There are very few places one can go to learn about welding cast aluminum, and the skill set needed to do so is highly specialized. However, cast aluminum is a material created by pouring molten aluminum into a mold, which results in a porous material with impurities. This does not occur with standard aluminum alloys. Because of these characteristics, welding is more difficult, and preparing carefully, keeping the heat precisely in check, and using the appropriate techniques is necessary to produce strong, robust welds. Oxidation is one of the greatest hurdles when welding cast aluminum. This thin oxide layer, formed when exposed to air is much thicker than what naturally forms on aluminum, and it melts at a much higher temperature than aluminum itself, making fusion difficult. Furthermore, the presence of impurities and trapped gases in the cast aluminum can result in porosity, which provides weak welds if not properly cleaned and preheated.
TIG (Tungsten Inert Gas) is the method of choice for precision and cleanliness, while MIG (Metal Inert Gas) is useful for speed and thicker material. To obtain a strong and defect-free weld, it is necessary to use the correct filler metal (such as 4045, 5356, or 4047) and shielding gas combination (of pure argon or argon-helium mixtures). Good preparation includes adequately cleaning and preheating as far as possible to minimize cracking, porosity and lack of fusion. Endurance and life of the welded joints is further improved by post-weld treatments like stress relief, grinding and corrosion protection after welding.
While the majority of cast aluminum welders are welded steel, welders can successfully work with cast aluminum using the right techniques, tools, and attention to detail so long as lightweight, high strength components are required in industries. This is a masterable process that leads to further development of aluminum welding applications and to a reliable and predictable performance of aluminum structures in critical environments.
Understanding Cast Aluminum
However, before proceeding with the welding techniques needed for cast aluminum, it is crucial to have a firm understanding of what constitutes cast aluminum and what makes it unique from other metals. Cast aluminum differs from wrought aluminum, which is mechanically shaped by using rolling or extruding, in that cast aluminum can be formed in complex shapes of high precision by melting aluminum and pouring this molten form into a mold. The unique internal structure so produced, usually characterized by porosity, impurities and varying alloy composition, has an important effect on weldability.
To be able to weld cast aluminum successfully, one should know its chemical and physical properties, its pros and cons as well as the different types of cast aluminium alloys from various industries. These factors will be taken into consideration for the determining the necessary welding method, selection of filler material and preweld preparation techniques to make strong and defect free welds.
Cast aluminum properties: What makes a cast different?
Another important consideration that use of cast aluminum has several properties that make it light weight, anti- corrosive and very flexible. However, the same properties also pose some difficulties when welding is being done, provided that proper measures are not taken.
1. Porosity: The Hidden Challenge
Possibly one of the biggest concerns about welding cast aluminum is porosity; it is known as the small bubbles of gas that get trapped in the metal when it is being cast. These eight are resulted from the entrapment of gases such as hydrogen, formation of small pores as a result of shrinkage during cooling of the aluminum metal and impurities.
🔹 How Porosity Affects Welding
- It weakens the mechanical strength, and the weld is liable to crack.
- Contributes to weld contamination and therefore undermines the strength of the joints that have been made.
- Secures gases in the weld area, once forming surface irregularities.
🔹 How to Minimize Porosity During Welding
- Surface preparation of the metal through cleaning should be proper before welding can begin.
- Grasp the aluminum foil and warm it to reduce any thermal stress on the aluminum and to also to minimise the formation of air bubbles.
- This should be done by using high-quality, inert gas of 100% Argon to avoid oxidation.
2. Oxidation: The Barrier to Clean Welds
It is an element that reacts with other elements particularly oxygen found in the space surrounding the metal. This oxidation generates a very thin but extremely hard skin of aluminum oxide (Al₂O₃) through which the further corrosion of aluminum is prevented. Nevertheless, oxide layer is a critical issue when welding since its melting temperature is around 3700°F (2037°C), which is much higher than that of aluminum, 1221°F (660°C).
Investigation on Why Oxidation is a Problem in Welding
- Is it instrumental to the formation of the long bond between the weld filler and base metal?
- This led to contamination in the weld pool and thus the provision of poor welds.
- It needs preparation before welding since it has an oxide layer.
