Una de estas aleaciones, muy utilizada en las industrias de fabricación y fundición, es la aleación Zamak 5 a base de zinc, que presenta algunas características únicas. Esto se debe a la gran solidez, excelente durabilidad y gran resistencia a la corrosión que ofrece el Zamak 5, lo que lo convierte en un material ideal para su uso en operaciones de fundición a presión. Tras la extracción, el Zamak 5 se funde muy poco y tiene unas características de fundición excelentes, lo que hace del Zamak 5 un material ideal para la fabricación de automóviles y las industrias de productos de consumo y ferretería. Los participantes de la industria tendrán la certeza sobre las propiedades de la aleación Zamak 5, como su composición y diversos usos concretos, para tomar decisiones de producción y optimizar el proceso de eficacia operativa.
El artículo analiza la aleación Zamak 5 a través de su composición química y la fabricación métodos junto con el control de la temperatura y el mantenimiento de la presión, y los atributos de las sustancias mecánicas en el rendimiento industrial.
Zamak 5 Aleación
Zamak 5 funciona como una aleación líder a base de zinc que la industria denomina aleación de zinc-aluminio. Zamak 5 se compone químicamente de 3,5 a 4,3 por ciento de aluminio junto con 0,03 a 0,08 por ciento de magnesio y 0,75 a 1,25 por ciento de cobre. También obtiene su resistencia superior gracias a los elementos que el fabricante puede utilizar para crear componentes de alta resistencia para su uso en las industrias de automoción y aeroespacial, y de bienes de consumo. La resistencia a la tracción, así como una densidad de 6,7 g/cm³ y un rango de punto de fusión relativamente amplio de 380-385°C, están presentes en esta aleación por su buena durabilidad y buena precisión.
Composición y propiedades del zamak 5

Composición química del Zamak 5
Las propiedades mecánicas del Zamak 5 se mejoran mezclándolo con una aleación a base de zinc en porcentajes controlados de zinc y aluminio y cobre, y magnesio.
Esta propiedad de fácil fusión es una de las cualidades que hacen del Zamak 5 una excelente aleación de fundición a presión en comparación con el 96-98% de la aleación que es el ZINC. Para obtener resultados superiores, es fundamental utilizar material de zinc con una pureza de 99,99% a fin de evitar contaminantes que perjudicarían la resistencia y la integridad estructural de la aleación.
La solidificación del material Zamak 5 mejora con la adición de aluminio (3,5 a 4,3%), ya que mejora la microestructura de la aleación. Las regiones que las forman tienen una composición que combina características de ductilidad y dureza en la estructura del material. Es necesario medir el contenido exacto de aluminio en el Zamak para evitar defectos en el material como el agrietamiento, así como problemas de fragilidad.
La presencia de magnesio entre 0,03% y 0,08% en el zamak 5 se debe a que con este elemento se bloquea la corrosión de las microfisuras en los límites de grano debido a las impurezas. Como esta adición hace que la aleación sea más fluida, el molde se beneficia al obtener mejores características de llenado. Si se omite el magnesio, la superficie del Zamak 5 será defectuosa, además de muy difícil de mecanizar.
El Zamak 5 se funde con grafito y tiene buena resistencia al desgaste y capacidad de tratamiento térmico cuando la cantidad de cobre añadida es del 0,75 al 1,25 por ciento, lo que mejora la resistencia a la fluencia, adecuada para aplicaciones de variación térmica. Dado que el Zamak 5 se vuelve quebradizo cuando se superan los límites correctos, la proporción de cobre es importante.
Propiedades físicas del Zamak 5

El peso de un material de Zamak 5 es de 6,7 g/cm³, con una densidad entre el acero y superior a la de las aleaciones de aluminio. Su favorable relación peso/resistencia hace que el Zamak 5 sea adecuado para muchas estructuras en las que intervienen materiales resistentes con pesos reducidos.
El zamak 5 funde entre 380 y 385 grados Celsius, lo que hace que la fundición exacta de zamak 5 resulte rentable en comparación con el aluminio.
A una temperatura media de 120 °C, la resistencia a la tracción del Zamak 5 fue de 330 MPa, con un límite elástico de 220 MPa y un potencial de alargamiento del 7-10%, que cumple los requisitos de uso industrial. El Zamak 5 es resistente y adaptable, ya que tiene un alto límite elástico de 220 MPa y el alargamiento máximo antes casi del fallo del 7-10%.
Propiedades mecánicas del Zamak 5
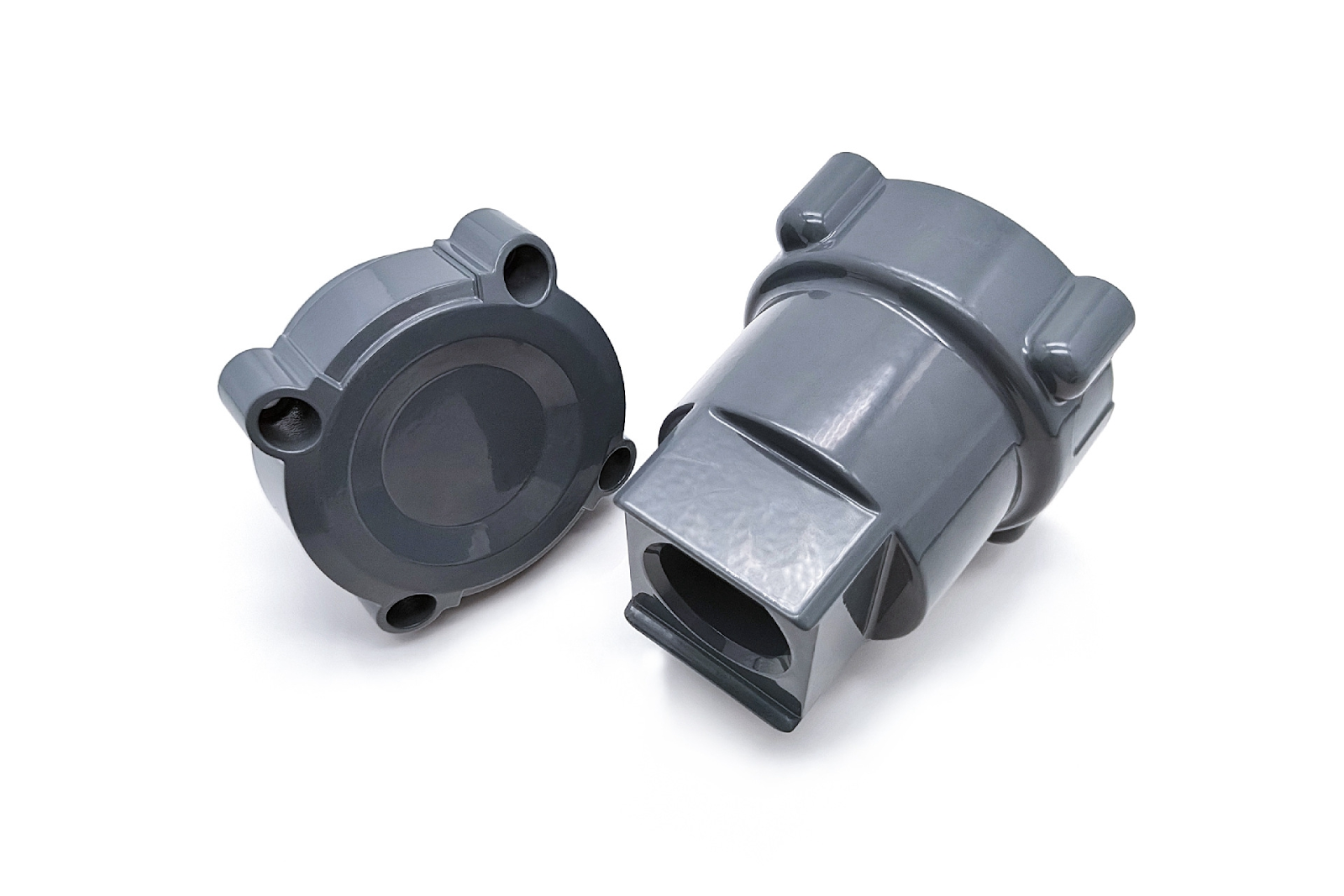
Zamak 5 tiene 91 niveles de dureza HB Brinell perfectamente equilibrados entre resistencia y dureza superficial, lo que lo convierte en una combinación excelente para mangos decorativos u otras piezas que exijan protección contra el desgaste.
