Литье под высоким давлением (HPDC) - один из наиболее часто используемых процессов литья металлов в современном производстве. Производители выбирают HPDC, потому что он позволяет изготавливать сложные металлические детали, обеспечивающие высокую точность и скорость производства, превосходную точность размеров и гладкую отделку. HPDC позволяет автомобильной и аэрокосмической промышленности, производству электронных компонентов и потребительских товаров изготавливать легкие прочные детали для таких применений, как двигатели и корпуса, конструктивные элементы и механические узлы. Производственный процесс литья под высоким давлением сопряжен с многочисленными рисками, которые приводят к возникновению существенных дефектов, снижающих качество продукции, сокращающих срок службы и ухудшающих эксплуатационные характеристики. Различные дефекты образуются из-за неправильной конструкции пресс-формы, турбулентного потока расплавленного металла, улавливаемых газов, несоответствующей скорости охлаждения и теплового напряжения в процессе производства. Технология HPDC сталкивается с семью основными дефектами, к которым относятся пористость, холодные замыкания, дефекты усадки, образование вспышек, дефекты поверхности, неправильные пробеги, эрозия матрицы и пайка. Эти виды производственных дефектов приводят к снижению прочности материала, неравномерным размерам и нежелательным визуальным эффектам, которые могут спровоцировать поломку компонентов. Производители борются с производственными проблемами с помощью оптимизации параметров обработки и более совершенных методов растачивания, а также систем контролируемой температуры и процедур литья под вакуумом. Мониторинг в режиме реального времени и программное обеспечение для моделирования являются передовыми методами контроля качества, повышающими эффективность и надежность процесса литья под давлением.
В данной статье представлен всесторонний анализ стандартных производственных проблем при работе под высоким давлением литье под давлением технологии с объяснением основных причин и стратегий решения для уменьшения этих дефектов. Только понимая эти проблемы и применяя передовые методы, производители могут повысить качество, долговечность и, конечно, производительность своих литых компонентов и одновременно сократить количество отходов и производственные затраты. Знание этих производственных дефектов поможет инженерам, менеджерам по производству и специалистам по контролю качества оптимизировать свои процессы для достижения наилучших результатов литья под давлением.
1. Пористость
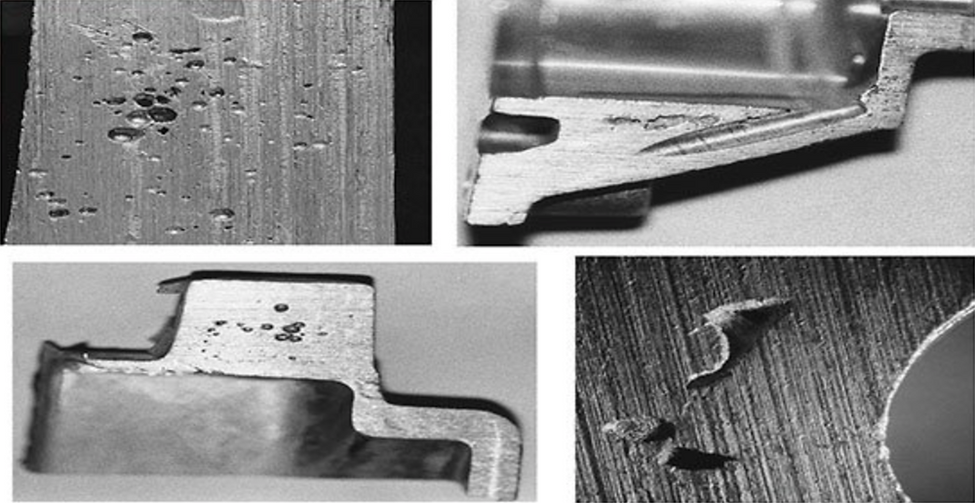
Пористость - это небольшие отверстия или газовые включения в металлической матрице, которые влияют на механические свойства, снижая прочность, в том числе позволяя воздуху и газам проходить через структуру, и приводя к видимым дефектам поверхности литых изделий.
Причины:
- Газообразное содержимое, присутствующее в материалах перед отливкой.
- Чрезмерная турбулентность в потоке расплавленного металла.
- Плохая вентиляция и неправильная конструкция формы.
- Быстрое затвердевание, вызывающее усадочную пористость.
- Загрязнение расплавленного металла.
- Недостаточное давление, из-за которого металл течет неравномерно.
