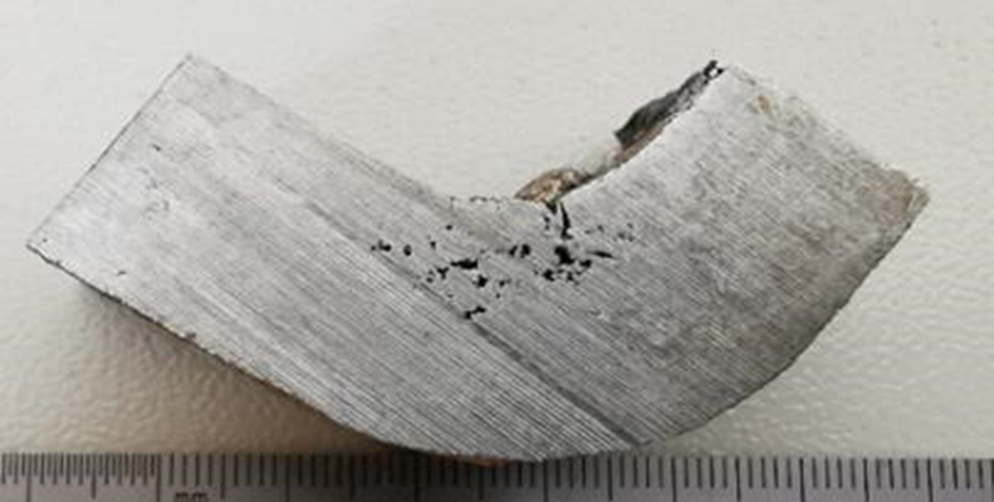
Schrumpfungsdefekte entstehen durch die Schrumpfung des Metalls während der Abkühlung, die zu inneren Hohlräumen oder Löchern führt, welche die strukturelle Integrität des Gussstücks beeinträchtigen. Infolgedessen verringern diese Fehler die mechanische Festigkeit des Endprodukts, führen zu potenziellem Versagen unter Belastung und verursachen eine schlechte Oberflächenqualität, was sowohl die Funktionalität als auch die Ästhetik der Endprodukte beeinträchtigt.
Die Ursachen:
- Unzureichende Metallzufuhr während der Erstarrung
- Ungleichmäßige Abkühlungsraten aufgrund eines ungeeigneten Werkzeugdesigns
- Hohe Metallschrumpfung aufgrund der Legierungszusammensetzung
- Rasche Abkühlung, die eine örtlich begrenzte Kontraktion verursacht
- Unzureichender Druck während der Erstarrungsphase
Prävention und Lösungen:
- Ändern Sie die Form so, dass sie gleichmäßig abkühlt und das geschmolzene Metall richtig zugeführt wird.
- Verwenden Sie Legierungen mit geringerer Schrumpfungsneigung und besseren Erstarrungseigenschaften.
- Sie wird zur Optimierung der Druckeinstellungen während der Erstarrung verwendet, um Lunker zu füllen und zu minimieren.
- Verwenden Sie kontrollierte Abkühlungsmethoden, um ein Gleichgewicht zwischen den Erstarrungsraten zu erreichen und die thermische Belastung zu verringern.
- Implementierung von Echtzeit-Überwachungs- und Simulationswerkzeugen zur Vorhersage und Vermeidung von Schwundfehlern.
4. Blitzlicht-Formation

Überschüssige dünne Metallschichten, die sich an der Trennebene oder am Formspalt durch das Entweichen von Metall unter hohem Druck bilden, werden als Grat bezeichnet. Obwohl der Grat nach dem Gießen abgeschnitten werden kann, führt ein übermäßiger Grat zu erhöhtem Materialabfall, Werkzeugverschleiß und damit verbundenen Produktionskosten und verringert somit die Gesamteffizienz des Druckgießverfahrens.
Die Ursachen:
- Übermäßiger Einspritzdruck führt dazu, dass das geschmolzene Metall in die Formspalte gepresst wird.