🔹 Different Techniques of Removing and Controlling Oxidation
- Rinse the aluminum item with warm water, Afterward, you should use a stainless steel brush that should only be used for the cleaning of aluminum to scrub off the oxide layer.
- Wipe the surface with acetone or alcohol as a pre-welding cleaning process because oil floats on metals and grease sinks in.
- To cut through oxidation, it is recommended to make use of AC in TIG welding.
3. Heat Sensitivity: Managing Thermal Conductivity
Different from steel, aluminum has high thermal conductivity and it can easily absorb and emit heat. This has always been a problem in maintaining a standard welding temperature; this tends to cause the following:
- Incomplete fusion due to rapid heat loss.
- Three, deformation or distortions chiefly in thin aluminum parts.
- Burn-through, particularly in highly porous or thinner sections of cast aluminum.
🔹 How to Overcome Heat Sensitivity Challenges
- This is done to regulate heat flow in such a way that all parts of the material being used are as hot as the desired temperature.
- Be able to fine-tune the heat control system and inclined use of TIG welding.
- Lessening the amount of heat that is put on the weld area can be done in this way, and that is by using shorter weld passes.
Common Types of Cast Aluminum Alloys
Various types of cast aluminum alloys can be cast according to their chemical composition and mechanical properties. Here are a few of the advantages and disadvantages of each type, as well as applications where they would be most useful.
1. A356 Cast Aluminum: The High-Strength Alloy
Its composition: Mainly encompasses aluminum (Al), silicon (Si) and magnesium (Mg).
🔹 Key Features
- It has high tensile strength and is suited for structural applications.
- Excellent corrosion resistance, especially in humid environments.
- It is good weldability, although post-weld heat treatment might be required to regain strength.
🔹 Common Applications
- It is used in engine components, wheels and transmission cases in the automotive industry.
- Aerospace industry – Found in aircraft structural parts due to its strength-to-weight ratio.
- Medical devices – Used in surgical instruments and high-strength casings.
2. 319 Cast Aluminum: The Wear-Resistant Allo
Composition: Contains higher levels of silicon (Si) and copper (Cu) than A356.
🔹 Key Features
- Very good wear resistance for heavy-duty applications.
- It is more brittle and has a higher silicon content and therefore is more difficult to weld.
- It takes specialized filler materials (4047) to prevent cracking.
🔹 Common Applications
- Wear-resistant variants: automotive cylinder heads and engine blocks.
- Durability is needed in pumps and housings.
- Parts for industrial machinery are intended for the most severe, high mechanical stress conditions.
3. 535 Cast Aluminum: The Marine-Grade Alloy
Composition: Contains a high percentage of magnesium (Mg) for corrosion resistance.
🔹 Key Features
- Superior corrosion resistance, especially in saltwater environments.
- The weldability is good, but full pre-welding cleaning is required to avoid contamination.
- Easier to shape and repair than 319.
🔹 Common Applications
- High resistance to saltwater corrosion makes them good for boat hulls, marine engine parts and propellers.
- It is used for aircraft and aerospace parts which require strong and lightweight materials.
- Elements that pose a minimum threat to industrial components subjected to harsh chemical environments.
Why Understanding Cast Aluminum Matters for Welding
Starting with cast aluminum welding mastery is all about determining what cast aluminum is made of, its properties, and associated challenges. Therefore, as cast aluminum is used extensively in automotive, aerospace and marine engineering, welders require strategies for casting porosity, oxidation and sensitivity to heat.
Different types of cast aluminum alloys respond to welding differently, and you should choose the correct filler materials, shielding gas and welding technique means the difference between a strong, reliable weld or a weak, porous joint.
With preparation of the material, using the correct cleaning procedures, and regulating heat input, welders can address the issues associated with cast aluminum and generate powerful, long lasting welds that comply with harsh applications.
Challenges in Welding Cast Aluminum
Welding of cast aluminum is notoriously difficult because of the unique physical and chemical properties of cast aluminum. The awareness of these challenges helps the welders to use the right tools and application methods, resulting in defect-free, strong welds.
1. Oxidation Issues: A Major Welding Barrier
When the aluminum is exposed to air, it oxidizes almost instantly, producing very thin but very tough aluminum oxide (Al₂O₃). He went on to explain that the oxide layer formed during the initial oxidation of the aluminum has a melting point of 3,700°F (2,037°C), three times higher than the melting point of aluminum, which is 1,221°F (660°C). However, this massive difference in melting points causes severe difficulties in welding, including the following:
- Incomplete fusion (oxide layer prevents the filler metal from bonding with the base material properly).