Профилактика и решения:
- Обеспечьте надлежащее отведение газов с помощью задвижек и вентиляционных отверстий.
- Замедлите скорость впрыска, чтобы повысить гладкость металла, поступающего в полость.
- Проблема захвата воздуха должна быть решена с помощью технологии литья под вакуумом.
- Убедитесь, что расплавленный металл достаточно дегазирован перед впрыском.
- Контролируйте скорость охлаждения для преодоления проблемы трещин и образования других дефектов затвердевания.
- Часто проверяйте и очищайте поверхности штампов, чтобы уменьшить вероятность появления пористости из-за загрязнений.
2. Холодное закрытие
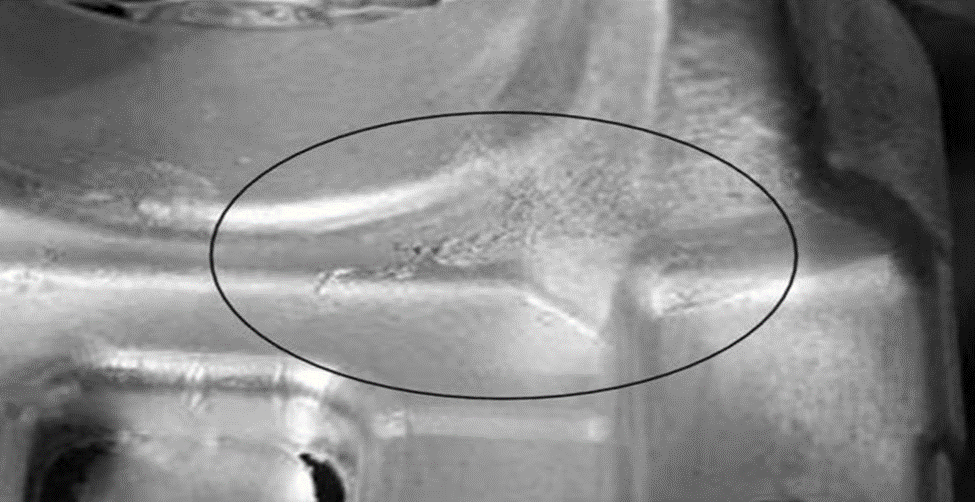
Холодный зазор образуется, когда два потока расплавленного металла не сплавляются должным образом и образуют слабые участки сцепления или видимые швы в отливке. Этот дефект не только снижает механическую прочность, но и повышает риск излома, а также негативно влияет на долговечность и внешний вид детали.
Причины:
- Низкая температура расплавленного металла.
- Отмечается низкая скорость впрыска, что обычно приводит к преждевременному застыванию.
- Плохая конструкция пресс-формы с недостаточными проточными каналами.
- Это может привести к чрезмерному окислению, которое образует поверхностные пленки, препятствующие правильному сплавлению.
- Непостоянный поток металла из-за плохой конструкции литниковой системы.
Профилактика и решения:
- Кроме того, необходимо поддерживать наиболее оптимальную температуру заливки металла, чтобы обеспечить надлежащую текучесть.
- Увеличьте скорость впрыска, чтобы завершить наполнение и сделать его цельным.
- Устраните ненужные препятствия для потока в конструкции пресс-формы, чтобы металл мог двигаться без затруднений.
- Выявление и решение проблем с потоком до начала производства с помощью инструментов термического анализа.
- Во избежание задержки воздуха, которая часто усугубляет дефекты холодного затвора, следует применять правильные методы вентиляции.