Resistencia al impacto:
La medida de la resistencia al impacto Charpy a temperatura ambiente del material es de 53 J, mientras que a -20 °C se reduce a 35 J. La aleación tiene una gran resistencia al impacto, por lo que puede protegerse de las tensiones mecánicas y las vibraciones en condiciones de fuerza dinámica.
Zamak 5 puede soportar esfuerzos cíclicos de 100 MPa y sobrevivir sin fallos hasta 1 millón de ciclos. Zamak 5 se comporta en la práctica con una estabilidad fiable bajo carga continua, por lo que es adecuado para los componentes de la máquina y la pieza de la lavadora.
Propiedades mecánicas de la aleación Zamak 5
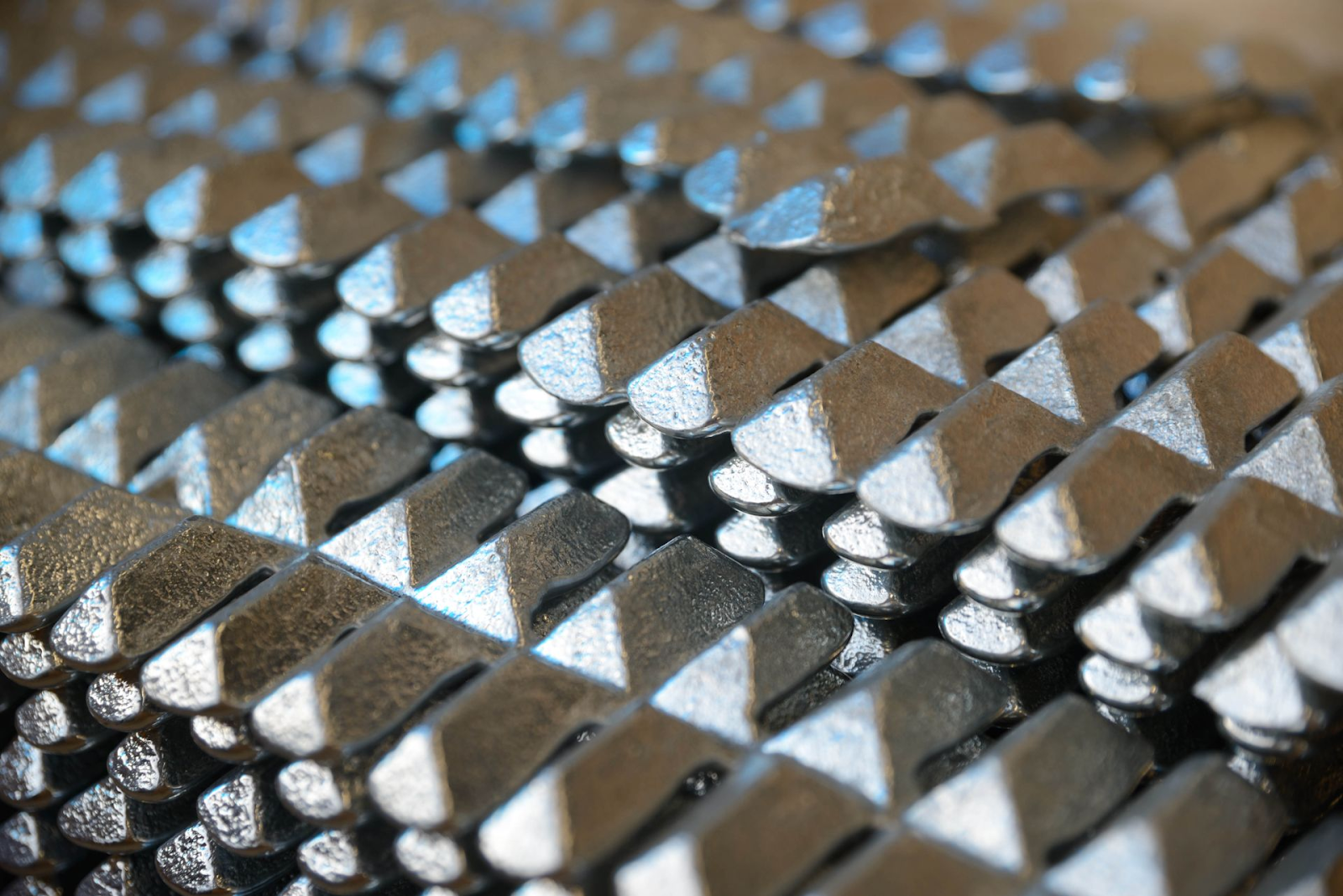
La tabla siguiente muestra las características mecánicas esenciales de la aleación de aluminio Zamak 5.
Propiedad | Valor |
Dureza Brinell | 91 HB |
Resistencia a la tracción | 328 MPa |
Límite elástico (0,2%) | 269 MPa |
Resistencia al cizallamiento | 262 MPa |
Resistencia a la compresión | 600 MPa |
Resistencia a la fatiga | 56,5 MPa |
Resistencia al impacto | 65 J |
Módulo de elasticidad | 96 GPa |
Alargamiento | 7% en 50 mm |
Los valores de resistencia de la aleación Zamak demuestran su capacidad para soportar tensiones y la sitúan dentro de otros materiales en los que puede utilizarse en aplicaciones exigentes. Zamak 5 ofrece una resistencia superior a las cargas de fatiga y a los impactos, por lo que es adecuado para piezas sometidas a cargas de fuerza repetidas.
Propiedades físicas de la aleación Zamak 5
A través de todo su conjunto de características, el comportamiento de Zamak 5 está controlado por las propiedades físicas.