- Contaminated welds – Oxidation present, which can cause porosity, weak joints, a nd inclusions when left in the weld.
- Oxide produces an unstable arc, which causes the arc to wander and the welding performance to be erratic.
Solution
TIG welding using alternating current (AC) helps to keep the oxide layer off of the workpiece and helps to maintain arc stability. Also, dedicated stainless steel brush and chemical cleaners such as acetone can clean the oxidation before welding.
2. Impurities and Contamination: The Hidden Threat
The aluminum is often cast from recycled materials and can thus include trapped gases, oil residues, dirt, and other impurities related to the casting production. These contaminants need to be cleaned correctly before welding, or they can lead to:
- The weld is weakened and prone to cracking due to tiny gas pockets (porosity).
- Inclusions: – It has trapped in the weld a nonmetallic substance that reduces the strength of the weld.
- Some areas may fuse well and others may remain weak with inconsistent weld quality.
Solution
Acetone or alcohol is used to thoroughly clean the surface of grease and dirt. The trapped gases need to be driven out using a preheating torch before welding.
3. Thermal Conductivity is too High: Controlling Heat is Needed
Aluminum, on the other hand, is expected to absorb and transmit heat extremely fast, compared to steel. This can lead to:
- Too much heat can melt through thinner sections (burn through).
- Unbalanced heating (warping and distortion) – The metal goes awry because it was heated unevenly.
- Inconsistent penetration – Too rapid heat dissipation causing weak fusion in the weld joint.
Solution
Also, you want to preheat your aluminum to 300°F – 600°F (150°C – 315°C) to obtain even heat distribution and better weld penetration. Higher heat input at the controlled travel speed keeps the weld pool stable.
Essential Tools and Equipment for Welding Cast Aluminum
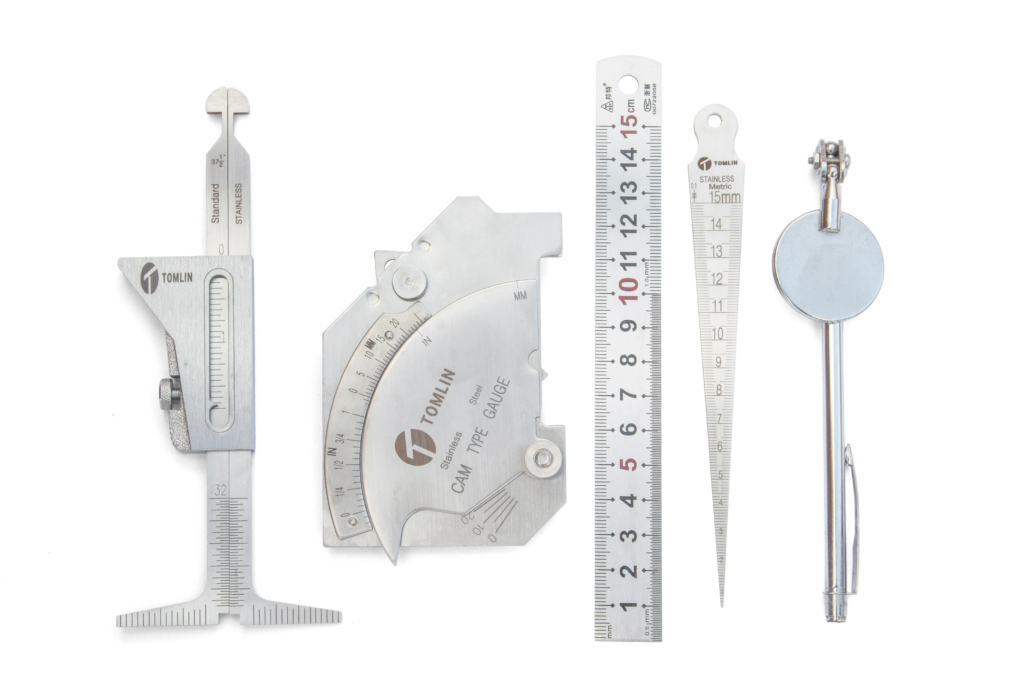
When welding cast aluminum, there is specialized equipment required and must be welded accurately, with strength and has durability in the weld.