- Verschlissene Matrize oder unsachgemäße Verriegelung der Matrize, die Leckagen ermöglicht.
- Wenn die Schließkraft unzureichend ist, was zu einer Trennung der Matrize während des Einspritzens führt.
- Sie werden schlecht liegen und Lücken aufweisen, aus denen Metall austreten kann.
- Unklare Metallflusskontrolle durch Schmierung der Matrize
Prävention und Lösungen:
- Die richtige Klemmkraft muss beibehalten werden, um eine Ablösung der Matrize und Gratbildung zu vermeiden.
- Überprüfen und ersetzen Sie regelmäßig verschlissene Matrizen, um eine einwandfreie Abdichtung zu erreichen.
- Achten Sie auf die optimale Einstellung des Drucks, damit die Füllung mit minimalem Grat gefüllt und abgefüllt wird.
- Um unbeabsichtigte Lücken und Metalllecks zu vermeiden, sollte die Neuausrichtung der Matrizen verbessert werden.
- Führen Sie präzise Schmierungstechniken für die Matrize durch, um den Metallfluss zu kontrollieren und übermäßigen Metallaustritt zu vermeiden.
5. Inspektion von Oberflächenfehlern (Blasen, Risse und Falten)

Eine Vielzahl von Oberflächenfehlern, wie Blasen, Risse und Falten, beeinträchtigen das optische Erscheinungsbild und die mechanische Festigkeit des Gussteils und müssen verhindert und beseitigt werden. Sie verursachen Schweißfehler, die die Haltbarkeit des Produkts verringern, die Ausschussquote erhöhen und dafür sorgen, dass das Produkt nach dem Gießen schlecht haftet, z. B. beim Lackieren oder Beschichten.
Die Ursachen:
- Die Luft, die während des Gießens im flüssigen Kunststoff eingeschlossen wird.
- Außerdem kommt es zu thermischen Spannungen und Oberflächenunregelmäßigkeiten aufgrund ungleichmäßiger Abkühlungsraten.
- Überhitzung oder unkontrollierte Temperatur während der Erstarrung.
- oder die Metallverunreinigungen oder Einschlüsse, die die Gussoberfläche beeinträchtigen können
- Schlechte Schmierung der Matrize führte zu ungleichmäßigem Metallfluss und Oberflächenfehlern.
Prävention und Lösungen:
- Ordnungsgemäße Entgasung der Metallschmelze zur Vermeidung von Gaseinschlüssen vor dem Gießen.
- Kontrollieren Sie die Erstarrung und vermeiden Sie thermische Spannungen, indem Sie gleichmäßige Kühltechniken anwenden.
- Die Temperaturregelung der Matrizen sollte optimiert werden, um Überhitzung und ungleichmäßige Abkühlung zu vermeiden.
- Schaffung einer strengen Qualitätskontrolle, die es ermöglicht, alle Verunreinigungen vor dem Gießen zu erkennen.
- Auftragen von Beschichtungen und Schmiermitteln für Werkzeuge, um die Oberflächenqualität zu verbessern und Fehler zu reduzieren.