Propiedad | Valor |
Intervalo de fusión | 380-386°C |
Densidad | 6,60 g/cm³ |
Conductividad eléctrica | 26% IACS |
Conductividad térmica | 109 W/mK |
Capacidad calorífica específica | 419 J/kg-°C |
Coeficiente de dilatación térmica | 27,4 µm/m°K |
Relación de Poisson | 0.30 |
La combinación de propiedades de Zamak 5 hace que funcione bien en diferentes entornos y para condiciones de aplicación adecuadas para la conductividad tanto térmica como eléctrica. Las características apropiadas de densidad y capacidad térmica hacen que Zamak 5 sea imprescindible para sistemas sensibles al calor y también posee buenas propiedades eléctricas, que proporcionan una variedad en una forma de uso de una pieza eléctrica.
Ventajas de la aleación Zamak 5
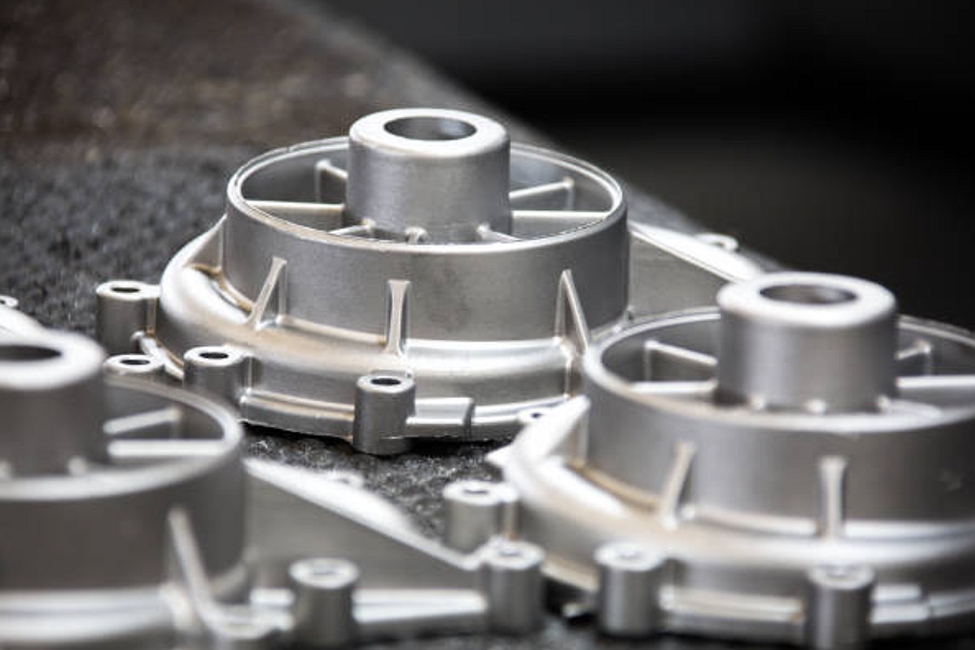
En comparación, las superiores propiedades de resistencia que exhibe Zamak 5 al mismo tiempo con un menor peso se deben a que su relación resistencia-peso es de 49 MPa, superior a la del aluminio A380. Debido a su característica dominante de alto nivel de resistencia con alta eficiencia de peso, Zamak 5 puede utilizarse con éxito en diversas aplicaciones industriales que están relacionadas con los sectores del automóvil y aeroespacial.
Buena resistencia a la corrosión: Su aleación hace que Zamak 5 sea superior a la corrosión en otras condiciones salinas y húmedas, en las que su aleación ofrece ventajas perfectas para herrajes marinos y aplicaciones expuestas. Zamak 5 ha sido probado en laboratorio, y la exposición a niebla salina durante más de 500 horas sobre el material no daña la superficie.
Excelente moldeabilidad: El Zamak 5 es especialmente bueno para la fundición a presión porque el metal es suficientemente fluido para fluir fácilmente en formas de fundición complejas. La colabilidad del Zamak 5 es aprovechada por los fabricantes con su fácil y rápida postproducción, que requiere un mínimo y particularmente cuando las variaciones en las dimensiones geométricas no afectarán a una función.
Alta ductilidad: El Zamak 5 puede conformarse en frío mediante procesos que tienen éxito debido a su ductilidad, que oscila entre 7% y 10%. El Zamak 5 admite operaciones de doblado, garganta y taladrado, lo que permite mejorar el Zamak 5 al aumentar su versatilidad de fabricación.
Proceso de fabricación del zamak 5
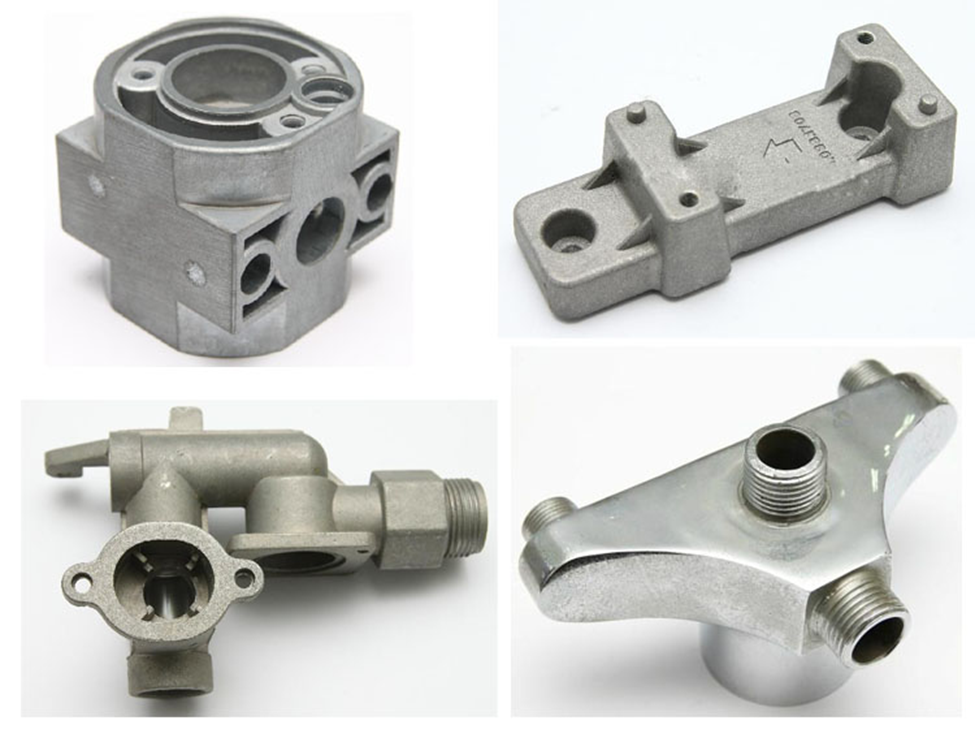
Proceso de fundición a presión
El material Zamak 5 tiene un punto de fusión bajo, lo que significa que no puede fabricarse en una macro matriz de inyección, pero es factible a partir de la matriz de cámara caliente. El metal fundido se recibe a alta presión en el molde de acero para fabricar piezas con una tolerancia estrecha y una superficie fina. Sin embargo, el método alcanza índices de eficacia sobresalientes, sobre todo cuando hay que fabricar grandes cantidades de productos.