3. Дефекты усадки
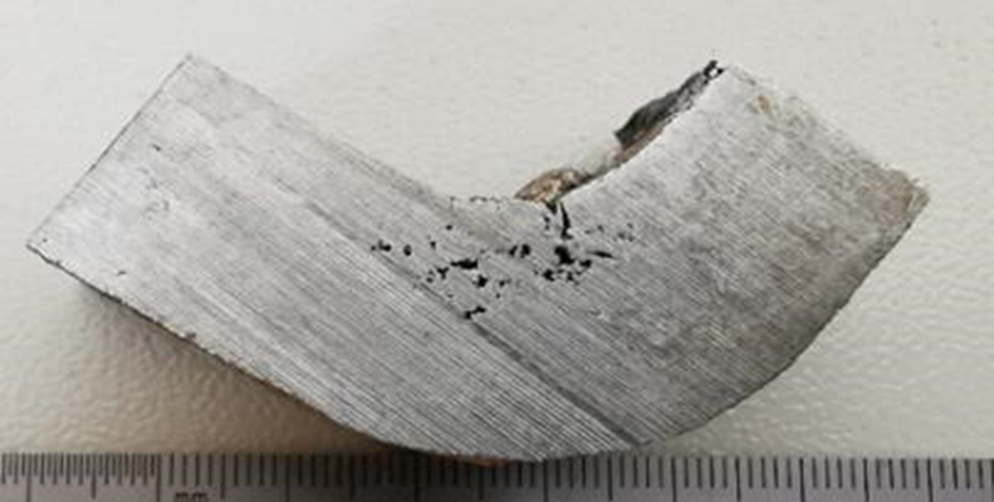
Усадочные дефекты возникают из-за усадки металла при охлаждении, что приводит к образованию внутренних пустот или полостей, которые нарушают структурную целостность отливки. В результате эти дефекты снижают механическую прочность конечного продукта, вызывают потенциальное разрушение под нагрузкой и приводят к ухудшению качества поверхности, что сказывается как на функциональности, так и на эстетике конечных изделий.
Причины:
- Недостаточная подача металла во время затвердевания
- Неравномерная скорость охлаждения из-за неправильной конструкции матрицы
- Высокая усадка металла из-за состава сплава
- Быстрое охлаждение, вызывающее локальное сокращение
- Недостаточное давление на этапе затвердевания
Профилактика и решения:
- Измените форму, чтобы обеспечить равномерное охлаждение и правильную подачу расплавленного металла.
- Используйте сплавы с меньшей склонностью к усадке и лучшими свойствами затвердевания.
- Он используется для оптимизации параметров давления во время затвердевания, чтобы заполнить и минимизировать усадочные пустоты.
- Используйте методы контролируемого охлаждения для достижения баланса в скорости затвердевания и снижения теплового напряжения.
- Внедрить средства мониторинга и моделирования в реальном времени для прогнозирования и предотвращения дефектов усадки.
4. Формирование вспышки

Избыточные тонкие слои металла, образующиеся на линии раздела или в зазоре штампа в результате вытекания металла под высоким давлением, называются вспышкой. Хотя вспышки можно обрезать после литья, избыточные вспышки приводят к увеличению отходов материала, износу инструмента и сопутствующим производственным затратам и, таким образом, снижают общую эффективность процесса литья под давлением.
Причины:
- Избыточное давление впрыска приводит к тому, что расплавленный металл протискивается в зазоры штампа.
- Изношенный штамп или неправильная фиксация штампа, допускающая утечки.
- При недостаточной силе зажима, что приводит к разъединению матрицы во время впрыска.
- Они будут плохо лежать с зазорами для утечки металла.
- Нечеткий контроль расхода металла при смазке штампа
Профилактика и решения:
- Во избежание расслоения штампа и образования вспышек необходимо поддерживать надлежащее усилие зажима.
- Регулярно проверяйте и заменяйте изношенные штампы, чтобы добиться надлежащего уплотнения.
- Обеспечьте оптимальные настройки давления, чтобы наполнение происходило с минимальной вспышкой.
- Для предотвращения нежелательных зазоров и утечки металла необходимо улучшить выравнивание матрицы.
- Применяйте точные методы смазки штампа, чтобы контролировать поток металла и уменьшить его чрезмерное вытекание.
5. Проверка поверхностных дефектов (пузыри, трещины и морщины)

Разнообразные дефекты поверхности, пузыри, трещины и морщины, ухудшающие внешний вид и механическую прочность отливки, необходимо предотвращать и устранять. Они вызывают дефекты сварного шва, которые снижают долговечность изделия, увеличивают процент брака и делают изделие плохо держащимся после обработки отливки, такой как покраска или покрытие.
Причины:
- Воздух, попавший в жидкий пластик при заливке.
- Кроме того, из-за неравномерной скорости охлаждения возникают тепловые напряжения и неровности поверхности.
- Перегрев или плохо контролируемая температура во время застывания.
- Или металлические примеси или включения, которые могут повлиять на поверхность отливки
- Плохая смазка штампа вызывала неравномерную подачу металла и дефекты поверхности.
Профилактика и решения:
- Правильная дегазация расплавленного металла во избежание попадания газов перед заливкой.
- Контролируйте затвердевание и избегайте термического напряжения, используя методы равномерного охлаждения.