- A welding process is itself a tool which must be chosen carefully and that is what is covered in this welding machine guide.
- The right selection of the welding machine is very important when aluminum welding is to be done.
- TIG (Tungsten Inert Gas) Welder (GTAW) – Best for precision and high-quality welds. It enables better control of heat input and is good for cast aluminum repair.
- TIG (Tungsten Inert Gas) – Suitable for inner metals, but much slower than MIG. Best for thicker cast aluminum sections.
1. Filler Metals: Strengthening the Weld
A strong, crack-free weld depends on a good right filler rod.
- 4045 Aluminum Filler – General-purpose option for cast aluminum repairs.
- 5356 Aluminum Filler – Provides high strength and corrosion resistance, ideal for marine applications.
- Aluminum Filler – 4047 has a high silicon content for the reduction of cracking, improvement of runoff
2. SHEILDING GAS
As the name suggests, a gas in the welding flux that prevents oxidation and porosity. They are typically inert gases chosen for their desired properties.
- The weld is protected from atmospheric contamination by shielding gas.
- Argon 100% – for TIG and MIG welding, the best choice to achieve a stable arc and a clean weld pool.
- Argon-Helium Mixture – Helium increases heat input and penetration, and thus is used to cut thicker aluminum sections.
3. Cleaning and Preparation Tools
The weld cannot be successful until there is a clean surface.
- Removes oxidation without contaminating the surface, stainless steel brush.
- If you need to clean oil, grease, or dirt before welding, acetone or alcohol will work well.
- Thermal shock is prevented, and moisture and trapped gases are driven out.
Preparing Cast Aluminum for Welding
Defects are to be avoided and a strong weld obtained by proper preparation.
Step 1: Cleaning the Surface
Since aluminum so retains dirt, grease, oxidation and moisture, you have no choice but to clean.
🔹 Why is Cleaning Important?
- Prevents porosity and contamination.
- It helps in better fusion between filler metal and base material.
- Assists in keeping the arc stable when welding.
🔹 Cleaning Process:
- Aluminum can be degreased with acetone or alcohol to remove oil and contaminants.
- ALWAYS remove the oxide layer with a stainless steel brush (dedicated for aluminum only).
- It is important to avoid touching the cleaned surface with bare hands to prevent recontamination.
Step 2: Preheating the Aluminum
It reduces internal stress and improves the weld penetration.
🔹 Why Preheat?
- It minimizes cracks in the porous cast aluminum.
- It assures better distribution of heat and quality of the weld.
- It helps drive trapped gases and moisture.
🔹 How to Preheat Cast Aluminum:
- Rectify the part to 300°F – 600°F (150°C – 315°C).
- An infrared thermometer can be used to monitor temperature.
- It can also be weakened by overheating; avoid this.
Welding Techniques for Cast Aluminum
To successfully weld cast aluminum, you have to make sure to use the correct technique, keep good heat control and use the proper welding parameters. The following are the best welding methods for cast aluminum with details on their best practices.
1. TIG Welding (Best for Precision and Strength)
The preferred method for welding cast aluminum is Tungsten Inert Gas (TIG) welding or Gas Tungsten Arc Welding (GTAW) because it has the precision to produce clean, strong welds.
🔹 Key TIG Welding Tips
- Use AC mode: The AC mode allows for a more effective breaking through of the aluminum oxide layer and arc stability.
- At 15° is the Best Angle for the Torch: This ensures that you maintain even penetration and no contamination.
- Short Arc Length is Important: The shorter the arc is, the better heat control is and less prone to burn through and porosity.
- Choose the Right Filler Rod: 4047 (high silicon content) reduces cracking and 5356 gives superiority in strength and corrosion resistance.
- High Frequency Start, provides a smooth arc start without contaminating the electrode with tungsten.
🔹 Best For: Thin cast aluminum parts, precision repairs, aerospace and marine applications.
2. MIG Welding (Best for Speed and Efficiency)
A faster alternative to TIG welding, except for very thick aluminum sections is Metal Inert Gas (MIG) welding, also known as Gas Metal Arc Welding (GMAW). However, the control of voltage and wire speed while MIG welding is very critical to prevent defects such as porosity or burn through.