Parámetros del proceso
De hecho, los tres parámetros cruciales del proceso son: la presión de inyección, que oscila entre 700 y 1.000 bares, junto con la temperatura de la matriz, que oscila entre 150 y 200 °C, y la velocidad de enfriamiento, que es de 50 °C/s. La calidad mecánica, excelente, debe controlarse con gran precisión para conseguir que los defectos del producto sean mínimos.
Mecanizado y acabado
Gracias a sus características, Zamak 5 se presta fácilmente a procesos de acabado tras la fase de fundición. La alta ductilidad del producto permite protocolos exactos de roscado y ranurado, así como procedimientos precisos de galvanoplastia y métodos de recubrimiento en polvo para mejorar la protección contra la corrosión y las características estéticas.
Diferencias entre Zamak 5 y Zamak 3
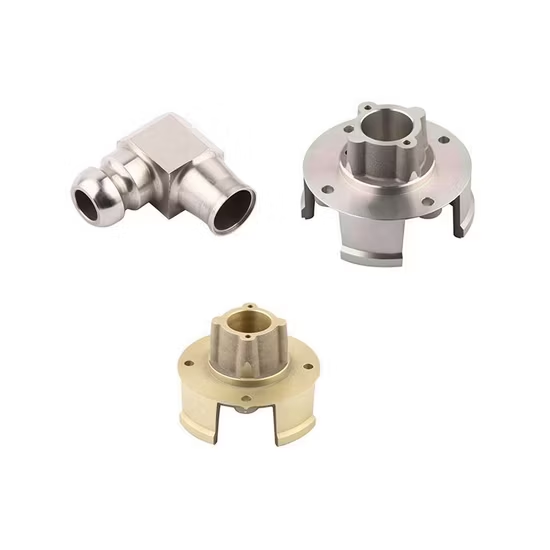
Composición química: El Zamak 5 no es Zamak 3 porque tiene tolerancia al calor debido a la inclusión de un elemento de cobre y el Zamak 3 no tiene cobre porque proporciona las mejores capacidades de protección contra la fundición y la humedad.
Propiedades mecánicas: El Zamak 5 tiene mayor resistencia y dureza, por lo que tiene mejores propiedades mecánicas y es más útil en piezas que tienen requisitos de carga que el Zamak 3.
Comparación entre Zamak 5 y Zamak 3
Propiedad | Zamak 5 | Zamak 3 |
Composición química | Zinc (96-98%), Aluminio (3,5-4,3%), Magnesio (0,03-0,08%), Cobre (0,75-1,25%) | Zinc (95-97%), Aluminio (3,5-4,3%), Magnesio (0,02-0,06%), Cobre (<0,1%) |
Resistencia a la tracción | 330 MPa | 240 MPa |
Límite elástico | 220 MPa | 160 MPa |
Alargamiento | 7-10% | 10-15% |
Dureza | 91 HB (Brinell) | 80 HB (Brinell) |
Densidad | 6,7 g/cm³ | 6,6 g/cm³ |
Punto de fusión | 380-385°C | 380-385°C |
Aplicaciones | Automoción, aeroespacial, bienes de consumo, aplicaciones de alta resistencia | Juguetes, artículos de decoración, aplicaciones poco estresantes |
Ventajas clave | Resistencia a altas temperaturas, resistencia al desgaste, mayor resistencia y durabilidad | Excelente colabilidad, resistencia a la corrosión en ambientes húmedos |
Desventaja | Menos dúctil, más susceptible a la fragilidad a temperaturas más elevadas | Menor resistencia a la temperatura y al estrés |
El zamak 5 y el zamak 3 poseen estructuras químicas, características mecánicas y casos de utilización comunes paralelos, y esta tabla lo muestra en un solo lugar.
Zamak 5 (ASTM AC41A, Z35531, Mazak 5) Aleación de zinc
El Zamak 5 es una aleación de zinc y aluminio que presenta numerosas aplicaciones por sus excelentes propiedades de resistencia y su versatilidad. Esta aleación es ampliamente conocida en la industria como Zamak 5, aunque bajo la denominación AC41A en las normas ASTM, y Z35531 en el sistema de clasificación UNS. El Zamak 5 está compuesto a base de zinc primario aleado con aluminio y cobre para potenciar sus características mecánicas, similares a la fuerza, la resistencia a la corrosión y la dureza. Como se ha indicado, las propiedades de fabricación se aplican al Zamak 5 en su estado previo a cualquier proceso de revenido u otro tratamiento. Dado que puede producir tanto piezas intrincadas y detalladas como piezas de alta calidad, la aleación Zamak 5 se utiliza para la fundición a presión. Dado que proporciona una capacidad operativa tanto económica como fiable, el zamak 5 ha establecido su posición en productos de automoción y electrónica, así como en artículos decorativos.
Punto de fusión del zamak 5
Los valores de fusión de la aleación Zamak 5 se sitúan entre 380°C y 386°C (716°F a 727°F), que son inferiores a los de otros materiales metálicos. El uso de Zamak,5 al tener una temperatura de fusión inferior a la media, tiene un papel importante en las operaciones de fundición a presión debido a la facilidad de moldeabilidad en temperaturas de proceso más bajas. El bajo intervalo de fusión de la aleación facilita el trabajo en la fabricación de precisión debido a su requisito de fusión y solidificación rápidas en la fabricación de componentes intrincados. El Zamak 5 tiene un punto de fusión bajo, lo que facilita al fabricante de acabados su elección en numerosas producciones de automoción, así como en la fabricación de muebles y bienes de consumo.
Módulo de Young de Zamak 5
La aleación Zamak 5 tiene ciertas características técnicas. El módulo de Young es de ~96 Giga pascales (GPa). Este valor da la rigidez del material, ya que refleja cuánto resiste el material a la deformación bajo la tensión aplicada. La rigidez media del Zamak 5 se debe a que el módulo de Young es de 96 GPa, lo suficientemente cerca para alcanzar los requisitos tanto de resistencia como de flexibilidad. El material tiene la resistencia para la que ha sido diseñado y sigue siendo flexible, ya que su rigidez en la escala moderada de 96 GPa (Giga pascales) permite a la aleación mantener la integridad estructural durante las aplicaciones mecánicas.
Materiales equivalentes a Zamak 5
Diferentes aplicaciones requieren diferentes sustancias, con la aleación específica de zinc Zamak 5 que tiene propiedades particulares, pero existe cualquier número de materiales equivalentes junto con sustancias adicionales. Los tres principales materiales alternativos que pueden utilizarse en lugar de Zamak 5 son Zamak 3 (ZnAl4Cu1), Zamak 2 y Zamak 13.