- Контроль температуры матрицы должен быть оптимизирован, чтобы предотвратить перегрев и неравномерное охлаждение.
- Создание строгого контроля качества, который позволит выявить все примеси перед отливкой.
- Нанесение покрытий и смазок на штамп с учетом качества поверхности и уменьшения дефектов.
6. Включения и загрязнения
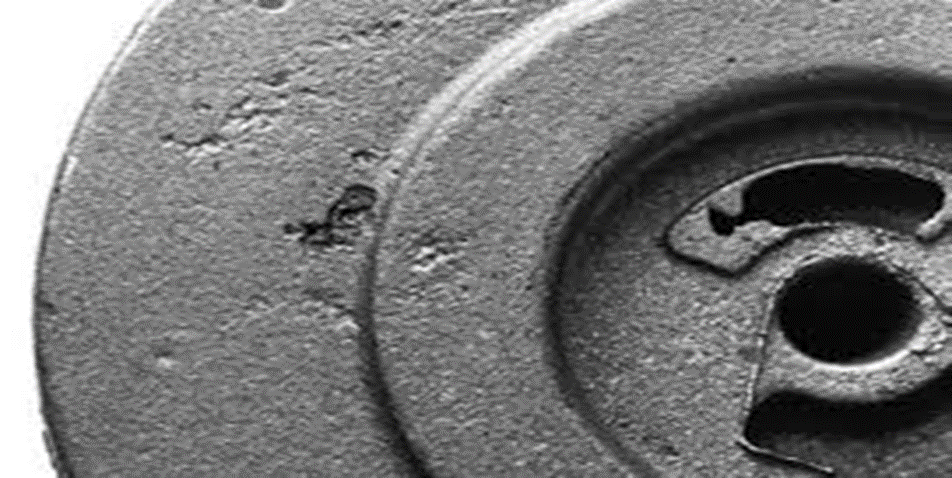
Нежелательные инородные частицы, такие как шлак, оксидные пленки, грязь или другие примеси, которые попадают в конечную отливку, создают плохие механические свойства, слабую структурную целостность и дефекты поверхности и называются включениями. Присутствие этих загрязнений может снизить производительность и долговечность литых деталей, поэтому они не подходят для высокоточных применений.
Причины:
- Например, загрязненное сырье состоит из нежелательных примесей.
- Посторонние частицы в расплавленном металле не могут быть хорошо отфильтрованы в результате
- Из-за длительного воздействия воздуха при плавке или заливке металла
- Включает в себя неэффективные методы обработки металла, которые, в свою очередь, приводят к повышенному образованию шлака
- Недостаточная смазка штампа включает в себя попадание постороннего вещества в расплавленный металл.
Профилактика и решения:
- Качественное сырье должно быть правильно очищено и не содержать загрязнений.
- Установите эффективные системы фильтрации для удаления шлака, оксидов и других примесей из расплавленного металла перед впрыском.
- Обеспечьте контролируемое обращение с расплавленным металлом и, где это возможно, используйте экранирование инертным газом для ограничения окисления.
- Регулярно очищайте и обслуживайте оборудование для литья, чтобы предотвратить загрязнение остатками материала.
- Используйте надлежащую смазку для пресс-формы, чтобы в ее полости не скапливались посторонние материалы.
7. Ошибки и неполное заполнение
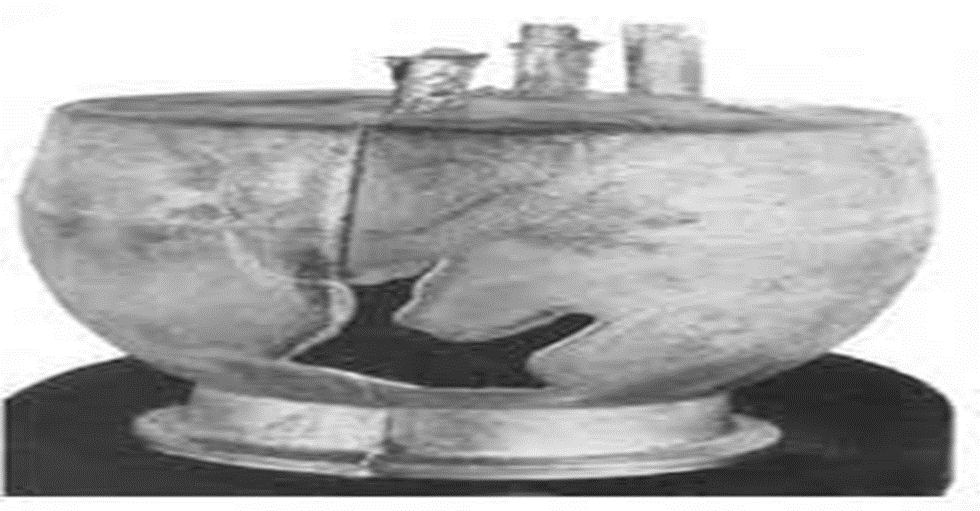
Неправильный прогон происходит при коротком заполнении полости пресс-формы, что приводит к отсутствию секций, тонким стенкам и слабым местам в конечном компоненте. Это негативно сказывается на структурной целостности и функциональности детали и, таким образом, не подходит для применения в производстве.