6. Einschlüsse und Verunreinigungen
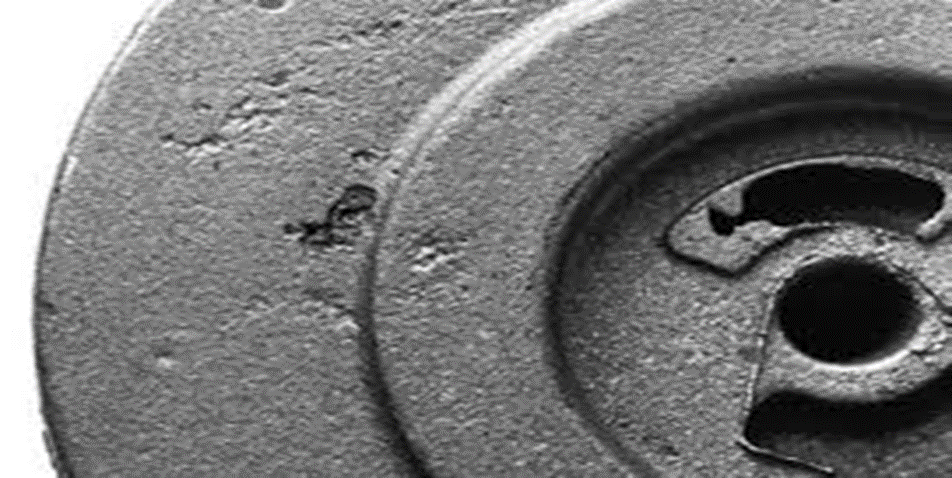
Unerwünschte Fremdpartikel wie Schlacke, Oxidschichten, Schmutz oder andere Verunreinigungen, die in einem fertigen Gussteil eingeschlossen sind, führen zu schlechten mechanischen Eigenschaften, schwacher struktureller Integrität und Oberflächenfehlern und werden als Einschlüsse bezeichnet. Das Vorhandensein dieser Verunreinigungen kann die Leistung und Haltbarkeit von Druckgussteilen verringern, so dass sie für Hochpräzisionsanwendungen nicht geeignet sind.
Die Ursachen:
- Verunreinigte Rohstoffe bestehen zum Beispiel aus unerwünschten Verunreinigungen.
- Fremdpartikel in einer Metallschmelze können nicht gut gefiltert werden, da
- Durch längere Einwirkung von Luft beim Schmelzen oder Gießen von Metall
- umfasst ineffiziente Metallverarbeitungspraktiken, die wiederum zu einer höheren Schlackenbildung führen
- Zu einer unzureichenden Schmierung des Gesenks gehört auch das Einbringen von Fremdkörpern in die Metallschmelze.
Prävention und Lösungen:
- Hochwertige Rohstoffe sollten ordnungsgemäß und ohne Verunreinigungen veredelt werden.
- Richten Sie wirksame Filtersysteme ein, um Schlacke, Oxide und andere Verunreinigungen vor dem Einspritzen aus der Metallschmelze zu entfernen.
- Sorgen Sie für eine kontrollierte Handhabung von geschmolzenem Metall und verwenden Sie gegebenenfalls eine Schutzgasabschirmung, um die Oxidation zu begrenzen.
- Reinigen und warten Sie die Gießgeräte regelmäßig, um eine Verunreinigung durch Materialreste zu vermeiden.
- Verwenden Sie eine geeignete Werkzeugschmierung, um sicherzustellen, dass sich keine Fremdkörper im Formhohlraum ablagern.
7. Fehlläufe und unvollständige Befüllung
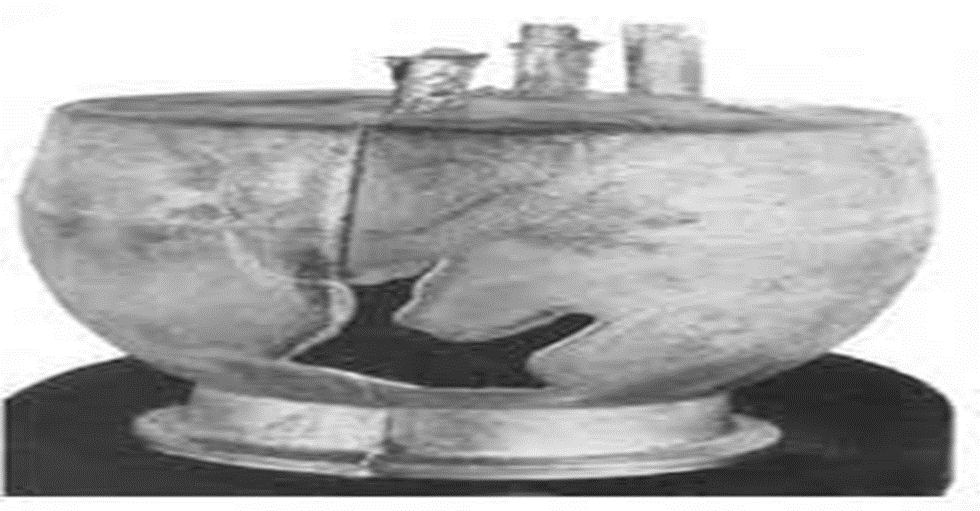
Eine Fehlschüttung liegt vor, wenn der Formhohlraum zu kurz gefüllt ist, was zu fehlenden Abschnitten, dünnen Wänden und Schwachstellen im fertigen Bauteil führt. Dies wirkt sich negativ auf die strukturelle Integrität und Funktionalität des Teils aus und ist daher für Hochleistungsanwendungen ungeeignet.