Zamak 3 (ZnAl4Cu1)
Entre las aleaciones de la familia Zamak, Zamak 3 se cuenta entre los tipos más populares debido a sus características similares con el Zamak 5. El zinc, el aluminio y el cobre son las sustancias de las que estas aleaciones derivan sus estructuras cristalinas. El zamak 3 se utiliza como sustituto del zamak 5 porque contiene menos cobre, responsable de su menor solidez y resistencia a la corrosión.
Fundición inyectada de zinc
Además, el zamak 2 y el zamak 7 tienen una buena capacidad de fundición que los hace adecuados para su uso en producciones que requieran gran precisión y alta calidad de acabado, tanto con fundición inyectada de zinc aleaciones. Aunque estas aleaciones tienen propiedades mecánicas diferentes, se utilizan los mismos procesos de fabricación para ellas.
ALSi12
Cuando se requiera una resistencia ligeramente elevada a temperaturas más altas, los usuarios podrán sustituir la aleación de aluminio y silicio ALSi12 por algunos suministros alternativos para su adquisición. La misma composición química no tiene por qué coincidir entre Zamak 5 y ALSi12, ya que ambos se utilizan en la producción de fundición y moldeado a presión.
ADC 12 (aleación de aluminio)
Cuando se requiera una buena resistencia a la corrosión y colabilidad, la aleación de aluminio ADC 12 puede utilizarse como material equivalente para sustituir algunas aplicaciones de fabricación. Dado que Zamak 5 puede ser ligeramente más duro, los criterios de rendimiento serían la base para la selección.
Según el equilibrio de las propiedades mecánicas individuales adquiridas de resistencia a la tracción y a la corrosión, así como de dureza, tal equivalente es elegido por los equipos de producción.
Proceso de fundición de Zamak 5
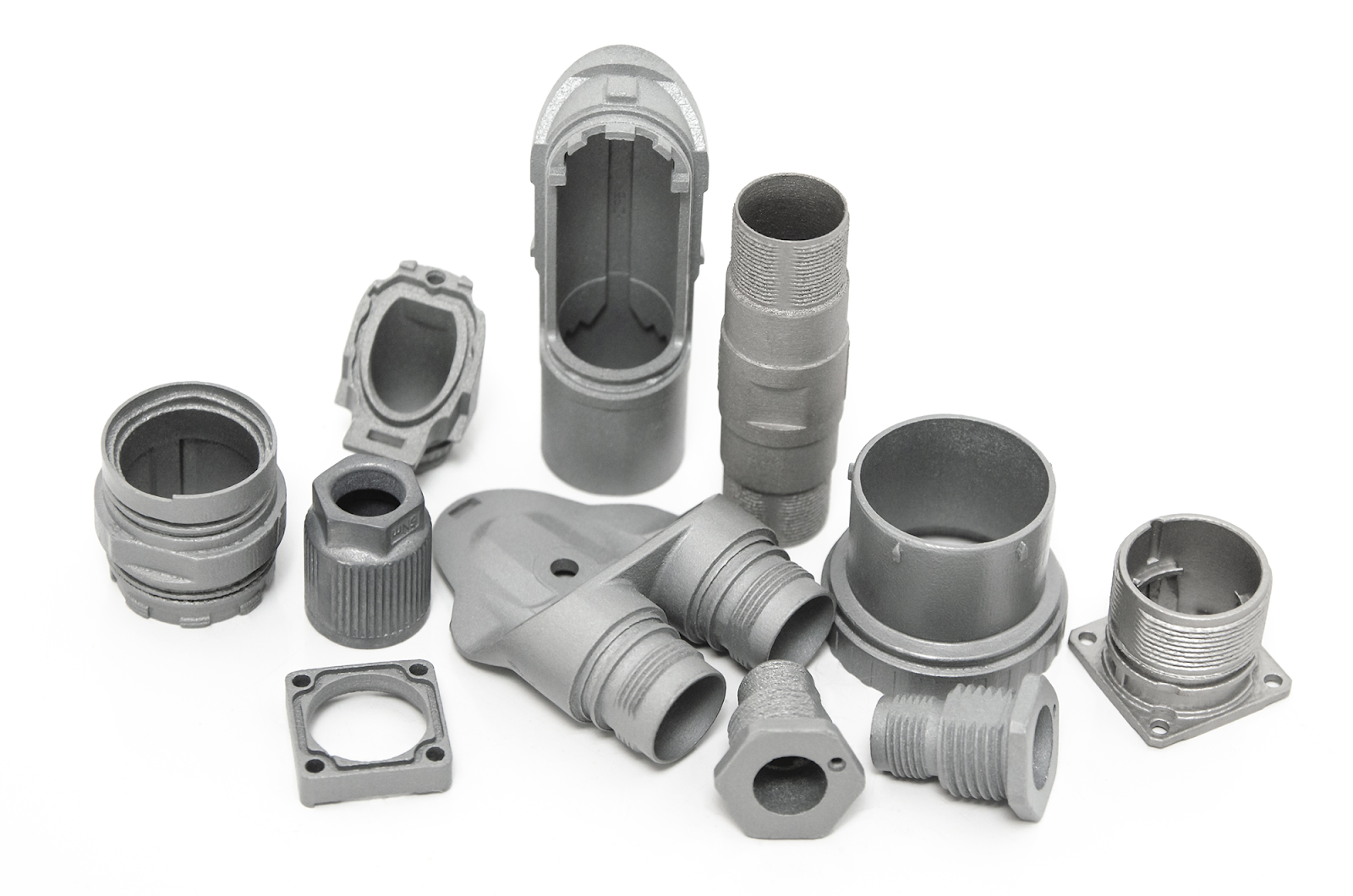
La fundición de Zamak 5 puede conservarse y optimizarse en el producto final mediante distintas fases del procedimiento de fundición de Zamak 5. El principal método de producción de Zamak 5 es la fundición a presión,g en la que el metal fundido de Zamak 5 se inyecta a alta presión en moldes metálicos. La operación de fundición de Zamak 5 se compone de varias operaciones sucesivas.
Preparación del molde:
Es necesario calentar la matriz por encima de una temperatura determinada para que, durante el proceso de inyección, se evite el choque térmico de la probeta. A continuación, permitimos que la corriente se utilice en el exterior para asegurarnos de que la superficie de colada y la producción de salida estén siempre libres de defectos.
Fundición de la aleación Zamak 5:
La Zamak 5 tiene que alcanzar un calor de entre 380-390°C (716-734°F) antes de volverse totalmente líquida. La aleación se calienta en el horno hasta esta temperatura especificada, y el estado de la aleación pasa a ser líquido, susceptible de inyección.
Inyección de la aleación fundida:
La aleación Zamak 5 pasa de la forma líquida a la cavidad del molde debidamente preparada bajo alta presión después de la fusión. Presiones de inyección para diferentes complejidades de piezas y su magnitud son 30-60 MPa, que se aplican por los fabricantes para formar.
Refrigeración y expulsión:
A continuación, cuando el molde recibe el material de aleación fundido, empieza a enfriarse y a solidificarse. Se expulsa del molde cuando deja de permanecer a una temperatura de enfriamiento adecuada. La duración del enfriamiento del molde y su temperatura pueden controlarse para garantizar la calidad de la colada final (evitar deformaciones).