Причины:
- При низкой скорости впрыска или давлении, не полностью покрывая пресс-форму
- Холодные поверхности штампа предотвращают протекание металла и преждевременное затвердевание
- Вызывает недостаточный объем расплавленного металла, что приводит к недостаточному заполнению полости
- Из-за плохой конструкции литников и бегунов, которые вызывают неравномерное распределение расплавленного металла
- При чрезмерной турбулентности образуются воздушные карманы, блокирующие поток металла
Профилактика и решения:
- Повысьте температуру металла, чтобы сделать его текучим и избежать преждевременного затвердевания.
- Кроме того, заполнение полости должно быть оптимизировано за счет правильной настройки давления и скорости впрыска.
- Поддерживайте надлежащую рабочую температуру штампов и не допускайте их преждевременного охлаждения.
- Улучшенная конструкция воротка и бегунка способствует плавному и равномерному распределению металла.
- Перед началом производства смоделируйте поток металла и вероятность пропусков с помощью программного обеспечения для моделирования.
8. Эрозия и износ штампа
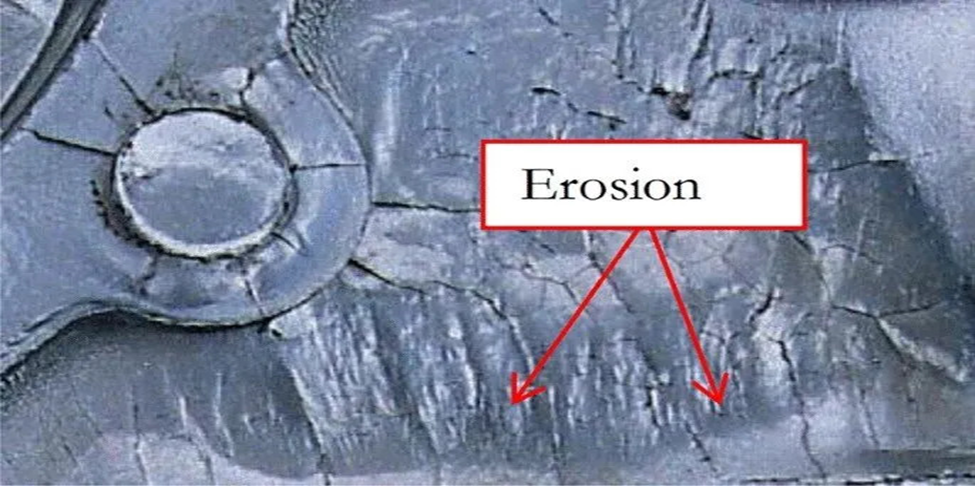
Износ расплавленных эрозионных штампов - это потеря поверхностей формы из-за того, что высокоскоростной металл постоянно изнашивает поверхности деталей формы до достижения требуемых размеров, что приводит к ухудшению качества поверхности и сокращению срока службы литейной оснастки. При возникновении этого дефекта часто требуется замена штампа, что приводит к увеличению производственных затрат и снижению качества литья.
Причины:
- Кроме того, он подвергается многократному воздействию высокотемпературного расплавленного металла, что приводит к постепенному износу.
- Относительно низкое качество материалов штампа с низкой устойчивостью к термическим и механическим нагрузкам
- Чрезмерное термоциклирование может привести к растрескиванию материала из-за усталости.
- Это приводит к разрушению материала матрицы под высоким давлением.
- Мало смазки? Больше трения и больше износа.
Профилактика и решения:
- Один из них - использование высококачественных термостойких материалов для штампов, которые отличаются повышенной прочностью.