🔹 Key MIG Welding Tips:
- Use a Push Technique: If you pull you back to get you closer, it completely contaminates the surface and it’s not as clean.
- In Spray Transfer Mode, Significant spatter is eliminated and the arc is very stable, producing a high-quality weld.
- Proper settings allow for good fusion without overheating.
- Helium will enhance penetration and can be used for thicker sections, or use Pure Argon or Argon-Helium mix.
- Preheating the Workpiece helps reduce thermal shock and reduces cracking.
🔹 Best For: Thicker cast aluminum parts, automotive repairs, industrial applications.
3. Alternative Welding Methods (when a special case arises)
Sometimes TIG or MIG welding will not be the best approach because of heat sensitivities, part complexity, or the need for repair. For special cases, the following alternative methods can be used.
- Brazing is the use of a lower temperature filler metal that minimizes the risk of distortion or weakening of heat sensitive components.
- Cold Metal Transfer (CMT) is low heat and the thermal stress is less, great for delicate repairs.
- Laser Welding – It can source precise local heat input to thin-walled aluminum components.
🔹 Best For: Low heat applications, minor repairs and high precision welding.
Welding Defects and How to Fix Them
Cast aluminum components pose problems even to experienced welders because of porosity, cracking, and fusion difficulties. These defects, and ways to avoid and fix them, are of vital importance if one is ever to achieve reliably strong, durable welds.
1. Porosity (Gas Pockets in Welds)
Gas pockets trapped in the weld are considered porosity, which weakens the structure. Because cast aluminum is naturally ‘porous’, it is more prone to this defect.
🔸 Causes
- OR Contamination with dirt, oil, grease or oxidation.
- A low shielding gas flow rate or a leak in the system.
- It has rapid cooling, which traps gas in the weld.
🔹 Solutions
- Make sure the surface of the aluminum is clean before welding, and wipe it thoroughly with acetone or even alcohol.
- Remove oxidation using a stainless steel brush (dedicated to aluminum).
- Maintain proper gas flow rate (15-25 CFH for pure Argon).
- Reduce trapped gas expansion and increase the penetration by preheating the workpiece.
- Reduce porosity issues by using a higher silicone filler (e.g, 4047).
Pro Tip: Always keep the filler metal dry and free of moisture since the presence of moisture in the filler rods can introduce porosity in the weld.
2. Cracking (Weak and Brittle Welds)
High thermal stress or selecting a wrong filler material can be a common reason of cracking. Aluminum contracts a great deal as it cools, putting stress build up resulting in cracking.
🔸 Causes
- Causes shrinkage cracks under high thermal stress.
- Employing the wrong filler metal and thus, the incompatibility.
- Preheating is insufficient, resulting in uneven cooling and buildup of stress.
🔹 Solutions
- Heat the workpiece to 300°F – 600°F (150°C -315°C) to minimize thermal shock.
- Use a high-silicon filler rod of 4047, which resists cracking.
- Ensure that the weld cools slowly so that there are no stress fractures.
- Aluminum castings for large parts may be welded using a multipass technique to distribute heat evenly and reduce stress.
Pro Tip: If cracks appear after welding, remove the crack using a die grinder, clean the area and re-weld it with proper preheating.
3. Lack of Fusion (Weak Bond Between Metal and Weld Bead)
Fusion is said to be absent when fusion has not been made between the weld bead and the base material, forming a weaker joint. Often the cause of this defect is under heat input or improper welding techniques.
🔸 Causes
- Low heating input restricts from that it can melting properly.
- Fast travel speed and no penetration.
- So create the incomplete fusion caused by an incorrect torch angle.
🔹 Solutions
- Increase the heat settings to penetrate the base metal properly.
- The travel speed must be slowed down to allow the nuclei to fuse more deeply.
- Maintain a steady torch angle (10-15 degrees) for consistent penetration.
- For a Helium-Argon gas mix and cast thick aluminum, the heat input will go up.
Pro Tip: In case lack of fusion is found, the defective weld is ground out, the surface is cleaned, and the weld is re-made with higher heat and slower travel speed.
Post-Weld Treatment and Finishing
Once the welding operation has been completed, strength, durability, and corrosion resistance can be ensured only by proper finishing and post weld treatments.