Operaciones de acabado:
La expulsión de las piezas de Zamak 5 exige su tratamiento mediante diversos procedimientos de acabado por los que las piezas se recortan y también se desbarban, y se pulen y, por último, se recubren para cumplir los requisitos finales.
El proceso de fundición Zamak 5 es eficaz para una producción de gran volumen, ya que puede crear objetos complejos con requisitos de tolerancia precisos. Una aleación con una fluidez excepcional corrige el llenado de zonas complejas de la cavidad del molde, por lo que la aleación es adecuada para la producción de componentes con detalles finos en los sectores de automoción y ferretería, así como en dispositivos electrónicos de consumo.
Diferentes normas para la aleación Zamak 5: Una perspectiva mundial
Zamak 5, la aleación de zinc algo versátil, se conoce generalmente por diferentes nombres; sin embargo, estas identificaciones se originan en la norma particular así como en el país de origen. Las distintas especificaciones relacionadas con el Zamak 5 presentan diferentes tendencias específicas de las regiones según el método de producción y la designación anterior. Estas designaciones son muy importantes para los usuarios de Zamak 5 porque definen protocolos para la empresa según las especificaciones de la aleación en diversos sectores del mercado y normas regionales. Todas las normas mundiales y denominaciones alternativas de la aleación Zamak 5 se presentan en una visión general considerable.
Nombres y normas mundiales para la aleación Zamak 5
En la tabla siguiente se indican las normas de los distintos países y las formas en que se denomina su aleación Zamak 5.
Nombre tradicional | Zamak 5 |
Composición breve Nombre | ZnAl4Cu1 |
ASTM | CA 41A |
Nombre común | Aleación 5 |
China | ZX03 |
JIS (Japón) | Lingote Tipo 1 (Lingote) ZDC1 (Aleación) |
Denominación europea abreviada | ZL0410 (Lingote) ZP0410 (aleación) |
Alemania DIN 1743-2 | Z420 |
Francia NFA 55-010 | Z-A4UI |
REINO UNIDO BS 1004 | Aleación B |
UNS (Sistema Unificado de Numeración) | Z35530 (Lingote) Z35531 (aleación) |
¿Por qué son importantes estas normas?
Las diferentes normas de aleación de Zamak 5 se adoptaron debido a la adopción global de una combinación de prácticas industriales de influencia regional y requisitos de comunicación internacional. Esto (Zamak 5) significa que las empresas que producen materiales Zamak 5 también, y sus ingenieros, necesitan conocer las normas regionales y las designaciones de ese material en particular para seleccionar el material adecuado para su aplicación. Las normas son detalles imperativos de la composición química de la aleación Zamak 5, las normas de rendimiento, para elegir los materiales adecuados para las operaciones de fundición y mecanizado.
Ventajas de la aleación Zamak 5
El Zamak 5 se emplea en numerosas aplicaciones industriales como una aleación de zinc versátil y robusta, que proporciona multitud de atributos útiles a diversos esfuerzos de fabricación. El Zamak 5 multiplica por tres las características de resistencia superior, así como de gran tenacidad y propiedades protectoras que lo hacen adecuado para abundantes aplicaciones materiales en dispositivos de consumo y equipos industriales. Estas son las ventajas fundamentales que la aleación Zamak 5 ofrece a los fabricantes.
1. Resistencia, durabilidad y seguridad
La aleación de zinc Zamak 5 conserva sus excelentes cualidades de rendimiento en términos de resistencia y también de niveles de dureza. Esta aleación ofrece una gran resistencia a la fuerza, por lo que sigue siendo una solución sólida para aplicaciones exigentes que requieren porcentajes muy elevados de tensión. Zamak 5 es importante para las industrias porque es muy resistente físicamente y, al mismo tiempo, cumple las medidas de seguridad absolutas para eventos de contacto.
El zamak 5 ofrece una ventaja de seguridad frente a algunos metales, como el magnesio, ya que evita los problemas relacionados con el fuego. El zamak 5 posee una cualidad poco común que lo distingue de los demás materiales comunes, ya que nunca absorbe humedad, por lo que no presenta problemas de absorción de agua similares a los del plástico. Debido a su característica de seguridad para el contacto humano, el Zamak 5 se utiliza en la fabricación de envases para cosméticos.
Como resultado de sus atributos relacionados con la fiabilidad, que dan seguridad tanto a los fabricantes como a los usuarios finales, Zamak 5 está siendo elegido por nuevas aplicaciones tecnológicas.
2. Calidad superior en fundición a presión
El Zamak 5 se utiliza para aplicaciones de fundición a presión debido a la capacidad de esta aleación para producir piezas de alta calidad sin defectos. Debido a su capacidad para crear productos lisos y acabados con defectos mínimos, la aleación Zamak 5 produce piezas de fundición a presión de alta calidad que requieren un proceso de postproducción mínimo.
El zamak 5 posee las propiedades del zam natural, lo que hace que se utilicen técnicas de moldeo exactas para fabricar productos que presentan altos niveles de perfección en el proceso de producción. Como el Zamak 5 posee las características de no tener etapas formales de acabado, el proceso de fabricación puede ahorrar tiempo, así como el coste de las operaciones de fabricación. Las piezas de Zamak 5 tienen un aspecto agradable porque los diseñadores pueden pintarlas o cromarlas a su gusto.
La sencilla capacidad de acabado del Zamak 5 lo ha hecho idóneo para aplicaciones en productos de decoración del hogar, detalles de mobiliario doméstico y componentes de iluminación decorativa. Las piezas de Zamak 5 resisten los efectos del deslustre gracias a su efecto duradero.
3. Transformados en diferentes productos finales
Zamak 5 tiene una naturaleza superior para el trabajo de producción. El hecho de que la aleación sea maleable por naturaleza, porque el zinc es dúctil, permite darle forma fácilmente para diferentes operaciones de trabajo durante la producción. Zamak 5 puede trabajar fácilmente con diferentes métodos de producción, como fundición y doblado y mecanizado, y remachado, para satisfacer los requisitos de fabricación.
El Zamak 5 posee características de fácil procesamiento, lo que lo convierte en un accesorio vital para diferentes industrias que se han beneficiado de la reducción de los gastos de fabricación y del mantenimiento de un proceso de producción sencillo. Al ser la opción preferida para ensamblar productos cerrados y componentes de asas que han sido fundidos, el proceso de montaje de las piezas de Zamak 5 resulta menos laborioso.
4. Fabricación rentable
El Zamak 5 es un material que pone a disposición de los fabricantes un precio excepcionalmente asequible. El Zamak 5 es tan económico que resulta más barato que otras aleaciones y muy rentable cuando se funde. Su razonable estructura de costes, sin embargo, invita a los fabricantes a alcanzar niveles superiores de rentabilidad, y sus propiedades superiores atraen a los fabricantes.