- Для продления срока службы штампа можно наносить защитные поверхностные покрытия, например, азотирование или керамические покрытия.
- Необходимо внедрить методы контролируемого охлаждения для снижения теплового напряжения и уменьшения преждевременного износа.
- Для достижения баланса между скоростью и давлением с минимальной нагрузкой на штамп.
- Регулярно осматривайте и обслуживайте штампы, чтобы как можно скорее обнаружить и устранить эрозию.
9. Горячее растрескивание
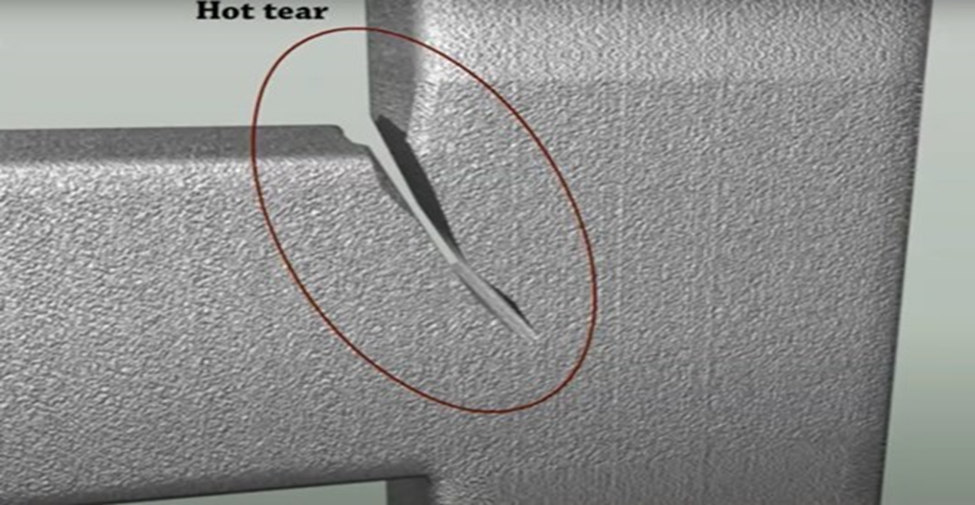
Трещины, возникающие в полутвердом состоянии металла из-за высокого термического напряжения и чрезмерной усадки, называются горячими трещинами. Эти трещины ухудшают механическую целостность отливки, то есть увеличивают вероятность разрушения отливки в том месте, где имеются трещины, под действием напряжения или нагрузки.
Причины:
- Ненадежная скорость охлаждения пресс-формы, приводящая к образованию точек напряжения в определенных местах
- Он обладает высокой восприимчивостью к термическим напряжениям и растрескиванию в составе сплава.
- Также вызывает чрезмерное остаточное напряжение, образующееся при быстром затвердевании и ограничивающее сжатие металла
- Если конструкция формы некачественная, то будут наблюдаться перепады температуры по всей отливке.
- Давление во время затвердевания было слишком мало, чтобы предотвратить распространение трещин.
Профилактика и решения:
- Также необходимо оптимизировать скорость охлаждения для равномерного затвердевания и минимизации теплового напряжения.
- Повышение трещиностойкости сплавов за счет использования сплавов с лучшей зерновой структурой.
- Использование методов снятия напряжения после литья, то есть контролируемой термообработки.
- Создавайте формы с меньшим перепадом температур.
- Обеспечьте надлежащее давление во время застывания металла, чтобы он текла и не образовывались трещины.