Die Ursachen:
- Bei niedriger Einspritzgeschwindigkeit oder niedrigem Druck wird die Form nicht vollständig bedeckt.
- Kalte Matrizenoberflächen verhindern Metallfluss und vorzeitige Erstarrung
- Verursacht ein unzureichendes Schmelzvolumen, das zu einer unzureichenden Kavitätenfüllung führt
- Schlechte Anschnitt- und Angusskonstruktion, die eine ungleichmäßige Verteilung des geschmolzenen Metalls verursachen
- Übermäßige Turbulenzen erzeugen Luftblasen, die den Metallfluss blockieren
Prävention und Lösungen:
- Erhöhen Sie die Temperatur des Metalls, damit es fließfähig wird und nicht vorzeitig erstarrt.
- Außerdem muss die Füllung der Kavitäten durch die richtige Einstellung des Einspritzdrucks und der Geschwindigkeit optimiert werden.
- Halten Sie die richtige Betriebstemperatur der Werkzeuge aufrecht und verhindern Sie, dass sie vorzeitig abkühlen.
- Verbesserung des Anschnitt- und Kufendesigns zur Förderung einer gleichmäßigen Metallverteilung.
- Simulieren Sie vor der Produktion den Metallfluss und die Gefahr von Fehlschüssen mit einer Simulationssoftware.
8. Matrizenerosion und -verschleiß
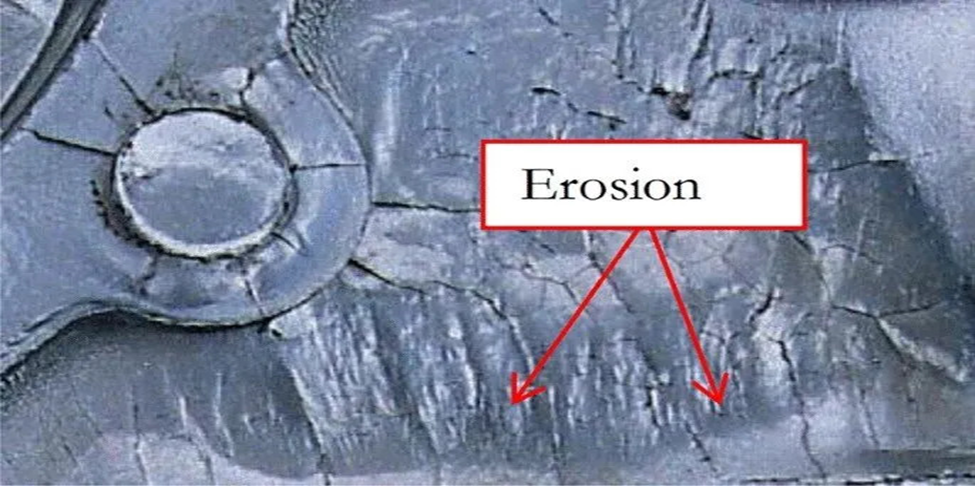
Unter dem Verschleiß von Erodierwerkzeugen versteht man den Verlust von Formoberflächen, der dadurch entsteht, dass das Hochgeschwindigkeitsmetall die Oberflächen der Formteile kontinuierlich abnutzt, bis die geforderten Abmessungen erreicht sind, was zu einer schlechten Oberflächengüte und einer kurzen Lebensdauer der Formwerkzeuge führt. Wenn dieser Fehler auftritt, muss die Form häufig ausgetauscht werden, wodurch die Produktionskosten steigen und die Gussqualität schwankt.