El zamak 5 tiene un gran potencial para ser reciclado, y eso sitúa la capacidad de reciclarlo como un factor importante para reducir los costes de fabricación a largo plazo. Los artículos de Zamak 5 son reutilizables y conducen a la producción de chatarra que se recuperará, sobre la base de ahorrar costes y minimizar los residuos debidos a ella.
5. Ciclo de producción respetuoso con el medio ambiente
La producción de Zamak 5 es muy respetuosa con el medio ambiente. El zamak 5 no supone una gran amenaza para el medio ambiente, ya que utiliza un procedimiento de fabricación diferente al de los procedimientos peligrosos de algunos metales. La fabricación de la aleación no presenta contaminación nociva porque no se forman subproductos. En cuanto a la legislación medioambiental, el zamak 5 es una buena opción, y además proporciona a la empresa un método respetuoso con el medio ambiente para cumplir sus propias normativas.
Limitaciones de Zamak 5
Aunque el Zamak 5 tiene muchos puntos beneficiosos, en el proceso de selección hay que tener en cuenta primero sus limitaciones fijas.
Escasa resistencia a la humedad
El contacto de Zamak 5 con condiciones húmedas formará oxidación en su superficie porque demuestra una débil resistencia a la humedad. Los fabricantes de productos de Zamak 5 deben prever medidas de protección contra la humedad excesiva y, en caso contrario, recubrimientos protectores adicionales contra su descomposición.
Resistencia limitada a altas temperaturas
La capacidad de resistencia térmica de Zamak 5 se sitúa en un nivel moderado. Zamak 5 no debe utilizarse para aplicaciones en las que la exposición a la temperatura supere los 80 °C debido a una caída muy elevada de la resistencia a la tracción, lo que aumentará el riesgo de rotura o flexión.
No es ideal para aplicaciones ligeras
La pieza obtenida utilizando Zamak 5 es más pesada, ya que tiene mayor densidad que las aleaciones no ferrosas competidoras. El elemento ligero para este tipo de aplicaciones requiere entonces que se consideren otros materiales de aleación, ya que determinan los requisitos.
Problemas de resistencia a la corrosión con otros metales
Cuando se combina zinc o estaño con plomo para fabricar este material, la durabilidad del Zamak 5 se ve comprometida debido a la menor resistencia a la corrosión de la aleación resultante. En el uso particular, es necesario prestar especial atención a la combinación de materiales cuando se utiliza Zamak 5.
Propiedades de impacto a bajas temperaturas
En ambientes fríos, la fuerza de efecto del Zamak 5 se ve afectada en los puntos donde la temperatura desciende a niveles extremadamente bajos, por lo que no es funcional en condiciones de frío.
¿Dónde utilizar Zamak 5?
El Zamak 5 se utiliza ampliamente en muchos sectores, incluida la industria de la fundición a presión. El Zamak 5 destaca entre los dos extremos del espectro de producción en la fabricación de elementos de automoción y artículos decorativos. Algunos usos comunes son:
Sanitarios: El zamak 5 tiene la capacidad de protegerse contra la corrosión, por lo que se utiliza ampliamente en la fabricación de accesorios de baño como grifos y manillas.
Componentes de armas de fuego: Esta aleación es muy duradera y resistente, por lo que funciona muy bien en la fabricación de piezas de armas de fuego.
Juguetes y artículos de colección: Sin embargo, debido a su sencillo proceso de moldeo y a su excelente acabado superficial, el Zamak 5 es una opción popular para la fundición a presión de juguetes y artículos en miniatura, así como de productos de colección.
Fabricación de cerraduras y herrajes: El Zamak 5 predomina en la industria manufacturera para producir cerraduras con manillas, pomos de cerraduras y otras piezas de ferretería gracias a las buenas propiedades de resistencia y la facilidad de mecanizado de esta aleación.
Electrónica y electrodomésticos: El Zamak 5 tiene aspectos de durabilidad y cualidades atractivas, y artículos domésticos como batidoras y grapadoras y ventiladores de techo, así como otros electrodomésticos, aprecian el Zamak 5.
Propiedades mecánicas de la aleación Zamak 5
La aleación Zamak 5 está determinada por sus cualidades estructurales para funcionar bien o mal en diversas operaciones industriales. La aleación Zamak 5 tiene resistencia a la tracción, junto con alargamiento y dureza y resistencia a la corrosión. Estos valores cambian cuantitativamente cuando el proceso de fundición es diferente y se modifican la composición de la aleación metálica y la velocidad de enfriamiento.
Resistencia a la tracción: La aleación Zamak 5 conserva una resistencia a la tracción de 280-300 MPa, superior a la de otros materiales de aleación a base de zinc.
Límite elástico: La aleación Zamak 5 tiene una excelente resistencia a la deformación por tensión, ya que el límite elástico es de aproximadamente 230 MPa.
Elongación: La aleación Zamak 5 presenta un círculo de ductilidad medio (entre 3 y 6%) en su índice de alargamiento. Sus propiedades permiten pequeñas deformaciones que no van acompañadas de grietas, de ahí que sea adecuada para su uso en sistemas flexibles.
Dureza: El valor de dureza del Zamak 5 es de 90-120 HB (dureza Brinell), lo que hace que el material sea aplicable a aplicaciones que requieren una resistencia al desgaste relativamente baja.
Resistencia a la corrosión: Incluso a expensas de un contenido medio de humedad y de sustancias químicas estándar, la aleación Zamak 5 resistirá muy bien la corrosión. Zamak 5 funciona bien como material para componentes de exterior y automoción.
Aplicaciones de la aleación Zamak 5
El Zamak 5 se elige para una amplia gama de industrias porque combina sus buenas características de fundición con fuertes propiedades mecánicas. Sus aplicaciones incluyen:
Industria del automóvil: Como material esencial para fabricar componentes funcionales finos para motores de automoción y carcasas de molduras de vehículos, carcasas de dispositivos electrónicos, el Zamak 5 es un material clave.
Herrajes y accesorios: Tales materiales, como el Zamak 5, han estado al servicio del sector de la automoción, ya que mantienen unidas una gran resistencia y durabilidad, y su acabado es agradable.
Bienes de consumo: La aleación Zamak 5 es el material que utilizan los productores por su resistencia favorable y a la corrosión, y por su moldeabilidad para fabricar juguetes y conectores eléctricos, así como electrodomésticos.
Electrónica: El zamak 5 conduce bien la electricidad, se amolda bien a formas complejas y se utiliza para fabricar carcasas de dispositivos electrónicos.
Ventajas de la aleación Zamak 5
El Zamak 5 ofrece varias ventajas importantes que pueden convertirlo en la aleación preferida de los fabricantes.
Rentabilidad: El coste del Zamak 5 es una opción excelente, ya que proporciona una buena durabilidad y una fundición fácil a un precio más sencillo y barato que otras alternativas metálicas.
Versatilidad: La razón por la que se elige Zamak 5 para fabricar piezas complejas y precisas es la facilidad para producir formas complicadas, sin acomodación.