10. Пайка
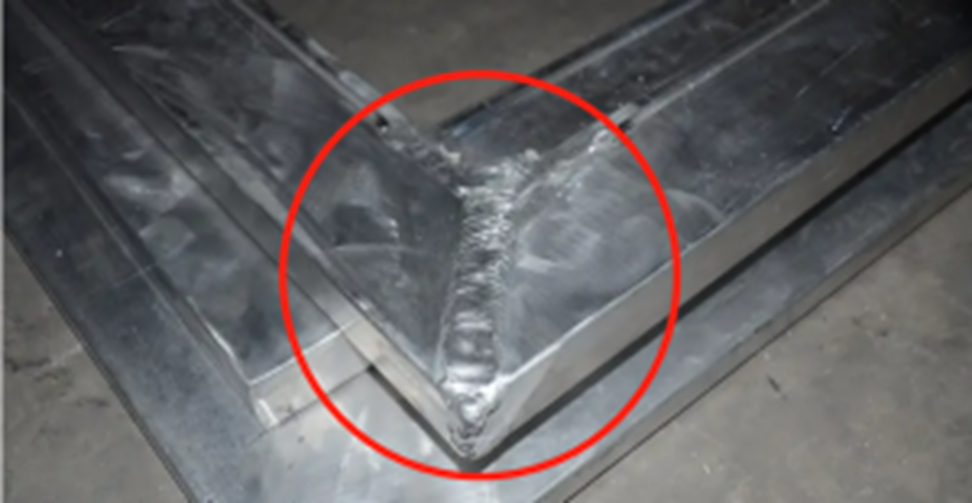
Расплавленный металл прилипает к поверхности формы, которую трудно удалить при литье, что приводит к дефектам поверхности, износу формы, а также длительным простоям производства. Неточности в размерах и плохая обработка поверхности также являются следствием этого дефекта, поскольку приводят к ухудшению качества конечного продукта.
Причины:
- Увеличение адгезии металлов в сплаве за счет высокого содержания в нем алюминия
- Слишком высокая температура штампа, чтобы металл сцеплялся с поверхностью штампа
- Недостаточная защита от заедания из-за плохой смазки штампа
- Недостаточное охлаждение приводит к тому, что расплавленный металл слишком долго находится в контакте со штампом - накипь или повреждение верхних поверхностей штампа, которые способствуют прилипанию металла.
Профилактика и решения:
- Для предотвращения налипания металла всегда применяются высококачественные смазочные материалы для штампов.
- Это позволяет регулировать температуру штампа в оптимальном диапазоне, если горячая адгезия слишком сильна.
- Уменьшите адгезию металла, используя подходящие покрытия штампа, например, керамические или нитридные слои.
- Для сокращения времени контакта металла с матрицей и повышения эффективности системы охлаждения.
- Регулярно проверяйте и полируйте поверхности штампов, чтобы добиться гладкой поверхности без адгезии.
Заключение
Высокое давление литьё под давлением это мощный производственный процесс, позволяющий создавать сложные металлические детали с высокой точностью и максимальной эффективностью. Однако при этом возникают различные виды дефектов, связанные с неправильными параметрами процесса, проблемами с материалом и/или недостатками конструкции пресс-формы. Понимая эти обычные производственные дефекты, производители могут принять превентивные меры, например, оптимальное управление технологическим процессом, правильно подобранный материал и т. д.
Компания может повысить качество продукции, снизить производственные затраты и добиться более высокой эффективности производства при литье под давлением, уделяя особое внимание постоянному совершенствованию процессов, а также стратегиям предотвращения дефектов.
Часто задаваемые вопросы (FAQ)
1. Каковы основные причины возникновения дефектов при литье под высоким давлением?
Основными причинами дефектов при литье под высоким давлением являются неправильная конструкция формы, плохая текучесть металла, задерживающийся газ, высокие термические напряжения, неравномерное охлаждение и загрязненное сырье. Эти дефекты можно уменьшить с помощью оптимизации параметров процесса и применения мер контроля качества.
2. Какую роль играет пористость в производительности литых деталей?
Наличие пористости ослабляет структурную целостность литых компонентов, снижая прочность и вызывая утечки воздуха в герметичных компонентах, а также дефекты анестезии. Пористость можно свести к минимуму с помощью правильной дегазации, оптимизированных литниковых систем и литья под вакуумом.
3. Как можно избежать холодных замыканий при литье под давлением?
Правильная температура заливки металла, более высокие скорости впрыска, оптимизированная конструкция пресс-формы для плавного течения металла и применение инструментов термического анализа для выявления возможных проблем с течением могут помочь предотвратить холодные остановки.
4. Эрозия штампа является важной проблемой при литье под высоким давлением, потому что?
Многократное воздействие высокотемпературного расплавленного металла на формы приводит к эрозии штампа, что сокращает срок службы форм и снижает точность литых деталей. Срок службы пресс-форм можно продлить за счет использования высококачественных материалов для пресс-форм, применения защитных покрытий и контролируемого охлаждения пресс-форм.
5. Что делает качество и последовательность литых изделий лучше?
Строгий контроль качества, оптимизация технологических параметров, контроль температуры в штампе, использование высококачественных сплавов, проверка штампов и оборудования периодически проводятся для постоянного улучшения качества литых изделий.