Die Ursachen:
- Außerdem ist es wiederholt geschmolzenem Metall mit hoher Temperatur ausgesetzt, was zu allmählichem Verschleiß führt.
- Relativ minderwertige Werkstoffe mit geringer Widerstandsfähigkeit gegen thermische und mechanische Belastungen
- Übermäßige Temperaturschwankungen können zu Rissen im Material aufgrund von Ermüdung führen.
- Dies führt zu einer Verschlechterung des Materials der Matrize bei hoher Einspritzung.
- Wenig Schmierung? Mehr Reibung und mehr Verschleiß sind die Folge.
Prävention und Lösungen:
- Eine davon ist die Verwendung hochwertiger, hitzebeständiger Stanzformen, die eine längere Lebensdauer aufweisen.
- Oberflächenschutzbeschichtungen, wie z. B. Nitrierung oder Keramikbeschichtungen, können aufgebracht werden, um die Lebensdauer der Matrize zu verlängern.
- Es sollen kontrollierte Abkühlungsmethoden eingesetzt werden, um die thermische Belastung und den vorzeitigen Verschleiß zu reduzieren.
- Um ein Gleichgewicht zwischen Geschwindigkeit und Druck bei minimaler Belastung der Matrize zu erreichen.
- Kontrollieren Sie die Stümpfe regelmäßig und halten Sie sie instand, um Erosionen so schnell wie möglich zu erkennen und zu beseitigen.
9. Heißes Knacken
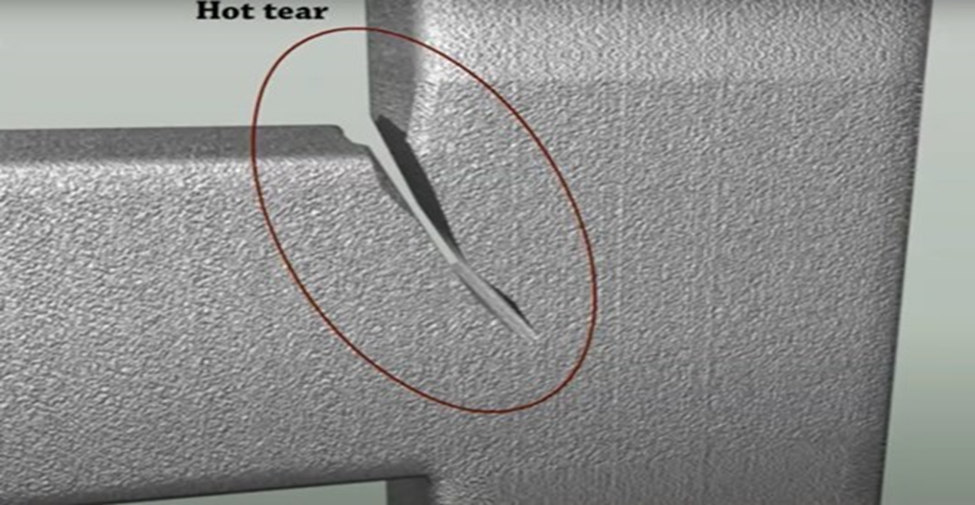
Risse, die während des halbfesten Zustands des Metalls aufgrund hoher thermischer Belastung und übermäßiger Schrumpfung auftreten, werden als Heißrisse bezeichnet. Diese Risse verschlechtern die mechanische Integrität des Gussstücks, d. h. sie erhöhen die Wahrscheinlichkeit eines Versagens des Gussstücks an der Stelle, an der die Risse unter Spannung oder Belastung auftreten.