Step 1: Stress Relief Treatment
- After the weld cools slowly to avoid residual stress and cracking.
- If necessary, post-weld heat treatment should be employed for the restoration of mechanical strength for critical components.
- Do not quench the weld with water or air blasting since rapid cooling might cause new cracks.
Pro Tip: It is recommendatable to cover the welded part with a thermal blanket so as the part can cool gradually, and the risk of stress crack will be reduced.
Step 2: Grinding and Polishing
- If excess weld material and smooth the surface, use a flap disc or die grinder.
- If the application is for a polished cosmetic, then polish the aluminum on fine sandpaper (600 – 1200 Grit) or buffing wheels.
- To finish, blend the weld into the surrounding metal if needed.
Pro Tip: Do not use a carbon steel grinding tool on aluminum, because the contamination can cause corrosion problems.
Step 3: Corrosion Protection
Although Aluminum is naturally corrosion resistant due to the oxide layer, further protection can be afforded in the case of harsh environments to increase life spans.
- Anodizing – Refers to a procedure where a protective oxide layer is formed in order to increase corrosion resistance and to improve the appearance of the part.
- Powder Coat – Gives the part a durable finish which protects against wear and damage from the environment.
- Paint or Sealants – Provides cost-effective protection for non-critical parts.
Pro Tip: When using paint, etching primer should be used because it will both increase adhesion and durability.
Practical Applications of Welding Cast Aluminum

Welding cast aluminum is commonly used in many industries, such as automotive repairs, aerospace manufacturing and more.
1. Automotive Repairs
- The ability of the TIG welding to pinpoint and repair engine blocks, cylinder heads and transmission cases.
- Repair of cracked alloy wheels and suspension components.
- Chassis parts reinforcement for high-performance or off-road.
Pro Tip: Welded aluminum components are found on many high performance racing vehicles in order to keep the weight down, but still retain strength.
2. Aerospace and Aviation
- Repairing aircraft fuselage components and engine parts.
- Welding of aluminium landing gear and airframe structures to keep weight whilst maintaining strength.
- Fabricating custom aerospace parts, such as fuel tanks, wing structures, and pressure vessels.
Pro Tip: A356 and 7075 are aerospace grade aluminum alloys that weld only if special techniques and exacting heat control can keep the integrity of the weld.
3. Marine Industry
- Aluminum boat, propeller, and marine engine casing repairs.
- Welding marine-grade aluminum for saltwater resistance.
- Repair of offshore structures and shipbuilding components normally subjected to rough environments.
Pro Tip: For all marine applications, the filler material should always be in saltwater resistant type, such as 5 356.
4. Industrial and Construction
- Repairing heavy machinery parts and factory equipment.
- Reinforcing aluminum scaffolding, piping and support beams.
- Fabricating custom aluminum structures for manufacturing and construction.
Pro Tip: Preheating large cast aluminum structures for welding to prevent cracking and distortion is generally done in industrial environments.
Conclusion
Welding cast aluminum is a skilled process that demands the perfect blend of preparation, equipment and first-class welding knowledge to perform the task well. Following correct cleaning, preheat, and welding methods will assure you of strong, reliable welds. However, you do not have to be involved with aerospace, marine or automotive industries or industrial applications to benefit from cast aluminum welding for repairs or fabrication. With time and practice, patience and attention to detail, cast aluminum will be something you weld with little problem, with minimal defects and professional quality results. With your technique, time must be invested to create welds that last the life of a part, in high-strength applications.
FAQs About Welding Cast Aluminum
1. What factors are considered more challenging in welding cast aluminum?
Porosity, oxidation and high thermal conductivity of cast aluminium increase cracking, porosity, and weak welds. The oxide layer on it fuses at far greater temperatures than the aluminum itself melts at, and as such is difficult to fuse.
2. What is the best workable type of welding a cast aluminum?
Precise and clean welds are made possible using TIG while MIG is good on thicker materials. Strong welds require preheating, the correct filler, and shielding gas.
3. What are the ways to avoid porosity and cracking?
Reduce thermal stress by thoroughly cleaning the surface, use of pure argon gas and preheat to 300F – 600F. The use of a high silicon filler metal (4047) can aid the resistance to crack development.