Calidad de acabado: Dado que el Zamak 5 produce excelentes superficies lisas, es necesario un trabajo de acabado de alta calidad, para que los fabricantes puedan obtener una mejor calidad de acabado.
Alta relación resistencia-peso: La aleación Zamak 5 es buena para la industria de la automoción y otros sectores similares, ya que esta aleación ofrece una gran resistencia y una gran independencia de peso.
Retos y consideraciones al utilizar Zamak 5
A pesar de que la aleación Zamak 5 presenta numerosas ventajas, hay varios puntos críticos en lo que se refiere a su uso.
Sensibilidad a la temperatura: Sin embargo, el Zamak 5 tiene un comportamiento térmicamente sensible, ya que carece de degradación de propiedades en presencia de un aumento de temperatura por debajo de 250°C (482°F). La vida útil de las piezas de Zamak 5 debe limitarse a entornos en los que la temperatura sea lo suficientemente baja como para no superar este umbral.
Limitaciones de mecanizado: Aunque el proceso de fundición de Zamak 5 es sencillo, el material crea problemas con las operaciones de maquinaria que implican métodos agresivos, ya que el material tiende a presentar mecanismos de gripado y desgaste. Para lograr resultados satisfactorios, los técnicos necesitan herramientas adecuadas y las técnicas correctas.
Impacto medioambiental: Evaluación de La buena resistencia a la corrosión del Zamak 5 también debe tenerse en cuenta en el impacto medioambiental que provoca en los procesos de producción y ciclo. El Zamak 5 puede mejorarse aún más mediante el reciclado y la reducción de residuos en las emisiones de fundición, y la industria lo está haciendo tanto para aumentar la sostenibilidad de la aleación de zinc.
Servicios de fundición a presión de Zamak 5 en CNM TECH
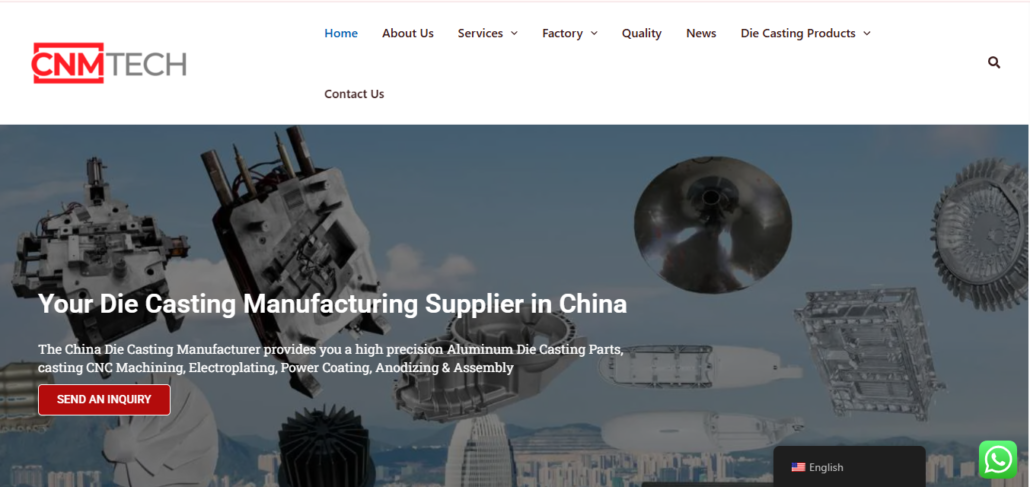
Ofrecemos excelentes soluciones de fundición a presión de Zamak 5 bajo la cartera de CNM TECH para diversas necesidades de la industria, desde la automovilística y aeroespacial hasta la producción de productos de consumo. Somos una organización especializada en una profunda experiencia y modernos sistemas de fundición a presión que nos permiten desarrollar piezas que ofrecen un excelente rendimiento, capacidad y mantenimiento.
Aplicando nuestro moderno método de fundición a presión, se suministrarán productos Zamak 5 con buenas dimensiones, excelente calidad superficial y tiempo de fabricación sistemático para una cantidad de producción económica. En pocas palabras, con CNM TECH, los clientes pueden dictar sus especificaciones al material de fundición a presión con precisión y obtener plazos de entrega ajustados.
Eche un vistazo a todas nuestras ofertas de Zamak 5 que ofrecen capacidades de creación de prototipos y fabricación a gran escala. En www.thediecasting.com, podrá descubrir cómo las soluciones Zamak 5 de nuestra empresa aumentan el rendimiento de la vida útil del producto.
Debe elegir los servicios de fundición a presión de Zamak 5 de CNM TECH, ya que son precisos.
Conclusión
Zamak 5 es la aleación de fundición más utilizada en las industrias para la fabricación de piezas que requieren precisión, especialmente en automoción, ferretería y electrónica, que tienen la capacidad de bajos costes de producción y eficacia. La mezcla de zinc, aluminio, cobre y magnesio de la aleación de zinc 5 hace que sea un material fuerte con grandes características mecánicas, resistencia y defensa contra la corrosión, y la capacidad de fundición. Las técnicas de fabricación mediante fundición de Zamak 5, si se enfocan adecuadamente, con los controles de temperatura y presión, producen componentes de gran calidad con imperfecciones muy mínimas siempre que se realizan. No obstante, el zamak 5 tiene un punto de fusión bajo y unas características de fluidez que lo hacen adecuado para diseños muy sofisticados, razón por la que está muy extendido para aplicaciones industriales.
Preguntas frecuentes
1. ¿Cuáles son las características esenciales del proceso de fundición a presión en CNM TECH que conducen a Zamak 5?
A: La aleación de zinc de alto rendimiento tiene descripciones como: excelente resistencia y estabilidad dimensional, y extraordinaria protección contra la corrosión. Una de ellas es Zamak 5. El Zamak 5 presenta una excepcional capacidad de fundición, gracias a la cual pueden fabricarse componentes extremadamente detallados e intrincados con un mecanizado mínimo. CNM TECH utiliza Zamak 5 para fabricar componentes fiables y rentables que pueden utilizarse en aplicaciones de automoción, electrónica de consumo y ferretería.
2. ¿Puede CNM TECH fabricar determinadas piezas de Zamak 5 según los requisitos de mi proyecto?
A: Absolutamente. Como empresa especializada, CNM TECH ofrece una solución individualizada de fundición a presión de Zamak 5. La empresa fabrica moldes con los clientes, aquellas empresas que necesitan prototipos de bajo volumen, así como piezas de gran volumen que deben ser exactamente como se especifica. El trabajo dedicado de nuestros empleados en los procesos de producción nos permite ofrecer resultados precisos y un rendimiento fiable.
3. ¿Cuáles son los posibles tipos de tratamientos para completar los productos de fundición Zamak 5?
A: En CNM TECH, los múltiples acabados disponibles para las piezas de Zamak 5 incluyen la galvanoplastia en combinación con el recubrimiento en polvo y el cromado y la pintura y el pulido. Mediante el uso de las técnicas de acabado, se puede mejorar el aspecto y la resistencia al desgaste y la protección contra la corrosión de piezas que pueden ser funcionales o decorativas.