Die Ursachen:
- Unzuverlässige Abkühlungsraten in der Form, was zu Spannungspunkten in bestimmten Bereichen führt
- Es ist sehr anfällig für thermische Spannungen und Rissbildung in der Legierungszusammensetzung.
- Verursacht auch übermäßige Eigenspannungen, die sich während der schnellen Erstarrung bilden und die Kontraktion des Metalls einschränken.
- Wenn die Form schlecht konstruiert ist, kommt es zu Temperaturschwankungen im Gussstück.
- Der Druck während der Erstarrung war zu gering, um die Ausbreitung von Rissen zu verhindern.
Prävention und Lösungen:
- Dazu gehört auch die Optimierung der Abkühlungsraten für eine gleichmäßige Erstarrung und die Minimierung der thermischen Belastung.
- Erhöhung der Rissfestigkeit von Legierungen durch geeignete Verwendung von Legierungen mit besserem Korngefüge.
- Anwendung von Entspannungsverfahren nach dem Gießen, d. h. kontrollierte Wärmebehandlung.
- Entwerfen Sie Formen mit geringerem Temperaturunterschied.
- Achten Sie beim Erstarren des Metalls auf den richtigen Druck, damit es fließt und keine Risse entstehen.
10. Löten
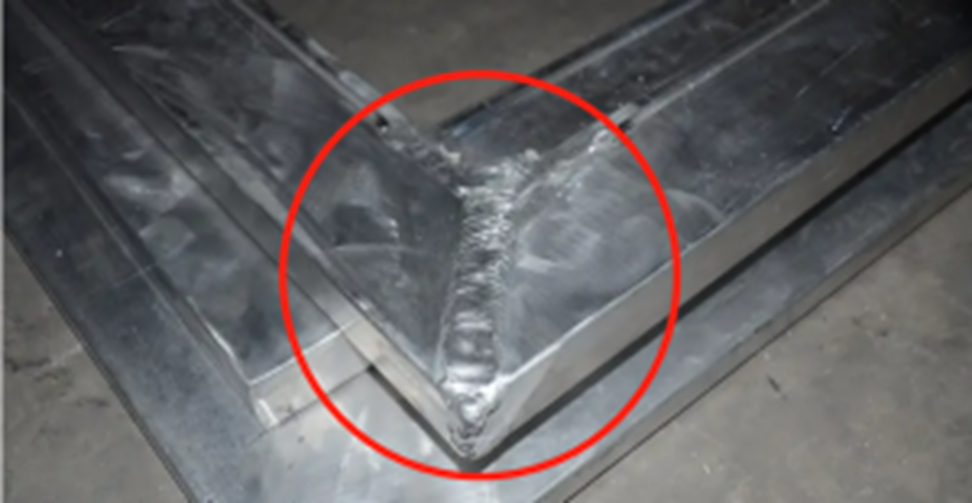
Das geschmolzene Metall haftet an der Oberfläche der Gussform, was sich beim Gießen nur schwer entfernen lässt und zu Oberflächenfehlern, Formenverschleiß und längeren Produktionsausfällen führt. Auch Maßungenauigkeiten und eine schlechte Oberflächengüte werden durch diesen Fehler verursacht, da er die Qualität des Endprodukts insgesamt beeinträchtigt.
Die Ursachen:
- Erhöhung der Metallhaftung in der Legierung aufgrund des hohen Aluminiumgehalts
- Zu hohe Werkzeugtemperaturen, damit sich das Metall mit der Werkzeugoberfläche verbindet
- Unzureichender Schutz gegen Verkleben aufgrund schlechter Schmierung der Matrize
- Unzureichende Kühlung führt dazu, dass das geschmolzene Metall zu lange mit der Matrize in Kontakt bleibt - Verzunderte oder beschädigte Matrizenoberflächen, die das Anhaften des Metalls fördern.
Prävention und Lösungen:
- Es werden stets hochwertige Schmiermittel verwendet, um ein Festkleben des Metalls zu verhindern.
- Sie ermöglicht es, die Werkzeugtemperatur im optimalen Bereich zu steuern, wenn die Heißhaftung zu stark ist.
- Verringern Sie die Metallhaftung durch geeignete Beschichtungen der Matrize, z. B. durch Keramik- oder Nitridschichten.
- Verkürzung der Kontaktzeit zwischen Metall und Werkzeug und Verbesserung der Effizienz des Kühlsystems.
- Prüfen und polieren Sie die Oberfläche der Stanzformen regelmäßig, um eine nicht klebende, glatte Oberfläche zu erhalten.
Schlussfolgerung
Der Hochdruck Druckguss ist ein leistungsfähiges Fertigungsverfahren, das komplexe Metallteile mit hoher Genauigkeit und maximaler Effizienz herstellt. Es gibt jedoch verschiedene Arten von Fehlern, die durch ungeeignete Prozessparameter, Materialprobleme und/oder Fehler in der Werkzeugkonstruktion entstehen. Hersteller können vorbeugende Maßnahmen ergreifen, z. B. eine optimale Prozesssteuerung der Form, die richtige Auswahl des Materials usw., wenn sie diese üblichen Fertigungsfehler verstehen.
Ein Unternehmen kann die Produktqualität verbessern, die Produktionskosten senken und eine höhere Produktionseffizienz in Druckgussbetrieben erreichen, indem es den Schwerpunkt auf eine kontinuierliche Prozessverbesserung sowie auf Strategien zur Fehlervermeidung legt.
Häufig gestellte Fragen (FAQs)
1. Was sind die Hauptgründe für Fehler beim Druckguss?
Zu den Hauptursachen für Defekte beim Druckguss gehören eine unsachgemäße Formgestaltung, schlechter Metallfluss, eingeschlossene Gase, hohe thermische Spannungen, ungleiche Kühlung und verunreinigte Rohstoffe. Diese Fehler lassen sich durch die Optimierung der Prozessparameter und durch den Einsatz von Qualitätskontrollmaßnahmen verringern.
2. Welche Rolle spielt die Porosität für die Leistung von Druckgussbauteilen?
Das Vorhandensein von Porosität schwächt die strukturelle Integrität von Druckgusskomponenten, verringert die Festigkeit und führt zu Luftlecks in druckdichten Komponenten sowie zu anästhetischen Mängeln. Die Porosität lässt sich durch ordnungsgemäße Entgasung, optimierte Anschnittsysteme und vakuumunterstütztes Gießen minimieren.
3. Wie lassen sich Kaltverformungen beim Druckguss vermeiden?
Die richtige Gießtemperatur, höhere Einspritzgeschwindigkeiten, eine optimierte Werkzeugkonstruktion für einen reibungslosen Metallfluss und die Anwendung von Thermoanalyse-Tools zur Ermittlung möglicher Fließprobleme können helfen, Kaltverschlüsse zu vermeiden.
4. Die Erosion der Druckgussform ist ein wichtiges Problem beim Druckguss, weil?
Die wiederholte Einwirkung von geschmolzenem Hochtemperaturmetall auf die Formen führt zu Erosion, die die Lebensdauer der Formen verkürzt und die Präzision der Gussteile beeinträchtigt. Die Lebensdauer der Formen kann durch die Verwendung hochwertiger Materialien, Schutzbeschichtungen und eine kontrollierte Kühlung der Formen verlängert werden.
5. Was macht die Qualität und Konsistenz von Druckgussprodukten besser?
Strenge Qualitätskontrollen, die Optimierung von Prozessparametern, die Kontrolle der Formtemperatur, die Verwendung hochwertiger Legierungen und die Überprüfung von Formen und Maschinen werden regelmäßig durchgeführt, um die Qualität der Druckgussprodukte ständig zu verbessern.